Related Topics
Top Features to Add to Your Next Prototype
Tune in as we share insights, anecdotes, and maybe a few confessions from our own prototyping adventures.
K-Factoring a Gumbo
Stephen finally gets a license for the Eagle EDA Tool but not for the reasons you would expect! Also, sheet metal design and IoT device security!
Kevin Beller of Seymour Duncan
Kevin Beller discusses his history with Seymour Duncan and how an engineer sells a creative idea.
Other Resources
Circuit Break Podcast
Webinars
Videos
Tour MacroFab's ITAR-Compliant Facility
April 26, 2024, Episode #428
This week we dive into the fascinating world of vintage tech repair, focusing on efforts to preserve General Motors' futuristic '80s digital displays. Hosts Parker Dillmann and Stephen Kraig discuss the resilience and repair techniques of the Visual Information Center (VIC) screens, introduced in the late '80s. They also highlight MacroFab's new inventory management features that streamline the process for electronic components, ensuring efficient project management and system updates.
Key Discussion Points
- Launch of MacroFab's enhanced inventory management system, improving component tracking and project management.
- The survival and repair techniques of GM's '80s digital displays, highlighting the challenges and techniques involved in maintaining legacy technology.
- Discussion on designing long-lasting electronic components and the importance of planning for product lifecycle and reliability.
- Exploring the impact of technology on product longevity and the potential of modern tools to extend the life of electronic devices.
Relevant Links
Community Questions
- How do you approach maintaining or repairing older technological devices to extend their lifespan?
- What are your thoughts on balancing modern design with the need for longevity in electronics?
- Have you worked on any projects that involve updating or maintaining older technology? Share your experiences!
About the Hosts
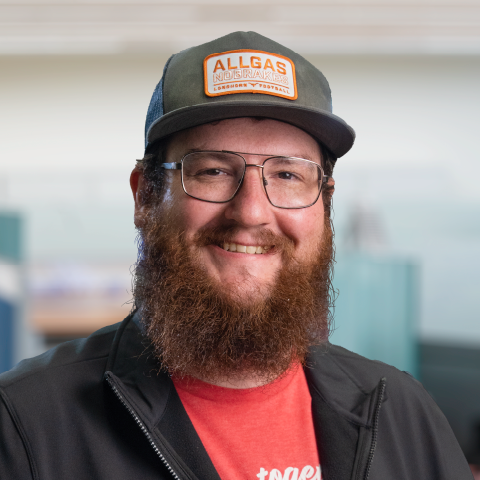
Parker Dillmann
Parker is an Electrical Engineer with backgrounds in Embedded System Design and Digital Signal Processing. He got his start in 2005 by hacking Nintendo consoles into portable gaming units. The following year he designed and produced an Atari 2600 video mod to allow the Atari to display a crisp, RF fuzz free picture on newer TVs. Over a thousand Atari video mods where produced by Parker from 2006 to 2011 and the mod is still made by other enthusiasts in the Atari community.
In 2006, Parker enrolled at The University of Texas at Austin as a Petroleum Engineer. After realizing electronics was his passion he switched majors in 2007 to Electrical and Computer Engineering. Following his previous background in making the Atari 2600 video mod, Parker decided to take more board layout classes and circuit design classes. Other areas of study include robotics, microcontroller theory and design, FPGA development with VHDL and Verilog, and image and signal processing with DSPs. In 2010, Parker won a Ti sponsored Launchpad programming and design contest that was held by the IEEE CS chapter at the University. Parker graduated with a BS in Electrical and Computer Engineering in the Spring of 2012.
In the Summer of 2012, Parker was hired on as an Electrical Engineer at Dynamic Perception to design and prototype new electronic products. Here, Parker learned about full product development cycles and honed his board layout skills. Seeing the difficulties in managing operations and FCC/CE compliance testing, Parker thought there had to be a better way for small electronic companies to get their product out in customer's hands.
Parker also runs the blog, longhornengineer.com, where he posts his personal projects, technical guides, and appnotes about board layout design and components.
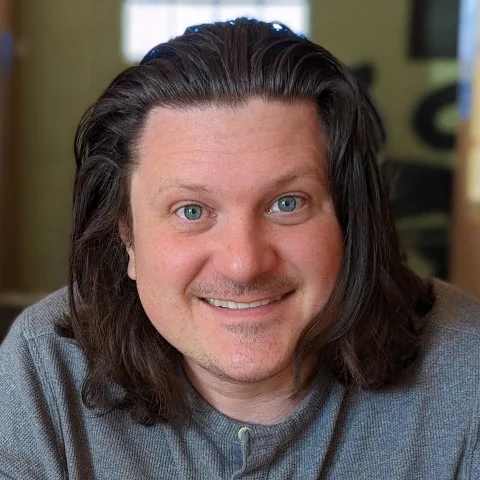
Stephen Kraig
Stephen Kraig is a component engineer working in the aerospace industry. He has applied his electrical engineering knowledge in a variety of contexts previously, including oil and gas, contract manufacturing, audio electronic repair, and synthesizer design. A graduate of Texas A&M, Stephen has lived his adult life in the Houston, TX, and Denver, CO, areas.
Stephen has never said no to a project. From building guitar amps (starting when he was 17) to designing and building his own CNC table to fine-tuning the mineral composition of the water he uses to brew beer, he thrives on testing, experimentation, and problem-solving. Tune into the podcast to learn more about the wacky stuff Stephen gets up to.
Transcript
Parker Dillmann
Welcome to circuit break from MacroFab, a weekly show about all things engineering, DIY projects, manufacturing, industry news, and long lived designs and complaining about Apple like we normally do. We're your hosts, electrical engineers Parker Dillmann. And Stephen Kraig. This is episode 428 and and before we get into the podcast proper, we have a platform update for MacroFab. We launched the enhanced inventory management system.
Parker Dillmann
We've always done energy inventory management in the platform, but it's we've got basically have a new display for it, and it handles overage, and it handles, like, how you let's say you up you you sent us some components for your inventory so we can store them, and you can build out of them. Well, what now is when you place orders, it will show, like, which parts of that inventory is reserved for builds and that kind of stuff. And it will actually tell you consumption reporting and burn down reports and that kind of stuff. And then there's, like, an improved inbound shipment management too, so you can see, like, where your component is at in terms of when it's being received in to the, HQ building.
Stephen Kraig
So can you see when your part is picked for a job and when it's gonna go out onto the floor?
Parker Dillmann
It's yeah. So it has, like, a reserved and then a work in progress section. Cool. So you can say, oh, you know, let's say you place an order and you need 20 of these components, it will reserve 20 of those for your order. That way you can, like, queue up multiple orders at once, And then the moment it gets kitted, it goes into work in progress.
Parker Dillmann
And kitting is when all the components come together for your order before it goes out to the floor or get shipped out to a partner facility.
Stephen Kraig
I I can tell you from from my side, things like that are absolutely wonderful. Given the job I work now, the parts that I deal with are considerably more expensive than previous jobs I've worked at. And so so a lot of times, I'll get asked by my project manager or by my manager or other people, hey. Where's x y z part? Can you give me a count on what's at your manufacturer?
Stephen Kraig
Blah blah blah. You know, when you have a reel of parts and every single part is $1200, you you wanna know the exact number of parts and you wanna know exactly where they are. And a lot of times, when I'm asked that question, it's, oh, let me send an email to my Centimeters and have them count it and tell me. But to be able to just look at my inventory and be like, yeah. I know they have this many, and they're in this stage kind of thing.
Stephen Kraig
That's really helpful.
Parker Dillmann
Yeah. That way you don't have to call us up or email, you know, Jerry.
Stephen Kraig
I do think that's funny because a lot of macro fab, is I don't think you were intending for this to be the case, but a lot of macro fab is set up for people who don't necessarily want to talk to people, or it's set up where if you don't want to talk to people, you don't have to. Right? It's all in the platform right there. I think that's kind of funny how it's, like, introverts, Centimeters. Right?
Parker Dillmann
It was planned that way. Yeah. It was. Wanted part of the initial was, like, never had to pick up the phone to figure out where your build's at or even to start your build. Mhmm.
Parker Dillmann
What's really interesting is I saw there's it's been this new term on social media in this in the hardware start or just the startup space called hard tech, and people are like, we should have a I I saw some discussion about we should have a pizza tracker for PCBA, and I'm like I just posted a screenshot. I'm like, we've had this for 6 years now. Yeah. We have a pizza tracker for your PCBA order, so you know exactly what's going on.
Stephen Kraig
Yeah. You know what stage it's any one point in time. Yeah.
Parker Dillmann
Yeah. So this basically is the same thing. It gives you more visibility into your inventory that you have at MacroFab.
Stephen Kraig
And and you know what's funny? For basically no work from your side, you being the engineer at xyzdesigncompanyorwhatever, it makes you look awesome. It, and I'm not just trying to sell here. What what what I'm saying is say that project manager comes up and says, I need, I need you to run a report of how much money we have in inventory at our contract manufacturer. You do it in 5 minutes and send it back to them.
Stephen Kraig
You look like a rock star, and all you really did was go to Macrobat and just say, hey. Give me the list of parts that you have.
Parker Dillmann
See, we actually do
Stephen Kraig
Yeah.
Parker Dillmann
Is you just take 45 minutes to do it. Oh. You get the information in 3 minutes from the platform Yeah. And then you go and take lunch.
Stephen Kraig
But you still look like a rock star because 45 minutes is still really fast for that.
Parker Dillmann
Yeah. It's pretty good. Yeah. So when your boss comes in and you say, that's gonna take a day, and you come back 45 minutes later with the answer.
Stephen Kraig
Man. Okay. Quick side channel. I absolutely hate estimating time to do a task or a project or or whatever. I I I don't know a lot of people who do, like, really enjoy that.
Stephen Kraig
I'm I'm sure there's plenty of business guys out there that really get their jollies out of estimating time on projects and things like that. But I I I was doing some recently, and I we were kind of looking at estimating time based on hours in a project. And a lot of times when I think about estimating time, I'm looking at, okay, 8 hours is a day's worth of work, but you're not constantly working on that project. So 8 hours like, if you say 8 hours on a spreadsheet somewhere, that doesn't necessarily mean I come in Monday, and I leave with that project done. Right?
Stephen Kraig
That 8 hours could be spread over 2 weeks because you're doing all kinds of other things. I don't know. I'm go I'm ranting a little bit here just because I've it's extended period of time is going to take, especially with testing. Even if you write a full test plan and you kind of have an idea of this probe goes here and I press this button on this device, and I do this kind of thing, it's still incredibly difficult to get anywhere near accurate.
Parker Dillmann
Yeah. Oh, yeah. I agree. You kinda have to just do it. You can get better as you get more experienced.
Parker Dillmann
Sure. And, like, platforms like Trello or Jira that can track, like, track time and statuses and stuff, but that's that's only as good as the data you give it. So you have to be diligent about, oh, like, for your example, 8 hours over 2 weeks, you have to be diligent about not just leaving, let's say, a task in progress overnight or the task, like, just in progress for the entire 2 weeks. Mhmm.
Stephen Kraig
Yeah.
Parker Dillmann
How we kinda did that was we in our this is in engineering, we had a our like, what everyone is working on board, kinda just like your current task. So it was a way so we could start measuring, like, workload and that kind of stuff. Mhmm. We had 2 well, actually, like, more than 2. We had a couple different, like, in progress statuses, and wanted to be, like, in process, like, in progress.
Parker Dillmann
I'm actively working on this thing right now. Then there's also in process, like, it's like on the back burner because it's like, I'm waiting on something. And we had different statuses for, like, you're waiting on a customer or you're waiting on someone else at Macrofab or something like that. And that got us pretty good, but it also you have to be you know, your team has to be diligent in doing it. And it's not something from micromanaging.
Parker Dillmann
It's just being like, okay. Every engineer's got 20 different projects. How do you know that what's the process of all 20 of those without having to bug that engineer?
Stephen Kraig
Yeah. Yeah.
Parker Dillmann
And have a, you know, 10 minute meeting every day. It was a way, basically, to get rid of stand ups and get rid of meetings and just be able to get rid of all that kind of just waste of time. Mhmm. And it helped a lot. Yeah.
Parker Dillmann
But, again, you have to be diligent, and it takes a while to get off the ground and get people used to, you know, when they task switch, they go and tell the system that they are task switching.
Stephen Kraig
Yeah. Feels a little micromanage y. But
Parker Dillmann
You could say that, but it got it it opened up 3 hours every week for people because there was no more meetings Sure. And that kind of stuff.
Stephen Kraig
You know, another thing is that kind of a system, I think, works if whoever is managing the system itself understands the type of work that's going into it. I I once worked under somebody who was very managy very micromanagy, And they they ran a Trello esque board and had very explicit dates for every little task that you do, but didn't understand how engineering worked necessarily. So so there was like, okay. This project kicks off. You have 4 days to create your schematic.
Stephen Kraig
So design your bore not board. Sorry. Design your project, make the schematic. And on the 4th day, the expectation was the schematic is 100% done, and then you move into layout. And then you have 2 weeks or whatever to do layout.
Stephen Kraig
And, you know, at the end of 4 days, I had the schematic, but they were like, is this done? I'm like, well, it's done, but I'm not gonna tell you it's done because that's not how this works. And then by the time and Yeah. Whenever I finished layout, they were like, okay. Are you done with that schematic and that layout?
Stephen Kraig
And I was like, well, I have to go make my drawings for all the manufacturing files. So, no, I'm not gonna call both of those done until they're done. And then after that, I had to get all of it approved. So I'm not gonna say anything's done until it's until everything was approved and then it all just in magically in a second it all wrapped up and was all of the tasks were complete. But the manager didn't understand that you can call something done, but it's still open in a way.
Stephen Kraig
During your layout portion, your schematic is done, but you may need to go back and make adjustments to it. So it doesn't just fit cleanly into this bin of, oh, it's done, and I will never need to see it again. It's and so I think engineering has a lot of wrinkles with that, and having a manager that understands it is important.
Parker Dillmann
Yeah. That's why we never really track statuses like that, like individual tasks inside of a project. It would just be like the total project that the engineer is working on.
Stephen Kraig
Yeah.
Parker Dillmann
So because each engineer has, you know, 20 different customers. Which one's behind, which one's our head.
Stephen Kraig
Which one's on fire?
Parker Dillmann
Yeah. Which one's on fire? And you don't so that way, you can look at the board, and we basically just had a notification system that would've been like, hey, if a project it's been in progress but been blocked by let's say it was blocked by an internal customer, which would be at MacroFab Right. For longer than 2 days, then the manager could go and go, hey. I'm gonna go talk to that one person that's the blocker and figure out why this is blocked and how do I unblock this so we can get progressing on this project again.
Parker Dillmann
Right. Right. Right. Whereas the only other way to know that is to have a stand up. And if you're doing a stand up every week, once a week, let's say on a Monday or or on a Friday, you won't know you you just have this gap 7 day gap of information.
Parker Dillmann
So it works really well, but, again, it it you do have to be diligent. I just it's better when you don't have to micromanage the tasks. It's just the overall what are you working on, and what's the status of that one project. Mhmm. So keeping it like a pro like a progress, like, product progress tracker or just status of it, but, yeah, we're not tracking, like, is the layout done?
Parker Dillmann
Is the schematic done? Is that, you know, did you verify the the document, like, the test document? That stuff wasn't in there. It's just hideable stuff. Not even that.
Parker Dillmann
It's just the let's say it was, like, the test building the test documentation and implementation and all that stuff for, let's say, Steven Craig amps. Because Steven Craig amps were is let's say you're we're building your stuff, and, there would just be a top level ticket in that board and you'd be assigned like an NPI engineer and you'd be assigned a test engineer And then but that test engineer is gonna have that ticket and be like, okay. I wanna spend probably an hour reviewing Steven Craig's documentation that they gave us. And so he'll move it into in progress actually in progress. I'm working on it right now Mhmm.
Parker Dillmann
And work on it. And when he's done, you know, if it's actually and okay. Well, the next step is we're waiting on actually getting in the equipment from Steven Craig amps. So they'll take the ticket and go, okay. I'm gonna put this in progress, but it's in it's waiting on the customer to get us some stuff.
Parker Dillmann
So they'll just move it into waiting on customer, and they'll just type in a note. This is where I'm, like, I'm waiting on the actual equipment because we don't have it yet. That's it.
Stephen Kraig
Yeah. So it's
Parker Dillmann
just it kinda just a mass like, the ticket just kinda grows and collects all this information. Yeah. Just a history document. If you're an engineer you should be doing that anyways is like recording what you're doing on a project that's kind of what that does.
Stephen Kraig
Yeah. Yeah. I like that.
Parker Dillmann
Yeah. Is there better systems? Probably. But does the development team uses JIRA here and it was like, well, that's just free for engineering to use. So we that's what we used.
Parker Dillmann
Sure. Sure.
Stephen Kraig
Yeah. I think when it comes to a project, the way I I kinda prefer it, and you and I are talking about slightly different methods and and industries here. But but I I like the idea that, say, a contract for a customer is written, or corporates come just down and says, I want a brake controller for this particular car. I want you to design that. And they say, you know, in the contract, we say, I want the first PCBs in my hand in 3 months.
Stephen Kraig
And the engineering team says, okay. And that's as much as needed because then the engineers that the engineering team including your manager sits down and breaks that 3 months up and they figure out how when they need to have schematics done, when they need to have layout done. I don't like it when the higher level says you have 2 days to do schematic and you have 5 days to do the layout. Blah blah blah. Like, that never seems to work.
Stephen Kraig
Just give me a date when I need to have a product or a PCB in your hand, and then I will work with my team to establish all the intermediate dates.
Parker Dillmann
Oh, yeah. I agree on that side. Yeah. Yeah. 100%.
Parker Dillmann
That's a higher level. Let's say the the document drafter. That's how we can call that person. Yeah. Or the product.
Parker Dillmann
Let's hope if I have another p word. The product person. The producter. Yeah. I mean, because they're not engineer, but they all they care about is they get the PCB or the device by a certain date.
Stephen Kraig
Well and okay. And, yes, give me what that date is that you have to have that PCB or the product or whatever. What's the deliverable? Give me that date, and I will come to you on a very regular basis and tell you it's going well or it's not. And if you need more granular data about if it how it's going, I will tell you the more granular.
Stephen Kraig
But if you're okay with not getting the granular, I I won't feed you that unless you need to know it. And you don't need to necessarily feed super granular dates down to me, especially if you don't understand general engineering practices for double lease of and that's not just me, like, being hoity toity or anything like that. That's it's just, like, compartmentalize each department and let them run their thing because they know that they're the experts at how the process flows through their department. Let them do that.
Parker Dillmann
Mhmm. No. I agree. You do have to have a way, which it's fine, except that you you still have in there that if that person needs more granular updates, let's just say it's progressing well or not well. K?
Parker Dillmann
Yeah. Like, a a a thumbs up or thumbs down on you hitting your dates. K? How do they know without asking you?
Stephen Kraig
Okay. So I honestly think that is one of the largest jobs of what a manager does. So a manager is a middleman between the individual contributors and whatever other department is there. So the granularity for a manager is day to day. And in some cases, hour to to hour.
Stephen Kraig
It is walking to the team and discussing what are you doing right now, how is this going, what is your progress, and then distilling that into larger packages of okay. Over 5 days, Steven or Parker got this chunk of work done and distill that and pack in a nice way that makes sense to whatever department needs to know what the progress is. If I laid out a switch mode power supply and I and I got all my ground planes really nice, blah blah blah, My project manager doesn't need to know that. But my project but my manager might say to my project manager, we are 20% closer to being done. That's something they do need to know.
Stephen Kraig
It's all about who is your audience, what are you trying to convey to them, and to what level of detail do they need. And 99% of the time, they don't need as much detail as engineers are willing to give or wanting to give. So knowing how to break that down is a skill for sure.
Parker Dillmann
Now what if your customer isn't in your company, and it's because you are doing something for an external customer?
Stephen Kraig
Yeah.
Parker Dillmann
And now they're tying up your support and your and your and your and your sales lines trying to get information.
Stephen Kraig
Well, that's just a bad customer. Once again, I think
Parker Dillmann
That's what that's what we're trying to do with the Mac event platform is so you don't have to the more we can record stuff and and make it easier to record that information and then trickle that information to the customer so they know how well or bad their build is going, that that's, you know, even better.
Stephen Kraig
You know? Okay. So I haven't I've been on the Macrofab platform a bit, but I haven't explored recently. Was it do you have the ability to set up different dashboards for people?
Parker Dillmann
No. Not yet. We have a dashboard, but it's not like a customizable dashboard.
Stephen Kraig
Yeah. Okay. So the you know, just an idea. Say, I have a login to my MacFab account, and I can see all of this information. But the client that I'm making a board for wants to see some of that information as well.
Stephen Kraig
I could make them a dashboard and send them a link, and that's just something that they could view. And they don't have any editable things, but, you know, maybe the customer, the client sent me some really expensive parts or something and I sent them to Macrofab and the clients, hey, I want to be able to see them at Macrofab. I could send them a link and it shows their parts that they sent to me that you guys now have. I don't know. It's just a thought.
Stephen Kraig
I that could be something that's cool.
Parker Dillmann
You could do that with other services and just using the MacFab API, basically, to get
Stephen Kraig
that information. Build that.
Parker Dillmann
Yeah. You could build that with something like Retool, which is a it's like an online app builder Right. That you can basically glue a whole bunch of, APIs together and databases. So you could hook that up to the MacVeth platform with your authentication and pull that information in and just show a inventory dashboard for one component for that customer.
Stephen Kraig
You can always do it that way. I I know what I was just saying. There's very extremely specific. Out of, you know, all customers, there's probably only a very few number that that would apply to. It's still I don't know.
Stephen Kraig
It's it'd be a cool idea. I could see that being a cool idea splitting up based off of your role at a company. You know? Purchasing sees this. Engineering sees that.
Stephen Kraig
Management sees this.
Parker Dillmann
Kinda have that. Yeah. And I remember when I
Stephen Kraig
was working there, you guys were setting that up.
Parker Dillmann
Yeah. We have different views, so to speak, for procurement and well, procurement slash purchasing and engineers on in organizations, but not nothing like what you're talking about, though.
Stephen Kraig
Yeah. And until recently, I can't see I haven't had a need for that kind of stuff. Most of the time that I've dealt with customers, a a, you know, a a regular meeting with them and a PowerPoint slide saying, here's how we've managed your stuff It's usually good enough.
Parker Dillmann
Yeah. It's just I I see a lot of people talking about wanting the information right away and not wanting to talk to people.
Stephen Kraig
Well and to kinda tie it all back, that's what your inventory system allows you to do. Right?
Parker Dillmann
Exactly. And I was just thinking about this, but because there there are a lot of customers that are old school in in terms of they want to call and talk to someone or email in. What have I just connected that to? I wonder if you used 11 Labs which is a AI service that you can basically clone your own voice. That's what I used for the the charity stream last year where it was Darth Vader was reading all the call outs from people.
Parker Dillmann
I basically made a clone of Darth Vader's voice.
Stephen Kraig
Mhmm.
Parker Dillmann
And so you you I could put a clone of my voice, and it could be me talking to you over the phone reading basically what the back of our platform says.
Stephen Kraig
I I wonder if you did that. I wonder if people would be okay with that or if they'd be upset.
Parker Dillmann
I think they wouldn't know. And then the moment they figured they knew it was an AI, they would be upset.
Stephen Kraig
Yeah. I agree. So so there's this concept that if you call a company and an actual human being answers the phone, then, like, you get excited and they feel like old school good customer service when that happens. Right? And you kinda got to the point where you expect if you call a large ish company, you're gonna get you're gonna get whatever telephone service they have, and then you gotta deal with that forever.
Stephen Kraig
But is that the next step of pissing people off? It's just you do get a human, but it's an AI human. And I don't know. That might actually work. That might not actually piss me off because I can interact with it like a human and get what I want as long as that all works.
Stephen Kraig
I don't necessarily care.
Parker Dillmann
Yeah. I don't care either because all I care about is just getting information I'm looking for as fast as I can.
Stephen Kraig
Yeah. The the under Yeah.
Parker Dillmann
That's like what I call, let's say, AT and T because my Internet is down or messed up or something's wrong with it. The first thing I do when I call these big companies is I just mash the zero button a bunch. Yeah. So I try to get a actual human being on the phone. Sure.
Parker Dillmann
Because I know the going through this the pressing all the buttons and typing all the information in, it's gonna take way longer than when I actually get a human on the phone. So if I could skip to so I'm just trying to get to the end where the answer is. I do see an a an a hooked up to it would probably not be good for data retention, though.
Stephen Kraig
Do you have a because
Parker Dillmann
think about well, think about how the biggest breaches of security is in just social engineering is the number one way of finding out yeah. Packing is mostly social engineering nowadays.
Stephen Kraig
Or you just convince the AI to give you data that it shouldn't.
Parker Dillmann
Yes. Exactly. Yeah. Yeah. So it's if if people are gullible is not the right word, but if people are susceptible
Stephen Kraig
Yeah.
Parker Dillmann
To social engineering, I bet you an AI is even more susceptible to because it doesn't it can't infer, I guess. It it does it doesn't get social cues on, like, the phone call and that kind of stuff. Right. Right. So I would say that was probably your biggest risk there.
Parker Dillmann
Be interesting to try out, though. Maybe if I wasn't in marketing now, I I would build something like that just to try it out.
Stephen Kraig
In some ways, I feel like marketing is actually an okay department to be in for that.
Parker Dillmann
I guess. Yeah. Because we don't have any AI chat bots or anything like that on our website. Yeah. Some of those are some of them are really good, like the Amazon one.
Parker Dillmann
When you talk to like, when you do their chat thing that's on their website Yeah. And that's an AI bot. There's no one on the back end of that. Yeah. But some of them are pretty there was I think it was GM slash Chevy implemented a chat gbt bot for their website, and you could get it to compile and run Python code on their website.
Parker Dillmann
Really? That was pretty yeah. So it was pretty funny. You can get, like, the chatbot to execute code. That was pretty good.
Stephen Kraig
Yeah. I was not aware of that.
Parker Dillmann
Yeah. That made the rounds on that. I think it was, like, earlier this year. I think it was in January. But, yeah, some interesting stuff for sure.
Parker Dillmann
Yeah. So back back to that is, like, I I wouldn't care. As long as the information is that's if that's the fastest way that company can get me the information I need, so be it. Don't let me put don't put me on I'd rather not be put on a waiting list to finally get ahold of someone.
Stephen Kraig
Yeah. I've been on I've been on hold for an hour
Parker Dillmann
and a half.
Stephen Kraig
Yeah. Right. Right. AI would be so helpful for answering all the really dumb, simple questions that probably burn tons of time. Okay.
Stephen Kraig
We're we're going on all kinds of fun tangents here. But but okay. Think of this. When when I go to a website for for, an establishment, let's say, a restaurant. Right?
Stephen Kraig
If I go to a website for a restaurant,
Parker Dillmann
the the the thing that
Stephen Kraig
should be on the front page of a of a restaurant is what are your hours and where's your location? Right? Because 99% of the time, that's what
Parker Dillmann
people Maybe also a website for food.
Stephen Kraig
Well, okay. That's what all I'm saying is the absolute most critical items that are on there. Now if you wanna add your menu or if you wanna add, you know, your schedule of events or whatever you're doing, like, if I don't know if you have bands that play at your restaurant or whatever. But what's the absolute most critical thing when you are a restaurant or something like that? Put that number on there.
Stephen Kraig
I bet you restaurants I I I it would be really fun to know how many man hours are burned every year from people calling a restaurant just being like, are you open? I bet you it's staggering how many hours are even for a 10 second phone conversation that somebody's just calling to see, are you open kind of thing? AI could take care of those kinds of things. Right?
Parker Dillmann
Yeah. And especially, let's say, like, all these restaurants, if you could Google that restaurant, it has its hours Yes. And all that stuff right there. So that information is really readily available, and people still call in and ask, what's your hours?
Stephen Kraig
Exactly. Well but okay. So so there are times when it's not necessarily super accurate. It may be a holiday, and you're not sure or and Google's still saying or Google says holiday hours may be different or something like that, an AI could just be like, yep. We're actually closed.
Stephen Kraig
Sorry.
Parker Dillmann
It's hooked up to the on sign on your,
Stephen Kraig
on your Yeah. For the neon sign?
Parker Dillmann
Yeah. The the on neon sign or open neon sign. Yeah. Yeah. Yeah.
Parker Dillmann
It just hooked up to that.
Stephen Kraig
So let a human say hard questions. Let an AI answer the dumb ones.
Parker Dillmann
That's a product right now. Okay. That's is an on or an open sign. I don't know why I keep saying on sign. An open sign that's hooked up to a that's, like, an IoT open sign.
Parker Dillmann
K? Yeah. And it's hooked into your your POS system and for the call system.
Stephen Kraig
Yeah. And if the open sign is on, the chatbot will say, yeah. Come on in. We're open.
Parker Dillmann
Yeah. The phone tree will say we're open.
Stephen Kraig
Right. Right.
Parker Dillmann
Right. Right. That is a product. Yeah. I I wonder if that has to exist, but make it simple like that where if the on oh, geez.
Parker Dillmann
I'll just
Stephen Kraig
say it again.
Parker Dillmann
If the open sign is on Yep. Then it says that we're open. And if it's off, it says that we're we're closed.
Stephen Kraig
See, we're solving the real problems in the world here.
Parker Dillmann
But making it super simple, so it's not like some other system that you have to log into or, like, a button they have to press, like, on the computer or whatever. It's literally the sign turn it off and on.
Stephen Kraig
Yeah. And, you know okay. A little bit further than that, if you call have you when was the last time you called, like, a Target or a Walmart and asked them if they have something in stock? It's been a while. Right?
Parker Dillmann
I would say I can't remember because usually I go onto their website and see if they have it in stock or not.
Stephen Kraig
Yeah. But an AI could do that as well. Right? Yeah. There's nothing saying that
Parker Dillmann
I I don't know. It's more useful for grocery stores because let's see. You're looking for one particular sauce. Yeah. And and it might be, like I mean, you know how big HEBs can get grocery stores in here in Texas.
Parker Dillmann
And onto the HEB website and going, okay. I'm looking for this sauce. What aisle is it in?
Stephen Kraig
Well, okay. So anytime you call one of those big stores, you always have to do the whole dance of, can you please connect me to the electronics department? You you you know, you always have to do that because the first person you talk is 100% guaranteed to not be able to answer your question. Right? But AI could just do that.
Stephen Kraig
Right? It just knows the inventory, and they could just spin it out
Parker Dillmann
for you.
Stephen Kraig
Just along the website, but
Parker Dillmann
We should get on to the real topics, but I'm wondering this what we just said. I wonder how the people who hate AI just because AI is going to defend that idea Yeah. Or attack that idea. Because there are some people out there that just AI, I hate it. So Just but just arbitrarily.
Parker Dillmann
Yeah. Arbitrarily. Right. Why is people are so, like, black and white nowadays?
Stephen Kraig
Yeah. I don't know.
Parker Dillmann
Polarized. Right? Yeah. Polarizing. Yeah.
Parker Dillmann
People need to have more than one bit of color.
Stephen Kraig
Gray is a nice color.
Parker Dillmann
Alright. So 36 minutes in. So the our first topic that's actually on our list to talk about today, not our dive into AI chat bots and Mac fab platform updates is this is a really cool article I found on Hackaday, but it's from the auto autopian? Autopian. Autopian?
Parker Dillmann
You're right. That's what it is. It's about a, a person named John who basically rebuilds a short lived add on or option for GM Toronados from, like, I think it's, like, 1989 to 92. 3 years, you can get a what was called a VIC, a visual information center inside your GM or Ultimate Beal Toronado, And this predates those tablets that are, like, glued to the dash of every single car nowadays by 2 decades. Okay.
Stephen Kraig
Yeah.
Parker Dillmann
And, basically, it's a CRT touchscreen that has controls for HVAC, has a trip computer compass. They also integrated the car phone because this is 15 years before a cell phone was a nothing, let alone, like, everyone having one. But this is like an article about repairing them, and what, John does to repair them. Mostly it's it's CRT repair because most time it's just like the control circuitry goes out and they have to replace some components. Most of it's like electrolytic capacitors, a lot like amplifier repair.
Parker Dillmann
Most time you're just replacing you shotgun all the capacitors, resolder everything, and it comes back to life.
Stephen Kraig
I I I love the the the old CRT stuff, especially with electrolytic caps because you can see the caps go bad. Because the screen just starts to wobble and flicker, and you could just look at it and be like, yep. I need to replace caps. It's time. Yeah.
Parker Dillmann
But it's a really cool I I knew they had CRT. GM did this this I went down like the rabbit hole reading about the VIC system, but what's even cooler is they even had a short term pilot program with GPS navigation down in Orlando, Florida. And they've been there only 90 Yes. And 92. Wow.
Parker Dillmann
I I think they built, like, 200 of these cars, and, like, Avis Avis had a hundred of them that you could actually just rent, and they had this GPS system into it. And it was like a combination of using, like, the car phone for data and the GPS system because it you could also get just like a modern, like, Android Auto setup or a modern navigation. You get traffic updates, and it would know that you were, like, off route. And if you needed help, it was kinda like pioneer, and they're also they're, OnStar service. So if you needed help, you could just click the help button on your dash, and it would call AAA for you, and they they would know where your location was and let you get and help you get back on the on track, basically.
Parker Dillmann
Right. Right. Right.
Stephen Kraig
I wonder what the resolution of it was. Because, GPS is kinda crazy now. GPS is what? 6 feet now or whatever?
Parker Dillmann
It's less than it's less than that.
Stephen Kraig
Well, I mean, correct. It is less than that, but but they don't necessarily give you that much resolution if you go to Google and whatnot. But, but regardless, I wonder what it was at this time.
Parker Dillmann
Yeah. I I think it was definitely probably, like, 30 feet or so. But if you look at the roads that's being displayed on this CRT monitor, they're not particularly super high risk. It looks like a vector screen.
Stephen Kraig
Yeah. Yeah.
Parker Dillmann
I mean, it is a yeah. I don't know if they were drawing them a lot as a vector display, or are they rasterizing it? I don't know that. Would be cool if it's a vector.
Stephen Kraig
That would be really neat.
Parker Dillmann
But they're colored displays, so that
Stephen Kraig
And they're touch screen too.
Parker Dillmann
Yeah. They're touch they had colored vector displays, so I don't know if they were vector or not, but really cool, system. Everyone that's interested in, like, weird automobile stuff, definitely go check this out. But this brought up a interesting idea, or topic I wanna talk about is if so this is 30 year 34 years down the road, right, that these CRTs are starting to fail in these cars, which, honestly, given the environment in a car with how many, like, heat cycles you go through in the day, that's actually kind of impressive Mhmm. For a TV.
Parker Dillmann
But if you were trying to design something and that I was saying like if you were designing the CRT monitor that's going in this car, like, how long should the lifespan be?
Stephen Kraig
Oh, that's a good that's a good question.
Parker Dillmann
Because I mean, back way back in the day in the, you know, forties, fifties, and sixties, you know, cars were really only designed for 3, 4 years max. If you got, like, 50,000 miles on a car, that was a lot of miles for a car back then.
Stephen Kraig
Yeah.
Parker Dillmann
And engines didn't last as long. In the early days, engines didn't have oil filters, lot of stuff. And nowadays, if a car doesn't hit a 100000 miles, it's a bad car, bad design.
Stephen Kraig
Oh, yeah.
Parker Dillmann
And you can even say double that. If it doesn't hit 200 1,000 miles, it's not even worth buying. Now and most people are keeping their cars for 7 7 to 8 years now for the first owner of that car, and it's gonna live 20 more years later in the secondhand market. So but back then, it was still like, do you did you plan for a 30, like, how would you even gauge that? Like, especially when, like, early on was, like, a low volume option.
Parker Dillmann
But on the other side of that is, let's say you want to design something, like, an end of the world electronic device where it will still work until the sun expands into a red giant and consumes the earth. How would you go about designing something like that? I mean, first of all, electrolytic capacitors are you can't use those.
Stephen Kraig
No. No. Okay. So it's funny. I've actually dealt a little bit of with this recently.
Stephen Kraig
So, basically, what you're talking about is reliability and how do you guarantee reliability for a long period of time. And on top of that, what you're really getting at is how do you calculate that you can guarantee reliability for a long time? And there's a handful of, frankly, not that difficult e equations that you could bang out that says, you know, at the end of the day, what is your probability of failure at x years given these input conditions? Like, how many temperature cycles it goes through every day and how many what's its duty cycle of on? A car is not a 100 duty percent duty cycle.
Stephen Kraig
You know, on average, it's probably the duty cycle of a car is actually probably pretty low because you drive to work, you turn it off, and then you drive back home. Right? So all of these are factors that can go into these equations. But if you're looking at just a single point or a single, I don't know, circuit, the reliability, it it trails off at a certain point. You you you just can't make something more reliable.
Stephen Kraig
You can only spend so much money, and that's when you start saying, okay. Now we get into redundancy. And redundancy, like a dual redundant circuit, doesn't reliability. And so then you have to start asking, what about triple or quadruple redundancy? And so you build a really robust circuit.
Stephen Kraig
You test the snot out of it, and then you just multiply it. And, frankly, to my knowledge, that's one of the easier ways to get more life out of something of this sort. And when it comes to the driver let let let's say we were actually trying to make a CRT that last 50 years. The funny thing is the CRT itself may not degrade, might not be the the the key factor that degrades. It may just be, you know, the the flyback transformer or the I'm sorry, the flyback circuit that does the high voltage to it and things like that.
Stephen Kraig
So, you know, identify your key circuits, test the snot out of them, and then add a boatload of redundancy would potentially get you there. But the thing is, it's still only probability. And and the way that you kinda work it out is you say you give a probability number with a time input to your circuit or to your equation. So you say something like, at age 20 years, I want 95% of all of my product to still be functioning. So you have to allow for 5% of your stuff to fail at at 20 years because there is no such thing as a 100% success at 20.
Stephen Kraig
You just can't guarantee that, but you can keep doing all these little tricks to bump that number up. And, eventually, you have to just assume the remainder is risk of failure.
Parker Dillmann
So yeah. Because we we talked about that with, James Lewis Right. On a previous podcast. I think it was, like, entropy rules the world or something like that is the title of that podcast.
Stephen Kraig
I like that.
Parker Dillmann
But I'll rephrase the question.
Stephen Kraig
Yeah.
Parker Dillmann
If you were building an amplifier
Stephen Kraig
Yeah.
Parker Dillmann
That you wanted to pass down to your son Yeah. What components would you pick?
Stephen Kraig
Yeah. So so what I first said is more of, like, the design equation side, and now you wanna know more, like, exact nitty gritties kind of things. So so, obviously, you pick components that you know are less temperature to have less of a temperature dependence and have nothing that can dry up and have really good aging parameters. So film capacitors as much as possible, things that are potted. If you if if you have something that is embedded in urethane, a lot of times that has a longer lifespan, Things that, resist vibration, things that resist temperature swing
Parker Dillmann
Keeping the design cool. Keeping the design Yeah. So, like, running undersized traces or underrate even not even, like, underrated, but just at rate resistors.
Stephen Kraig
Yeah. Also, a circuit that that is used regularly because because one argument you could say, I wanted to make an amplifier that I would give to my son in 30 years. I wouldn't just make an amplifier. Let it sit for 30 years, and then turn it on because that's not reliable either. So something that gets regular use.
Stephen Kraig
Right?
Parker Dillmann
Yeah. It's an interesting thing to talk think about because when because I'm gonna start going more into automotive OEM, like, aftermarket designs for my electronics moving away from pinball, and that's one thing I'm thinking about. I'm like, well, if I design, let's say, this motor controller and in in 30 years, I want that motor controller to still work. Mhmm. You know?
Parker Dillmann
How do I because that's, like, the worst thing that can happen is if I build let's say I build, like, a 100 of these motor controllers and sell them, and in 3rd and I'm using some of them. Right? In 30 years and if they if mine breaks, I can't replace it because it's like a, you know, spokespoke motor controller. Right? You know?
Parker Dillmann
So I would like it, from my standpoint, for the last forever. And especially if you, like, make that as part of your sales argument too, why it costs more. It's you know, it's more expensive as we are using these components for a longer life. You can't say it can last forever because there's you're talking about those odds that something will fail or
Stephen Kraig
Can stack the odds in your favor.
Parker Dillmann
You can stack the odds in your favor. Yeah. I think that's very interesting to think about because my computer for video gaming at home, we were talking about this last year, beginning of last year, was it was starting that computer was starting to fail. Mhmm. It was having weird issues with this hard drive, and we couldn't and I think it's been, like, a month of podcast episodes where, like, I was bringing it on that floor home.
Parker Dillmann
Yeah. It was sitting on the floor, like, with all its guts hanging out because it worked that way. Yeah. And then the moment you reassembled it the normal way, it was it would exhibit the same problem. And then that being, like, the south bridge failed, so all everything that's that runs off the south bridge on that motherboard is just dead.
Parker Dillmann
And, And, but there's some SATA ports that run on the north bridge. And if you plug into that, it works just fine. It doesn't care. And if you use the lower PCI Express lines, doesn't work. If you use the upper ones, totally works fine.
Stephen Kraig
That's weird.
Parker Dillmann
And so I reassembled it in a different configuration, still play games on it every single day. But what's interesting is that motherboard, I bought it. Jeez. 9 years is it almost 9 years old now? And one of the it was it's an Asus TUF, and the selling point was it doesn't have electrolytic capacitors on it.
Parker Dillmann
Mhmm. Because I was bitten by long time ago, capacitor plague was, like, a big thing in motherboards. Probably still is now. I just not in that news sphere anymore. I'm enthusiast computer technology nowadays.
Parker Dillmann
But anyways, back in the day, electrolytic capacitors, there would always be, like, a bad batch, and motherboards would just fail. And so I bought this tough motherboard because it it it quoted what was the quote? Solid state capacitors. Yep. Which means What?
Parker Dillmann
Probably tantalum?
Stephen Kraig
Those were more expensive, so I really doubt it. It probably just Yeah. Tantalum. Yeah.
Parker Dillmann
And I don't know what caused the southbridge to fail on the board, but it did last 9 years or 8 years before it started exhibiting problems, which is the longest I've ever had a motherboard last. Mhmm. So there's that. But definitely did did I it definitely was not an heirloom motherboard, though.
Stephen Kraig
Yeah. I don't know. It starts to get difficult, especially with computers because they are way more of a higher duty cycle product. They are they remain on a lot longer. So they're in, you know, they're functioning all the time, and that just leads to where.
Stephen Kraig
Right? So 9 years sounds actually like a pretty long time for something like that to continuously function. Like I said, I think I don't know how much better you're gonna get than that without doing redundancy.
Parker Dillmann
Yeah. And so that's gonna be interesting looking at I mean, I yeah. I agree on the motherboard side. Yeah. It's just the automotive side.
Parker Dillmann
I think what I'll do is I'll I'll make up my first design, and we'll rip it apart and figure out how to make it last longer without,
Stephen Kraig
Go ahead. Simplicity helps so much because the fewer items you have in there, your your probability of survival goes up. The one of the main drivers in reliability is is part count. The more parts you have because because if you think of everything as a system, you ask the question, what is the probability of a failure? For every part that you add in there, you add probability of failure.
Stephen Kraig
Now you have to define what a failure means in that sense. Okay. Let's say you have a TV with a 1000000 LEDs on it or a 1000000000 LEDs on it. If 1 LED fails, is that considered a failure?
Parker Dillmann
Oh, yeah. The whole dead pixel argument.
Stephen Kraig
Right. Right. Is that considered a failure? If so, I bet you if you run the reliability calculation on TVs, you get abysmal numbers just because of the part count. But their reliability is actually a lot better than that.
Stephen Kraig
So so the calculations actually do start to fall apart when you have trouble defining what failure means. But in an automotive sense, there's you end up having a lot fewer functions that it does. Right? It's not like you're not doing a 1,000,000 things. You're doing 15 or or whatever.
Stephen Kraig
So what's nice is in your case, you can rely a lot on those calculations because it is way more stripped down and you can really you can define what a failure means. If this output just stops doing the output, that's a failure. Right? Yep. And I'm assuming a lot of the stuff that you wanting to design probably doesn't have a lot of maybe I'm wrong here, but probably doesn't have a lot of analog control.
Stephen Kraig
Right? It's probably a lot more digital or just binary on off kind of stuff.
Parker Dillmann
Yeah. Well, the outputs yeah. The inputs are mostly analog, though.
Stephen Kraig
Well, yeah. You have sensor readings and things like that.
Parker Dillmann
Yeah. You're writing reading sensors that are usually, like, 0 to 5 volt sensors.
Stephen Kraig
Right. So not, one thing you can do to increase, reliability is do what's called an EPSA, electronics parts stress analysis, where you take every single part and you say, here's the max rated from the customer or not sorry, the manufacturer. Here's a resistor. It says that it can handle 1 watt. What am I running this resistor at?
Stephen Kraig
Am I running it at 1 watt? Is it at its maximum rated? Well, it it will have a degraded life compared to if you're running at 700 milliwatts or if you're running at half a watt. And so what you can do is do an EPSA where you arbitrarily pick derated values. So, say, a ceramic capacitor.
Stephen Kraig
Let's say, you want a ceramic capacitor. I'm just gonna pick a random number. Let's say, a cap that's on a 24 volt line. That cap has to be rated for at least 24 volts, so you could pick a 25 volt cap. Right?
Stephen Kraig
Because that technically meets derating or not derating. That technically meets the maximum rated. But it might make more sense to pick a higher rated cap or, you know, pick any parameter, derate it by a certain amount, and you can actually extend the life of that component. And so if you want to get further reliability numbers or if you wanna get further life out there, pick arbitrarily or, you know, go do some research on on, you know, industry, what their derating values are. A lot of times with this stuff, it's just 50%, 50 or 60%.
Stephen Kraig
A lot of times with with things like tantalum capacitors, it's actually 30%. You derate all the way down to 30% of them of the part, and then you get extended life out of it. So there's a lot of little tricks like that where the circuit doesn't change. You just pick an appropriate component based off of what kind of lifespan you're trying to get out of it. So there's really fun.
Stephen Kraig
If if you really wanna put yourself to sleep, there's fun documents out there that just go part by part that says ceramic capacitors, here's their derating values. Bipolar junction transistors, here's their derating values. Blah blah blah. And just just hundreds of pages of if you got this, run this test, do this derating. If you got this, you know, I could I could show you those if you really wanna fall asleep.
Stephen Kraig
But, actually, you know what? That that would be a fun thing to do. If you come up with a design, it would be fun for us to do a an EPSA analysis.
Parker Dillmann
Yeah. On that. Yeah. We can do it as a as a, yeah, exercise. I don't know if that would make great podcast content if
Stephen Kraig
You know you you know what might make fun? Doing it live would be awful content, but what might be fun is doing a first stab at a design, and then you and I do the analysis and see how close did you get to derating in a high reliability application with your first gut check on parts, and then come back and say, we had to change this and this. Now it's really difficult to say because we change these things, you'll get an extra 5 years or 10 years of lifespan. It's really difficult to put a number on that, but, you can't say that you at least analyzed it for higher reliability.
Parker Dillmann
Yeah. Yeah. Well, looks like I need to start a design then.
Stephen Kraig
Yeah. I'm excited now. Let's do this.
Parker Dillmann
Yeah. It's gonna be a lot of fun. I don't know if there's any breakers still listening, but would you want us to do a podcast episode about that? Let us know in the discussion, form.macrev.com. So we have this other topic.
Parker Dillmann
We can just go right into it. It'd be a long episode.
Stephen Kraig
Why don't you know what? Why don't we actually, I'm gonna I'm gonna say, because we're at an hour, let's put this let's push this one. Let's go ahead and leave this for another time or yeah. I think That'd
Parker Dillmann
be the first thing we'll talk about next week.
Stephen Kraig
I think that that
Parker Dillmann
works. Yeah. It's the Justice Department sues Apple from monopolizing smartphone markets. So we'll talk about that first first thing. We won't get sidetracked for 30 minutes talking about
Stephen Kraig
Project manager.
Parker Dillmann
AI. Yeah. Project management with AI. So thank you, everyone, for listening to circuit break for MacFab. We are your hosts, Perky Dolan.
Stephen Kraig
And Steven Craig.
Parker Dillmann
Later, everyone.
Stephen Kraig
Take it easy.
Parker Dillmann
Thank you, Yes You Breaker, for downloading our podcast. Tell your friends and coworkers about circuit break the podcast for Macofab. Please, we need more listeners.
Stephen Kraig
Also, go give us a review.
Parker Dillmann
Yeah give us a review I think there's a link we have a new like email newsletter now I don't think you can immediately sign up for it yet which is not good, but it exists. And I bet you some listeners here got that email on Monday, but there's a link in that email that we'll send you to Apple to review us. I don't know if there's other places where you can review us, but please review us. We need more listeners. Everyone out there that listens right now is very loyal y'all listen to every single word that we say even this word right here So if you have a cool idea project or topic you want us to discuss or the community to discuss let us know It's form.macfab.com, where we talk about personal projects, discussions about the podcast, engineering topics, and news.
Parker Dillmann
That's form.macrofab.com. And I just fixed it. It used to if you just went to there without logging in, it would only show you half the content there. Fixed it. So now you see everything.
Parker Dillmann
If you even if you you can go there without even logging in and just you can view. You can, like, peep into the window.
Related Podcasts
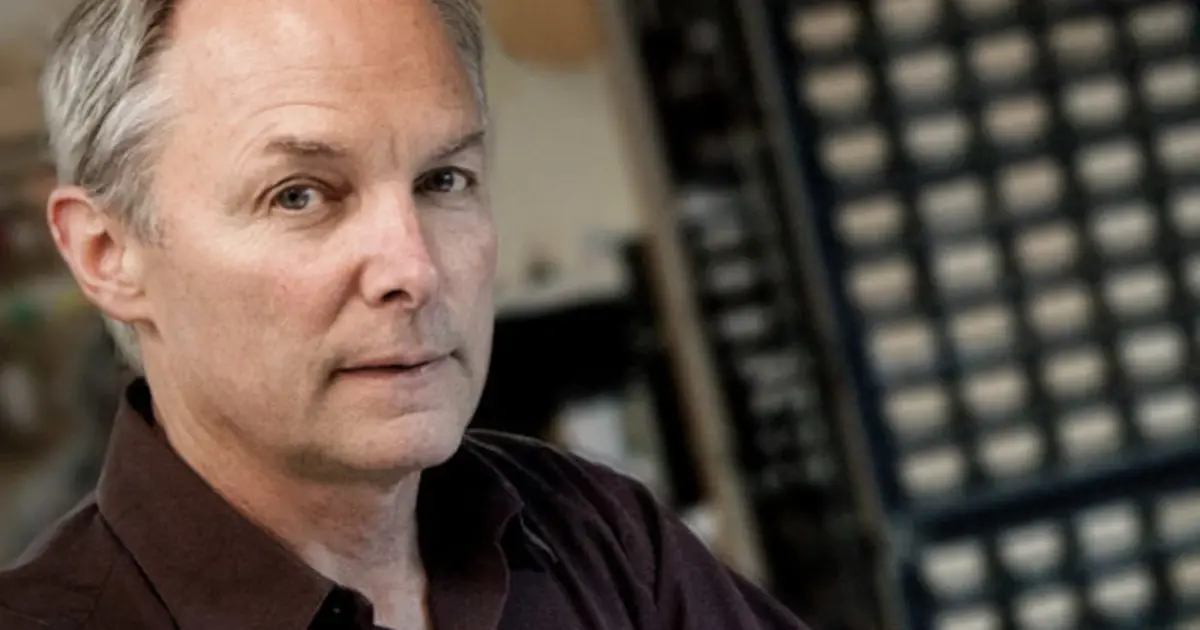
Kevin Beller of Seymour Duncan
Kevin Beller discusses his history with Seymour Duncan and how an engineer sells a creative idea.
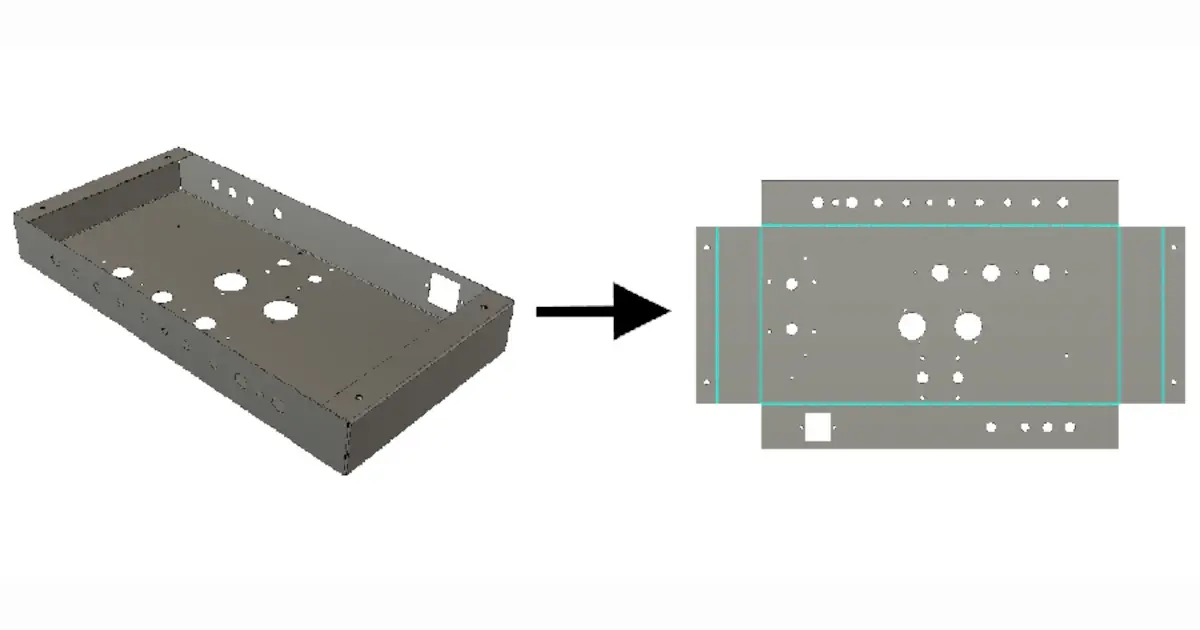
K-Factoring a Gumbo
Stephen finally gets a license for the Eagle EDA Tool but not for the reasons you would expect! Also, sheet metal design and IoT device security!
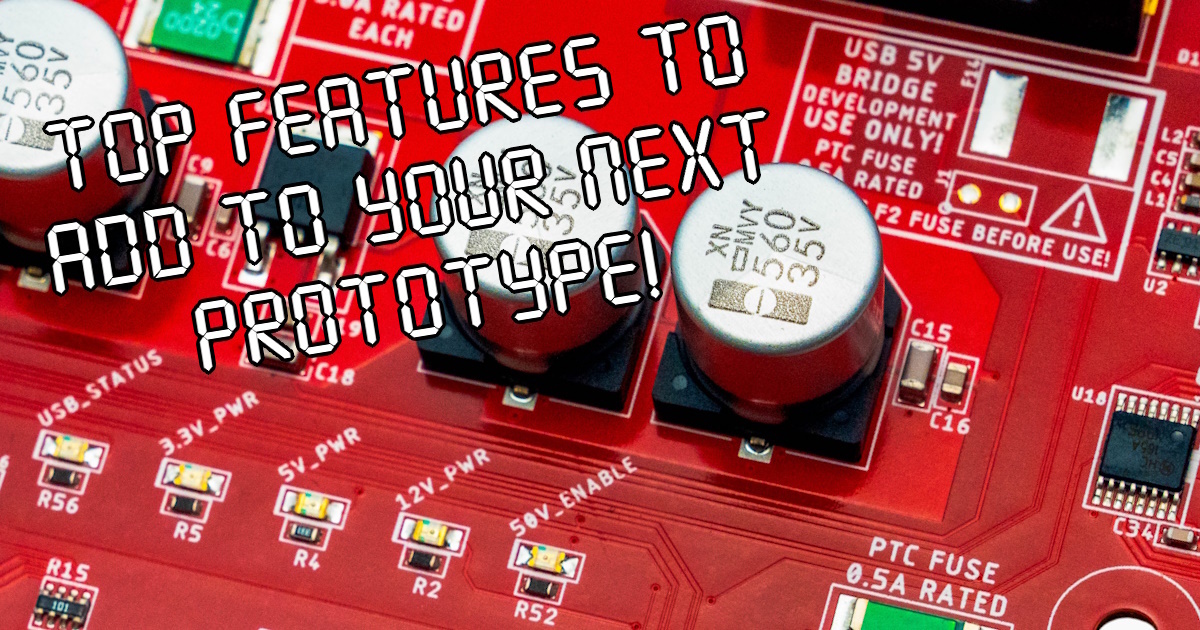
Top Features to Add to Your Next Prototype
Tune in as we share insights, anecdotes, and maybe a few confessions from our own prototyping adventures.
About MacroFab
MacroFab offers comprehensive manufacturing solutions, from your smallest prototyping orders to your largest production needs. Our factory network locations are strategically located across North America, ensuring that we have the flexibility to provide capacity when and where you need it most.
Experience the future of EMS manufacturing with our state-of-the-art technology platform and cutting-edge digital supply chain solutions. At MacroFab, we ensure that your electronics are produced faster, more efficiently, and with fewer logistic problems than ever before.
Take advantage of AI-enabled sourcing opportunities and employ expert teams who are connected through a user-friendly technology platform. Discover how streamlined electronics manufacturing can benefit your business by contacting us today.