Related Topics
Conductive Cuisine
We'll explore an in-depth study conducted by Seth Jenkins, Neil LaTourette, and Brendan Liverman on how boiling time affects hot dog conductivity.
Wanting to be a Wizard - Matt Brown
Matt Brown, shares his career insights, including his experiences working at Tesla and on personal projects like the land speed car and the off-road Viper.
Exploring the Arctic Through Art and Technology with Cy Keener
Cy Keener's work includes a range of data-based efforts to visualize diverse phenomena including ice, wind, rain, and ocean waves.
Other Resources
Circuit Break Podcast
Webinars
Videos
Tour MacroFab's ITAR-Compliant Facility
July 24, 2019, Episode #182
- Has nearly three decades of experience in government and commercial electromagnetic research and design
- Prior to establishing the Wireless Research Center in 2010, Dr. Hayes worked for Sony Ericsson Mobile Communications and Lockheed Martin
- At Sony Ericsson Mobile Communications (USA) Inc., Dr.Hayes provided global technical leadership in the Technology and Research organization with contributions to handset antenna design, technology, and radiated performance optimization
- At Lockheed Martin (formerly Lockheed Missiles and Space Co.), Dr. Hayes supported research and development efforts for space-based, phased array application
- Experience encompasses electromagnetic theory, bioelectromagnetics, antenna design, RF circuit analysis, and material engineering
- Participated in the development of international standards for OTA, HAC, and SAR evaluation which includes IEEE, IEC, CTIA, and C63 standards
- Senior staff engineering consultant at the Wireless Research Center
- Has over 15 years of experience in RF and antenna engineering in the commercial, defense and medical device markets and has developed products from early concept to production
- Has held technical positions at RFMD, HTC, Sony Ericsson and Harris.
- What is it?
- 501 C (3)
- Accreditations
- A2LA (American Association for Laboratory Accreditation)
- CTIA (Cellular Telecommunications Industry Association)
- Verizon Authorized Independent Test Lab for OTA radiated performance
- OTA Testing
- FCC Pre-certification
- Lots of engineers looking for this
- LTE (Long-Term Evolution)
- WCDMA (Wide-Band Code-Division Multiple Access)
- Total Radiated Power
- Total Isotropic Sensitivity
- FCC Pre-certification
- Engineering Services
- Antenna and RF design
- Simulation and Analysis
- Field Testing and Propagation Modeling
- Engineering and Development
- First time tips and tricks for engineers developing their first product.
- What do they need to test for?
- Estimated costs
- What to bring
- What is the result? What do you get?
Visit our Public Slack Channel and join the conversation in between episodes!
About the Hosts
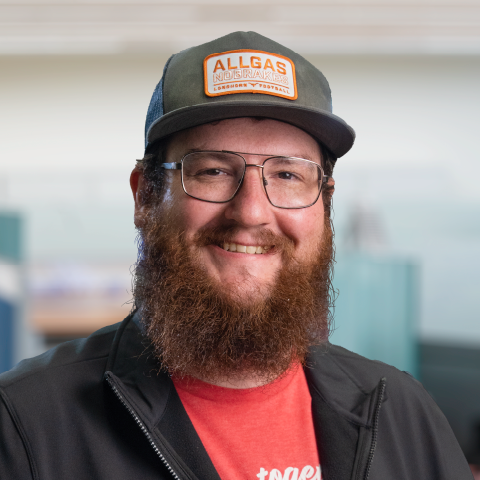
Parker Dillmann
Parker is an Electrical Engineer with backgrounds in Embedded System Design and Digital Signal Processing. He got his start in 2005 by hacking Nintendo consoles into portable gaming units. The following year he designed and produced an Atari 2600 video mod to allow the Atari to display a crisp, RF fuzz free picture on newer TVs. Over a thousand Atari video mods where produced by Parker from 2006 to 2011 and the mod is still made by other enthusiasts in the Atari community.
In 2006, Parker enrolled at The University of Texas at Austin as a Petroleum Engineer. After realizing electronics was his passion he switched majors in 2007 to Electrical and Computer Engineering. Following his previous background in making the Atari 2600 video mod, Parker decided to take more board layout classes and circuit design classes. Other areas of study include robotics, microcontroller theory and design, FPGA development with VHDL and Verilog, and image and signal processing with DSPs. In 2010, Parker won a Ti sponsored Launchpad programming and design contest that was held by the IEEE CS chapter at the University. Parker graduated with a BS in Electrical and Computer Engineering in the Spring of 2012.
In the Summer of 2012, Parker was hired on as an Electrical Engineer at Dynamic Perception to design and prototype new electronic products. Here, Parker learned about full product development cycles and honed his board layout skills. Seeing the difficulties in managing operations and FCC/CE compliance testing, Parker thought there had to be a better way for small electronic companies to get their product out in customer's hands.
Parker also runs the blog, longhornengineer.com, where he posts his personal projects, technical guides, and appnotes about board layout design and components.
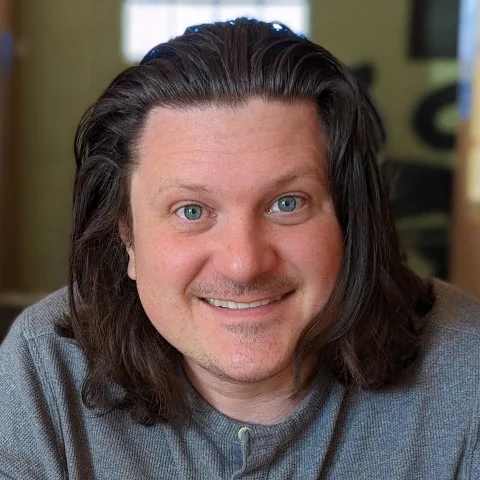
Stephen Kraig
Stephen Kraig is a component engineer working in the aerospace industry. He has applied his electrical engineering knowledge in a variety of contexts previously, including oil and gas, contract manufacturing, audio electronic repair, and synthesizer design. A graduate of Texas A&M, Stephen has lived his adult life in the Houston, TX, and Denver, CO, areas.
Stephen has never said no to a project. From building guitar amps (starting when he was 17) to designing and building his own CNC table to fine-tuning the mineral composition of the water he uses to brew beer, he thrives on testing, experimentation, and problem-solving. Tune into the podcast to learn more about the wacky stuff Stephen gets up to.
Special thanks to whixr over at Tymkrs for the intro and outro!