Related Topics
Modern College Education with Derek Fronek
Derek Fronek is a current engineering student at Purdue University. We dive into how education has changed with COVID and a decade of automation.
Other Resources
Circuit Break Podcast
Webinars
Videos
Tour MacroFab's ITAR-Compliant Facility
November 14, 2018, Episode #146
Podcast Notes
- John Waidner
- Electronics Engineer with a background in Logic design, analog circuit, system integration and testing
- Currently John is a mentor for the TechHOUNDS and volunteers for the Boy Scouts of America
- Derek Fronek
- High school student from Carmel High School
- Part of the Carmel High School robotics team the TechHOUNDS
- TechHOUNDS
- What are the TechHOUNDS and how did you start?
- Leadership? Who leads the group?
- Divisions
- Robot Ops
- Programming/Electrical
- Construction
- Information Technology
- Public Relations
- How do you handle the overlap between divisions?
- Derek – What division are you most involved with?
- John – How involved are you in the process?
- What is FIRST (For Inspiration and Recognition of Science and Technology)
- Who can be a part of FIRST?
- How to get involved
- Funding?
- Competing in FRC (First Robotics Competition)
- What are the competitions?
- How does your team prepare for them?
- Who gets to go?
- Who gets to drive the bot?
- The TechHOUNDS youtube channel has lots of videos of the robot and competitions the group has been in
- What is next for the TechHOUNDS?
Visit our Slack Channel and join the conversation in between episodes and please review us, wherever you listen (PodcastAddict, iTunes). It helps this show stay visible and helps new listeners find us.
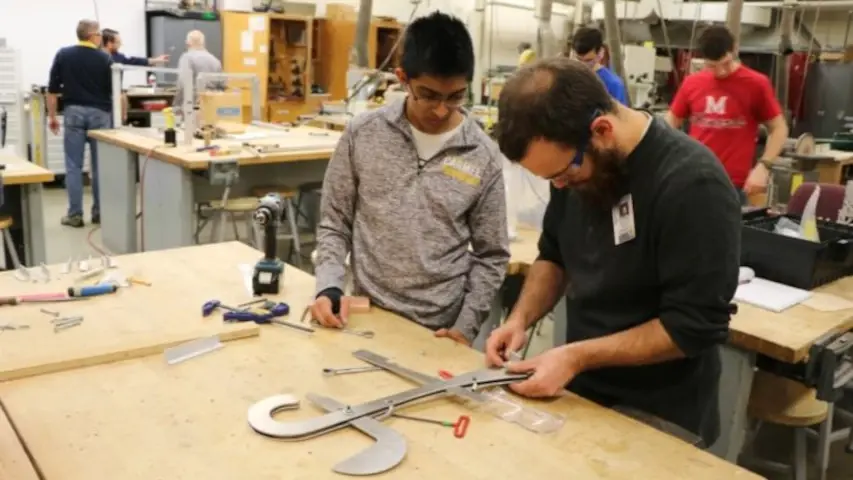
Carmel High School students mid build in 2018.
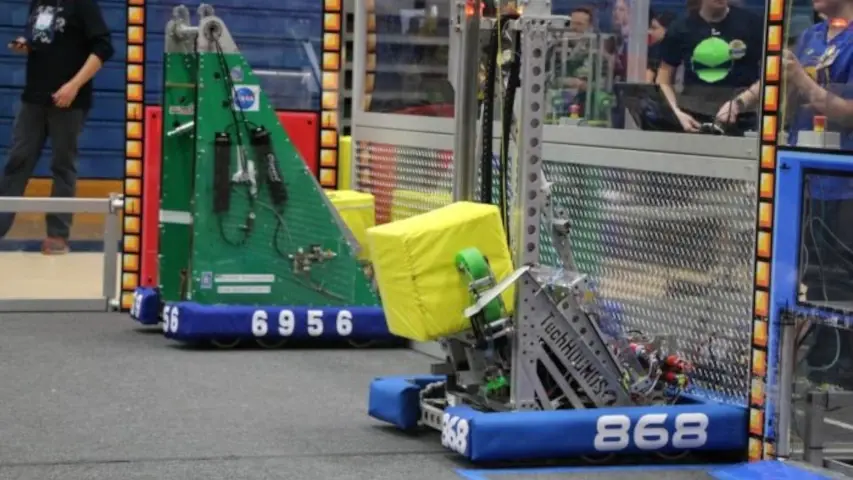
TechHOUNDS 868 robot in the ready position right before a match.
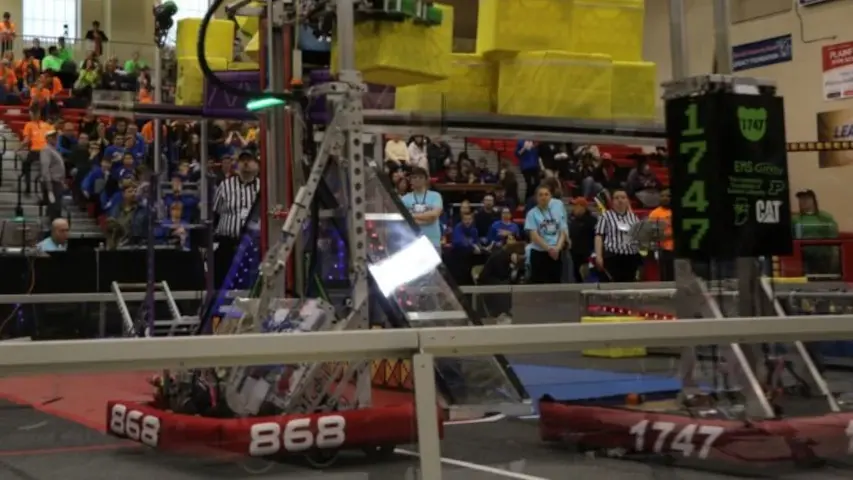
The TechHOUNDS robot lifting the crates onto the scale.
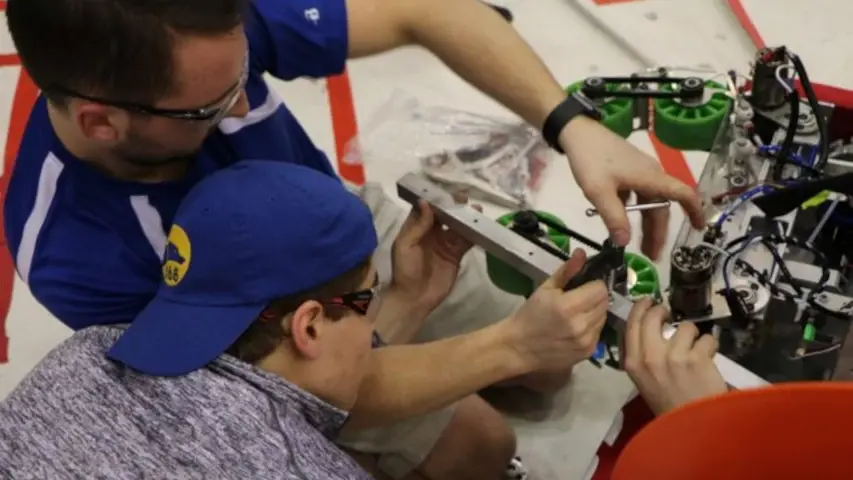
Fixing the crate intake on the robot between matches.
About the Hosts
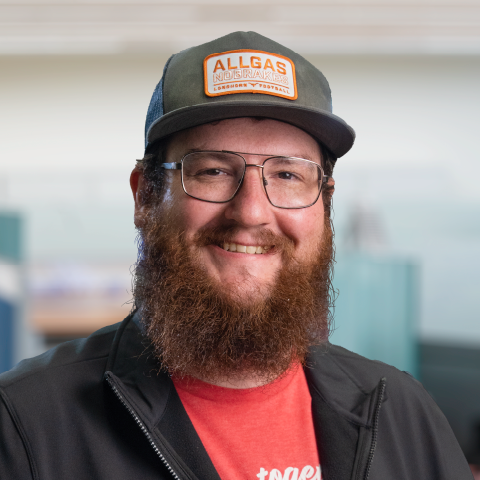
Parker Dillmann
Parker is an Electrical Engineer with backgrounds in Embedded System Design and Digital Signal Processing. He got his start in 2005 by hacking Nintendo consoles into portable gaming units. The following year he designed and produced an Atari 2600 video mod to allow the Atari to display a crisp, RF fuzz free picture on newer TVs. Over a thousand Atari video mods where produced by Parker from 2006 to 2011 and the mod is still made by other enthusiasts in the Atari community.
In 2006, Parker enrolled at The University of Texas at Austin as a Petroleum Engineer. After realizing electronics was his passion he switched majors in 2007 to Electrical and Computer Engineering. Following his previous background in making the Atari 2600 video mod, Parker decided to take more board layout classes and circuit design classes. Other areas of study include robotics, microcontroller theory and design, FPGA development with VHDL and Verilog, and image and signal processing with DSPs. In 2010, Parker won a Ti sponsored Launchpad programming and design contest that was held by the IEEE CS chapter at the University. Parker graduated with a BS in Electrical and Computer Engineering in the Spring of 2012.
In the Summer of 2012, Parker was hired on as an Electrical Engineer at Dynamic Perception to design and prototype new electronic products. Here, Parker learned about full product development cycles and honed his board layout skills. Seeing the difficulties in managing operations and FCC/CE compliance testing, Parker thought there had to be a better way for small electronic companies to get their product out in customer's hands.
Parker also runs the blog, longhornengineer.com, where he posts his personal projects, technical guides, and appnotes about board layout design and components.
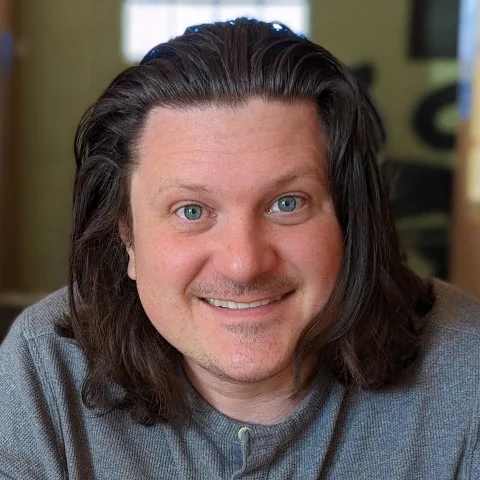
Stephen Kraig
Stephen Kraig is a component engineer working in the aerospace industry. He has applied his electrical engineering knowledge in a variety of contexts previously, including oil and gas, contract manufacturing, audio electronic repair, and synthesizer design. A graduate of Texas A&M, Stephen has lived his adult life in the Houston, TX, and Denver, CO, areas.
Stephen has never said no to a project. From building guitar amps (starting when he was 17) to designing and building his own CNC table to fine-tuning the mineral composition of the water he uses to brew beer, he thrives on testing, experimentation, and problem-solving. Tune into the podcast to learn more about the wacky stuff Stephen gets up to.
Special thanks to whixr over at Tymkrs for the intro and outro!
Related Podcasts
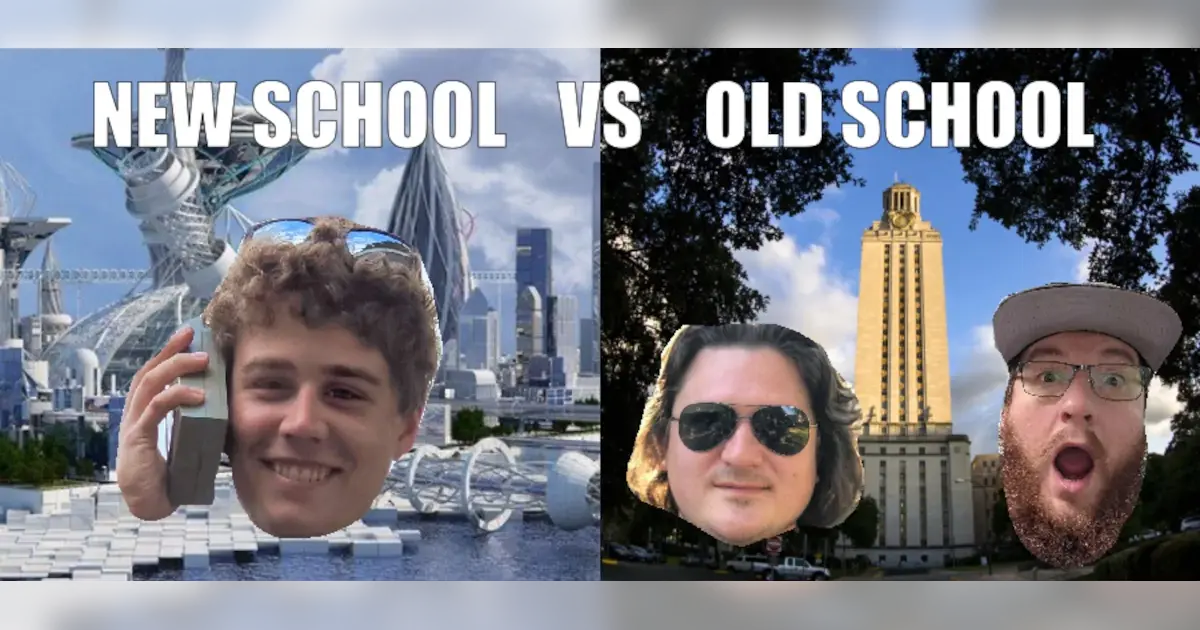
Modern College Education with Derek Fronek
Derek Fronek is a current engineering student at Purdue University. We dive into how education has changed with COVID and a decade of automation.
About MacroFab
MacroFab offers comprehensive manufacturing solutions, from your smallest prototyping orders to your largest production needs. Our factory network locations are strategically located across North America, ensuring that we have the flexibility to provide capacity when and where you need it most.
Experience the future of EMS manufacturing with our state-of-the-art technology platform and cutting-edge digital supply chain solutions. At MacroFab, we ensure that your electronics are produced faster, more efficiently, and with fewer logistic problems than ever before.
Take advantage of AI-enabled sourcing opportunities and employ expert teams who are connected through a user-friendly technology platform. Discover how streamlined electronics manufacturing can benefit your business by contacting us today.