MacroFab Blog
Wired for Autonomy: Confronting PCBA Complexities in Mobile Robotics
The field of untethered robotics is booming, and across industries, autonomous robots are rapidly assuming responsibility for an increasing number of tasks. In their expansion into increasingly diverse industries, these robots place additional demands on their internal workings, specifically the PCBAs that help them function.
However, developing PCBAs for autonomous robot systems presents several unique challenges that electrical engineers must overcome to succeed. We take a deep dive into these challenges by exploring design considerations beyond those associated with conventional PCBAs.
Beyond the Basics: Design Considerations for Autonomous Robots
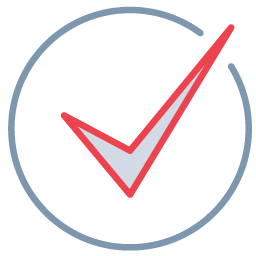
Checkpoint
Autonomous robotics must anticipate and plan for the unexpected, often in harsh, changing environments.
While core electrical principles remain a top priority, autonomous robotics introduces additional complexity to PCBA design that electrical engineers must consider from day one. To function properly, these machines must anticipate and plan for the unexpected in harsh, changing conditions.
Intuitive Machines’ Odysseus moon lander recently brought this to light, when the private spacecraft landed on the moon’s surface. As much as the sideways landing attracted media attention, few reports focused on last-minute troubleshooting that kept the mission afloat, a testament to the quick-thinking nature of the engineers involved.
Here are some of the important factors to consider when designing PCBAs for untethered robotics:
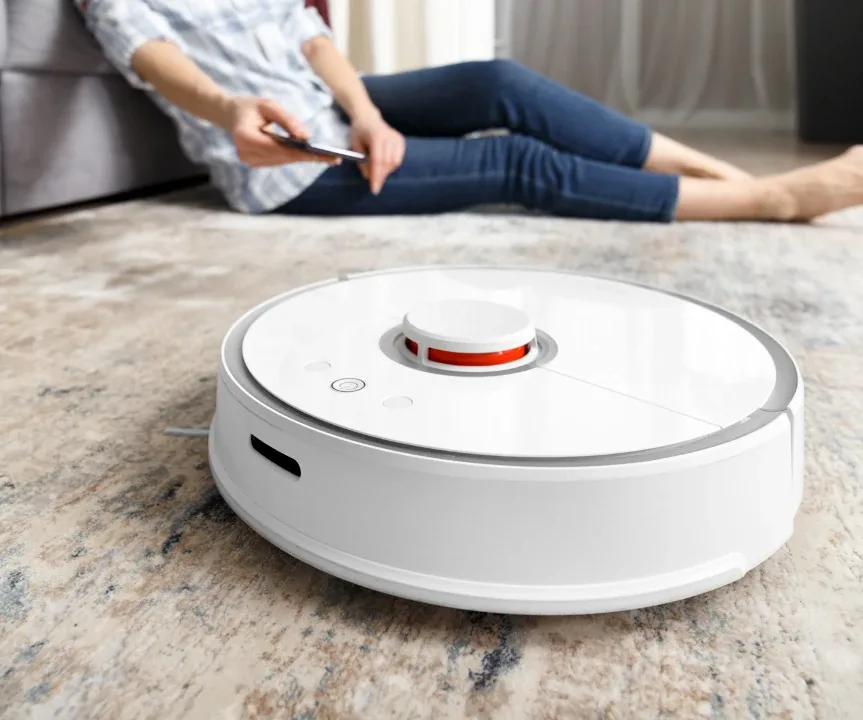
- PCBAs Must Prioritize Efficiency: Untethered robots almost entirely rely on batteries, so PCBAs must focus on efficiency. The key to this is meticulous component selection, such as using low-power microcontrollers and efficient voltage regulators, as well as excellent circuit design that minimizes standby currents. Using clock gating also maximizes battery life and reduces heat generation.
- Maintain Signal Integrity Amid Noise: Robots operate in dynamic environments with potential electrical noise from motors, sensors, and external sources. EMI can wreak havoc on robotic sensors, causing glitches, calibration issues, or even complete sensor failure. Consider layout strategies in detail to cut crosstalk and ground loops and maintain clear signal transmission.
- Build for Endurance: Many robots are subjected to extreme temperatures, temperature fluctuations, vibrations, and shocks. Use ruggedized PCBA boards that have components with adequate vibration and temperature ratings. To prevent overheating, soldering must be properly performed to handle thermal expansion and contraction, mechanical fatigue, and dust and moisture infiltration. Enclosures need to protect against dust and moisture egress.
- Size Matters: Robots must be mobile, so PCBAs must also be compact and lightweight to minimize robot weight. Choose wisely when choosing mechanisms within your robot, like vacuum track-based models or electromagnetic ones. They may increase the mass of your robot and reduce maneuverability. High-density interconnect (HDI) techniques and minimizing wasted space become crucial.
- Don’t Compromise Reliability: Autonomous robots, operating alone, demand ultra-reliable PCBAs to minimize failure. Filtering tackles this by reducing sensor noise for cleaner data, smoothing data for fewer errors, extracting key features for better navigation, and even lowering processing load for faster decision-making. Redundancy and fail-safe features further enhance reliability.
- Play by the Rules: Robots must comply with Electromagnetic Compatibility (EMC) regulations to ensure proper operation and avoid interfering with other electronic devices. Shielding techniques and filtering components become necessary.
- Ensure Maintainability: After assembling, it’s crucial to diagnose faults and perform maintenance. Make sure test points are conveniently accessible after the final assembly. Consider implementing Built-in Test (BIT) features on the PCBA for self-diagnostic features or options for wireless troubleshooting.
The Unexpected Factors: When Biology Interferes
Biological influences are often overlooked when designing PCBAs for autonomous robotics but are an important factor. Autonomous robotics may work in many different environments, encountering biological challenges that can undermine even the most robust and reliable designs.
Biofouling
Biofouling, or the accumulation of microorganisms on surfaces, happens most frequently in aquatic environments. However, this issue can also occur within humid industrial settings or food processing facilities. Biofouling causes issues in many ways including:
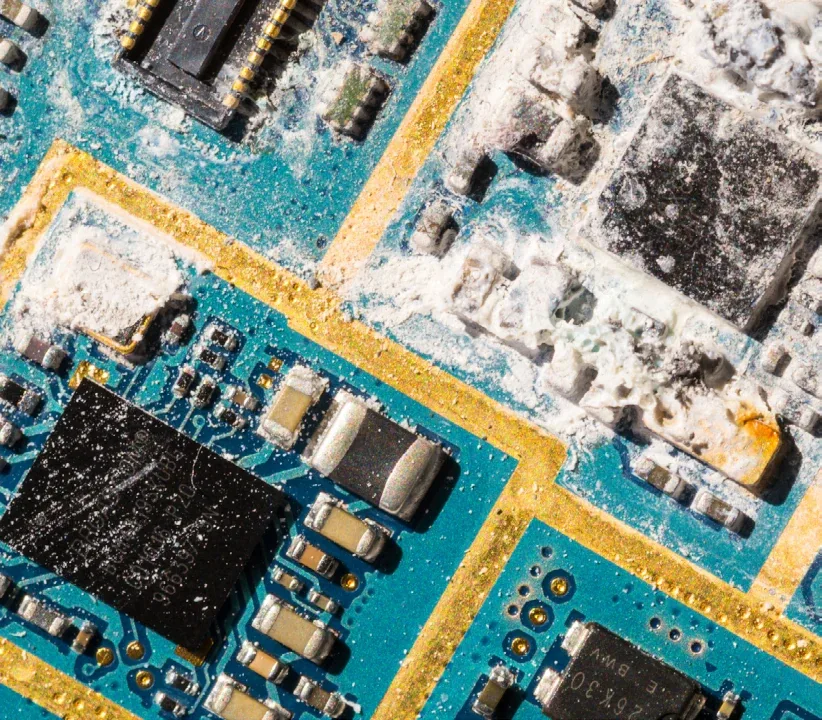
- Reduced Performance: Fouling on sensors, thrusters, and hulls can decrease efficiency and accuracy. As a result, sensors become less sensitive, propellers drag more, and overall power consumption increases. Special coatings applied to surfaces can deter organism attachment.
- Problems with Navigation: Fouling on navigational equipment leads to positioning and localization errors, which make it difficult for the robot to map its surroundings, keep its trajectory, and reach its destination.
- Maintenance Issues: Regular cleaning to remove biofouling is essential, particularly in remote locations. As a result, downtime occurs and reduces operational efficiency. Prevent biofouling with brushes or wipers, as well as scheduled cleaning protocols.
- Damage and Disruption: Biofouling can cause physical damage by promoting barnacle growth and corroding structures. Choosing materials that discourage organism growth is a passive defense, and monitoring systems can detect biofouling early and trigger automatic cleaning.
Especially within industrial and food processing industries, biofouling can create a surprising but challenging issue for logistics robotics in order fulfillment, for example, or other autonomous vehicles. Make sure to consider this possibility when designing for specific applications.
Biological Challenges Across Environments
While biofouling dominates aquatic environments, other biological factors impact robots in other settings:
- On Land: Dust, dirt, and debris can accumulate on sensors and cameras in terrestrial robots, hindering performance. Agricultural robots may encounter challenges with mud and plant debris.
- Airborne: Airborne robots face issues with dust, pollen, insects, and other airborne particles that can increase drag, reduce lift, and affect sensor accuracy.
To address animal-related challenges, EEs can employ design strategies like:
- Physical Resilience:
- Challenge: Animals may chew on cables or antennas, causing malfunctions.
- Solution: Employ ruggedized components, reinforced substrates, and protective enclosures to enhance PCBA durability against physical damage from animal interactions. Additionally, utilize encapsulation and conformal coatings to safeguard critical components from moisture, dust, and possible damage by animals.
- Sensor Integrity:
- Challenge: Animals brushing against sensors can distort sensor inputs, leading to navigation errors.
- Solution: Design sensors with robust shielding, noise filtering capabilities, and redundancy features to ensure reliable operation and accurate data despite potential interference from animals. Develop strategies for preventing animals from brushing against sensors to keep distortions and navigational errors from happening. For example, anti-fouling paints or cages around the robot could prevent fouling, or sensors might be placed where animals cannot access them.
- Mobility Optimization:
- Challenge: Animals blocking pathways or obstructing movement can impede the robot’s forward progress.
- Solution: Develop strategies to address mobility constraints caused by animals blocking pathways or obstructing movement, ensuring that robots can navigate effectively and complete their objectives. This could include low-power LEDs or subtle sounds that encourage animals to move away. Optimize power management systems to maximize operational autonomy and extend battery life in resource-constrained environments where robots may interact with animals.
Security: The Next Level in AMR PCBA Design
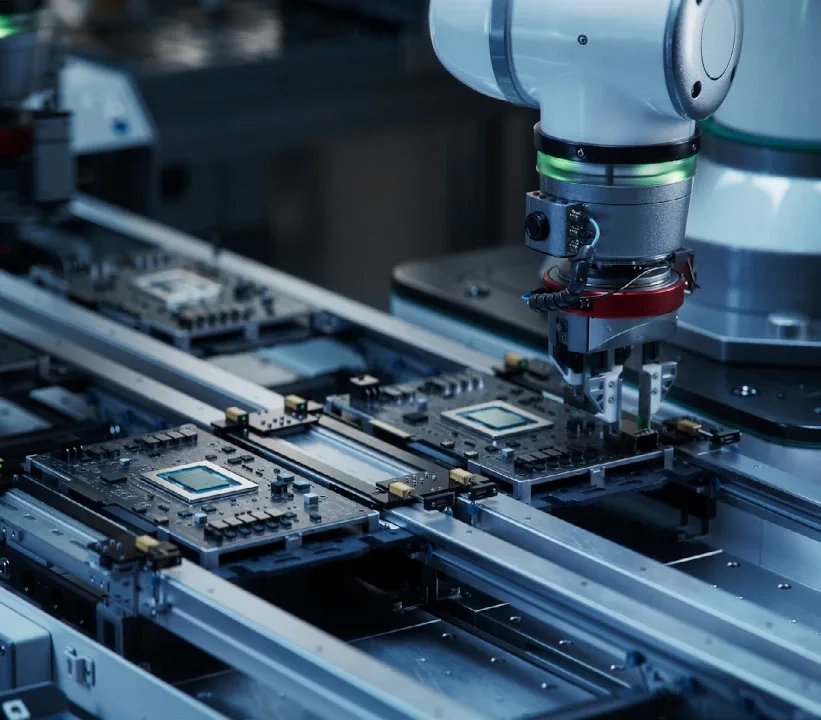
AMR PCBA security
PCB design traditionally focuses on protecting against electrical malfunctions and physical damage. However, for AMRs (autonomous mobile robots) connected to the internet, cybersecurity emerges as a key concern. Hacking hazards present significant security risks. A compromised robot can open the door to major security breaches. Thus, incorporating encryption and secure boot mechanisms in PCBA design is essential to block unauthorized access.
Hardware Trojan Horses also pose a silent yet profound threat. These sneaky modifications, made during manufacturing, can go almost unnoticed. To counteract this, it’s critical to partner with trustworthy suppliers and employ hardware authentication methods.
Consider working with a partner with a connected technology platform that keeps you in touch with your manufacturing process from start to finish. Moreover, work with a partner that employs robust security practices and can provide proof of such, such as ISO and ITAR certifications, or membership in the ERAI, an organization established to combat counterfeit electronics and high-risk components in the electronics industry. MacroFab holds these standards, and it is a member of ERAI.
Another challenge is the theft of PCBAs after robot deployment, especially those containing valuable intellectual property. Consider using tamper-evident seals or protective enclosures if you will be installing robotics in an unsupervised area.
Want to read more about designing PCBAs for robotics? Read Reshaping Robotics: How PCBA Advances Drive Tomorrow's Autonomous Soutions now.
Conclusion: Embracing the Challenge
The realm of PCBA design for autonomous robots transcends the traditional electrical engineer’s domain. While electrical fundamentals remain the cornerstone, navigating the complexities of this field necessitates venturing beyond the confines of the schematic. It’s a world where understanding environmental stresses, mitigating biological influences, and safeguarding against security vulnerabilities are equally critical.
By embracing these unique challenges and fostering a spirit of relentless innovation, electrical engineers will become the architects of a new era in robotics. The future holds immense potential for these autonomous machines, with robust, adaptable PCBAs serving as their foundation.
Want to discuss this article with your peers? Head over to the Circuit Break Forum now.
Related Topics
How MacroFab Ensures Peak Production Quality for Modern Electronics
Discover how MacroFab ensures exceptional production quality for modern electronics, meeting the challenges of complexity and innovation with ease.
How to Shorten PCBA Production Lead Times with MacroFab
In the rapidly evolving electronics sector, extended production lead times are no longer tolerable, and minimizing these lead times is crucial for success.
How Companies Cut Electronics Production Costs
Companies face both direct and indirect costs, which can impact financial statements at various stages.
Need PCBAs for your robotic assembly?
Get an Instant Quote NowAbout MacroFab
MacroFab offers comprehensive manufacturing solutions, from your smallest prototyping orders to your largest production needs. Our factory network locations are strategically located across North America, ensuring that we have the flexibility to provide capacity when and where you need it most.
Experience the future of EMS manufacturing with our state-of-the-art technology platform and cutting-edge digital supply chain solutions. At MacroFab, we ensure that your electronics are produced faster, more efficiently, and with fewer logistic problems than ever before.
Take advantage of AI-enabled sourcing opportunities and employ expert teams who are connected through a user-friendly technology platform. Discover how streamlined electronics manufacturing can benefit your business by contacting us today.