Related Topics
The Name Will Arrive
The quest for the right connector for a project! The right of passage for any hardware electrical engineer starts with a connector catalog.
Connector Catalogs
This is the last installment of Stephen's 'Adventures in Injection Molding'. We are going to recap the entire two year sage and close the book on it.
AVRDUDE All The Way Down
The Jeep Prop Fan project rides again! Well some iteration of it at least. Lets design an open source PCM (Power Control Module) for automotive apps!
Other Resources
Circuit Break Podcast
Webinars
Videos
Tour MacroFab's ITAR-Compliant Facility
May 13, 2020, Episode #224
Stephen
- DC Heating and Thermal Testing
- A low voltage moderate current linear power supply
- 12.6V dc @ 0.55A 6.93W
- LM2940T-12.0 LDO
- TIP42 bootstrap transistor to share the load
- 12V @ 2A transformer supplies ~16.2vdc with 200mV ripple
- ~2W of heat to be handled
- Shooting for about 250mW in the regulator and the transistor then the rest will get dumped in some resistors
- PCB heatsinking
- Diptrace 4.0 is finally here!
- Snapping and aligning items
- Circles and arcs actually have a center now…
- Paste and Mask layers are finally visible
- Pad angles other than 0 and 90 are now available in the pattern editor
- One button for removing silkscreen from pads
- Progressive searching for components instead of the seizure it used to be
- Export options now can export all the manufacturing files as a single zip
- Teardrops!
Parker
- Wagoneer Engine Work
- Timing cover
- Water pump
- Timing chain
- Distributor gear
- Distributor camshaft gear
- Harmonic Balancer
- All the gaskets
- Radiator next
- Dash Cluster
- Timing cover
- Fixing a wine chiller
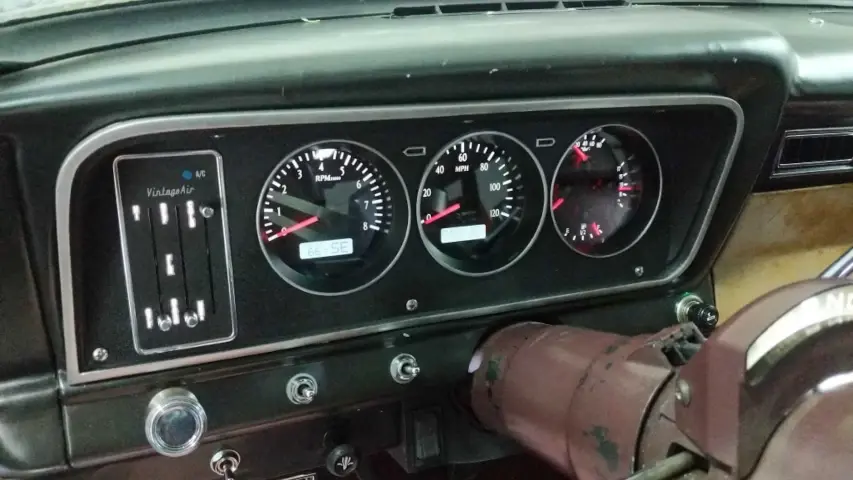
Refinished dash Parker restored and installed new gauges into.
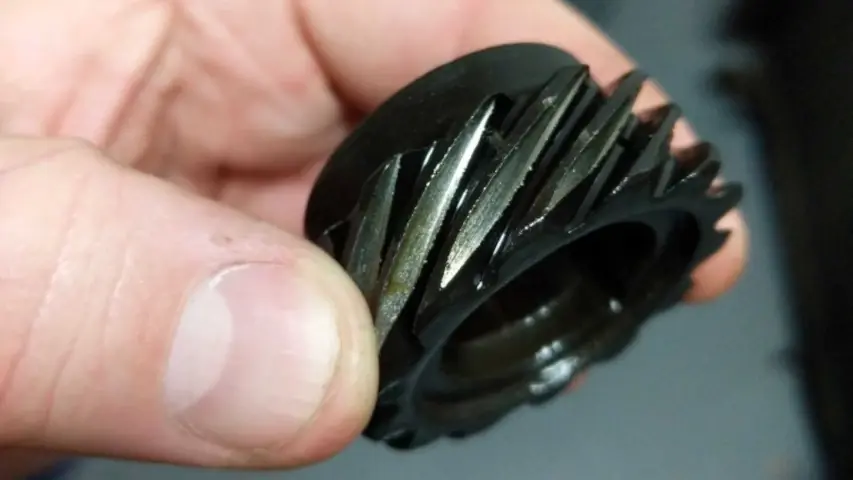
Gears are not supposed to be shiny and sharp! Cam distributor gear is all chewed up.
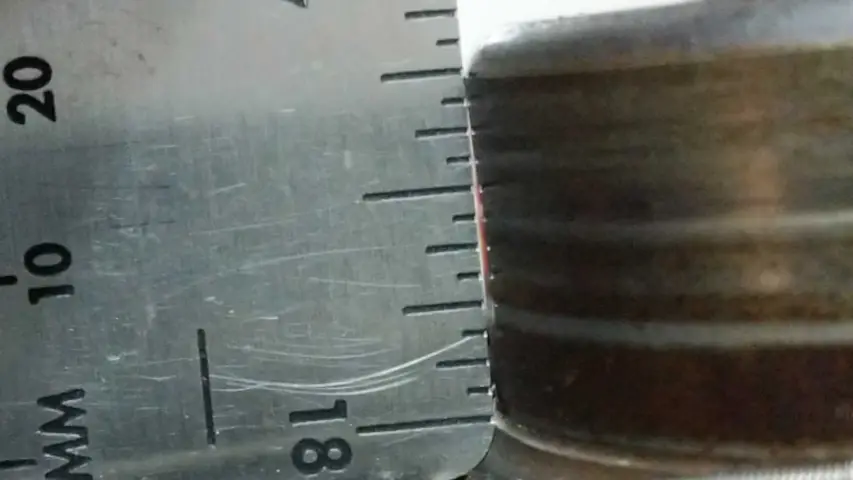
Oil seal surface on the harmonic balancer. Supposed to be flat…not dished and grooved.
About the Hosts
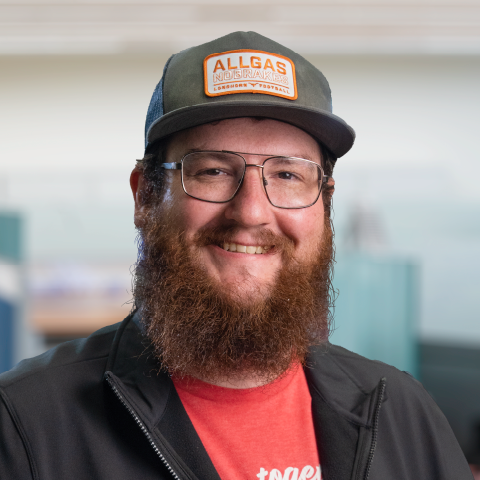
Parker Dillmann
Parker is an Electrical Engineer with backgrounds in Embedded System Design and Digital Signal Processing. He got his start in 2005 by hacking Nintendo consoles into portable gaming units. The following year he designed and produced an Atari 2600 video mod to allow the Atari to display a crisp, RF fuzz free picture on newer TVs. Over a thousand Atari video mods where produced by Parker from 2006 to 2011 and the mod is still made by other enthusiasts in the Atari community.
In 2006, Parker enrolled at The University of Texas at Austin as a Petroleum Engineer. After realizing electronics was his passion he switched majors in 2007 to Electrical and Computer Engineering. Following his previous background in making the Atari 2600 video mod, Parker decided to take more board layout classes and circuit design classes. Other areas of study include robotics, microcontroller theory and design, FPGA development with VHDL and Verilog, and image and signal processing with DSPs. In 2010, Parker won a Ti sponsored Launchpad programming and design contest that was held by the IEEE CS chapter at the University. Parker graduated with a BS in Electrical and Computer Engineering in the Spring of 2012.
In the Summer of 2012, Parker was hired on as an Electrical Engineer at Dynamic Perception to design and prototype new electronic products. Here, Parker learned about full product development cycles and honed his board layout skills. Seeing the difficulties in managing operations and FCC/CE compliance testing, Parker thought there had to be a better way for small electronic companies to get their product out in customer's hands.
Parker also runs the blog, longhornengineer.com, where he posts his personal projects, technical guides, and appnotes about board layout design and components.
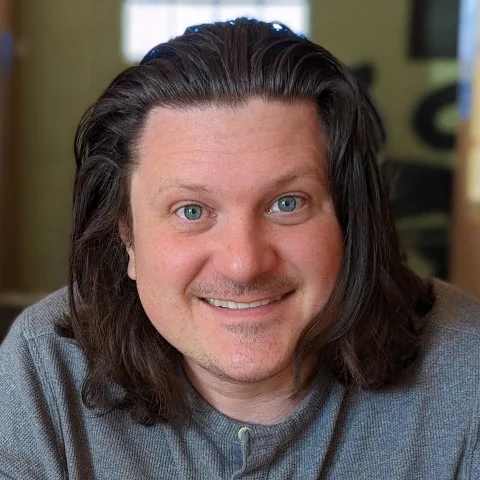
Stephen Kraig
Stephen Kraig is a component engineer working in the aerospace industry. He has applied his electrical engineering knowledge in a variety of contexts previously, including oil and gas, contract manufacturing, audio electronic repair, and synthesizer design. A graduate of Texas A&M, Stephen has lived his adult life in the Houston, TX, and Denver, CO, areas.
Stephen has never said no to a project. From building guitar amps (starting when he was 17) to designing and building his own CNC table to fine-tuning the mineral composition of the water he uses to brew beer, he thrives on testing, experimentation, and problem-solving. Tune into the podcast to learn more about the wacky stuff Stephen gets up to.
Special thanks to whixr over at Tymkrs for the intro and outro!
Related Podcasts
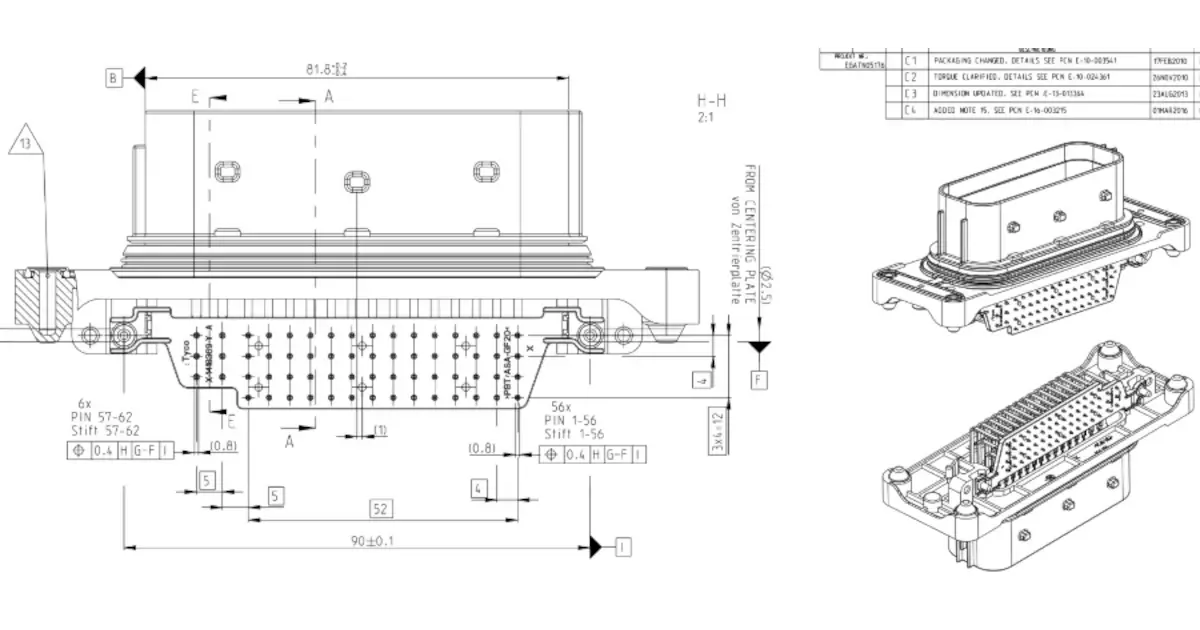
The Name Will Arrive
The quest for the right connector for a project! The right of passage for any hardware electrical engineer starts with a connector catalog.
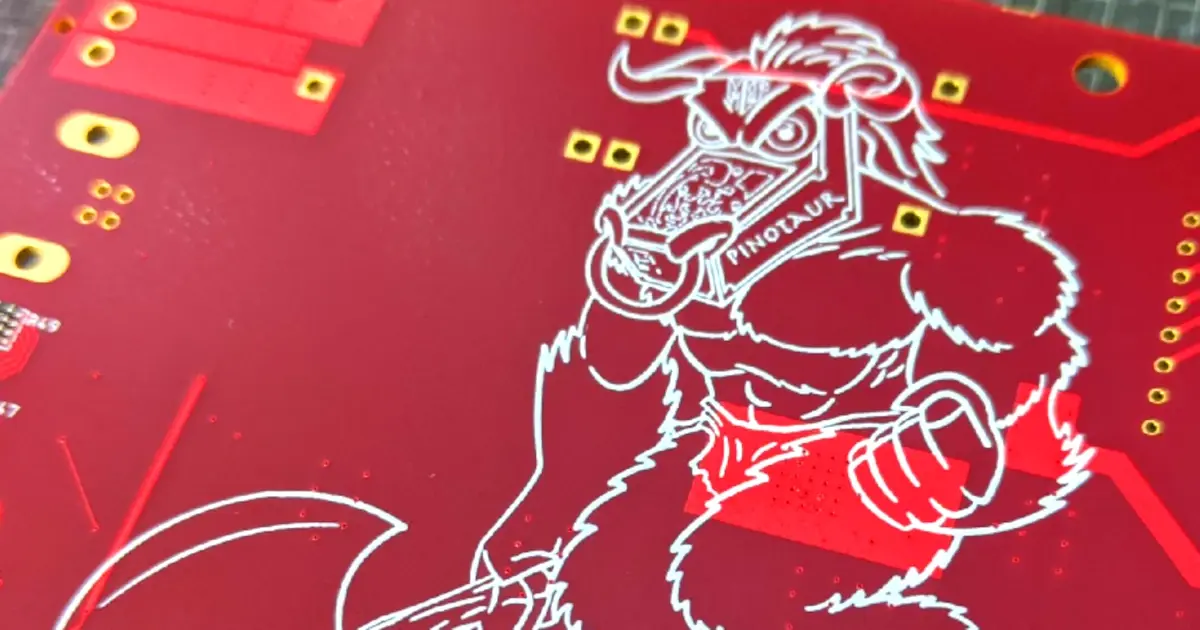
Illuminati Moment
Is there a statue of limitations on open source hardware projects? This week, Stephen and Parker dive into what open source means for both of them.
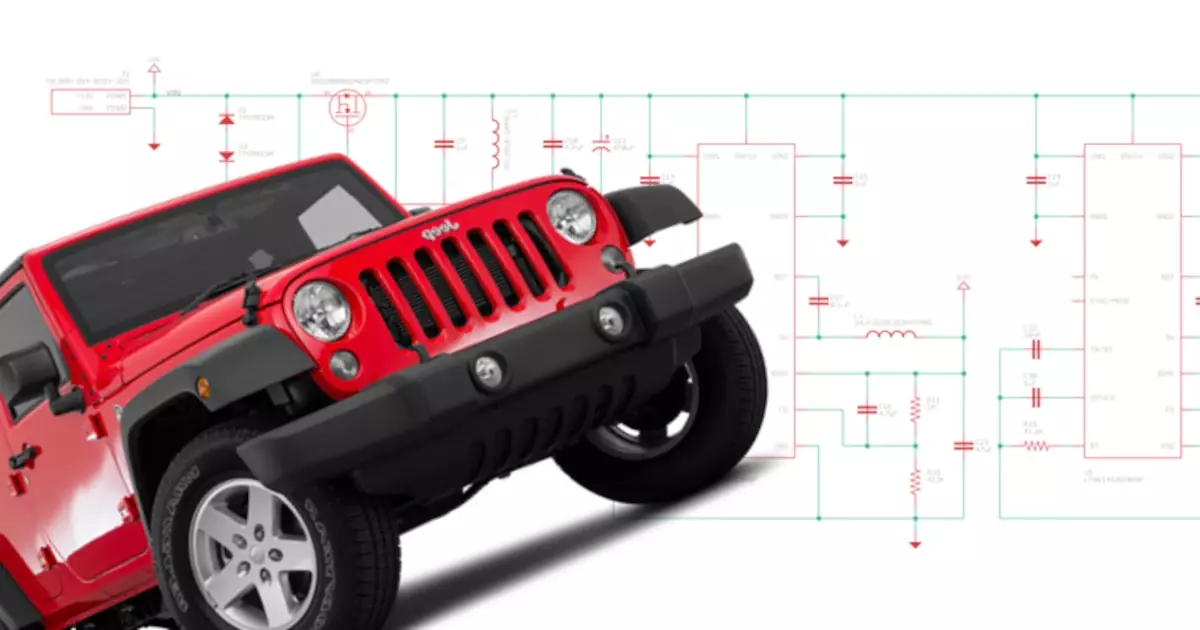
AVRDUDE All The Way Down
The Jeep Prop Fan project rides again! Well some iteration of it at least. Lets design an open source PCM (Power Control Module) for automotive apps!
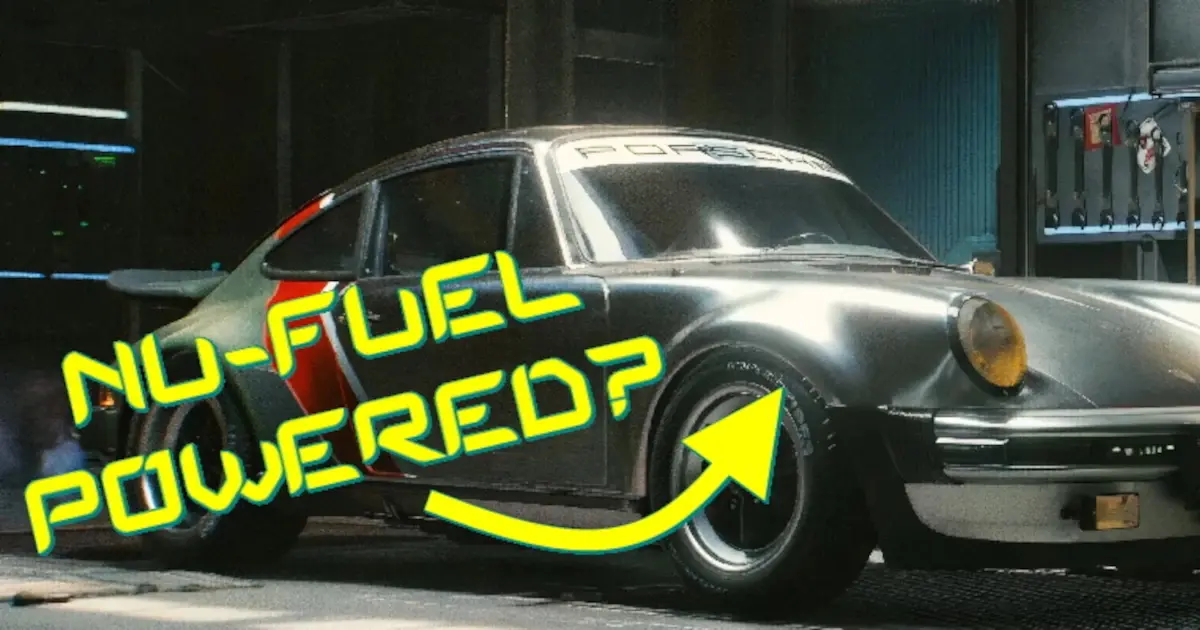
NuFuel and Gas Classic
Parker and Stephen discover new EDA tool features in both Eagle and Diptrace! The Auto industry is now waking up to a new tech order of the world.
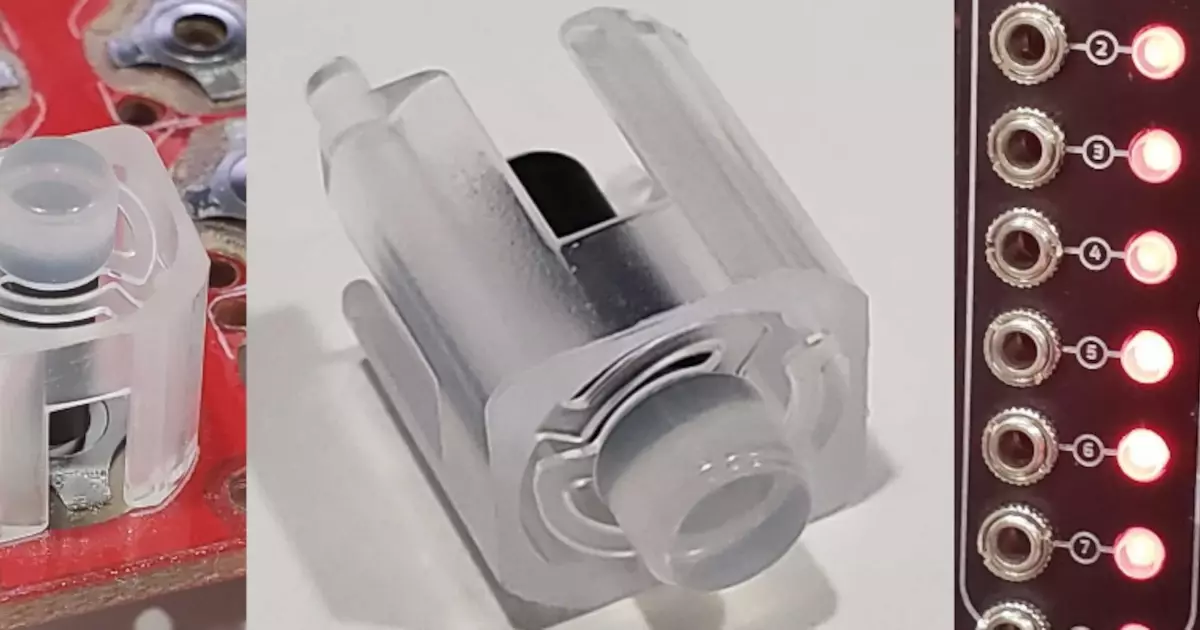
Connector Catalogs
This is the last installment of Stephen's 'Adventures in Injection Molding'. We are going to recap the entire two year sage and close the book on it.
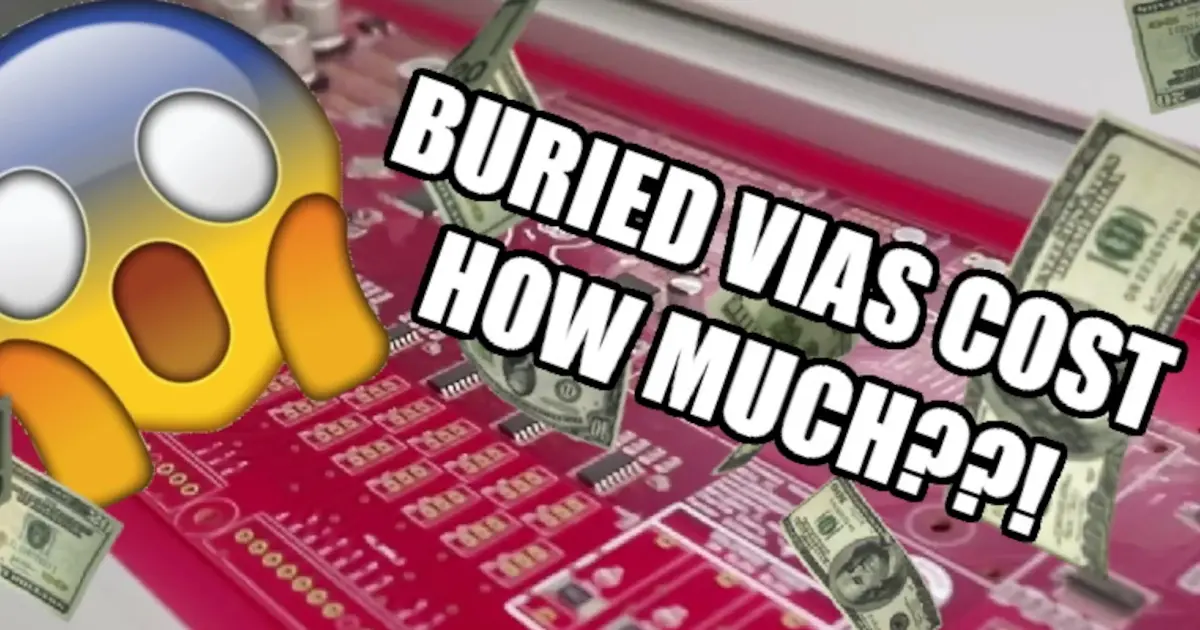
Avoid The Extremes
Controlling PCB costs of your next product is all about avoiding the extremes of the manufacturing specifications. Don't let your EDA tool fool you!
About MacroFab
MacroFab offers comprehensive manufacturing solutions, from your smallest prototyping orders to your largest production needs. Our factory network locations are strategically located across North America, ensuring that we have the flexibility to provide capacity when and where you need it most.
Experience the future of EMS manufacturing with our state-of-the-art technology platform and cutting-edge digital supply chain solutions. At MacroFab, we ensure that your electronics are produced faster, more efficiently, and with fewer logistic problems than ever before.
Take advantage of AI-enabled sourcing opportunities and employ expert teams who are connected through a user-friendly technology platform. Discover how streamlined electronics manufacturing can benefit your business by contacting us today.