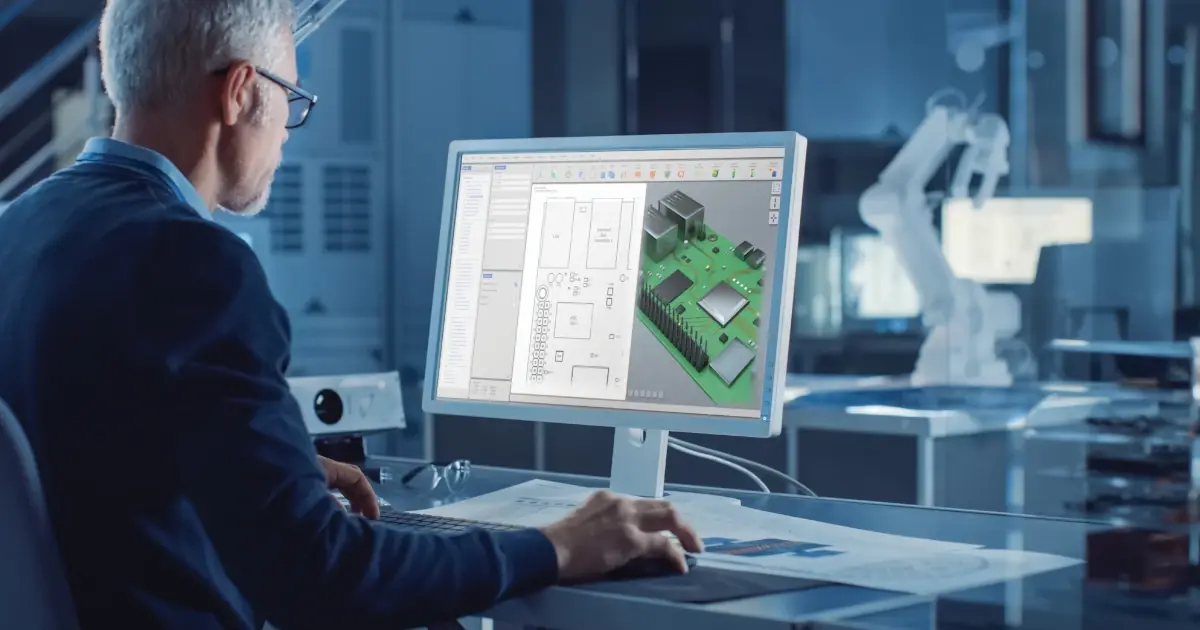
MacroFab Blog
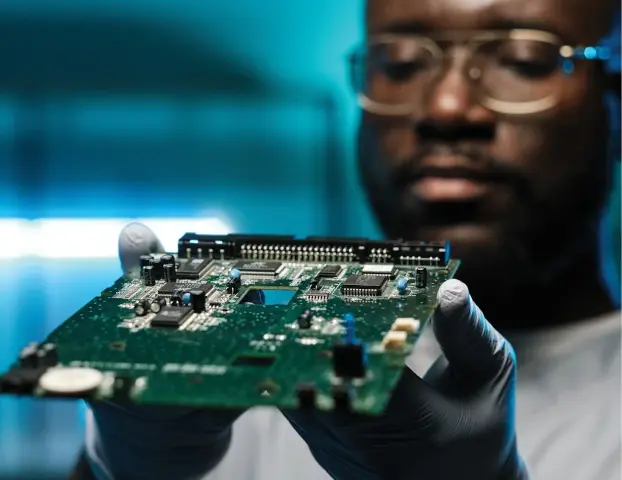
Designing electronic products requires a high degree of efficiency but must also meet the needs of an ever-more demanding target audience. This means that innovation and practicality are constantly competing. As a result, firms hoping to deliver a successful electronics product to market are continually seeking out new, cutting-edge solutions and faster ways to design.
When designing Printed Circuit Board Assemblies (PCBAs), engineers must strike a balance between this efficiency and competitiveness. However, the path to successful PCBA product development has its challenges. Companies, often navigating a labyrinth of obstacles requiring swift and astute decision-making, must identify and understand the primary impediments to PCBA product development.
The following are the five primary obstacles to effective PCBA product development and how to circumvent them.
Barrier #1 - Ineffective Teamwork
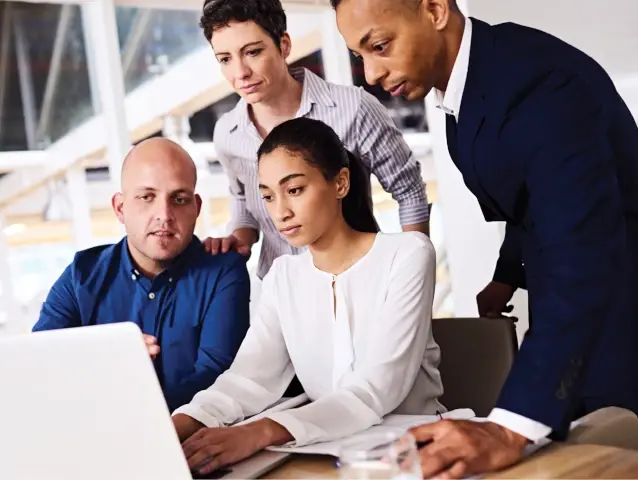
For PCBA projects to be successful, it is important to have a strong team at the company level. Communicating and cooperating effectively across departments is essential. When these are lacking, the consequences can be significant, leading to wasted time and ongoing disputes that hinder the progress of a PCBA product launch.
One effective strategy for promoting teamwork is to use early testing. Early testing can clarify expectations and identify potential issues, fostering open and ongoing communication at the outset while establishing baseline standards that must be met.
Moreover, this powerful tool saves time and money in PCBA projects when implemented correctly. Specifically, teams that utilize early testing can achieve a 25 percent reduction in development time and a 30 percent decrease in rework.
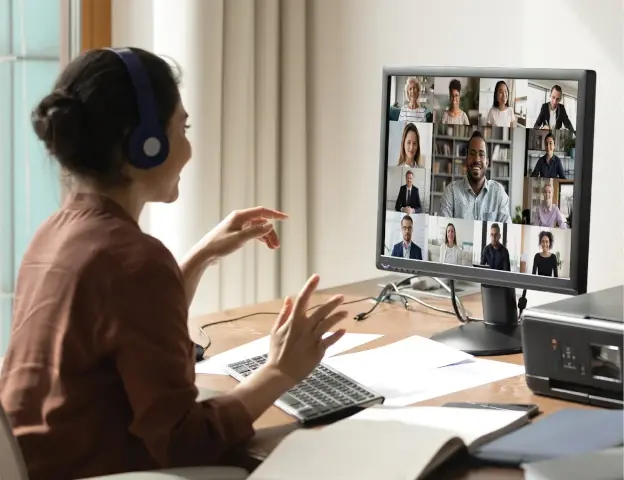
Open communication is the cornerstone of a collaborative and productive team environment, particularly when it comes to the success of PCBA projects. To foster open communication within the team, consider implementing the following measures:
- Establish Cross-Functional Meetings: Regular cross-functional meetings with a clear agenda and prepared documents help align goals, ensure productivity, and keep everyone informed on critical points under development.
- Use Collaboration Tools: Facilitate real-time communication with collaboration tools and file-sharing features to ensure all team members have access to resources and up-to-date documentation.
- Cultivate a Culture of Transparency: Create a culture of openness by encouraging team members to voice their concerns and ideas while promoting active listening and open dialogue.
Does your team constantly launch products behind schedule? Read What’s Holding Your Electronics Product Launch Back now.
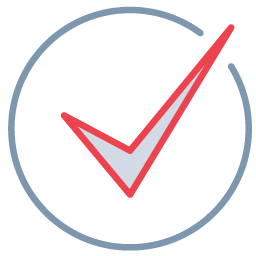
Checkpoint
Effective teams are built on open communication.
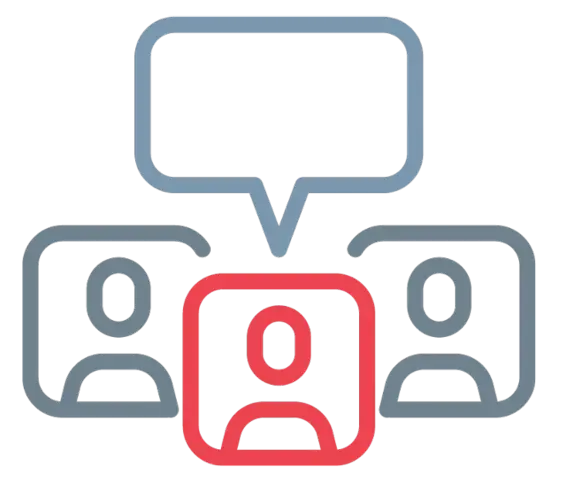
By implementing these measures, teams can work together seamlessly, minimize inefficiencies, and achieve success in their PCBA projects. In addition, open communication enables teams to navigate challenges effectively and fosters a positive and inclusive team environment.
Barrier #2 - The Costs of Delayed Testing
Undertaking testing too late in the process can lead to a high-cost burden and numerous complications. The discovery of errors near the end of a project may require substantial modifications that might have been more easily resolved at an earlier stage.
This scenario can become even more challenging if skilled members of the team have already moved on to other projects or–worse–left the organization. Replacing such professionals can cost more than twice their annual salary, representing a considerable financial impact. To avoid such scenarios, taking proactive measures is crucial.
To enhance and streamline the testing process, consider these approaches:
- Adopt a “shift-left” testing approach: This promotes early design-phase testing activities as opposed to waiting until later stages. By integrating testing into initial design processes, teams can identify and address issues promptly, leading to improved quality and reduced overall costs.
- Leverage simulation software: Simulation software can validate design performance before physical prototyping, and can provide invaluable feedback that will help your team detect potential flaws or design weaknesses as quickly as possible.
- Conduct iterative testing: Cyclical and repetitive testing minimizes the chance of encountering significant problems toward the end of a project.
Barrier #3 - Employee Churn:
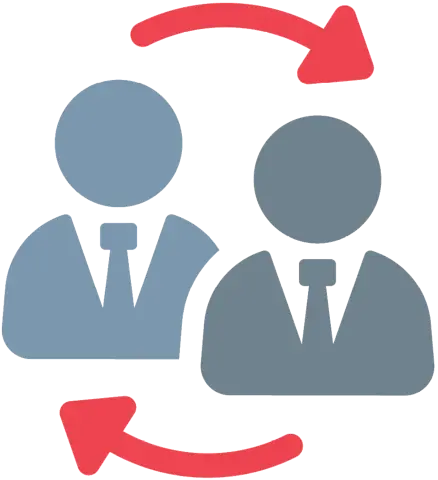
High employee turnover can significantly disrupt the PCBA product development process, leading to costly delays and declining project quality. The loss of experienced team members can create knowledge gaps, hinder collaboration, and increase training costs for new employees.
Churn can also be extremely costly. While replacing an unskilled worker may cost up to 20 percent of their annual salary, replacement costs can skyrocket to as much as 213% for highly skilled positions.
Data points illustrating the impact of employee churn on project timelines and quality include:
- Increased time and resources spent onboarding and training new employees
- Loss of institutional knowledge and expertise, leading to potential errors and inefficiencies
- Lower team morale and productivity due to constant team restructuring
To reduce employee churn and promote retention, consider implementing the following strategies. Provide competitive compensation and benefits as a first step. This involves not only offering competitive salaries but also a robust benefits package and clear pathways for professional development.
Secondly, cultivate a positive work environment. Keeping employees satisfied and motivated requires a supportive and inclusive workplace culture that promotes collaboration, recognition, and a healthy work-life balance.
Finally, prioritize the provision of growth opportunities. This can be achieved by encouraging employee development through continuous training, mentorship programs, and advancement opportunities.
The Work Institute’s 2020 Retention Report found that 76 percent of employee turnover is preventable through clearer communication, more opportunities for professional growth, or other management strategies. By addressing these issues, companies can reduce employee churn and thus improve the efficiency and quality of their PCBA product development projects. As companies in the industry struggle to retain knowledgeable employees, this becomes increasingly important.
Barrier #4 - The Risks of Unallocated Duties
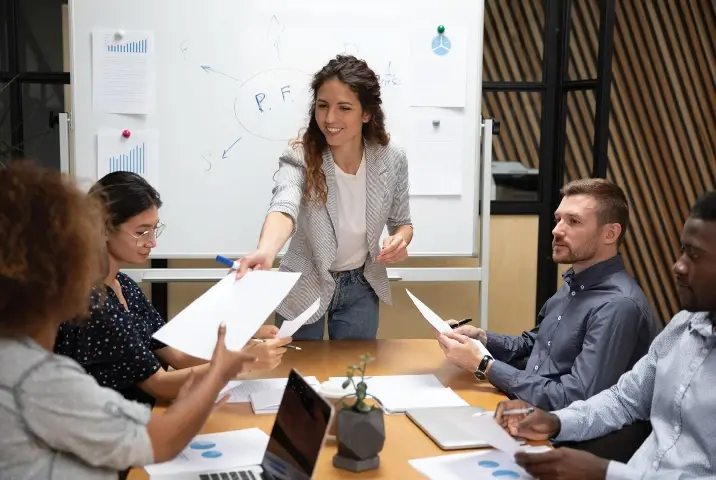
In the PCBA product development process, unclear roles and responsibilities can create a maze of confusion and delays. When task and milestone ownership is not properly designated, team members can operate in a state of uncertainty. This can result in inefficiencies and a lack of accountability, leading to critical tasks being overlooked. In extreme cases, this can cause missed deadlines and suboptimal project outcomes.
For instance, without a clear owner for the product design review process, teams may overlook critical considerations or make uninformed decisions, impacting the project’s quality and deliverability. Conversely, when responsibilities are clearly defined, team members can focus on their areas of expertise, leading to more effective collaboration and timely project completion.
To overcome this barrier, implement the following strategies that assign responsibility, establish clear communication, and ensure accountability:
- Define Clear Roles at the Project’s Outset: Develop a detailed project charter that outlines each team member’s roles, responsibilities, and authority. The charter should include expectations regarding communication, collaboration, and decision-making to promote transparency and accountability.
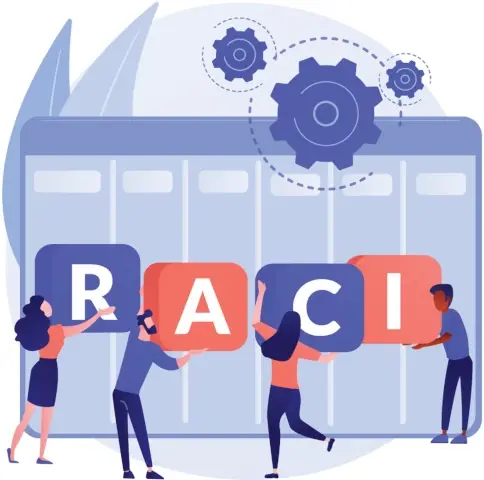
- Leverage RACI Matrix for Project Activities: The RACI (Responsible, Accountable, Consulted, Informed)matrix is an effective tool to assign ownership for each activity or deliverable in the project. By assigning an owner to every task and aligning stakeholders on their roles, the matrix can help clarify responsibilities.
- Implement Regular Status Updates: Digital collaboration platforms can be utilized to allow team members to provide progress updates and address challenges. Asynchronous communication should be fostered to promote knowledge-sharing and collaborative problem-solving. Encouraging open communication is acritical first step.
By adopting these strategies, teams can establish clarity in roles, enhance collaboration, and ensure accountability in their PCBA product development projects, leading to smoother execution and a higher likelihood of success.
Barrier #5 - Ignoring the End Goal
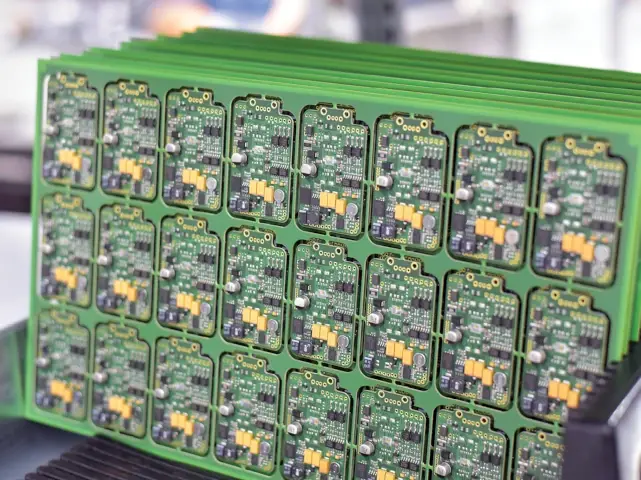
Unclear or unrealistic requirements can be a stumbling block in the PCBA product development process. Poorly defined requirements can lead to misaligned expectations, costly rework, and delays in product delivery. For example, ambiguous specifications for component tolerances may result in incompatible parts, necessitating redesign and additional costs.
To avoid this, it is crucial to define clear and realistic requirements that align with the project’s end goals. By starting with the end in mind, teams can create a well-defined roadmap for product development and minimize the risk of costly errors.
Consider the following strategies for defining precise requirements and ensuring stakeholder alignment:
- Conduct Collaborative Requirements Gathering: Identify and gather requirements from all stakeholders, including product owners, engineers, and manufacturers. Requirements must be specific, measurable, achievable, relevant, and time-bound (SMART).
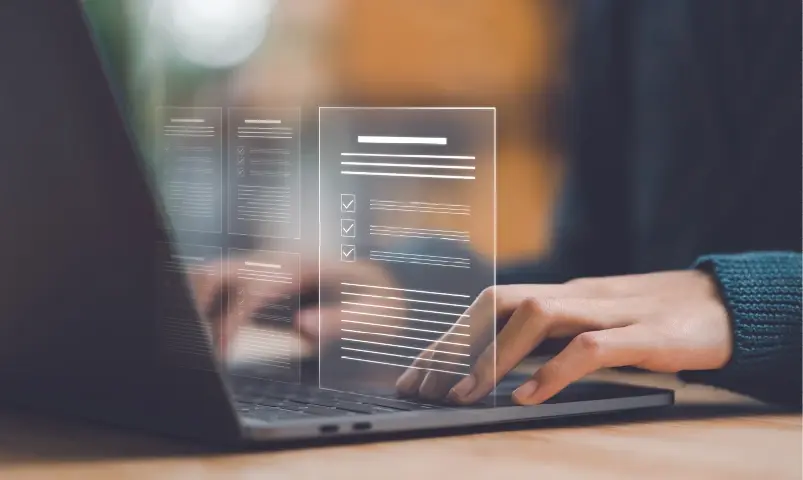
- Document and Review Requirements: Establish a formal requirements document for all stakeholders and conduct thorough reviews to ensure that the document is accurate and complete.
- Implement Change Management Processes: During the project, establish a straightforward change management process to handle requirements changes. Communicate changes transparently and promptly to all stakeholders to minimize disruptions.
By defining clear and realistic requirements and maintaining alignment among stakeholders, teams can confidently and efficiently confidently and efficiently confidently and efficiently navigate the PCBA product development process, ultimately delivering high-quality products that meet the intended objectives.
Want more tips to launch your product faster? Read Design Faster, Improve Quality: Tips for PCBA Development now.
Conclusion
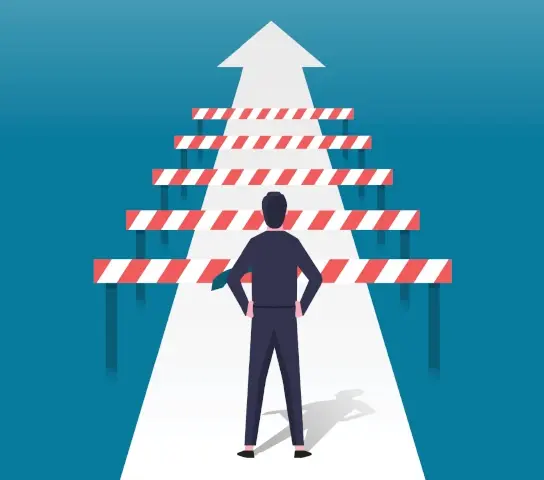
Efficient PCBA product development, though an arduous journey, is well within reach. Teams can overcome challenges and succeed by addressing the five barriers to efficient PCBA product development and implementing the respective solutions.
Overcoming barriers to efficient PCBA product development involves fostering cross-functional collaboration, integrating early and iterative testing in the development stages, and establishing clear roles and accountability within the team.
Enhancements such as defining roles in the project charter, using a RACI matrix, and regular status updates streamline execution. Lastly, starting the project with a clear end goal, achieved through collaborative requirements gathering, documentation review, and change management processes, ensures alignment toward the shared objective.
By employing these product development strategies, teams can facilitate a smoother transition of their product from the initial concept to physical production, all the way through to the product launch. By adhering to these strategies, teams can significantly reduce potential issues or setbacks at each stage of the development process.
Related Topics
Struggling with Inflexible PCBA Manufacturing? MacroFab's Got Your Back.
Many electronics designers struggle with systems that demand complete data and specific formats upfront. Wouldn't it be great if there was a better way?
Fab Insights: HASL vs ENIG
Choosing the right surface finish for a PCBA can be tricky. HASL and ENIG differ in their methods of coating printed circuit boards.
How Do QFN Packages Compare to Other Surface Mount ICs?
This article aims to arm electrical engineers and PCBA designers with comprehensive insights into the QFN package.
Discover How MacroFab Will Improve Your Efficiency
Upgrade your electronics manufacturing process by leveraging a technology platform that offers differentiated services at every stage, from prototyping to mass production.
About MacroFab
MacroFab offers comprehensive manufacturing solutions, from your smallest prototyping orders to your largest production needs. Our factory network locations are strategically located across North America, ensuring that we have the flexibility to provide capacity when and where you need it most.
Experience the future of EMS manufacturing with our state-of-the-art technology platform and cutting-edge digital supply chain solutions. At MacroFab, we ensure that your electronics are produced faster, more efficiently, and with fewer logistic problems than ever before.
Take advantage of AI-enabled sourcing opportunities and employ expert teams who are connected through a user-friendly technology platform. Discover how streamlined electronics manufacturing can benefit your business by contacting us today.