MacroFab Blog
In our previous series, Programming for PCB Production, we provided an overview of different methods to program PCB products. So far, we’ve covered how to design and build a simple programming fixture. In this article, we’ll cover how to design pogo pin programming cables for faster production programming. This coincides with our release of Tag-Connect footprints for Eagle. Other EDA tools will follow!
What is a Pogo Pin Connector?
A Pogo Pin Connector, often called a spring-loaded connector, is a reliable and efficient electrical connection solution prized for its robustness and consistent performance. Engineered with an innovative helical spring design, reminiscent of a pogo stick, these connectors guarantee a steady and continuous normal force against the mating interface, regardless of external disturbances. This resilient design mitigates connection interruptions caused by vibrations, shocks, or other mechanical stresses.
The unique spring mechanism within a Pogo Pin Connector ensures a secure and reliable connection, even under demanding conditions. This makes them ideal for various applications, including wearable devices, mobile phones, automotive electronics, and industrial equipment. By selecting the appropriate Pogo Pin Connector, engineers can optimize device performance, durability, and user experience.
Tag-Connect Cables and Footprints
Pogo pin programming cables are essentially pogo pins molded in a handle that connects a programmer to the device to be programmed. They are similar to a full-on test fixture like we designed in the last article, but are more flexible since they are not designed specifically for one PCB. Tag-Connect is the supplier we like to use here at MacroFab for these kind of projects.
Figure 1 shows the end of a Tag-Connect cable. These kind of cables are great for low volume production programming since there is no cost in designing and building a fixture. You also save in not having to populate a part for a programming header saving in the BOM costs and assembly labor. The downside to pogo pin programming cables compared to a full-on fixture is that you still need to apply power to the board that is being programmed but this can be addressed in some cases.
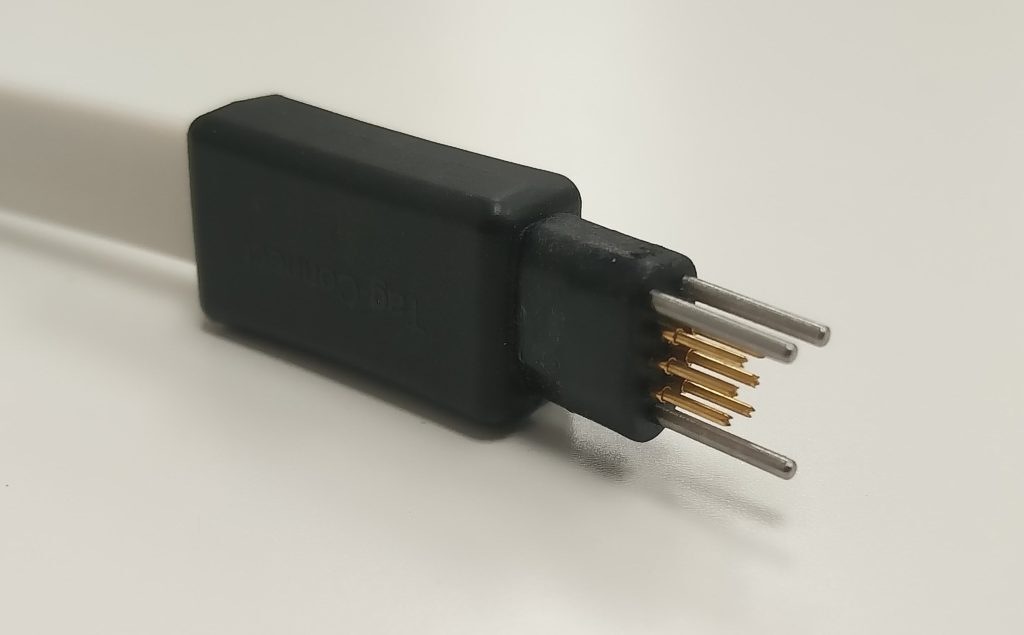
IMG 20160726 141728 1024x635
Figure 1: Tag-Connect TC2030 cable with no locking legs
Tag-Connect carries several different cables that can connect a wide variety of programmers to your project and MCU. There are three different connector sizes:
• TC2030 is a 02 x 03 (6 Position) connector,
• TC2050 is a 02 x 05 (10 Position) connector,
• TC2070 is a 02 x 07 (14 Position) connector.
Figure 2 shows all the different sizes Tag-Connect offers. For these connectors there are two different sets of legs. Tag-Connects without locking legs (shown above in Figure 1) and Tag-Connects with locking legs. The locking legs are useful for prototyping as you don’t need to hold the connector in while programming which makes it easier for debugging. The downside to the locking legs is that they take a bit more room then the non-locking legs version and are a bit more fiddly to use while in production. In the MacroFab parts libraries we have pre-built footprints (see Figure 3 for an example) for the TC2030, TC2050 style connectors as these are the most common. For Eagle they are in the MF_Connectors.lbr library under CON_02x03 and CON_02x05.
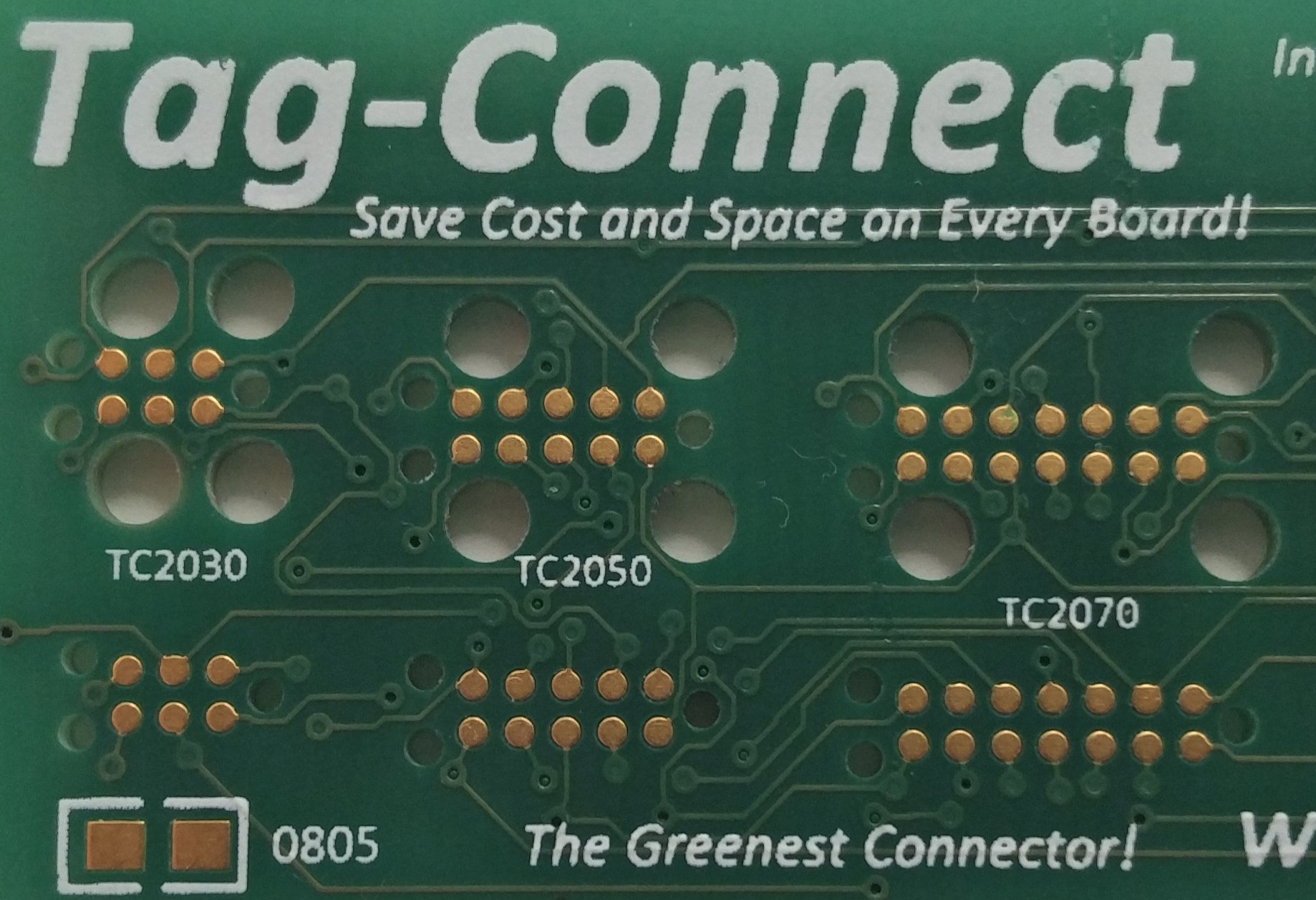
IMG 20160726 141648
Figure 2: Footprint comparisons for Tag-Connects different sizes
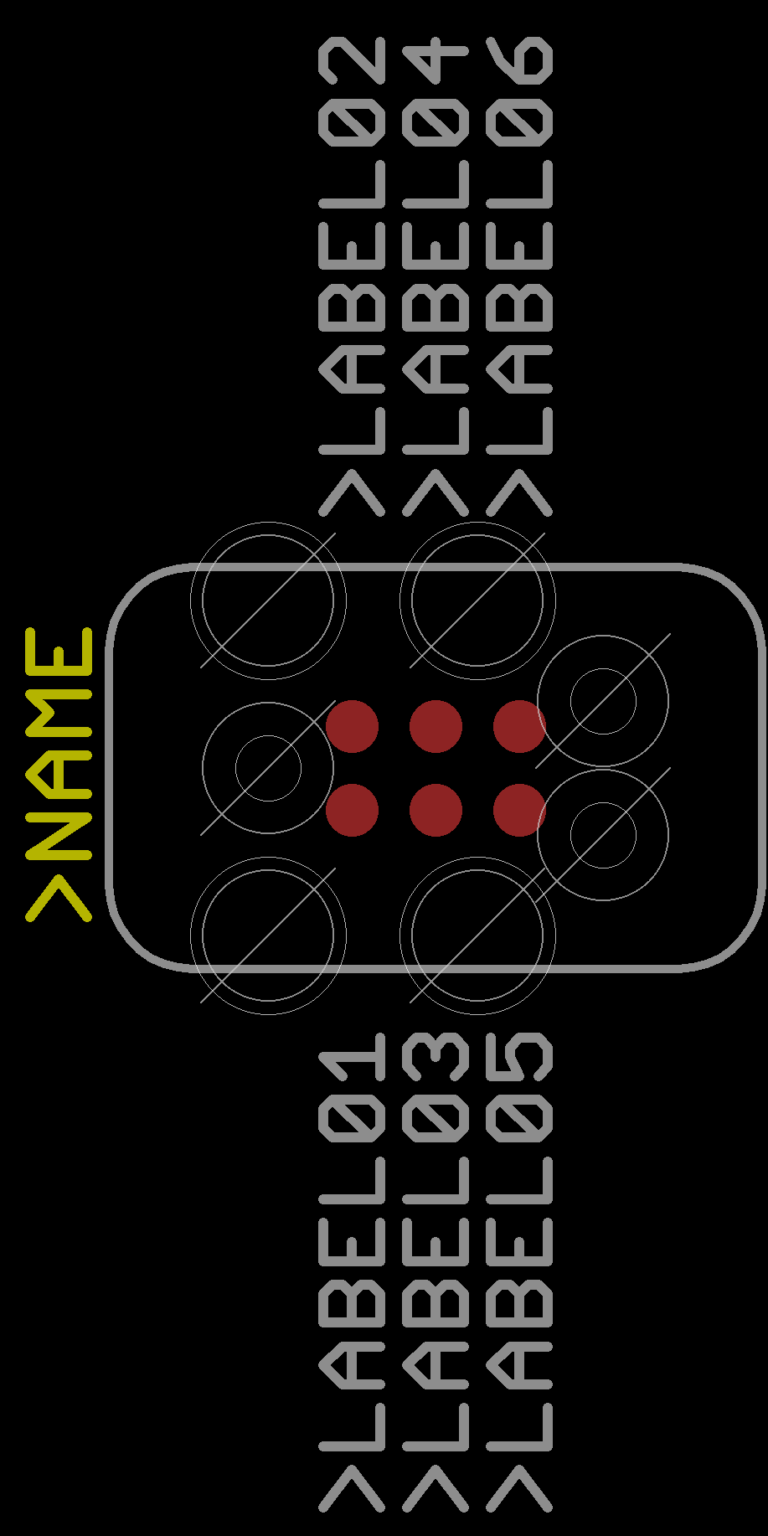
TC2030 768x1536
Figure 3: The Tag-Connect TC2030-IDC-FP footprint in Eagle
Using Tag-Connect Cables
To use the Tag-Connect cable you just line up the locating pins and press it into the board. If you are using the no locking legs version you must hold it until programming is done (See figure 4).
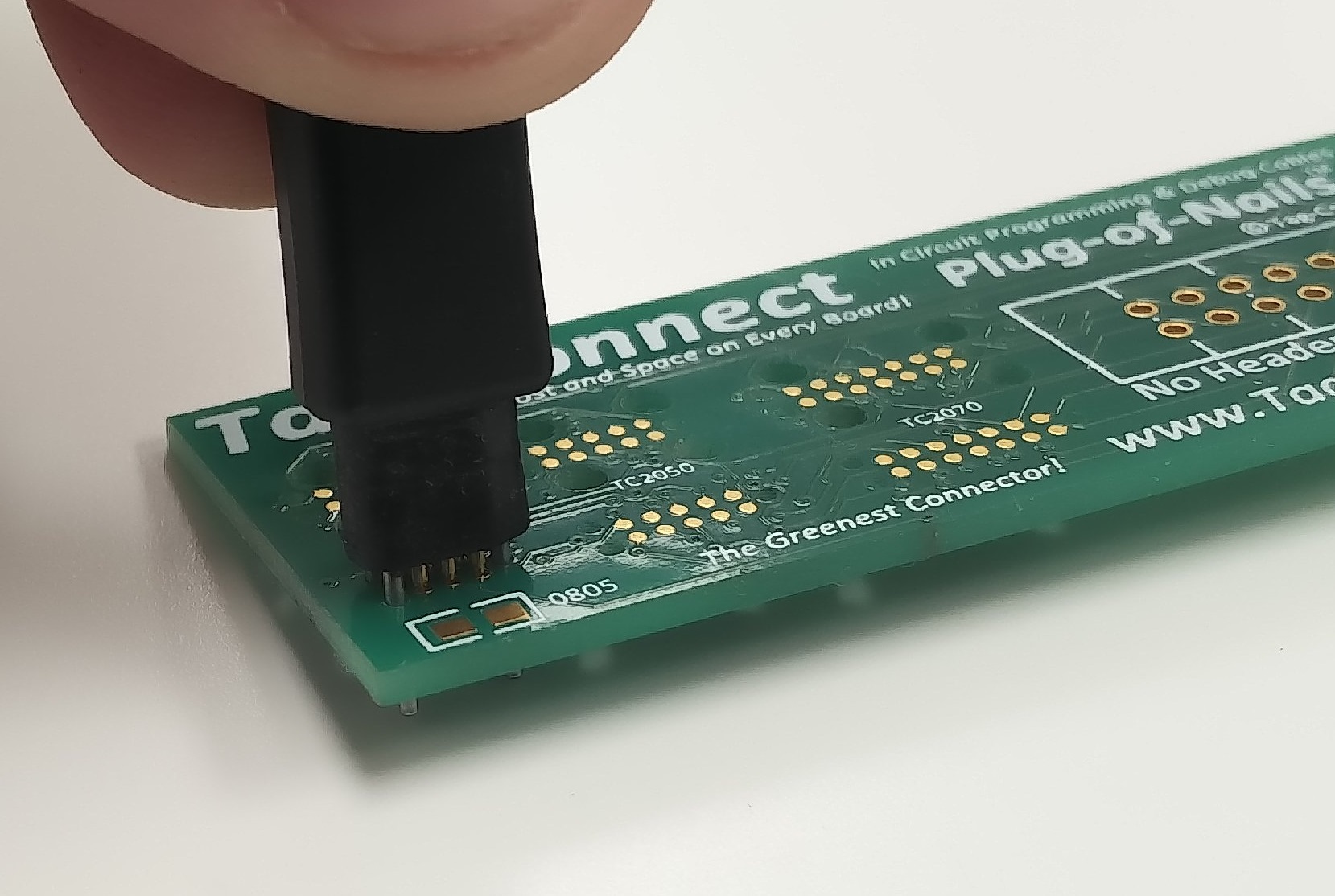
IMG 20160726 141906
Figure 4: Example of how to use a Tag-Connect cable
In the next article, we’ll go over how to adapt your design to use a Tag-Connect cable by building up a small AVR-based PCB and programming it with ISP over a Tag-Connect cable.
Ready to Get Started?
Get an Instant Quote NowAbout MacroFab
MacroFab offers comprehensive manufacturing solutions, from your smallest prototyping orders to your largest production needs. Our factory network locations are strategically located across North America, ensuring that we have the flexibility to provide capacity when and where you need it most.
Experience the future of EMS manufacturing with our state-of-the-art technology platform and cutting-edge digital supply chain solutions. At MacroFab, we ensure that your electronics are produced faster, more efficiently, and with fewer logistic problems than ever before.
Take advantage of AI-enabled sourcing opportunities and employ expert teams who are connected through a user-friendly technology platform. Discover how streamlined electronics manufacturing can benefit your business by contacting us today.