Circuit Break Podcast #203
Lizard Brain Information – David Gunness of Fulcrum Acoustic
Related Topics
Conductive Cuisine
We'll explore an in-depth study conducted by Seth Jenkins, Neil LaTourette, and Brendan Liverman on how boiling time affects hot dog conductivity.
Wanting to be a Wizard - Matt Brown
Matt Brown, shares his career insights, including his experiences working at Tesla and on personal projects like the land speed car and the off-road Viper.
Exploring the Arctic Through Art and Technology with Cy Keener
Cy Keener's work includes a range of data-based efforts to visualize diverse phenomena including ice, wind, rain, and ocean waves.
Other Resources
Circuit Break Podcast
Webinars
Videos
Tour MacroFab's ITAR-Compliant Facility
December 18, 2019, Episode #203
David Gunness
- Vice President of R&D at Fulcrum Acoustic
- Lead Product Designer
- Photographer
- Copy Writer
- Ambassador to Italy
- Facilities Maintenance
- Director of Calculus
- Technical Writer
- Lead Coffee Maker
Fulcrum Acoustic
- Who are they and what do they do?
- What does it take to get into sound design?
- Education?
- Frequency Theory
- Passive Cardioid Technology
- Technology to eliminate rear low frequency radiation
- Where is this an issue?
- Active solution
- Passive solution
- Patent 10,123,111 B2 “Loudspeaker with passive low frequency directional control”
- Technology to eliminate rear low frequency radiation
- Building a better coaxial speaker
- What is a coax?
- Beamwidth
- How is this validated/tested?
- Manufacturing enclosures with wood
- Why wood?
- Sourcing materials
- General Design
- Tolerancing considerations?
- Finishing and Covering
- Sanding
- Painting
- Spraying materials
About the Hosts
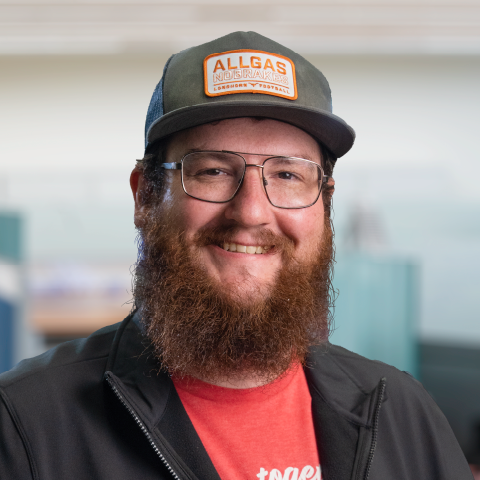
Parker Dillmann
Parker is an Electrical Engineer with backgrounds in Embedded System Design and Digital Signal Processing. He got his start in 2005 by hacking Nintendo consoles into portable gaming units. The following year he designed and produced an Atari 2600 video mod to allow the Atari to display a crisp, RF fuzz free picture on newer TVs. Over a thousand Atari video mods where produced by Parker from 2006 to 2011 and the mod is still made by other enthusiasts in the Atari community.
In 2006, Parker enrolled at The University of Texas at Austin as a Petroleum Engineer. After realizing electronics was his passion he switched majors in 2007 to Electrical and Computer Engineering. Following his previous background in making the Atari 2600 video mod, Parker decided to take more board layout classes and circuit design classes. Other areas of study include robotics, microcontroller theory and design, FPGA development with VHDL and Verilog, and image and signal processing with DSPs. In 2010, Parker won a Ti sponsored Launchpad programming and design contest that was held by the IEEE CS chapter at the University. Parker graduated with a BS in Electrical and Computer Engineering in the Spring of 2012.
In the Summer of 2012, Parker was hired on as an Electrical Engineer at Dynamic Perception to design and prototype new electronic products. Here, Parker learned about full product development cycles and honed his board layout skills. Seeing the difficulties in managing operations and FCC/CE compliance testing, Parker thought there had to be a better way for small electronic companies to get their product out in customer's hands.
Parker also runs the blog, longhornengineer.com, where he posts his personal projects, technical guides, and appnotes about board layout design and components.
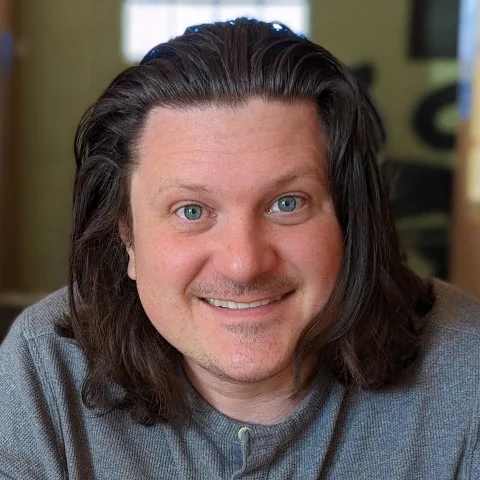
Stephen Kraig
Stephen Kraig is a component engineer working in the aerospace industry. He has applied his electrical engineering knowledge in a variety of contexts previously, including oil and gas, contract manufacturing, audio electronic repair, and synthesizer design. A graduate of Texas A&M, Stephen has lived his adult life in the Houston, TX, and Denver, CO, areas.
Stephen has never said no to a project. From building guitar amps (starting when he was 17) to designing and building his own CNC table to fine-tuning the mineral composition of the water he uses to brew beer, he thrives on testing, experimentation, and problem-solving. Tune into the podcast to learn more about the wacky stuff Stephen gets up to.
Special thanks to whixr over at Tymkrs for the intro and outro!