Circuit Break Podcast #309
Perpetual Prototypes
Did Stephen and Parker complete there holiday projects?
Related Topics
Eighth Annual MacroFab Star Wars Christmas Special
Not unlike Han Solo emerging from cryosleep, the annual MacroFab Star Wars Christmas Special is back!
Screaming into the Social Media Void
AutoDesk is dropping support and development for the dedicated Eagle EDA tool and moving efforts to the AutoDesk Fusion 360 Electronics.
Seventh Annual Star Wars Christmas Special
Will the Rebel Codebreakers be able to emerge victorious against the Empire, or will they succumb to the overwhelming power of the Empire? Tune in!
Other Resources
Circuit Break Podcast
Webinars
Videos
Tour MacroFab's ITAR-Compliant Facility
December 29, 2021, Episode #309
- Tube Compressor
- Stephen “Completed”
- Wants to add more features….
- Synchrotron phaser
- Works but needs value tweaking on some gains
- Have a sample of the audio in the podcast
- Parker’s Mother’s Golf Cart
- Finished paint and started reassembly!
SendcutSend sheet metal bending experience
- Sent off a design for a custom rack mount shelf
- Used Autodesk Fusions Sheet Metal tool to design it
- Parts came out great!
- Looking forward to trying Xometry’s new sheet metal service
- SendcutSend offers powdercoating now?
Pinouts.org
- Art that is also functional?
- Some really cool t-shirts as well!
About the Hosts
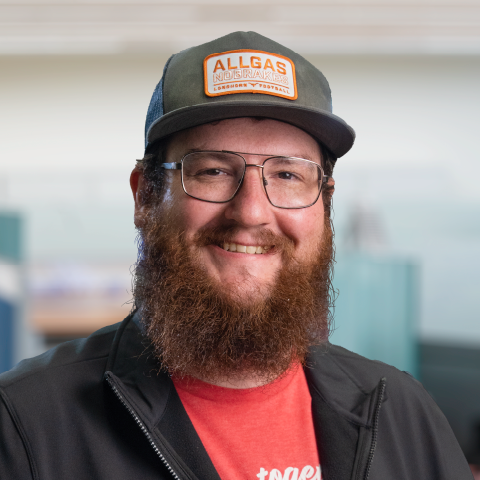
Parker Dillmann
Parker is an Electrical Engineer with backgrounds in Embedded System Design and Digital Signal Processing. He got his start in 2005 by hacking Nintendo consoles into portable gaming units. The following year he designed and produced an Atari 2600 video mod to allow the Atari to display a crisp, RF fuzz free picture on newer TVs. Over a thousand Atari video mods where produced by Parker from 2006 to 2011 and the mod is still made by other enthusiasts in the Atari community.
In 2006, Parker enrolled at The University of Texas at Austin as a Petroleum Engineer. After realizing electronics was his passion he switched majors in 2007 to Electrical and Computer Engineering. Following his previous background in making the Atari 2600 video mod, Parker decided to take more board layout classes and circuit design classes. Other areas of study include robotics, microcontroller theory and design, FPGA development with VHDL and Verilog, and image and signal processing with DSPs. In 2010, Parker won a Ti sponsored Launchpad programming and design contest that was held by the IEEE CS chapter at the University. Parker graduated with a BS in Electrical and Computer Engineering in the Spring of 2012.
In the Summer of 2012, Parker was hired on as an Electrical Engineer at Dynamic Perception to design and prototype new electronic products. Here, Parker learned about full product development cycles and honed his board layout skills. Seeing the difficulties in managing operations and FCC/CE compliance testing, Parker thought there had to be a better way for small electronic companies to get their product out in customer's hands.
Parker also runs the blog, longhornengineer.com, where he posts his personal projects, technical guides, and appnotes about board layout design and components.
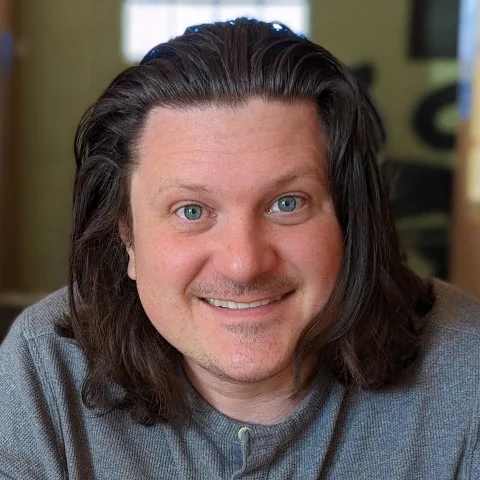
Stephen Kraig
Stephen Kraig is a component engineer working in the aerospace industry. He has applied his electrical engineering knowledge in a variety of contexts previously, including oil and gas, contract manufacturing, audio electronic repair, and synthesizer design. A graduate of Texas A&M, Stephen has lived his adult life in the Houston, TX, and Denver, CO, areas.
Stephen has never said no to a project. From building guitar amps (starting when he was 17) to designing and building his own CNC table to fine-tuning the mineral composition of the water he uses to brew beer, he thrives on testing, experimentation, and problem-solving. Tune into the podcast to learn more about the wacky stuff Stephen gets up to.
Credits
Special thanks to whixr over at Tymkrs for the intro and outro!
Related Podcasts
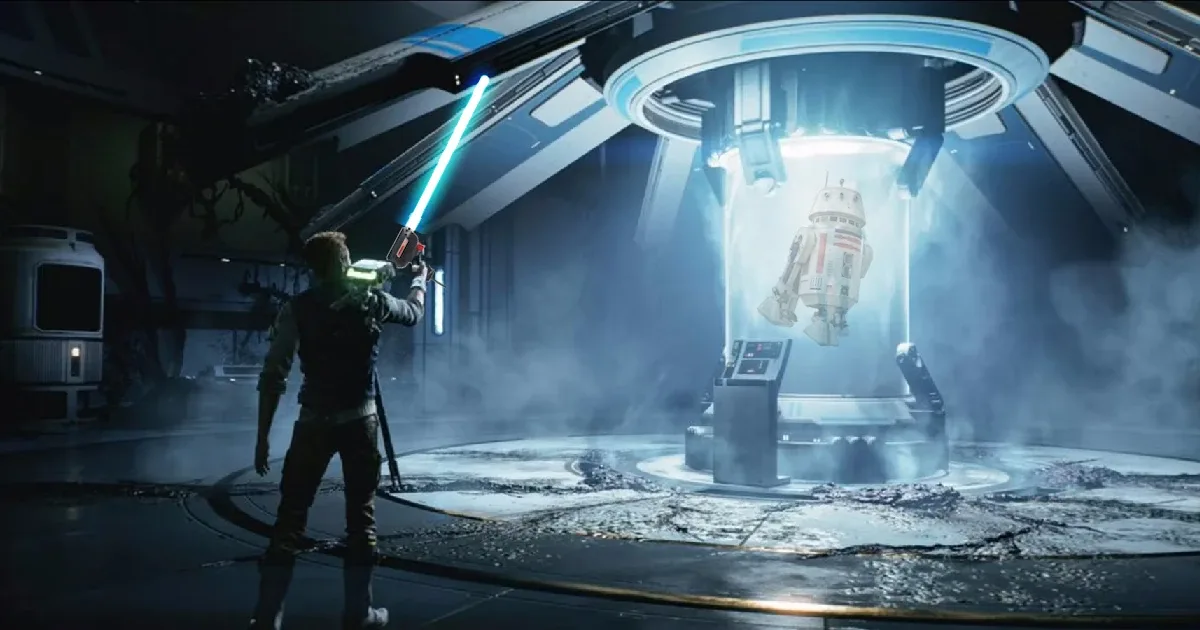
Eighth Annual MacroFab Star Wars Christmas Special
Not unlike Han Solo emerging from cryosleep, the annual MacroFab Star Wars Christmas Special is back!
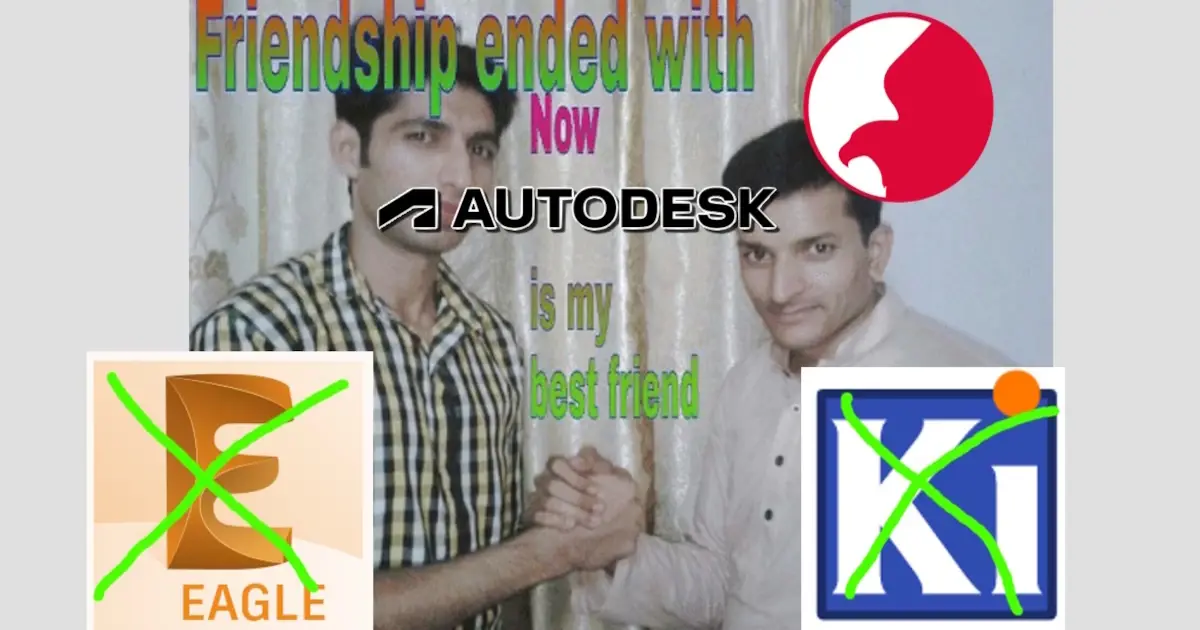
Screaming into the Social Media Void
AutoDesk is dropping support and development for the dedicated Eagle EDA tool and moving efforts to the AutoDesk Fusion 360 Electronics.
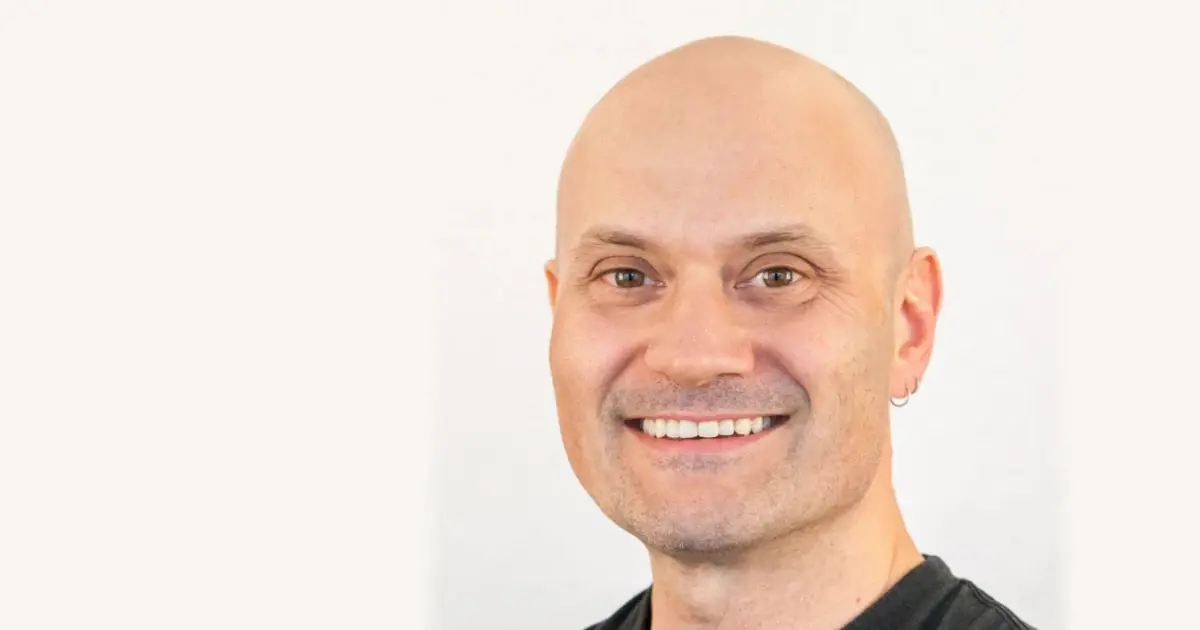
Benjamin Jordan of Autodesk
Senior Product Manager for ECAD in Autodesk Fusion 360, Ben Jordan, joins Stephen and Parker to discus the future of ECAD, Eagle, Autodesk, and PCBs.
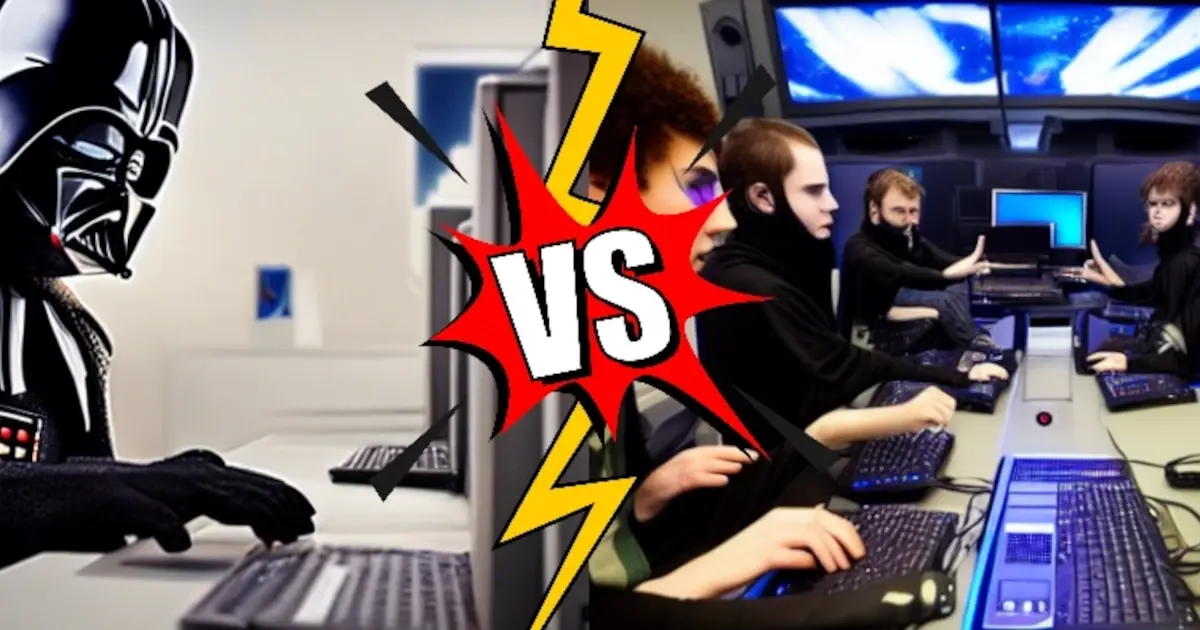
Seventh Annual Star Wars Christmas Special
Will the Rebel Codebreakers be able to emerge victorious against the Empire, or will they succumb to the overwhelming power of the Empire? Tune in!
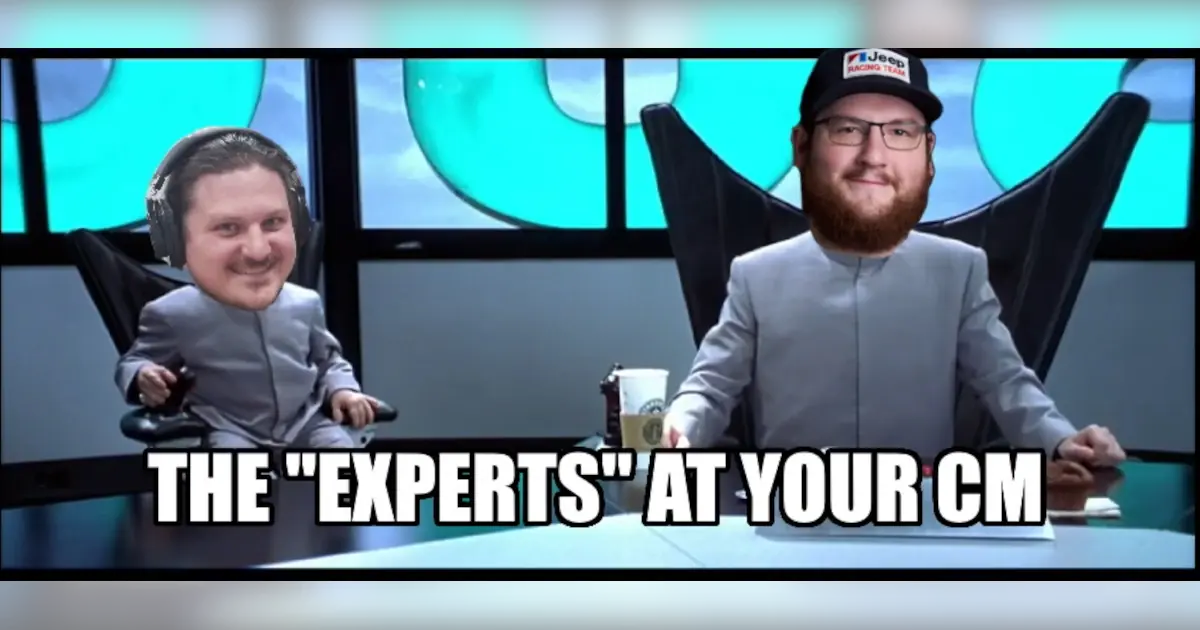
The Expert
Design for Testing means enabling your product to be tested easier or quicker. But what about the documentation and implementation of the testing?
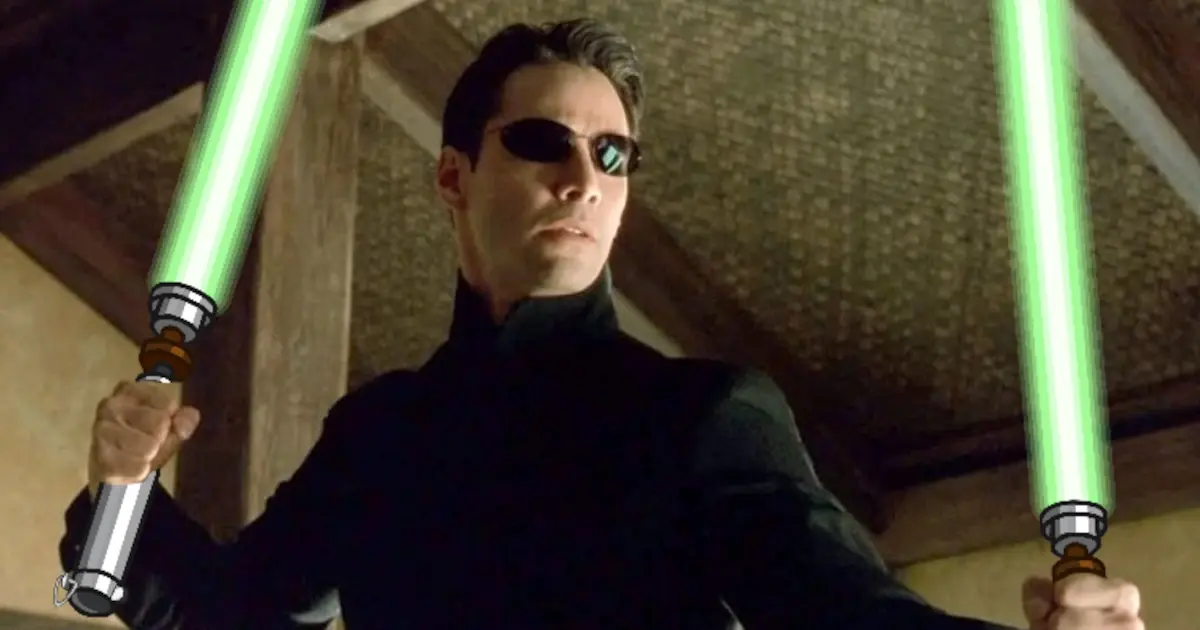
Fifth Annual MacroFab Star Wars Christmas Special – Neo Jedi
On this episode, Josh Rozier joins to discuss Star Wars. Is the force a glitch in the Matrix? How much energy does it take to vaporize a Jawa?
About MacroFab
MacroFab offers comprehensive manufacturing solutions, from your smallest prototyping orders to your largest production needs. Our factory network locations are strategically located across North America, ensuring that we have the flexibility to provide capacity when and where you need it most.
Experience the future of EMS manufacturing with our state-of-the-art technology platform and cutting-edge digital supply chain solutions. At MacroFab, we ensure that your electronics are produced faster, more efficiently, and with fewer logistic problems than ever before.
Take advantage of AI-enabled sourcing opportunities and employ expert teams who are connected through a user-friendly technology platform. Discover how streamlined electronics manufacturing can benefit your business by contacting us today.