Related Topics
Entangled Steam
Parker and Stephen dive into the world of batteries, sparked by the BetaVolt BV100's claim of a 50-year lifespan.
Laser Cutting Tolerancing
They may be known for being electrical engineers but on this episode, Parker and Stephen dig into the more mechanical aspects of their current projects
Current Conscience Comparator
How low can the power consumption of the Cat Feeder Unreminder go? Parker and Stephen discuss leakage current on this episode of the podcast!
Other Resources
Circuit Break Podcast
Webinars
Videos
Tour MacroFab's ITAR-Compliant Facility
September 16, 2020, Episode #242
Parker
- Battery charger and maintainer died
- Took all my batteries with it
- Company is replacing the unit
- Nothing looks particularly wrong with the PCB Assembly besides it being gross
- SF1565SG
- Current Mode PWM Controller
- FQPF12N60C
- Fet used in the PWM Controller
- HT46R004 HolTek MCU
- Cost Effective?
- Cat Feeder Unreminder
- Ordered a breakout board for the AEM10941
- Super Caps SCCS30B106PRB
- 10F @ 2.7VDC
- Solar Panel AM-1816CA
- 84µA at peak power
- This is specced at 200lx
- Will this be enough?
- LTC2956 draws 0.8μA
- LEDs at 40μA a piece
- Total draw when Cat Feed Indicator is on is 40.8μA
- 5F x (4.5V-3.6V) / 0.0000608 = 74,013 seconds -> 20 and a half hours!
Stephen
- Magnetics
- Transformers arrived!
- Be specific with what you ask for and ask questions. I almost got bit with dimensional issues
- Diy Tag connect
- Made a pogo pin test connector
- Mill-Max 0955-0-15-20-71-14-11-0 Pogo pins with solder cup on back
- Using FR4 as mechanical supports
- Designing a Pawl system to clasp the pcb
- Next Revision
- Make the landing pads bigger
- Add something for strain relief
- Move the pins slightly down for more spring
- Add more anti rotation pins
About the Hosts
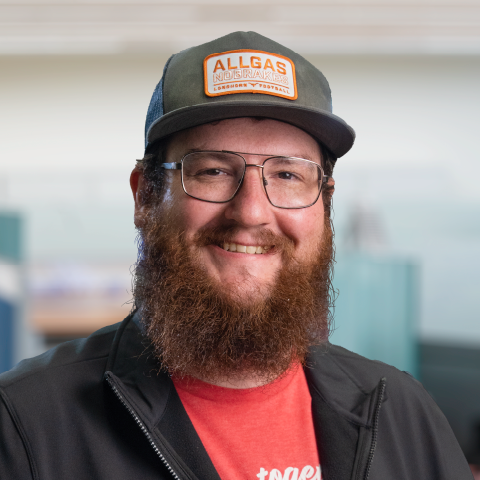
Parker Dillmann
Parker is an Electrical Engineer with backgrounds in Embedded System Design and Digital Signal Processing. He got his start in 2005 by hacking Nintendo consoles into portable gaming units. The following year he designed and produced an Atari 2600 video mod to allow the Atari to display a crisp, RF fuzz free picture on newer TVs. Over a thousand Atari video mods where produced by Parker from 2006 to 2011 and the mod is still made by other enthusiasts in the Atari community.
In 2006, Parker enrolled at The University of Texas at Austin as a Petroleum Engineer. After realizing electronics was his passion he switched majors in 2007 to Electrical and Computer Engineering. Following his previous background in making the Atari 2600 video mod, Parker decided to take more board layout classes and circuit design classes. Other areas of study include robotics, microcontroller theory and design, FPGA development with VHDL and Verilog, and image and signal processing with DSPs. In 2010, Parker won a Ti sponsored Launchpad programming and design contest that was held by the IEEE CS chapter at the University. Parker graduated with a BS in Electrical and Computer Engineering in the Spring of 2012.
In the Summer of 2012, Parker was hired on as an Electrical Engineer at Dynamic Perception to design and prototype new electronic products. Here, Parker learned about full product development cycles and honed his board layout skills. Seeing the difficulties in managing operations and FCC/CE compliance testing, Parker thought there had to be a better way for small electronic companies to get their product out in customer's hands.
Parker also runs the blog, longhornengineer.com, where he posts his personal projects, technical guides, and appnotes about board layout design and components.
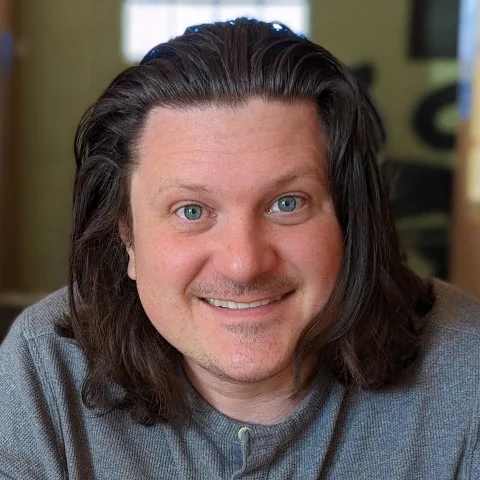
Stephen Kraig
Stephen Kraig is a component engineer working in the aerospace industry. He has applied his electrical engineering knowledge in a variety of contexts previously, including oil and gas, contract manufacturing, audio electronic repair, and synthesizer design. A graduate of Texas A&M, Stephen has lived his adult life in the Houston, TX, and Denver, CO, areas.
Stephen has never said no to a project. From building guitar amps (starting when he was 17) to designing and building his own CNC table to fine-tuning the mineral composition of the water he uses to brew beer, he thrives on testing, experimentation, and problem-solving. Tune into the podcast to learn more about the wacky stuff Stephen gets up to.
Special thanks to whixr over at Tymkrs for the intro and outro!
Related Podcasts
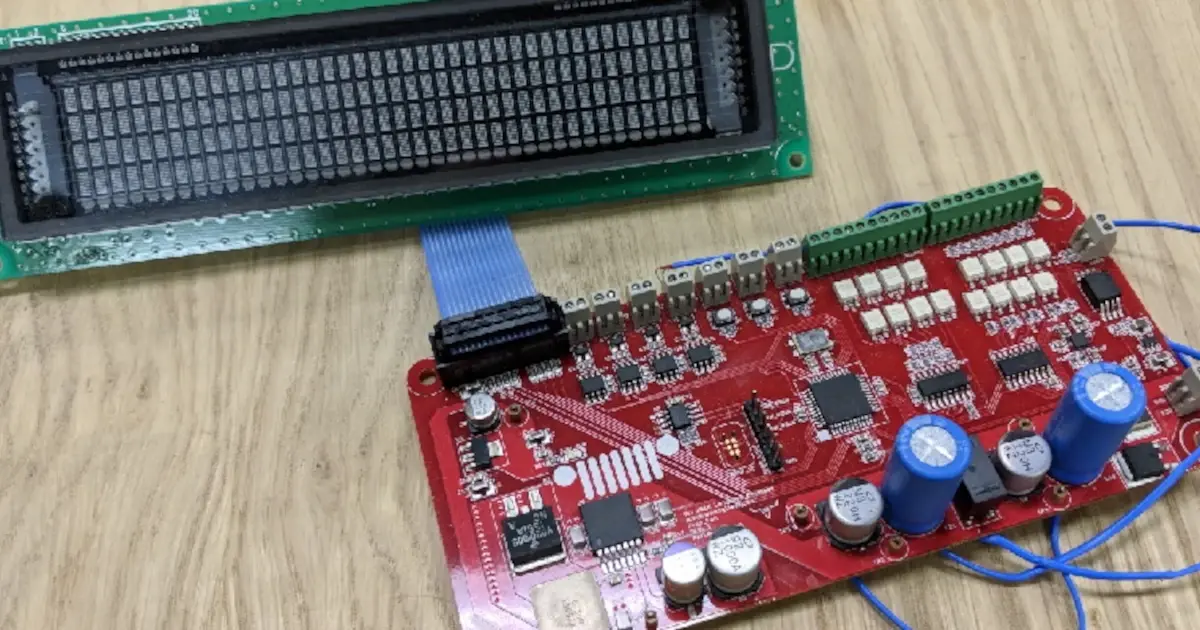
Color Clashing Chip Consolidation
What is the worst thing about the Analog Devices and Linear Technologies merger? The incompatible color schemes of course.
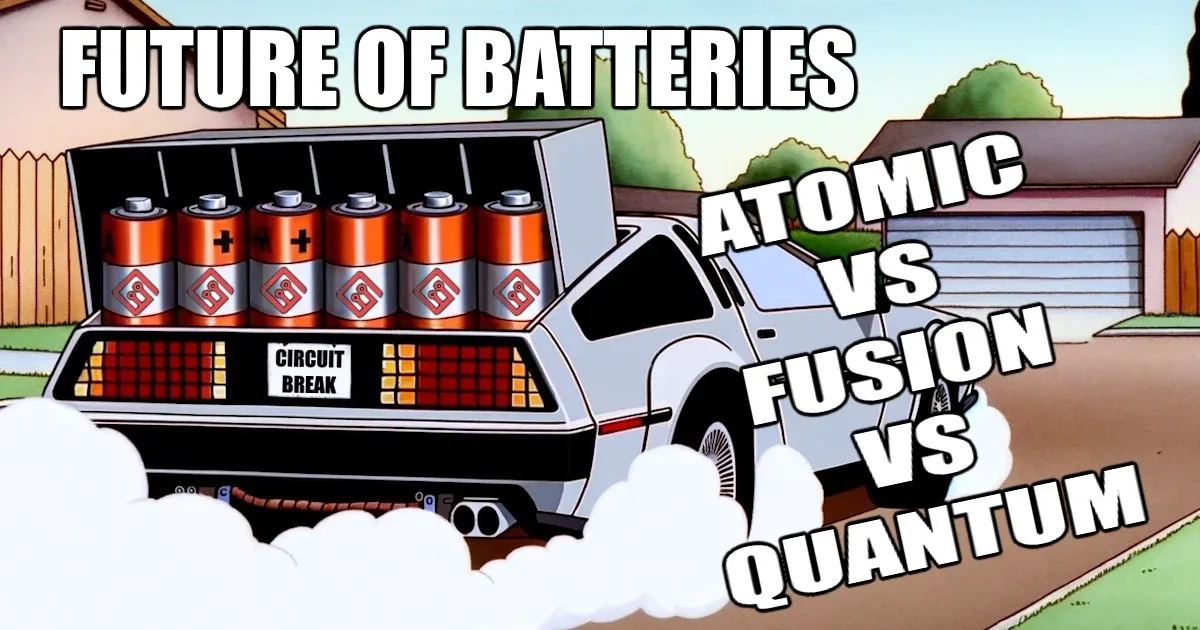
Entangled Steam
Parker and Stephen dive into the world of batteries, sparked by the BetaVolt BV100's claim of a 50-year lifespan.
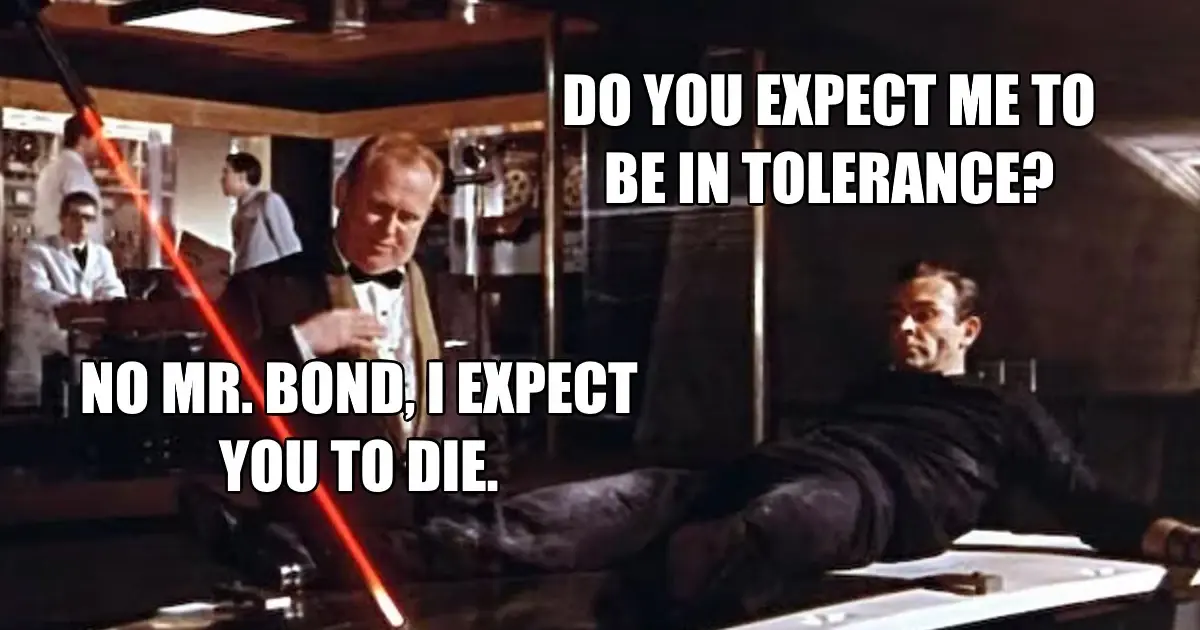
Laser Cutting Tolerancing
They may be known for being electrical engineers but on this episode, Parker and Stephen dig into the more mechanical aspects of their current projects
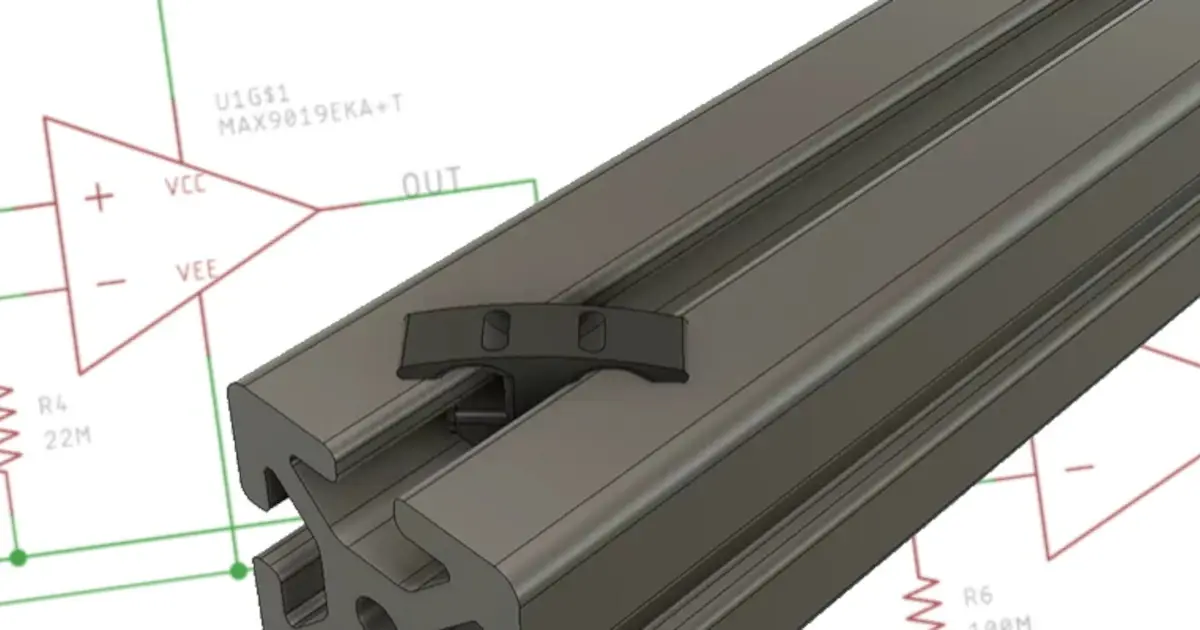
Current Conscience Comparator
How low can the power consumption of the Cat Feeder Unreminder go? Parker and Stephen discuss leakage current on this episode of the podcast!
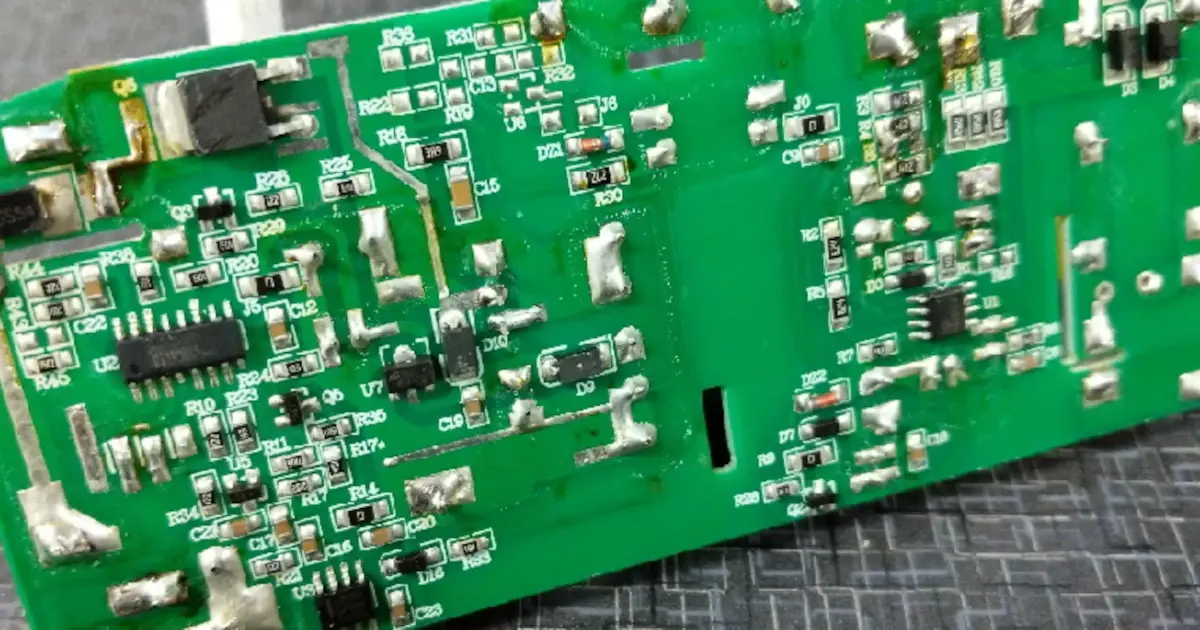
Schematics and Connectors, Name a More Iconic Duo…
Stephen deeps dives into schematics and connectors this week by asking what is the best way to draw symbols for connectors on schematics? Net Names!
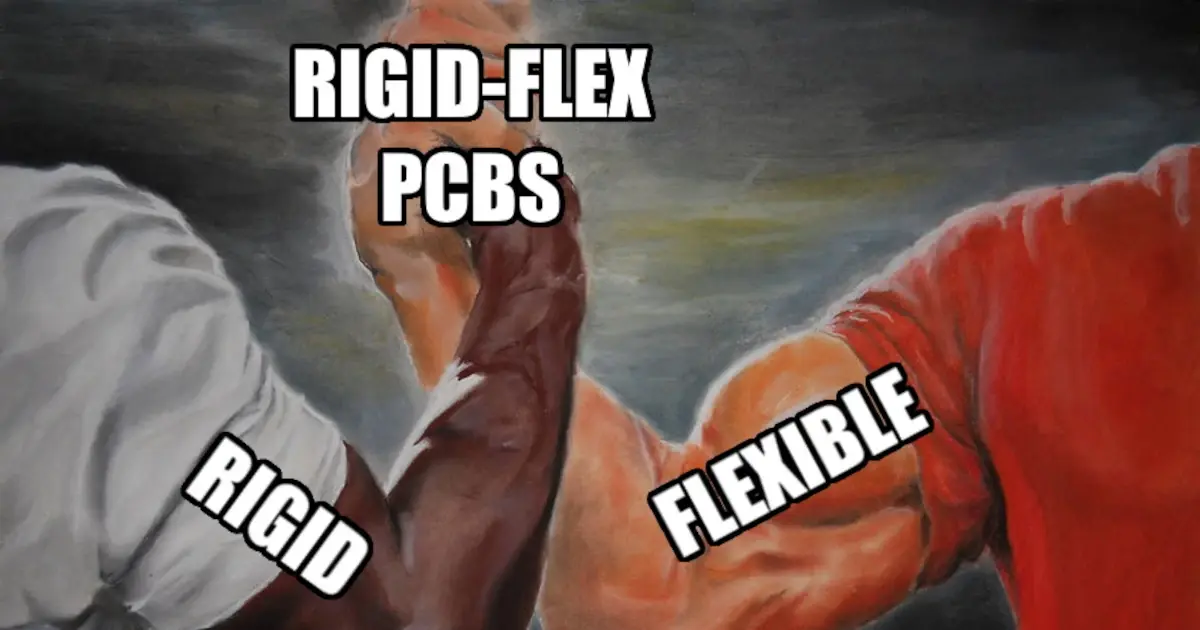
Flex PCB Primers
Stephen gives the MEP an introduction on Flex and Rigid-Flex PCB assemblies while Parker looks at an automotive Analog Devices application note.
About MacroFab
MacroFab offers comprehensive manufacturing solutions, from your smallest prototyping orders to your largest production needs. Our factory network locations are strategically located across North America, ensuring that we have the flexibility to provide capacity when and where you need it most.
Experience the future of EMS manufacturing with our state-of-the-art technology platform and cutting-edge digital supply chain solutions. At MacroFab, we ensure that your electronics are produced faster, more efficiently, and with fewer logistic problems than ever before.
Take advantage of AI-enabled sourcing opportunities and employ expert teams who are connected through a user-friendly technology platform. Discover how streamlined electronics manufacturing can benefit your business by contacting us today.