Related Topics
Removing The Barriers
Electronic bench equipment for hardware development. Stephen and Parker dive into a high level of what kind of equipment is needed to outfit a bench.
Scott Hinson of Pecan Street Inc.
Scott Hinson of Pecan Street Inc. joins Parker and Stephen to discuss the most important of topics. Is its Pa-kawn or Pee-can?
The Expert
Design for Testing means enabling your product to be tested easier or quicker. But what about the documentation and implementation of the testing?
Other Resources
Circuit Break Podcast
Webinars
Videos
Tour MacroFab's ITAR-Compliant Facility
June 10, 2020, Episode #228
William Mathewson
- An entrepreneur, electrical engineer, and user experience designer for his company William Mathewson Devices otherwise known as WMD
- Began WMD in 2007
- Designed over seventy products that inspire artists and sound designers throughout the music industry
Starting A Hardware Manufacturing Company
- The name WMD
- How did William arrive at deciding to start WMD?
- What do y’all do at WMD?
- The story? How did it all start?
- Pedals to modular synth
- Products
- Services
- The story? How did it all start?
- Manufacturing Business
- Hardware is Hard
- How did this begin?
- How did you build this service?
- Best thing about it all
- Worst thing about it all
- War stories
- The future?
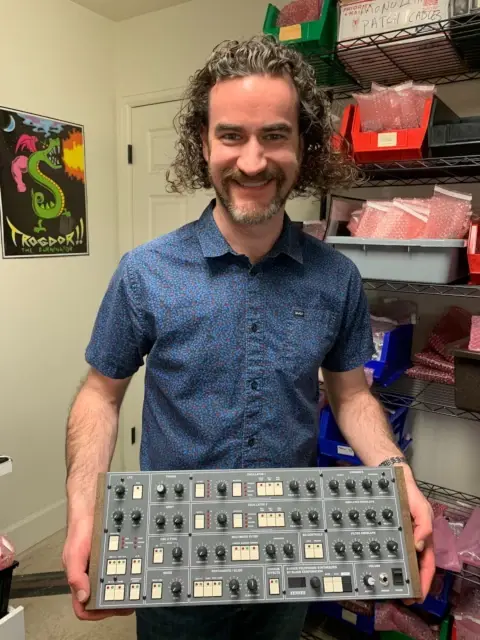
William Mathewson of WMDevices. WMD manufactures all there Eurorack and Pedals in-house in Denver, Colorado, USA.
About the Hosts
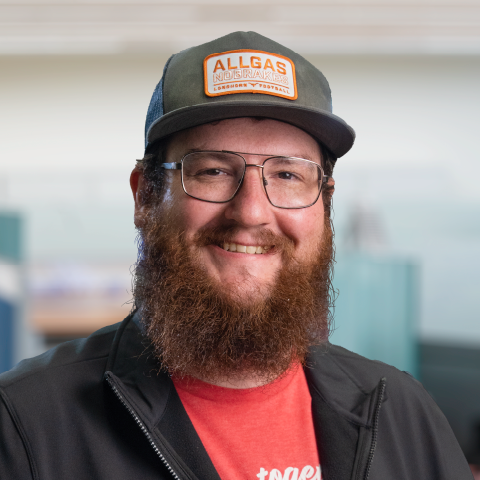
Parker Dillmann
Parker is an Electrical Engineer with backgrounds in Embedded System Design and Digital Signal Processing. He got his start in 2005 by hacking Nintendo consoles into portable gaming units. The following year he designed and produced an Atari 2600 video mod to allow the Atari to display a crisp, RF fuzz free picture on newer TVs. Over a thousand Atari video mods where produced by Parker from 2006 to 2011 and the mod is still made by other enthusiasts in the Atari community.
In 2006, Parker enrolled at The University of Texas at Austin as a Petroleum Engineer. After realizing electronics was his passion he switched majors in 2007 to Electrical and Computer Engineering. Following his previous background in making the Atari 2600 video mod, Parker decided to take more board layout classes and circuit design classes. Other areas of study include robotics, microcontroller theory and design, FPGA development with VHDL and Verilog, and image and signal processing with DSPs. In 2010, Parker won a Ti sponsored Launchpad programming and design contest that was held by the IEEE CS chapter at the University. Parker graduated with a BS in Electrical and Computer Engineering in the Spring of 2012.
In the Summer of 2012, Parker was hired on as an Electrical Engineer at Dynamic Perception to design and prototype new electronic products. Here, Parker learned about full product development cycles and honed his board layout skills. Seeing the difficulties in managing operations and FCC/CE compliance testing, Parker thought there had to be a better way for small electronic companies to get their product out in customer's hands.
Parker also runs the blog, longhornengineer.com, where he posts his personal projects, technical guides, and appnotes about board layout design and components.
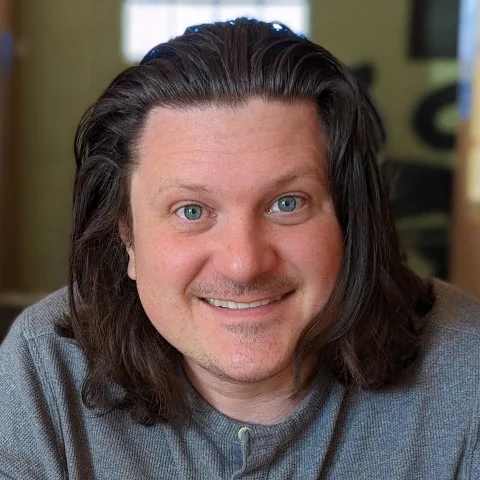
Stephen Kraig
Stephen Kraig is a component engineer working in the aerospace industry. He has applied his electrical engineering knowledge in a variety of contexts previously, including oil and gas, contract manufacturing, audio electronic repair, and synthesizer design. A graduate of Texas A&M, Stephen has lived his adult life in the Houston, TX, and Denver, CO, areas.
Stephen has never said no to a project. From building guitar amps (starting when he was 17) to designing and building his own CNC table to fine-tuning the mineral composition of the water he uses to brew beer, he thrives on testing, experimentation, and problem-solving. Tune into the podcast to learn more about the wacky stuff Stephen gets up to.
Special thanks to whixr over at Tymkrs for the intro and outro!
Related Podcasts
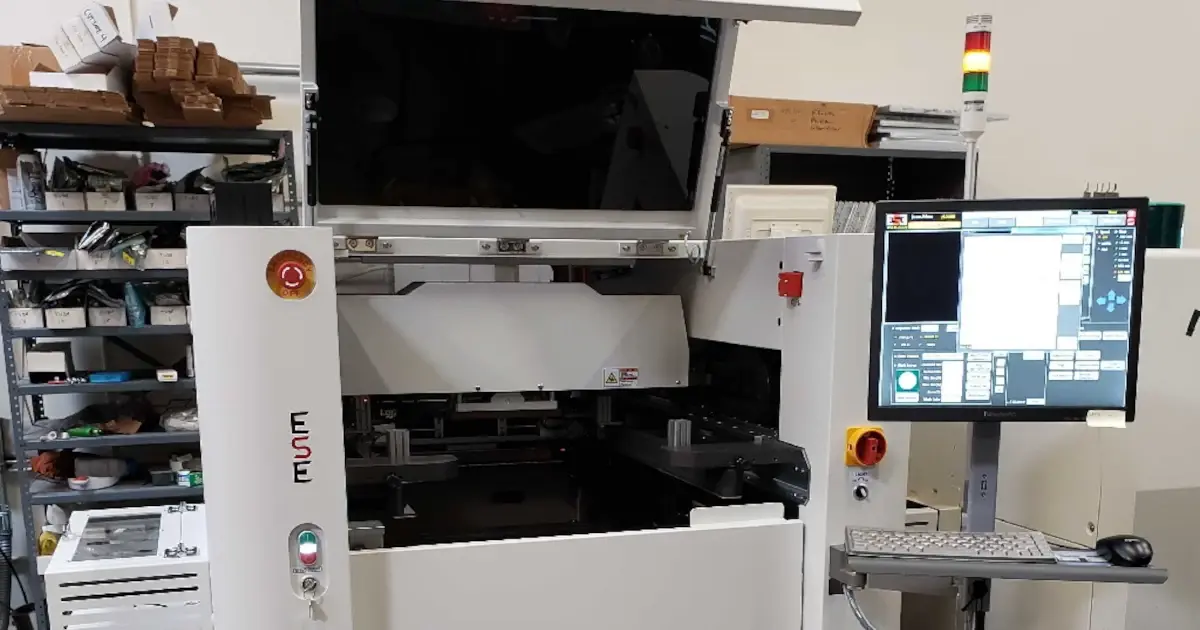
Viciously Different Creams
Does anyone actually use the metric sizing for chip components? The ole' 0603 metric and 0201 imperial chip component switcheroo on this episode.
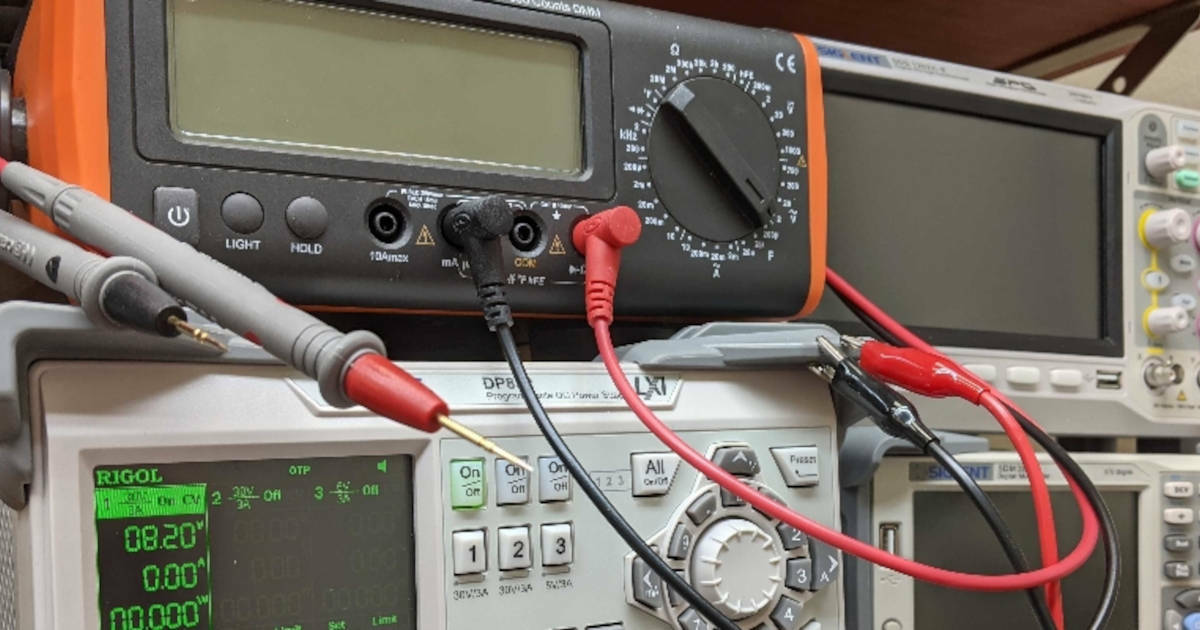
Removing The Barriers
Electronic bench equipment for hardware development. Stephen and Parker dive into a high level of what kind of equipment is needed to outfit a bench.
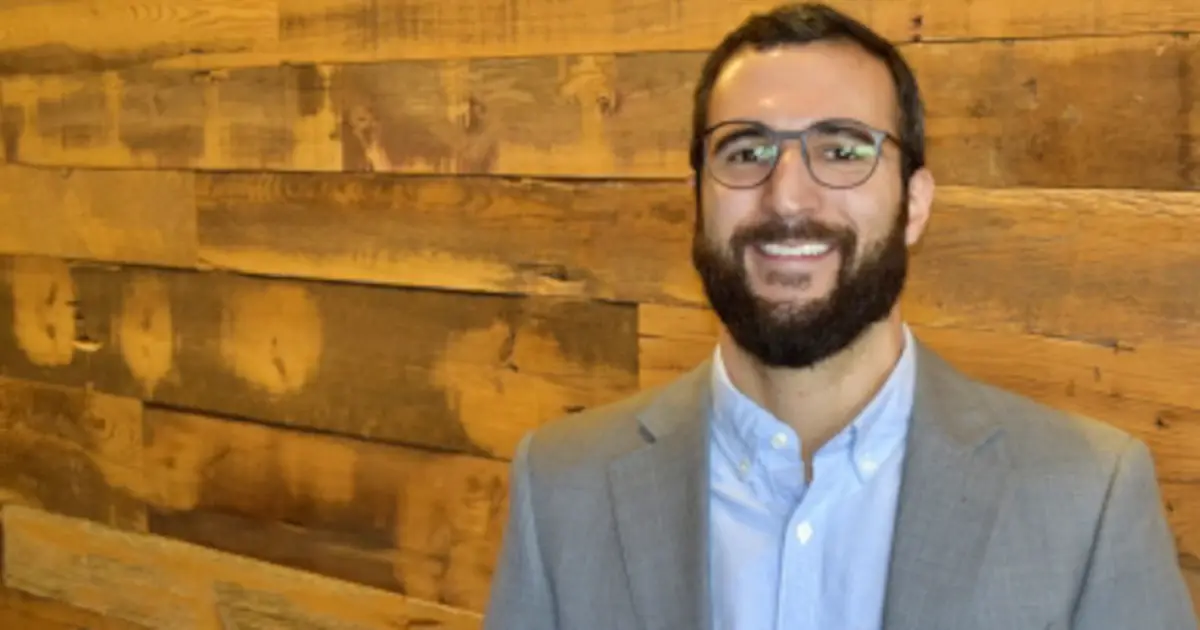
Not Even My Final Form: Jeff Garoon on Industrial Design
Jeff Garoon joins Parker and Stephen to discuss the design, testing, and regulations of creating low volume Industrial IoT devices.
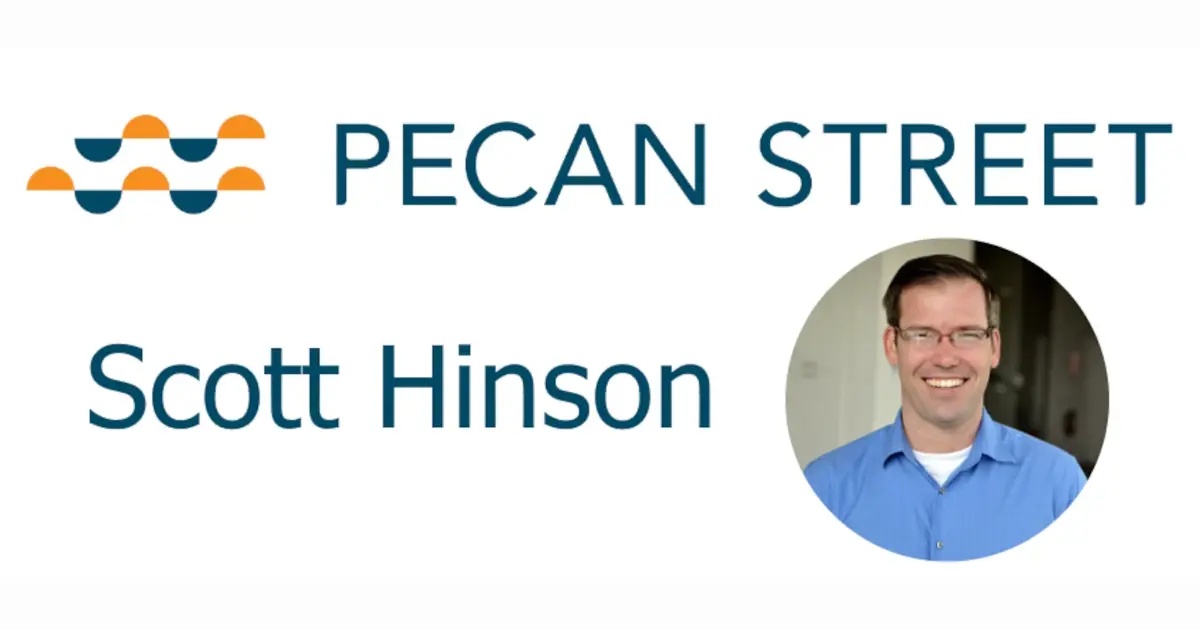
Scott Hinson of Pecan Street Inc.
Scott Hinson of Pecan Street Inc. joins Parker and Stephen to discuss the most important of topics. Is its Pa-kawn or Pee-can?
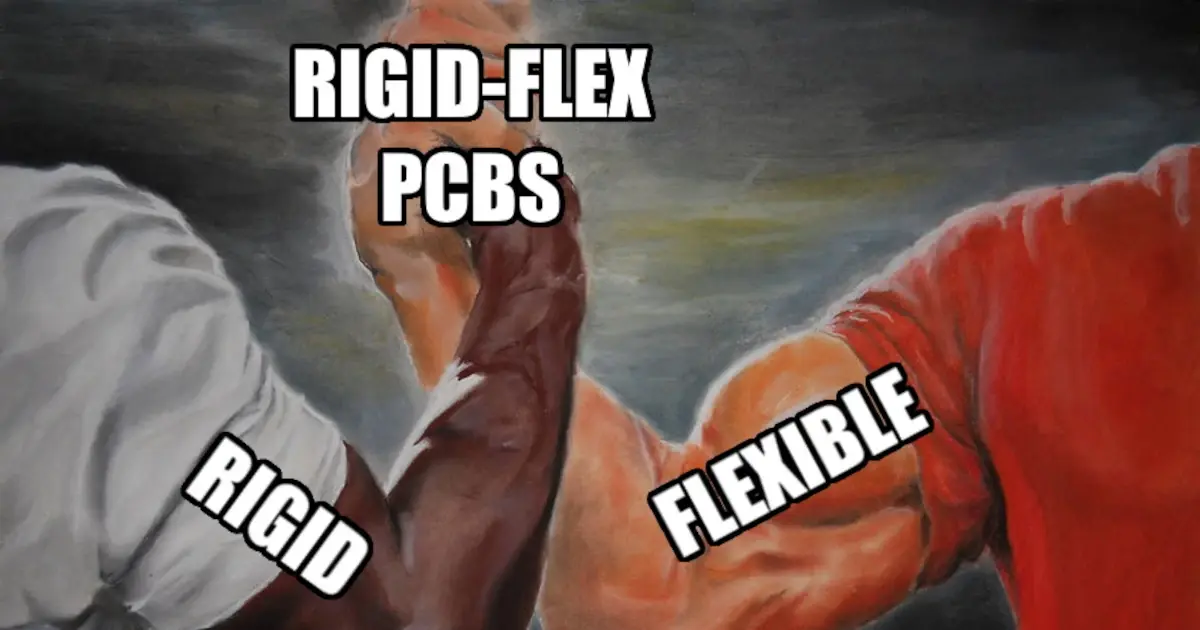
Flex PCB Primers
Stephen gives the MEP an introduction on Flex and Rigid-Flex PCB assemblies while Parker looks at an automotive Analog Devices application note.
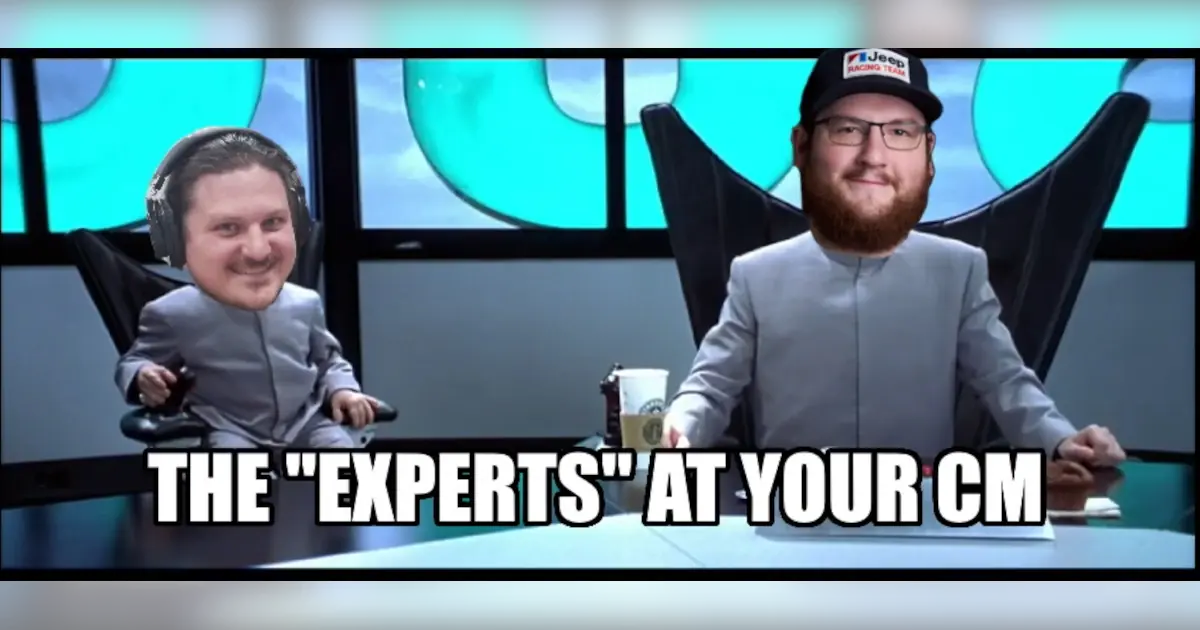
The Expert
Design for Testing means enabling your product to be tested easier or quicker. But what about the documentation and implementation of the testing?
About MacroFab
MacroFab offers comprehensive manufacturing solutions, from your smallest prototyping orders to your largest production needs. Our factory network locations are strategically located across North America, ensuring that we have the flexibility to provide capacity when and where you need it most.
Experience the future of EMS manufacturing with our state-of-the-art technology platform and cutting-edge digital supply chain solutions. At MacroFab, we ensure that your electronics are produced faster, more efficiently, and with fewer logistic problems than ever before.
Take advantage of AI-enabled sourcing opportunities and employ expert teams who are connected through a user-friendly technology platform. Discover how streamlined electronics manufacturing can benefit your business by contacting us today.