Related Topics
Captured Pads
Parker & Stephen dive into Circuit Break Discourse, LT3073 regulator, Weldestroyer updates, Box Truk progress, and more!
Don’t Let AI Brew Your Beer
Parker and Stephen discuss Chat GPT-3, a language processing AI system, and what it can mean for engineers and society.
Skippy Documentation
Are Stephen's LM338 regulators fake? Parker uses X-Ray vision to find out the answer! This and an Adventure in Plastic Injection Molding this week.
Other Resources
Circuit Break Podcast
Webinars
Videos
Tour MacroFab's ITAR-Compliant Facility
May 5, 2021, Episode #275
- Log stepper
- Exercise in madness
- 24 position stepped attenuator
- 1db steps with step 0 being -infinite and step 24 being 0db attenuation
- Requires lots of non-standard resistor values
- Constant total resistance
- Excel sheet
- Make before break operation
- Revision workflow
- How do you document and handle revisions for schematics and pcbs?
- Process
- Get new rev
- Go to testing
- Find issues and document
- Make new revision
- Repeat
- Venturing into hobby level SLA printing
- Elegoo Mars 2
- Quality is amazing
- Print speed is interesting
- Will have to experiment with different resins to find a high strength, high temperature
- Plating process to test
- Elegoo Mars 2
- Amplifier update
- Live next week on parts replacement?
- Recovering it
About the Hosts
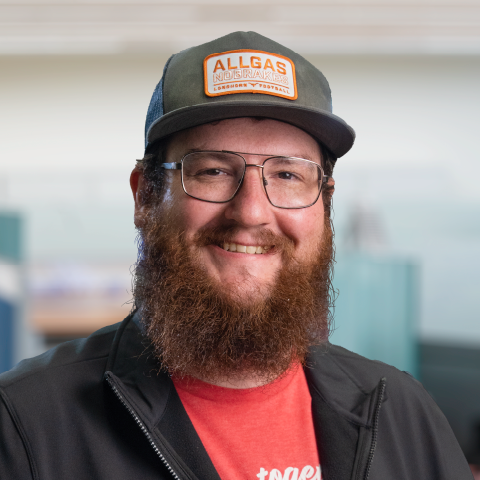
Parker Dillmann
Parker is an Electrical Engineer with backgrounds in Embedded System Design and Digital Signal Processing. He got his start in 2005 by hacking Nintendo consoles into portable gaming units. The following year he designed and produced an Atari 2600 video mod to allow the Atari to display a crisp, RF fuzz free picture on newer TVs. Over a thousand Atari video mods where produced by Parker from 2006 to 2011 and the mod is still made by other enthusiasts in the Atari community.
In 2006, Parker enrolled at The University of Texas at Austin as a Petroleum Engineer. After realizing electronics was his passion he switched majors in 2007 to Electrical and Computer Engineering. Following his previous background in making the Atari 2600 video mod, Parker decided to take more board layout classes and circuit design classes. Other areas of study include robotics, microcontroller theory and design, FPGA development with VHDL and Verilog, and image and signal processing with DSPs. In 2010, Parker won a Ti sponsored Launchpad programming and design contest that was held by the IEEE CS chapter at the University. Parker graduated with a BS in Electrical and Computer Engineering in the Spring of 2012.
In the Summer of 2012, Parker was hired on as an Electrical Engineer at Dynamic Perception to design and prototype new electronic products. Here, Parker learned about full product development cycles and honed his board layout skills. Seeing the difficulties in managing operations and FCC/CE compliance testing, Parker thought there had to be a better way for small electronic companies to get their product out in customer's hands.
Parker also runs the blog, longhornengineer.com, where he posts his personal projects, technical guides, and appnotes about board layout design and components.
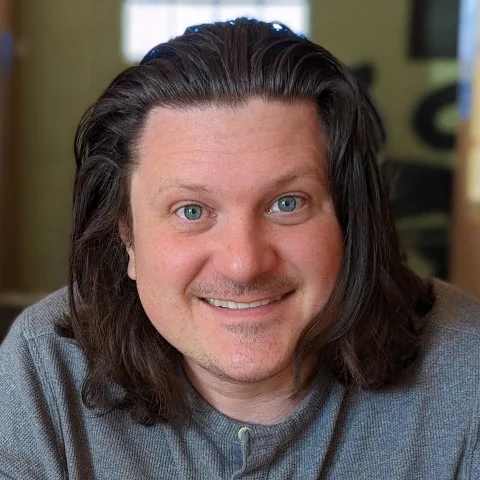
Stephen Kraig
Stephen Kraig is a component engineer working in the aerospace industry. He has applied his electrical engineering knowledge in a variety of contexts previously, including oil and gas, contract manufacturing, audio electronic repair, and synthesizer design. A graduate of Texas A&M, Stephen has lived his adult life in the Houston, TX, and Denver, CO, areas.
Stephen has never said no to a project. From building guitar amps (starting when he was 17) to designing and building his own CNC table to fine-tuning the mineral composition of the water he uses to brew beer, he thrives on testing, experimentation, and problem-solving. Tune into the podcast to learn more about the wacky stuff Stephen gets up to.
Special thanks to whixr over at Tymkrs for the intro and outro!
Related Podcasts
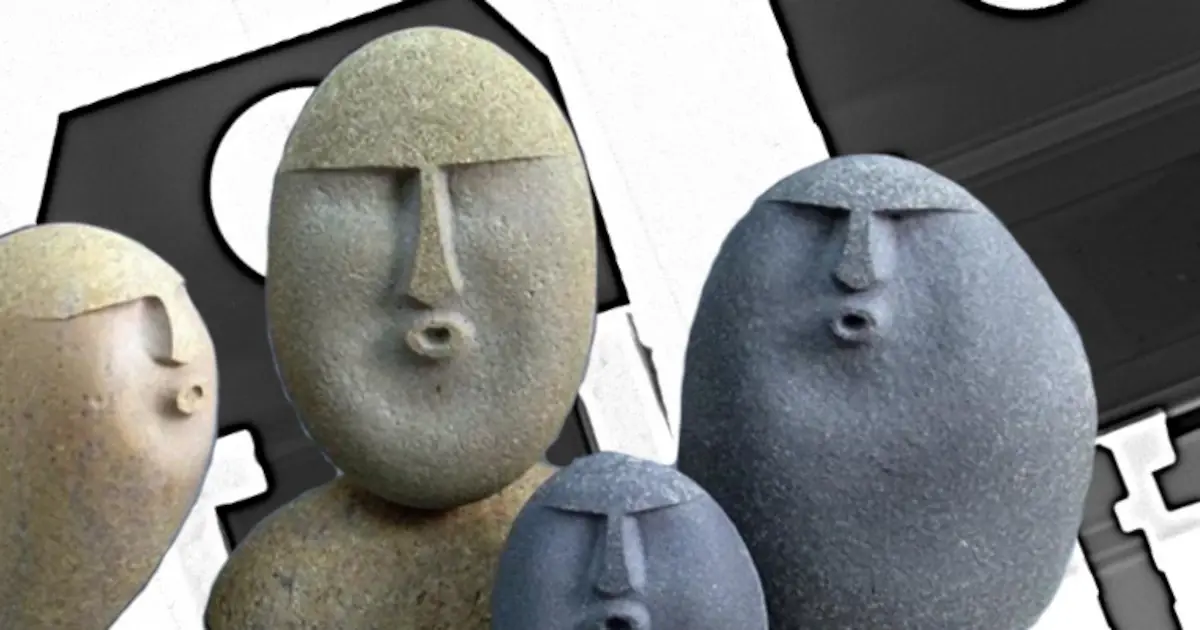
Skippy Documentation
Are Stephen's LM338 regulators fake? Parker uses X-Ray vision to find out the answer! This and an Adventure in Plastic Injection Molding this week.
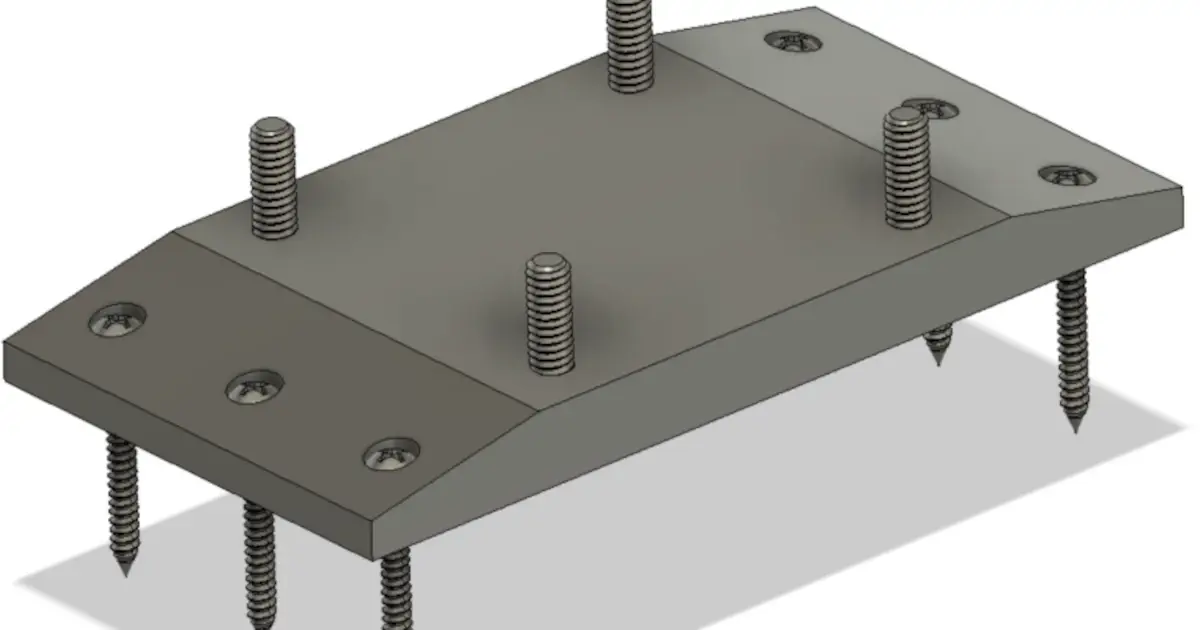
Just Another Meatloaf Title
Why are all Python PDF creator modules just terrible to work with? Does anyone have one they like? Help me. Oh and Stephen's CNC machine is moving!
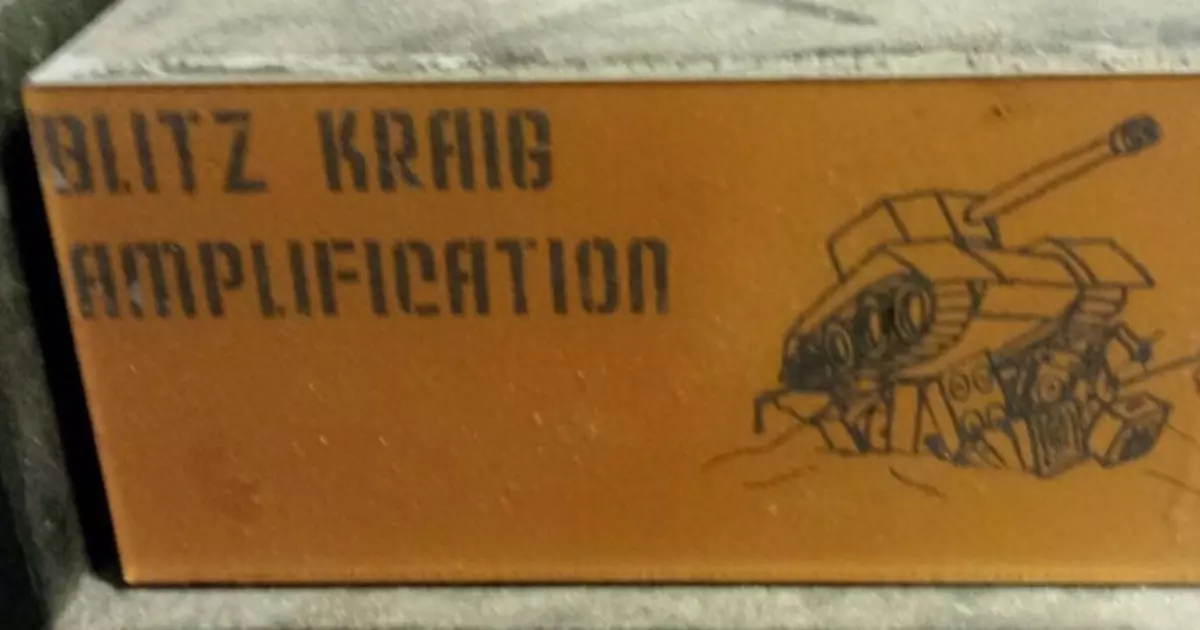
Gotta Look Pro
It is National Engineers Week and Stephen spills the beans on his Audio Amplifier Past.
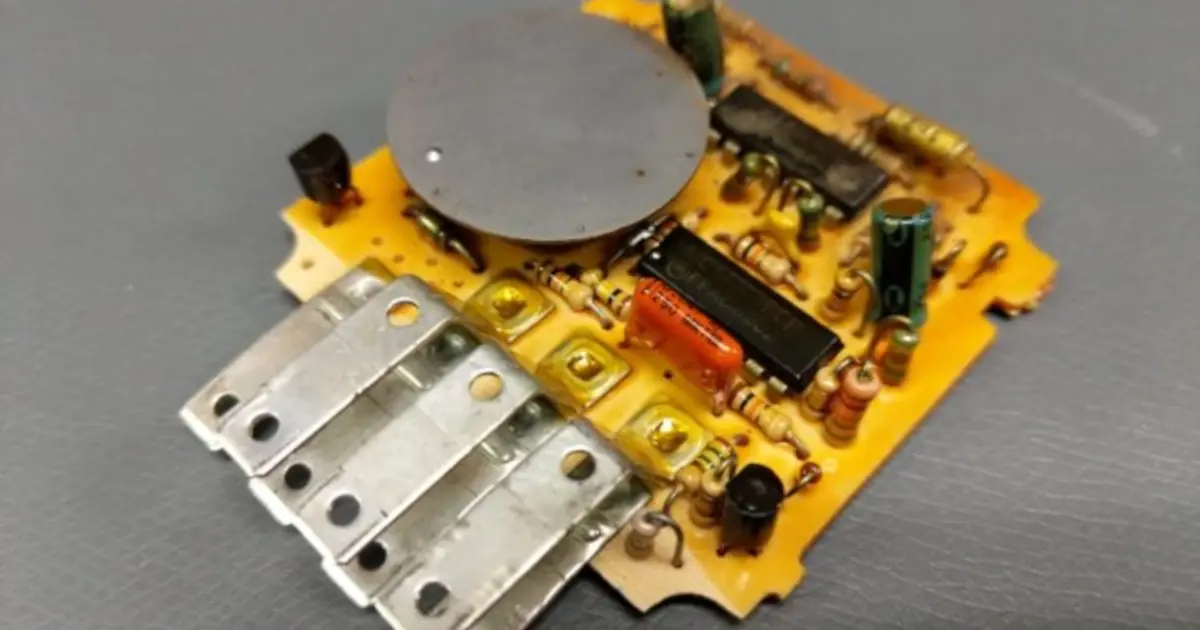
Big Mattress is Coming For You
Come celebrate the third anniversary of the MEP as Parker and Stephen discuss a potential video game.
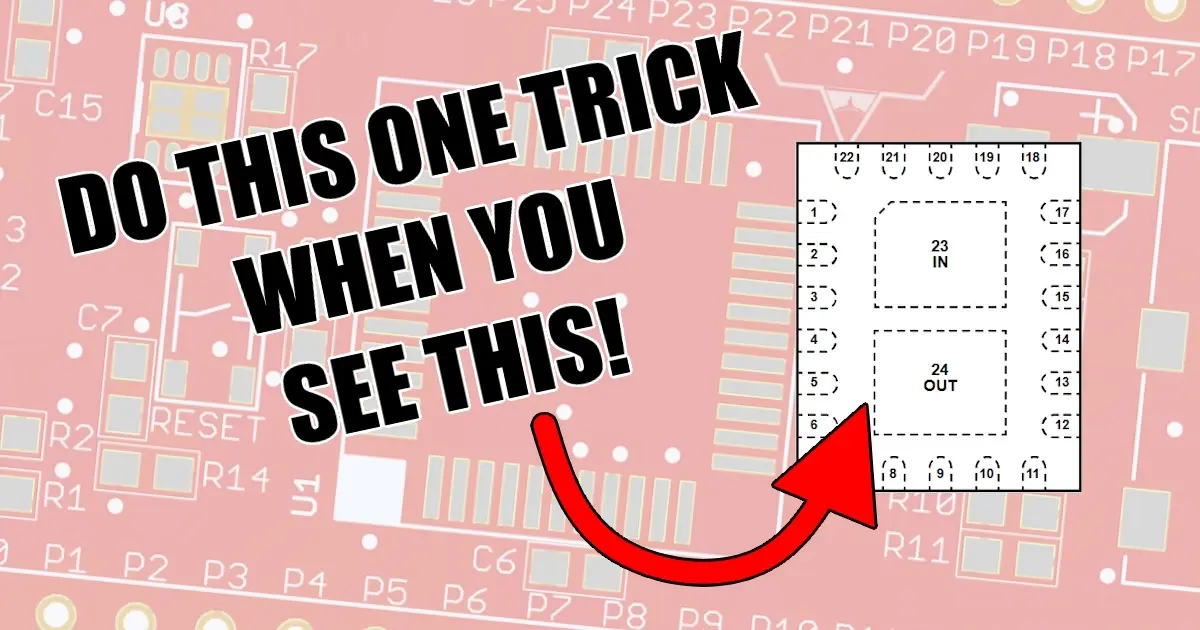
Captured Pads
Parker & Stephen dive into Circuit Break Discourse, LT3073 regulator, Weldestroyer updates, Box Truk progress, and more!
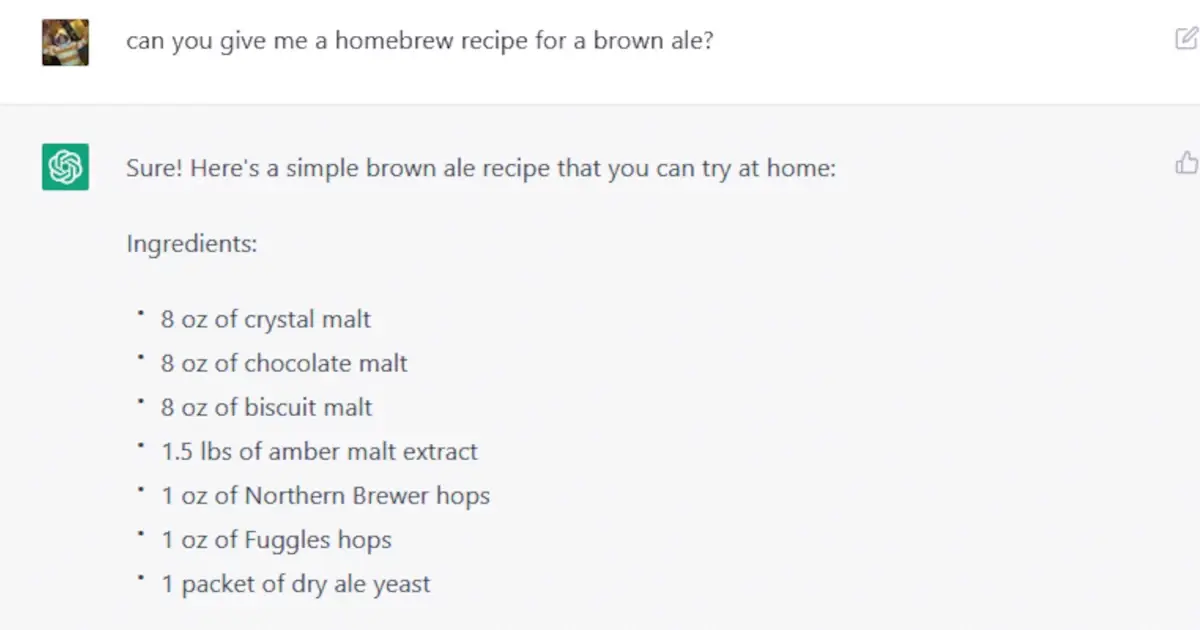
Don’t Let AI Brew Your Beer
Parker and Stephen discuss Chat GPT-3, a language processing AI system, and what it can mean for engineers and society.
About MacroFab
MacroFab offers comprehensive manufacturing solutions, from your smallest prototyping orders to your largest production needs. Our factory network locations are strategically located across North America, ensuring that we have the flexibility to provide capacity when and where you need it most.
Experience the future of EMS manufacturing with our state-of-the-art technology platform and cutting-edge digital supply chain solutions. At MacroFab, we ensure that your electronics are produced faster, more efficiently, and with fewer logistic problems than ever before.
Take advantage of AI-enabled sourcing opportunities and employ expert teams who are connected through a user-friendly technology platform. Discover how streamlined electronics manufacturing can benefit your business by contacting us today.