MacroFab Blog
Your success in PCB prototyping depends on following a robust final checklist to address all design details.
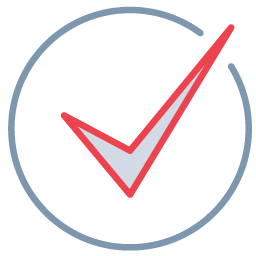
Checkpoint
Undocumented knowledge is non-repeatable and leaves your design at risk.
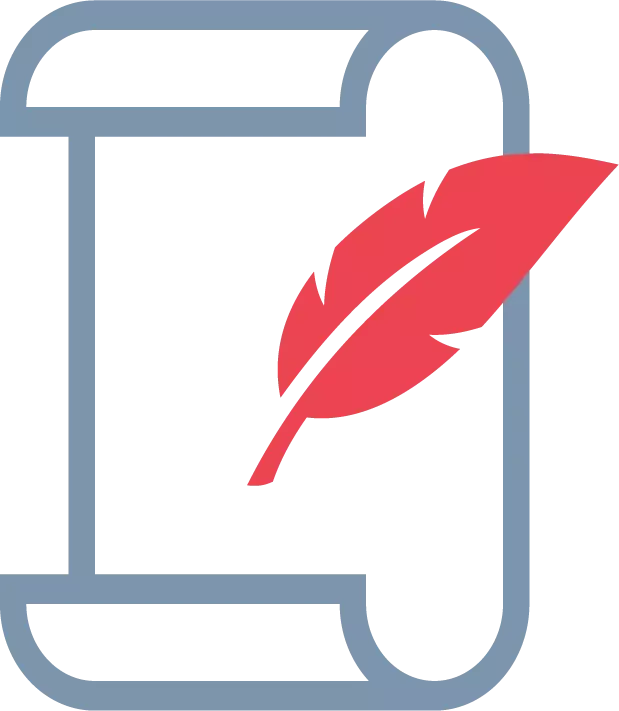
A rapid prototyping design project occurs in various situations, but time is often a leading factor. However, your success in PCB prototyping depends on following a robust final checklist to address all design details to ensure a seamless transition to manufacturing without costly delays. This quick process should happen before uploading the final files to your CM.
While changes are possible at any time, once a quote is accepted changes may slow down your rapid prototyping process or increase costs. It’s better to spend a few minutes making sure everything is correct the first time.
Working with your CM and communicating changes will help mitigate issues and will maximize the probability of success. Take these five key steps before your CM begins work to improve the chance of prototyping and project success.
Essential Steps for Successful PCB Prototyping
While this list is not exhaustive by any means, it should help guide you through the most important steps before finalizing your rapid prototyping order.
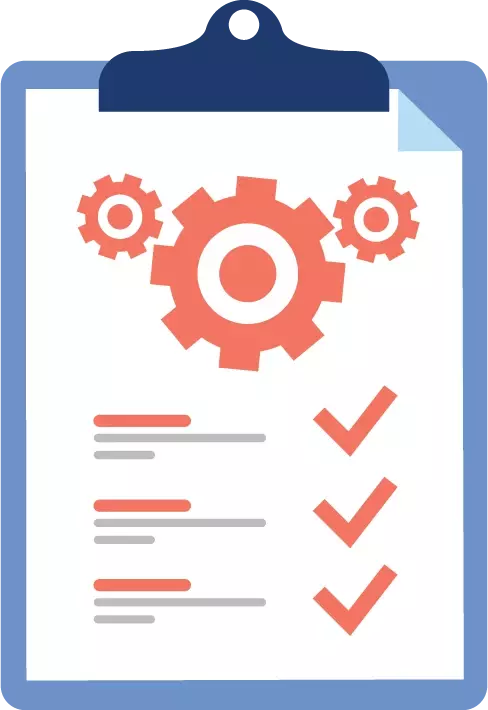
Conduct a thorough PCB BOM (Bill of Materials) review to confirm all components align with operational and design requirements. This confirms all details are correct for operation. While component function drove your initial choice during the design phase, check all listed components' part names and MPN now. Double-check to ensure details of each part’s performance still match project requirements.
Specifics such as operating temperature, footprint, pinout, lead-free designation, and package type need to match design expectations and CM equipment capabilities. Keep in mind that some of these differences are denoted by only a single letter, number, or a subtle suffix.
Finally, in a volatile market, both prices and lead times can fluctuate like stock prices. Make sure that the displayed specifics work for your project.
Compile a backup list of alternate components for smooth PCB prototyping in case of supply chain challenges. Your BOM needs more than just a primary component list. Alternate components serve as a substitute when the primary part is either out of stock or has a prohibitively long lead time.
While passive resistors and capacitors may have easy-to-identify replacement components, higher-performance components may have fewer direct substitutes. The more alternate components identified for the BOM, the easier it is to have the PCB assembled. The MacroFab technology platform will automatically find engineer-approved alternates as part of your upload process. This serves not only the rapid prototyping phase but can also be leveraged for high-volume manufacturing.
In a volatile market, this step can make a huge difference in product deliverability. Customers who do not take this step experience more delays and much more friction earlier in their build process.
Verify files using the MacroFab platform. Use the MacroFab connected platform for visualizing assembly designs, confirming part placements, and finalizing your PCB manufacturing files. This gives you a chance to check internal planes, assign layers to a category, verify layer count and select your manufacturing type. It also gives you a chance to ensure parts are properly aligned on the board’s surface.
Run a detailed PCB design rules check (DRC) to verify spacing, vias, and nets, ensuring compliance with your CM's manufacturing standards. Examine any reported issues by your CAD to ensure they are acceptable to your team. Also, ensure any traces with required controlled transmission impedance are specifically identified for your CM. Additional care and processing are required to maintain this trace impedance performance. MacroFab has four different sets of design rule checks for PCB assemblies depending upon the complexity of build. Our team of engineers reviews every order to identify potential issues before parts are ordered.
Ensure all critical PCB manufacturing files—Gerbers, BOMs, and layer files—are correctly formatted for your contract manufacturer. This includes
- Gerber files
- Bill of materials (BOM)
- PCB layer files
- Component layout files
Ensure that the formats generated by your tools are compatible with those supported by your CM. Once you confirm agreement on the formats, starting rapid prototyping with a cloud manufacturer is as simple as dragging and dropping your files. This can be even easier for Altium users, as they can accomplish this with push-button ease from within Altium Designer.
How Cloud Manufacturing Speeds Up Prototyping
A cloud manufacturing platform provides a central intelligence hub for all the information needed to manufacture a product, from prototype to full production. The above checks can happen on your own time, whether that’s in the middle of a workday or at 4 am. Make decisions, review information, and accept quotes without having to interact with CM sales or other internal teams, unless you want to. Quotes populate automatically, offering you a fast and accurate window into costs and turnaround times while allowing you the flexibility to toggle quantities and other data to reach the best cost/turnaround ratio for your needs.
Cloud manufacturing services help automate final process checks for your PCB project. It provides all the visibility to your design and procurement teams to ensure that the technical and logistic details are communicated in near real-time for effective decisions by your team.
Scaling Beyond PCB Prototyping: What’s Next?
After a successful rapid prototyping phase, the last thing a project development team wants to do is to restart all the work again.
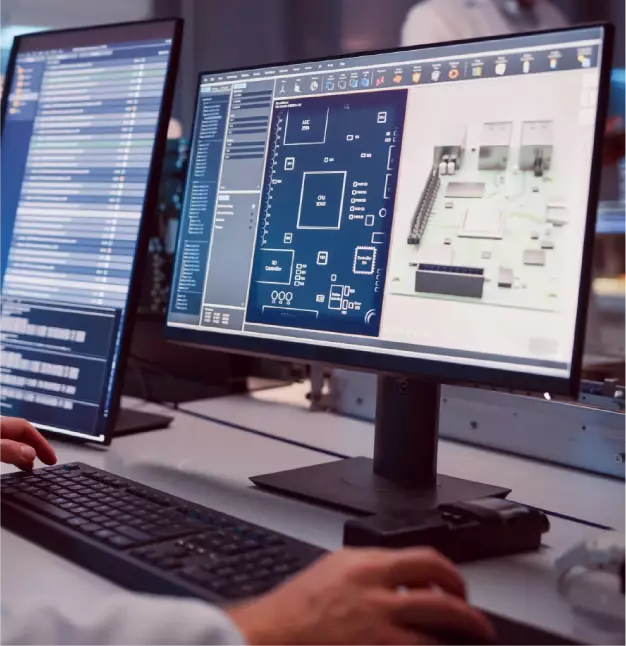
By using a CM with over 100 manufacturing partners at its disposal, this transition can be seamless. Through the use of a CM’s cloud manufacturing service, the effort, time, and iterative work spent in the earlier phases of the hardware development process can be leveraged in volume production. The learnings from earlier phases are retained within a native digital thread that remains constant regardless of how volume production is routed through the factory network.
This is an important change from traditional manufacturing where natively held knowledge for a product run may remain undocumented as “tribal knowledge” with key employees. But undocumented knowledge is non-repeatable and leaves your design at risk. The digital thread used within cloud manufacturing ensures production runs remain repeatable and portable, significantly reducing risk and increasing manufacturing flexibility.
Although the prototype phase is only the beginning of your project, it is also the foundation for building toward higher volume manufacturing.
Five of the most critical final checks before uploading your project to your CM involve performing a final BOM review, selection of alternate components, design rules check verification, visual alignment using MacroFab’s platform, and preparing all the manufacturing files your CM needs to complete the job. By optimizing your PCB prototyping process and leveraging a cloud manufacturing platform, you set the stage for streamlined production and long-term success in electronics manufacturing.
Related Topics
PCB Antenna Design: A Step-by-Step Guide
Step-by-step guide to the PCB antenna design process, providing practical tips to help you successfully integrate the antenna into your wireless product.
Top 10 Electronics Podcasts You Should Listen To
This curated list of top electronics podcasts is tailored for those trying to keep up with the rapidly evolving tech world.
MacroFab's Certifications Benefit PCBA Production
Your PCBA production must be secure and reliable for your products to compete in the market. We have listed our certifications and how they benefit you.
Read our White Paper
“Choose the Optimal Contract Manufacturer for New Product Prototyping” to learn more about building a successful prototyping plan.
About MacroFab
MacroFab offers comprehensive manufacturing solutions, from your smallest prototyping orders to your largest production needs. Our factory network locations are strategically located across North America, ensuring that we have the flexibility to provide capacity when and where you need it most.
Experience the future of EMS manufacturing with our state-of-the-art technology platform and cutting-edge digital supply chain solutions. At MacroFab, we ensure that your electronics are produced faster, more efficiently, and with fewer logistic problems than ever before.
Take advantage of AI-enabled sourcing opportunities and employ expert teams who are connected through a user-friendly technology platform. Discover how streamlined electronics manufacturing can benefit your business by contacting us today.