Related Topics
The Barcode Turns 50
Paul V. McEnroe is best known for his primary role in developing the UPC, the barcode used on every product in supermarkets and the retail industry.
Countdown to Hype
Consider your product in an environment that will actively destroy the semiconductors. We'll dip our toes into Radiation exposure for electronics!
Product of Many Imaginations
MacroFab's Misha Govshteyn and Chris Church check in with Parker and Stephen to give his take on supply chains, nearshoring and reshoring.
Other Resources
Circuit Break Podcast
Webinars
Videos
Tour MacroFab's ITAR-Compliant Facility
February 19, 2020, Episode #212
- Founder and current Chief Product Officer of MacroFab Inc
- The former founder of Dynamic Perception
- The former Co-Founder and Chief Architect of Alert Logic
- Was on the previous MacroFab Engineering Podcast episodes
- Topic today is the Coronavirus or COVID-19 outbreak in China and its impact on the global Electronic Manufacturing Supply Chain
- If you want to know more about the virus itself I suggest going to the CDC website
- ~80% of factories in general are back to work in China, but only about 21% are fully staffed
- PCB Vendors
- Extended holiday, workers at a lot of Chinese plants who went home weren’t allowed to come back for two weeks
- We have lots of production in Taiwan
- Taiwan blocked all entrance to mainland Chinese on the 5th of February, many limits still in place
- This is causing significant delays in engineering time for new PCB orders, as most of our vendors’ engineers went back to mainland China for the holiday, and haven’t been allowed to return
- PCBs going to Taiwan/Vietnam/Malaysia, etc.
- As soon as delays started happening, a lot of companies sent orders over to other Asian companies, of course, this caused a fast building backlog at those companies
- Prices going up in Taiwan, Vietnam, etc
- FR4 is now the real problem
- Even if production wanted to speed up in Taiwan, Vietnam, ect.. they can’t get the raw materials fast enough
- Mechanical / Custom Mfg Materials
- This is the biggest challenge for a lot of our customers
- Plastics and metals made in China are getting delayed by a month or more against the original lead times
- Factories are under-staffed and backed up with big orders
- Components
- Right now, most component suppliers are back up and running, even if under-staffed
- Small to mid-size orders won’t be impacted much, but high-volume orders sent direct to the manufacturers are getting longer lead times and higher prices
- Yageo is one of the vendors we’re hearing about, as of late last week pushing lead times out past a year on some bulk orders with price increases as high as 50%
- Vishay also has several plants closed as of Monday
About the Hosts
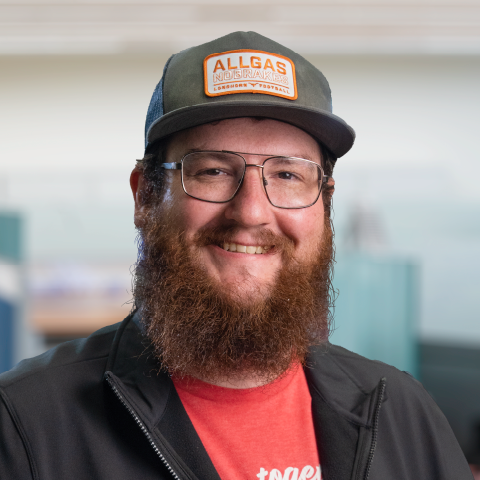
Parker Dillmann
Parker is an Electrical Engineer with backgrounds in Embedded System Design and Digital Signal Processing. He got his start in 2005 by hacking Nintendo consoles into portable gaming units. The following year he designed and produced an Atari 2600 video mod to allow the Atari to display a crisp, RF fuzz free picture on newer TVs. Over a thousand Atari video mods where produced by Parker from 2006 to 2011 and the mod is still made by other enthusiasts in the Atari community.
In 2006, Parker enrolled at The University of Texas at Austin as a Petroleum Engineer. After realizing electronics was his passion he switched majors in 2007 to Electrical and Computer Engineering. Following his previous background in making the Atari 2600 video mod, Parker decided to take more board layout classes and circuit design classes. Other areas of study include robotics, microcontroller theory and design, FPGA development with VHDL and Verilog, and image and signal processing with DSPs. In 2010, Parker won a Ti sponsored Launchpad programming and design contest that was held by the IEEE CS chapter at the University. Parker graduated with a BS in Electrical and Computer Engineering in the Spring of 2012.
In the Summer of 2012, Parker was hired on as an Electrical Engineer at Dynamic Perception to design and prototype new electronic products. Here, Parker learned about full product development cycles and honed his board layout skills. Seeing the difficulties in managing operations and FCC/CE compliance testing, Parker thought there had to be a better way for small electronic companies to get their product out in customer's hands.
Parker also runs the blog, longhornengineer.com, where he posts his personal projects, technical guides, and appnotes about board layout design and components.
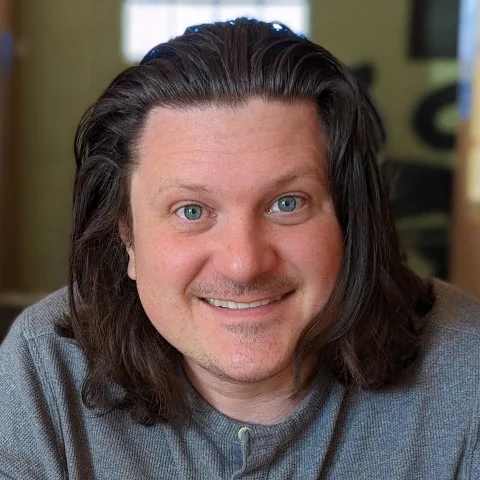
Stephen Kraig
Stephen Kraig is a component engineer working in the aerospace industry. He has applied his electrical engineering knowledge in a variety of contexts previously, including oil and gas, contract manufacturing, audio electronic repair, and synthesizer design. A graduate of Texas A&M, Stephen has lived his adult life in the Houston, TX, and Denver, CO, areas.
Stephen has never said no to a project. From building guitar amps (starting when he was 17) to designing and building his own CNC table to fine-tuning the mineral composition of the water he uses to brew beer, he thrives on testing, experimentation, and problem-solving. Tune into the podcast to learn more about the wacky stuff Stephen gets up to.
Special thanks to whixr over at Tymkrs for the intro and outro!
Related Podcasts
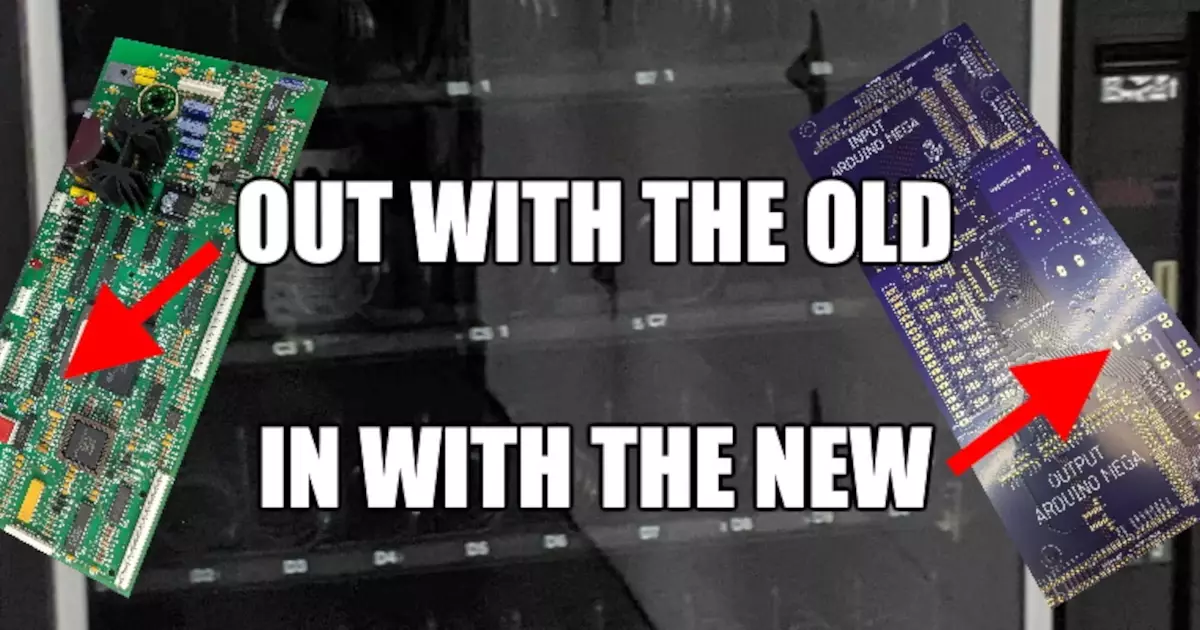
Double as Good!
Nichicon is obsoleting entire electrolytic capacitor lines. Is this a sign of how electronic component manufacturers will handle supply crunches?
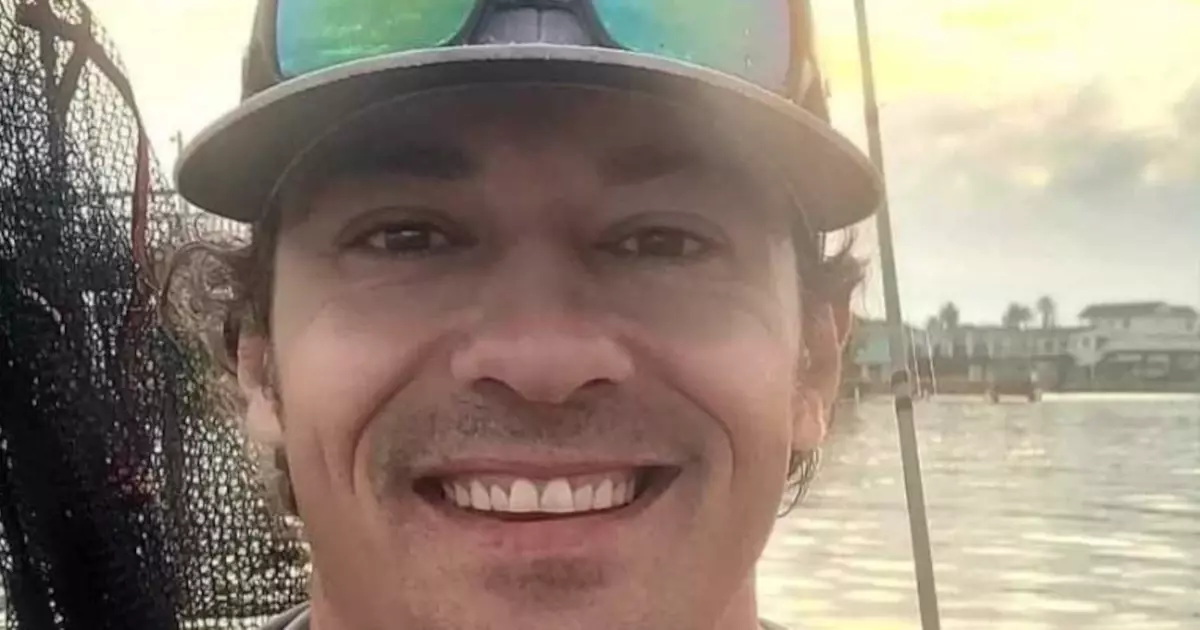
Cody's Corner - Q2 2022
Cody Endlich is back on the podcast to discuss the electronic component supply chain squeeze and what the future magic 8-ball says about the industry.
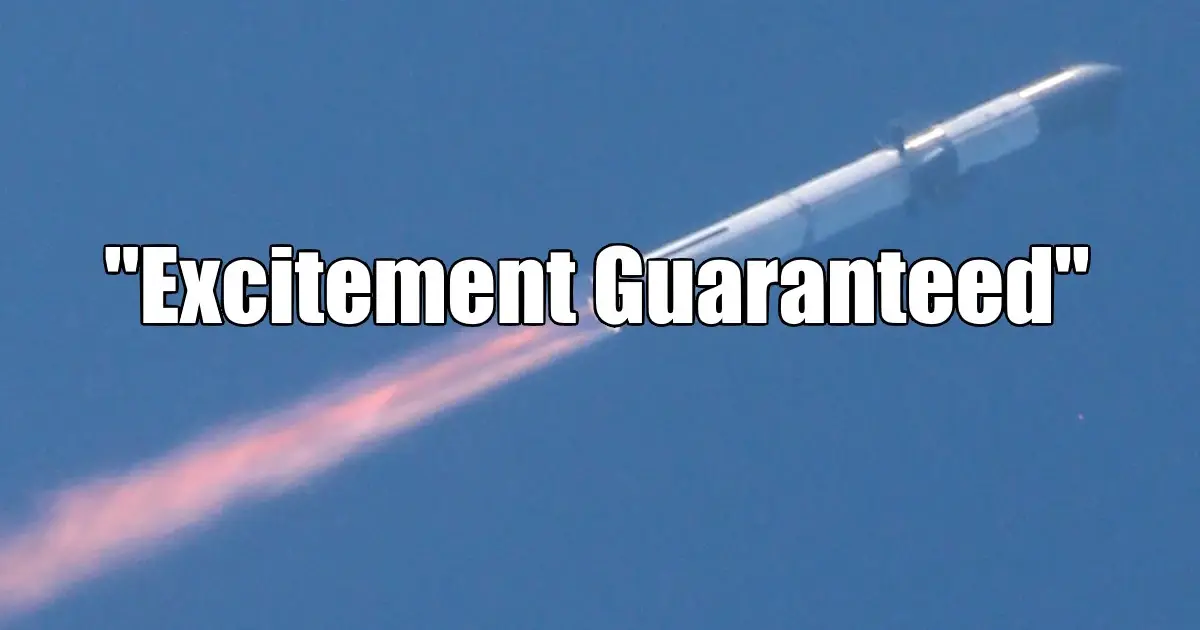
Countdown to Hype
Consider your product in an environment that will actively destroy the semiconductors. We'll dip our toes into Radiation exposure for electronics!
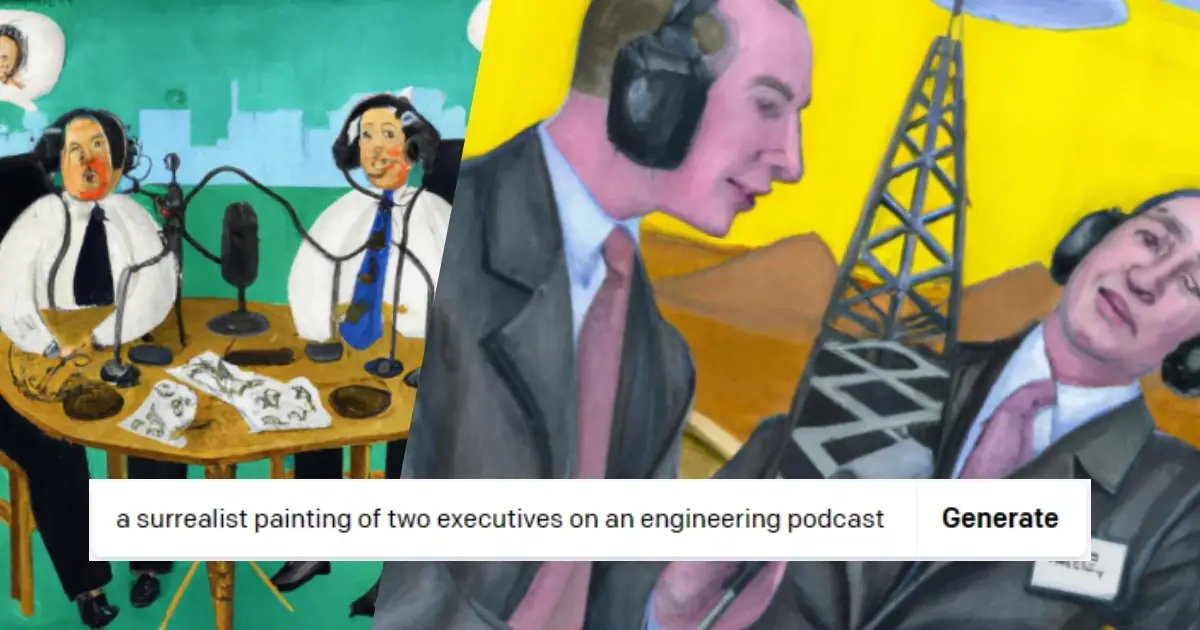
Product of Many Imaginations
MacroFab's Misha Govshteyn and Chris Church check in with Parker and Stephen to give his take on supply chains, nearshoring and reshoring.
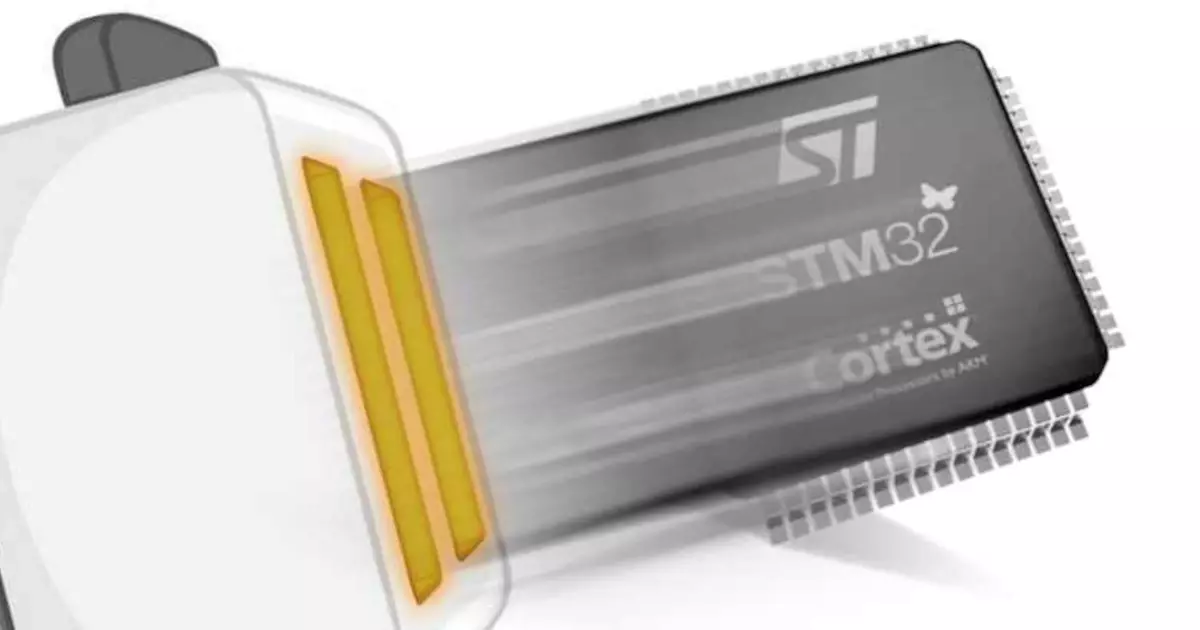
Your Toaster is Toast
Part shortages and obsolescence got you down? Parker and Stephen have some tips and tricks to help your design stay ahead of the End Of Life game!
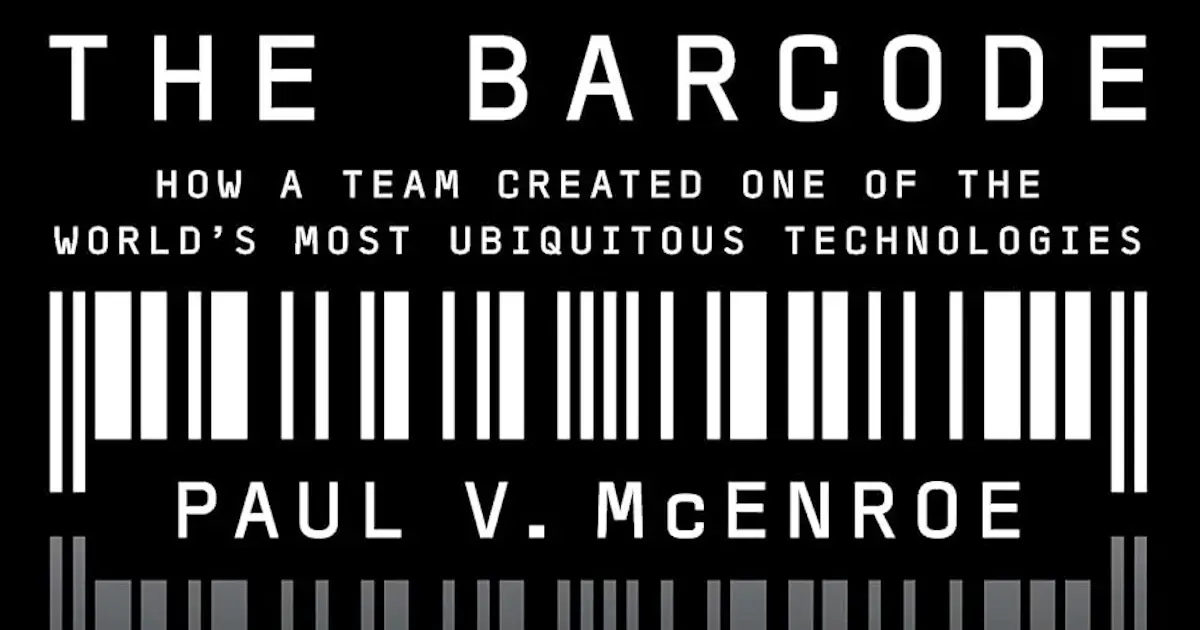
The Barcode Turns 50
Paul V. McEnroe is best known for his primary role in developing the UPC, the barcode used on every product in supermarkets and the retail industry.
About MacroFab
MacroFab offers comprehensive manufacturing solutions, from your smallest prototyping orders to your largest production needs. Our factory network locations are strategically located across North America, ensuring that we have the flexibility to provide capacity when and where you need it most.
Experience the future of EMS manufacturing with our state-of-the-art technology platform and cutting-edge digital supply chain solutions. At MacroFab, we ensure that your electronics are produced faster, more efficiently, and with fewer logistic problems than ever before.
Take advantage of AI-enabled sourcing opportunities and employ expert teams who are connected through a user-friendly technology platform. Discover how streamlined electronics manufacturing can benefit your business by contacting us today.