Related Topics
Conductive Cuisine
We'll explore an in-depth study conducted by Seth Jenkins, Neil LaTourette, and Brendan Liverman on how boiling time affects hot dog conductivity.
Wanting to be a Wizard - Matt Brown
Matt Brown, shares his career insights, including his experiences working at Tesla and on personal projects like the land speed car and the off-road Viper.
Exploring the Arctic Through Art and Technology with Cy Keener
Cy Keener's work includes a range of data-based efforts to visualize diverse phenomena including ice, wind, rain, and ocean waves.
Other Resources
Circuit Break Podcast
Webinars
Videos
Tour MacroFab's ITAR-Compliant Facility
August 1, 2018, Episode #131
- Scott Swaaley
- Electrical Engineer from California Polytechnic State University
- Started his career rewiring 18th century tall ships
- Designed electrical systems for hospitals and data centers before becoming a specialist in renewable energy economics
- Had a career in teaching and working with students in makerspaces
- Founder of MAKESafe Tools
- YouTube Channels Scott likes
- Clickspring
- This Old Tony
- What is MAKESafe Tools?
- Bringing industrial-level safety to everyday shop tools with an easy to install plug and play device
- Design Challenges?
- High power A/C switching
- DC Isolation from the A/C side
- Triacs and Hybrid relays
- Physical board layout considerations
- Documentaries and other links
- Most Likely To Succeed
- Beyond Measure
- Makerspace work
- TE Application Note: Coil Suppression Can Reduce Relay Life
Visit our Slack Channel and join the conversation in between episodes and please review us, wherever you listen (PodcastAddict, iTunes). It helps this show stay visible and helps new listeners find us.
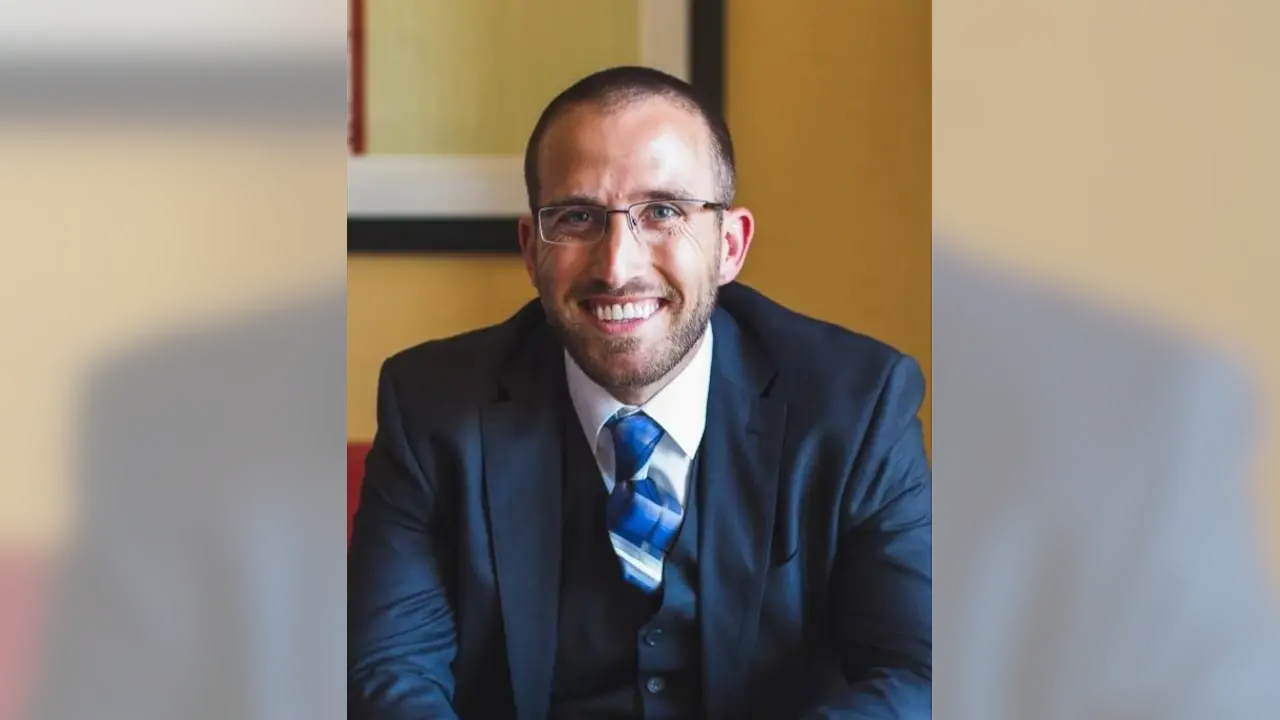
Scott Swaaley of MAKESafe Tools.
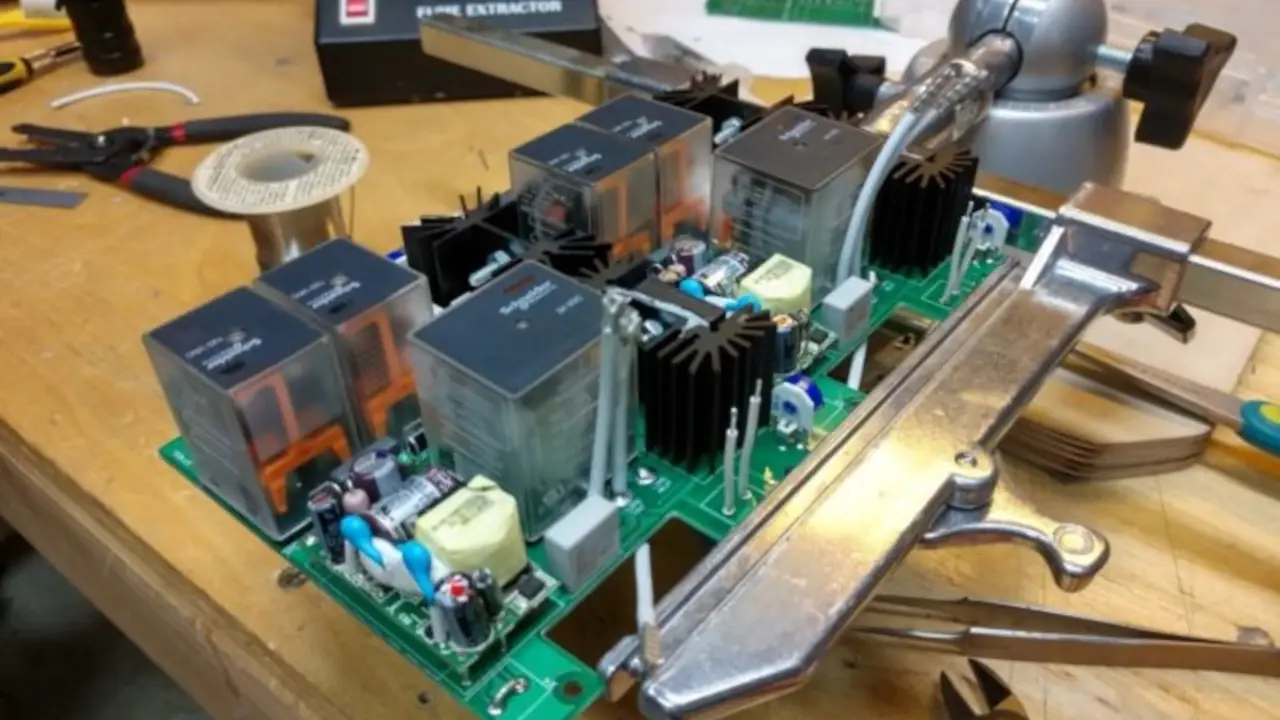
Testing a version of the Scott’s Power Tool Brake.
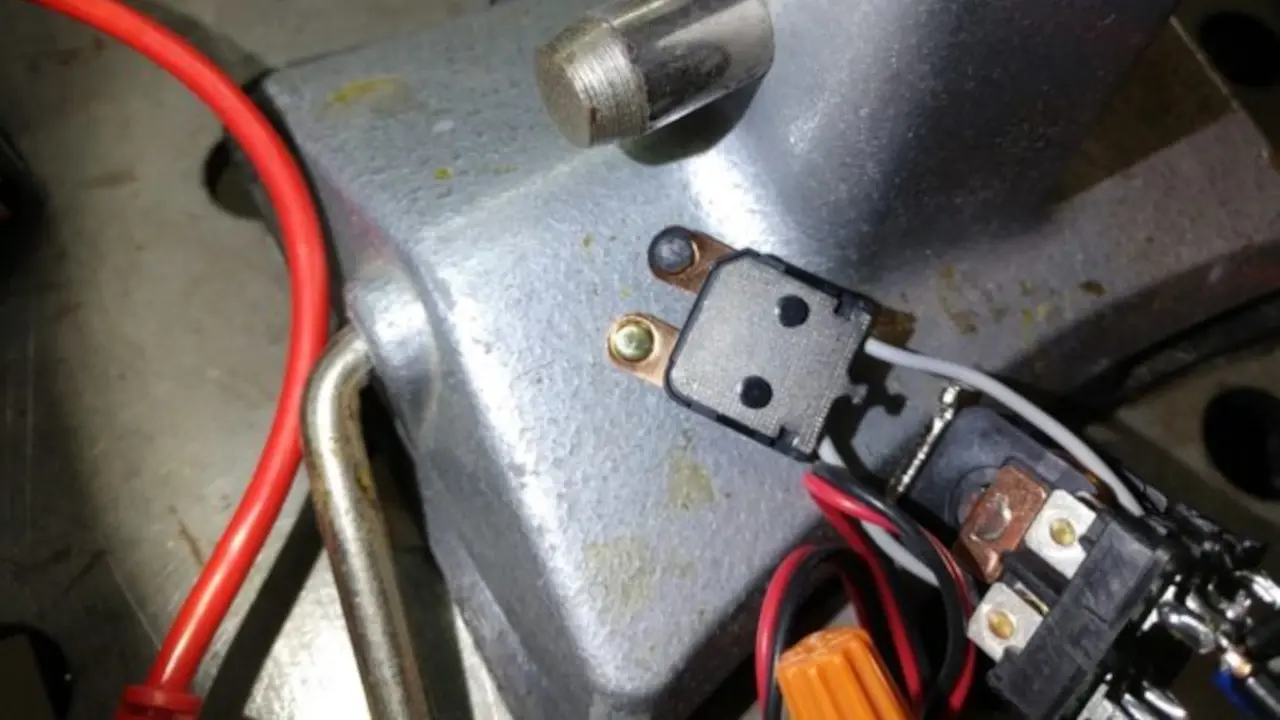
Contacts of a relay after 10,000 cycle with Arc Prevention (left side) verse no Arc Prevention (right side).
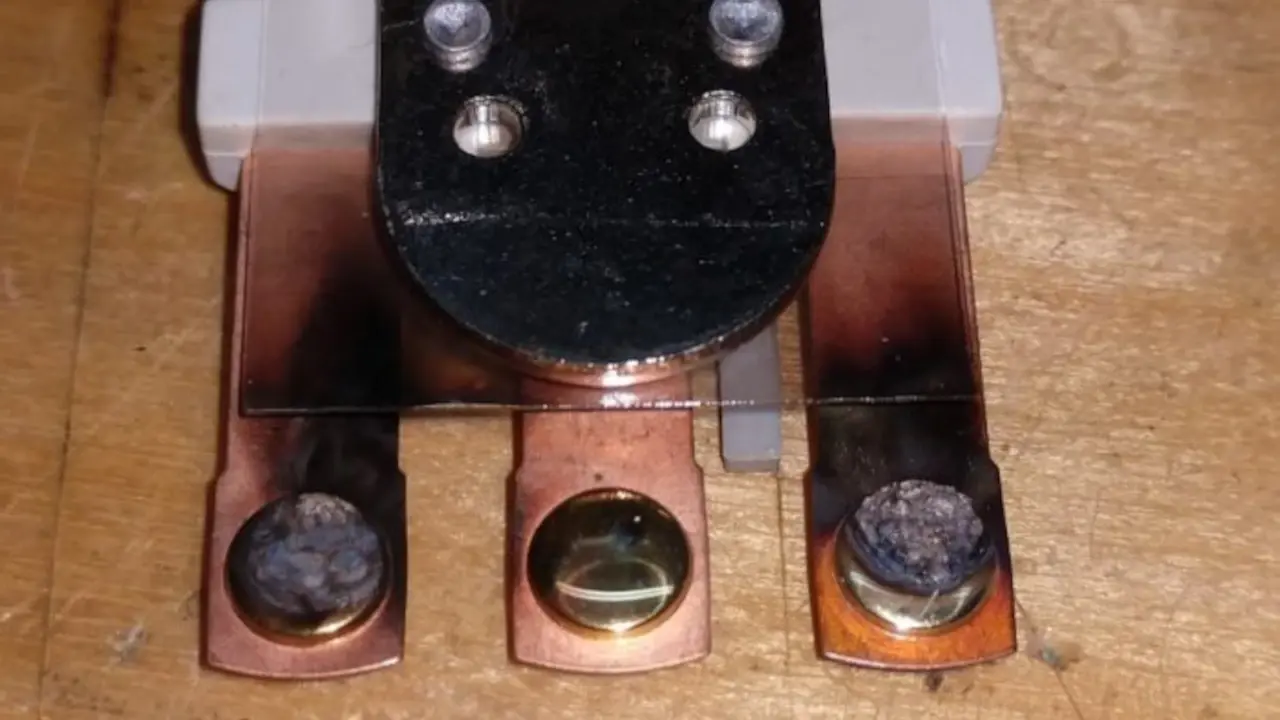
Close up of some welded relay contacts.
About the Hosts
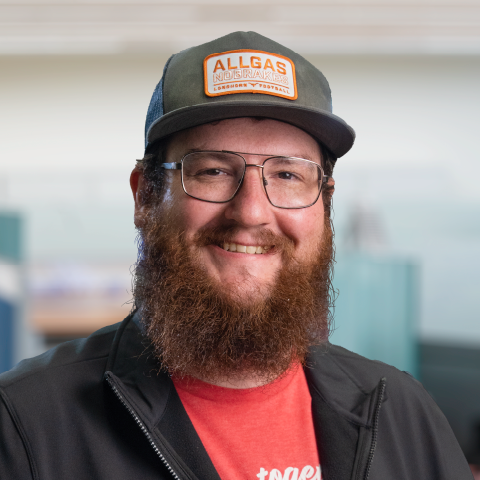
Parker Dillmann
Parker is an Electrical Engineer with backgrounds in Embedded System Design and Digital Signal Processing. He got his start in 2005 by hacking Nintendo consoles into portable gaming units. The following year he designed and produced an Atari 2600 video mod to allow the Atari to display a crisp, RF fuzz free picture on newer TVs. Over a thousand Atari video mods where produced by Parker from 2006 to 2011 and the mod is still made by other enthusiasts in the Atari community.
In 2006, Parker enrolled at The University of Texas at Austin as a Petroleum Engineer. After realizing electronics was his passion he switched majors in 2007 to Electrical and Computer Engineering. Following his previous background in making the Atari 2600 video mod, Parker decided to take more board layout classes and circuit design classes. Other areas of study include robotics, microcontroller theory and design, FPGA development with VHDL and Verilog, and image and signal processing with DSPs. In 2010, Parker won a Ti sponsored Launchpad programming and design contest that was held by the IEEE CS chapter at the University. Parker graduated with a BS in Electrical and Computer Engineering in the Spring of 2012.
In the Summer of 2012, Parker was hired on as an Electrical Engineer at Dynamic Perception to design and prototype new electronic products. Here, Parker learned about full product development cycles and honed his board layout skills. Seeing the difficulties in managing operations and FCC/CE compliance testing, Parker thought there had to be a better way for small electronic companies to get their product out in customer's hands.
Parker also runs the blog, longhornengineer.com, where he posts his personal projects, technical guides, and appnotes about board layout design and components.
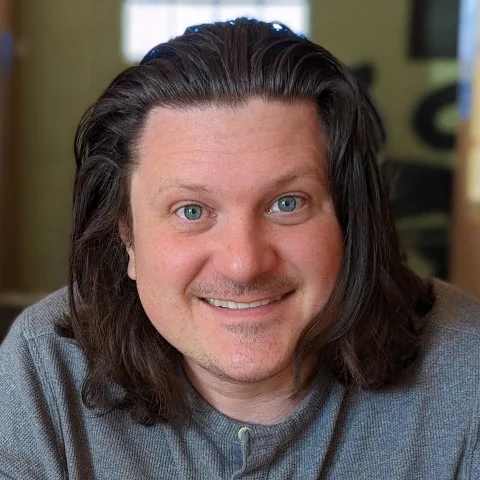
Stephen Kraig
Stephen Kraig is a component engineer working in the aerospace industry. He has applied his electrical engineering knowledge in a variety of contexts previously, including oil and gas, contract manufacturing, audio electronic repair, and synthesizer design. A graduate of Texas A&M, Stephen has lived his adult life in the Houston, TX, and Denver, CO, areas.
Stephen has never said no to a project. From building guitar amps (starting when he was 17) to designing and building his own CNC table to fine-tuning the mineral composition of the water he uses to brew beer, he thrives on testing, experimentation, and problem-solving. Tune into the podcast to learn more about the wacky stuff Stephen gets up to.
Special thanks to whixr over at Tymkrs for the intro and outro!