Circuit Break Podcast #425
MacroFab Platform Updates from Kyle McLeod and Nicholas Lundgard
Related Topics
Tracing a Path for PCB Design Automation with Sergiy Nesterenko
Sergiy Nestorenko, founder of Quilter and former SpaceX engineer, discusses revolutionizing PCB design automation.
Dr. Duncan Haldane from JITX on Automating Circuit Design
Dr. Haldane on his background, the problems JITX is trying to resolve, & new auto-router plans. What's the deal with the "hyper-aggressive pogo-stick"?
Breadboarding for Success
This week we are talking about Breadboards. Is breadboarding a circuit or design still applicable in today's SMT component dominated world?
Other Resources
Circuit Break Podcast
Webinars
Videos
Tour MacroFab's ITAR-Compliant Facility
April 9, 2024, Episode #425
This week, hosts Parker Dillmann and Stephen Craig are joined by Kyle McLeod, the OE Project Manager, and Nicholas Lundgaard, the OE Team Lead at MacroFab. They delve into recent software releases enhancing the ordering experience on the MacroFab platform, including ITAR compliance, improvements in design file uploads, and the introduction of customer-furnished material options. They discuss the importance of seamless user interactions for uploading PCBs, placing orders, and how MacroFab's platform facilitates these processes. The episode provides insights into MacroFab's efforts to make PCB manufacturing more accessible and efficient for their customers.
Discussion Highlights
- Introduction of ITAR compliance and its significance for MacroFab's platform and users.
- Enhancements in PCB design file uploads, including support for additional file types and improved user interface.
- The role and benefits of customer-furnished material options in the ordering process.
- Discussions on intelligent overage logic for parts ordering and the impact on manufacturing efficiency.
- The introduction of completed board photo updates for quality assurance and customer verification.
- Preview of upcoming features and improvements, focusing on user interface enhancements, bomb management tools, and expanded quoting capabilities.
Relevant Links
Community Questions
- Have you used MacroFab's platform for your PCB manufacturing needs? Share your experiences and any features you'd love to see in the future.
- What challenges have you faced in PCB design and ordering, and how do you think platforms like MacroFab can solve them?
- How important is ITAR compliance for your projects, and what has been your experience dealing with ITAR-compliant manufacturers?
- What features would you like to see added to the MacroFab platform to improve your experience?
Stephen and Parker discuss the importance of diversity and inclusion with Kaylan Smith, Lead Software Developer for Supply Chain and Finance at MacroFab, and Laura Manley, Product Manager for Marketplace & Factory Experience on EP #436 for International Women in Engineering Day.
About the Hosts
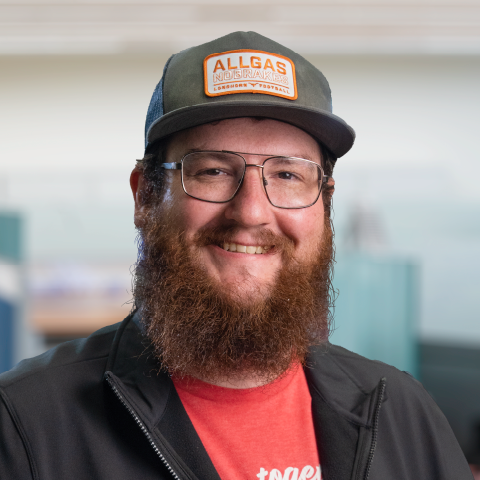
Parker Dillmann
Parker is an Electrical Engineer with backgrounds in Embedded System Design and Digital Signal Processing. He got his start in 2005 by hacking Nintendo consoles into portable gaming units. The following year he designed and produced an Atari 2600 video mod to allow the Atari to display a crisp, RF fuzz free picture on newer TVs. Over a thousand Atari video mods where produced by Parker from 2006 to 2011 and the mod is still made by other enthusiasts in the Atari community.
In 2006, Parker enrolled at The University of Texas at Austin as a Petroleum Engineer. After realizing electronics was his passion he switched majors in 2007 to Electrical and Computer Engineering. Following his previous background in making the Atari 2600 video mod, Parker decided to take more board layout classes and circuit design classes. Other areas of study include robotics, microcontroller theory and design, FPGA development with VHDL and Verilog, and image and signal processing with DSPs. In 2010, Parker won a Ti sponsored Launchpad programming and design contest that was held by the IEEE CS chapter at the University. Parker graduated with a BS in Electrical and Computer Engineering in the Spring of 2012.
In the Summer of 2012, Parker was hired on as an Electrical Engineer at Dynamic Perception to design and prototype new electronic products. Here, Parker learned about full product development cycles and honed his board layout skills. Seeing the difficulties in managing operations and FCC/CE compliance testing, Parker thought there had to be a better way for small electronic companies to get their product out in customer's hands.
Parker also runs the blog, longhornengineer.com, where he posts his personal projects, technical guides, and appnotes about board layout design and components.
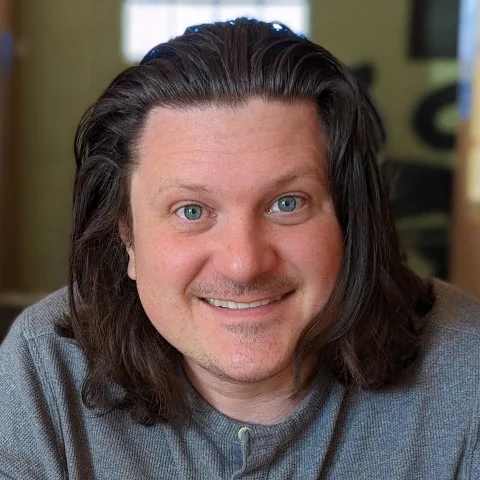
Stephen Kraig
Stephen Kraig is a component engineer working in the aerospace industry. He has applied his electrical engineering knowledge in a variety of contexts previously, including oil and gas, contract manufacturing, audio electronic repair, and synthesizer design. A graduate of Texas A&M, Stephen has lived his adult life in the Houston, TX, and Denver, CO, areas.
Stephen has never said no to a project. From building guitar amps (starting when he was 17) to designing and building his own CNC table to fine-tuning the mineral composition of the water he uses to brew beer, he thrives on testing, experimentation, and problem-solving. Tune into the podcast to learn more about the wacky stuff Stephen gets up to.
Transcript
Parker Dillmann
Welcome to circuit break from MacroFab, a weekly show about all things engineering, DIY projects, manufacturing industry news, and recent MacRAB software releases. We're your hosts, electrical engineers, Parker Dillmann, and Steven Kraig. This is episode 425. And this week, we have Kyle McLeod. I even asked right for the podcast and Nicholas Lundgaard hi hi for the fun.
Kyle McLeod
Yeah. We're excited to be here. Good to be here.
Parker Dillmann
So Kyle is the o e project manager, and Nick is the o e team lead. So what is o e?
Nick Lundgaard
O e is order experience.
Parker Dillmann
Not not original equipment?
Nick Lundgaard
Not original equipment, although definitely did start out as OEM.
Kyle McLeod
Yeah. Yeah. We are the order experience team. So that involves anyone uploading PCBs and placing orders.
Nick Lundgaard
Yep. That's right. Yeah. Design file upload experience, the BOM population, part placements, all that good stuff, getting you to a quote and then placing the order, taking it in. We also have some pretty extensive interfacing with the order view team as well.
Nick Lundgaard
So we we manage the the interface that Macrofabrics use to to validate your part placements and other aspects of your design before we go ahead and process your order.
Parker Dillmann
So you'd be safe to assume, basically, if anyone's using the MacFab platform as a customer, y'all are the ones that Yes. That's absolutely right. So what are y'all's email addresses so people can tell?
Kyle McLeod
Product atmacrofab.com. We really read that one. I I like read all the comments you send there.
Nick Lundgaard
Yeah. And likewise, you know, if you get a customer care ticket that is that is complicated enough that our customer care team needs help, you will you will find me helping you out there.
Parker Dillmann
So you actually do get the respond to customers?
Nick Lundgaard
No. Not directly.
Kyle McLeod
Hop on chat for the first time the other day. Did some live chat with a customer.
Parker Dillmann
Oh, yeah. The the what's that module called?
Kyle McLeod
It's a live chat.
Parker Dillmann
I think it's just called live chat.
Kyle McLeod
It's called live chat. Yeah. There's actually, like, really good people on the other side of it, though. It's one of the things I think people are probably skeptical of because you think you're getting someone, like, you know, in another country or who who knows who but we're actually getting, you know, our our support team who's very well versed in the Macafab platform and sometimes you're getting the the product manager who will try to come in and help get your bomb ready.
Stephen Kraig
So so you guys are watching on the back end, I guess, of what people are doing and trying to sculpt the experience, such that it's what? As pleasant as possible in terms of ordering a board?
Kyle McLeod
Yeah. We we get a lot of We set a lot of tracking events. So we have events when people upload PCB files. You know, we we don't always jump in and look at each one, but I try to look at, I don't know, 3 to 10 PCB uploads a day just to see what people are doing. And then, you know, we have data and metrics around, you know, how how we're doing.
Kyle McLeod
I mean, really, are people able to get their design files from their EDA into our platform in a way that makes sense? Are they able to, you know, get their bomb components uploaded? Do we match them with market parts? Do we have those parts available? We're tracking all of that, you know, as a metric for our excellence of, like, are we are we getting you, like, what you want, which is, like, you wanna automatically price your PCB, but we wanna deliver that as smoothly as possible.
Kyle McLeod
And so we track that at a, you know, big picture level of, you know, looking at metrics and then, you know, individual boards. I'll jump in just to see because there's some nitty gritty details sometimes, you know, someone says they can't get their components in through their o d b plus plus project. Okay. Are those components in the component layers and we're just not grabbing them? Are they using, you know, some manufacturer MPN names that we're not extracting from?
Kyle McLeod
You can try to, like, troubleshoot that stuff to get as much of the data out and into our platform as possible.
Parker Dillmann
Before we dive too much more back into that, I wanna know more about y'all's backgrounds. What led up to y'all being on to this podcast? Because I know Nick was like, no. I've never been on a podcast ever.
Nick Lundgaard
That is true.
Parker Dillmann
Kyle was like hell yeah let's go. Like 2 opposite spectrums here.
Nick Lundgaard
Yeah for sure even.
Kyle McLeod
Yeah. So I have a mechanical engineering background. I started out as a, design engineer and manufacturing engineer, but doing, oil and gas drilling equipment. Did that for a few years and then decided I wanted to get into product management and tech, and so I went back to school for a couple of years, like, my MBA, and then was at a software company that did insurance marketing, which, while not exciting, there's a lot of awesome data and marketing experience that I gained from that and then got an opportunity to join Macrofab and saw it as an awesome opportunity to kind of combine that passion I have for engineering and building things with some software experience and desire ahead to, like, actually launch software products that, you know, while while we don't build the cool stuff, like, we, you know, we help people build really cool products and so that that's that's what got me here. Yeah, and I'm on a podcast because I run the customer facing stuff and I was like, anything to talk about, like, what we do, and, you know, I I help our customers get to see, you know, who we are and what we're passionate about and, you know, that we, like, care and really wanna help them get stuff built.
Kyle McLeod
That's that's
Nick Lundgaard
why I'm on. Yeah. And Nicholas here. I went to, oh, sorry. My background is in computer science.
Nick Lundgaard
My grandfather actually was worked at Los Alamos National Lab. He was a lab tech there for 30 years. And I got I got the opportunity to, to do, you know, internship there when I was in college. But, wound up in actually oil and gas here in Houston. And, and then, actually, worked at Alert Logic, before before Macrofab.
Nick Lundgaard
I met Misha at a at a food event, actually, and while I was
Parker Dillmann
Misha is our CEO.
Nick Lundgaard
Yes. Misha is our CEO. That's right. So I met him and he he was and we found out that I was in when I was a software developer, he, basically started interviewing me at this restaurant that we were, that we were randomly placed together at. And ended up at Alert Logic for about 10 years.
Nick Lundgaard
My background is very much, microservices, functional programming languages, and just back end systems. I'm I'm very much like a a systems person. I I do love front end user interfaces. I love to see them come together. I love to see them how they're presented, how they're presenting our back end work to users and giving value.
Nick Lundgaard
But that is my background and my bread and butter for sure. And so I, you know, progressed to the role of technical leadership and then met met Dan Holm at Euler Logic and he he was looking for people here at Macrofab and kind of sold me on the experience. I I don't have an electrical engineering background. Don't know too much about PCBs, but it was super exciting to get the experience from from Chris Church showing us the the the showing us, like, how the the manufacturing floor works. This the process end to end and the UI demo for how the platform works.
Nick Lundgaard
Yeah. I wanna I wanna go build some stuff. I wanna help people build stuff. So yeah.
Stephen Kraig
And how long have both of you been a part of Macofab?
Kyle McLeod
I'm coming up on 2 years.
Nick Lundgaard
Yeah. Same here. It'll be 2 years in July. Nice.
Parker Dillmann
Do you need my answer, Steven?
Stephen Kraig
What what are you what are you sitting at now? You you're you've gotta be over a decade now. Right, Burger?
Parker Dillmann
Yeah. Actually In it's actually a year and a half. Not gonna be at 1 third of my life.
Stephen Kraig
Yikes. Hey. Hey. Technically, next year is a decade for me. Oh, yeah.
Stephen Kraig
Yeah. 2015 is is when I jumped on. So
Parker Dillmann
Yeah. This this October will be 11 years of the company because we had our 10th anniversary last fall. Yeah. And then basically another year and a half is be like I'll be, like, 38, and I'll be at the company for 13 years. So man you're crossing that third third of your life can you have a middle age crisis not I guess that is middle age When do how do when do they consider middle age for people nowadays?
Stephen Kraig
Isn't it forties? For like 45, something like that?
Parker Dillmann
Can you be middle aged with a company? I guess I'm already way past that part.
Nick Lundgaard
Yeah.
Stephen Kraig
I don't know. Yeah. You've been doing all the car crap for so long. You were you were middle aged in your, like, mid twenties.
Parker Dillmann
I don't have a Corvette yet.
Stephen Kraig
No. That's true. You just have a box truck that you're retrofitting.
Parker Dillmann
Yeah. So I I got Kyle and Nick on. Nick really wanted to go on this podcast. But, basically, talk about our software releases we did last year and then what's coming up next. So last year, I think, is probably a very impressive list of just releases that kind of went under the radar from a customer experience side.
Parker Dillmann
And so that's why I wanted y'all on to talk about those and showcase kinda like all the work we did. Because from a customer standpoint, the biggest one was, like, in 2018 where we released the new interface. And mostly from last year there's a lot of under the hood changes for the customers and so yeah. Let let's just rip through that list. Sounds great yeah Kyle can't see the list
Stephen Kraig
yeah. What? He is
Parker Dillmann
he is correct. I I had to listen.
Kyle McLeod
You have to listen.
Nick Lundgaard
I'm only when
Parker Dillmann
I can see the list.
Stephen Kraig
No. He's probably sitting there thinking, oh my gosh. I have to remember of this, recall it all.
Kyle McLeod
Yeah. I was like Yeah.
Parker Dillmann
No. No. So one of releases we had a I'll actually, I'll just go through the whole list, and then we can start talking about them. Okay. We have improved design file uploads, completed board photo updates.
Parker Dillmann
I actually worked on that. A better park placement experience, customer furnished material options, intelligent overage logic. I guess that means it was done before. And then we have we have ITAR, which was the big one, and then PCB file view.
Kyle McLeod
So Yeah. Yeah. I'll start with the ITAR compliance. That's one of our biggest ones. Yeah.
Kyle McLeod
Nick Nick and
Parker Dillmann
I are actually wearing our ITAR shirts.
Kyle McLeod
I know. Yeah. You're wearing ITAR shirts. It feels weird looking at the videos you guys. Yeah.
Kyle McLeod
Itar compliance is a big effort by really everyone at Macrofab because that, you know, the customer what the customer sees is they see, you know, a really easy ITAR interface. Like, you just click a box and, you know, it says ITAR, you know, ITAR PCB, ITAR order, and what goes on behind the scenes is a really impressive suite of, like, software tools that take that flag that you've checked and secure every touch point of your order from who gets to see your PCB files, like, how, you know, what papers have ITAR markings on them. We had a consultant come in, and we told him what we were doing, and he said, Oh, this is, like, way over the top. In a sense, we didn't think it was over the top. We thought, you know, ITAR, we've gotta lock this down.
Kyle McLeod
You know, we have this software that already handles manufacturing. Let's just add it, you know, from the get go and then, you know, flow that indicator through our whole system to to lock lock all the, you know, manufacturing touch points down as far as data protection goes. And so, it's it's you know, it's one of those things that probably as a customer, you like assume that every manufacturer does that but you know, a lot of manufacturers have more paper oriented processes or, you know, sending more things through email where there's, you know, either a, like, a higher risk that they're gonna send it to the wrong person or send it to, you know, a a group they're not supposed to, But also, they're gonna send it through a service that isn't ITAR locked down. Like, they don't they don't know about, you know, gov cloud. Like, they're not they're storing stuff on, you know, gov cloud secured ITAR servers and so, that was a really big effort that we undertook that we're really proud of because it's a really, probably awesome ITAR offering that, you know, I think customers, like, you know, won't necessarily see the, like, thoroughness of our ITAR compliance, but it is, something that we're we're proud of and like to talk about.
Kyle McLeod
And then, yeah, the the the PCB file uploads, that's kinda one of those things that's like part of Itar. Is that we needed like a We have these Previously we just tried to You you upload a PCB file, we wanna process it and render a design from it, but there's a lot of stuff that's, you know, just not not part of the Gerber files or bomb data, you know, the PDFs, you know, for construction, stuff like that, that we want stored securely on the platform and attached to our PCB. And we had places for that, but we've exposed it to our customers this year, and wanna expand that as an offering of, you know, we understand that there are designs that, you know, aren't just simple PCBA and we wanna be able to to support that and handle it as best as possible and, you know, part of that is just getting getting those files on our platform where they have traceability and, you know, good history and are attached to PCBs. Nicholas, do you wanna talk about the, you know, upload enhancements we did?
Nick Lundgaard
Yeah. Sure. I just, another I mean, another brief point to call home, like, how much effort engineering put into well, software development put into the ITAR effort. In October of last year, we migrated our entire platform from AWS into gov cloud. Every single piece of it.
Nick Lundgaard
And that was, that was done with, a very, you know, very brief amount of downtime. But it was done quite seamlessly. I was just it was a joy to be a part of that. It was impressive to see my colleagues working diligently on that. There was so much preparation that went into making sure that every detail of that migration would go as planned with practicing and all of that.
Nick Lundgaard
And the team just
Stephen Kraig
Did you guys do that at 7 o'clock in the morning on a Sunday or something like that?
Nick Lundgaard
We we did start we did start on a Saturday night. And it it just went went through the night and and was completed by the next afternoon. That's right. It's in Saturday afternoon.
Parker Dillmann
Do do we have any stats on did anyone actually hit the outage? No. We publicly announced that we had an outage. And then, like Yeah.
Nick Lundgaard
Yeah. We did. I I we definitely had a redirect to a page. I don't know that we have stats on on how many how many visits we had visiting the the I
Parker Dillmann
wanna upload my new PCB now.
Stephen Kraig
I was about to say that there's, like, someone who's I need 10,000,000 PCBs right now at Saturday at midnight. They're like, oh, damn it.
Nick Lundgaard
Yeah. Yeah. I think
Kyle McLeod
it was, like, so short that we didn't even bother, like, looking to see
Stephen Kraig
Sure. Sure. Yeah. Yeah.
Parker Dillmann
Yeah. Because it was
Kyle McLeod
planned for
Stephen Kraig
Which is ideal. That's exactly how you want.
Kyle McLeod
Yeah. It's just I have, you know, all the emails, like, drafted of we're sorry, like, it's taking longer, but luckily I didn't have to send any of those.
Stephen Kraig
One one very distinct memory I have working back at at MacroFab was being in the Hutchins location and and we there there was there was a I'm doing air quotes conference room in in there. It it was this it was this one room that was just like table and chairs in it. And I remember being part of the move of going from Hutchins over to Governor Street, and and having Chris Church look at everyone and go, and he said very clearly, we're doing this with military precision in terms of how we're moving all of this stuff over, and it's still etched in my memory. I can recall that. And so I can only imagine Chris doing the exact same thing with we're going to, you know, switch all of the servers over to to GovCloud with military precision.
Nick Lundgaard
Yeah. Yeah. Absolutely. I mean, the entire team, pitched in on on preparing us for that, doing extensive testing. I I've known of I definitely have to call out, Isaac and Tim on our infrastructure team.
Nick Lundgaard
They just, the amount of work that they did to, to make sure that that process went smoothly was astonishing.
Stephen Kraig
And and I I gotta I gotta think, you know, a a standard Centimeters doesn't necessarily have the same platform that you guys do that handles all the file and and all the data transfer with everything. So so, you know, having an ITAR in my my experience with with working with with ITAR regulated circuit boards has been frankly not terribly difficult. We encrypt the files, we send passwords, we we we get a way to get the files over to the Centimeters and then we're, like, okay. There you go. It's in your hands kind of thing.
Stephen Kraig
But with you guys having the platform, it seems infinitely more difficult to, you know, cross all the t's and dot all the i's in terms of who's checking everything and and making sure that everything is done properly. So it I I'm all I'm saying is it's very impressive.
Nick Lundgaard
Yeah. Thanks. Yeah. And I guess moving back to to file uploads. Yeah.
Nick Lundgaard
I think one of the themes last year, in addition to just, you know, improving improving, adding a new ability to upload non designed files has has been just improving the reliability of our Gerber processing. We've done some significant speed enhancements to Gerber processing, you know, by adding parallelism and these kinds of things. And also done a number of bug fixes with respect to, with respect to complex border detection. And, you know, the net, the net results on the other end is just a wider array of design files can be uploaded to our platform with without need of of any support from from our MacFabb experts.
Kyle McLeod
Yeah. I think you had Colin on the podcast
Parker Dillmann
earlier. Right? Yeah. We had Colin on before he was a MF er.
Kyle McLeod
Oh. That's hilarious. Yeah. Yeah. So he's on our team now and we turned him loose on a lot of the like file upload because he is a electrical is he electrical engineer by the time?
Kyle McLeod
Okay, yeah. Electrical engineer and just like Also a physics. In physics. I Yeah. Yeah.
Kyle McLeod
I can't box him in. I think he's too old to
Stephen Kraig
list all
Kyle McLeod
of us.
Nick Lundgaard
I would box him in as a polymath. Yes.
Parker Dillmann
Yes. That was episode 328. Where Colin talked about we called it berry based physics.
Stephen Kraig
Mhmm. And what really happens down on the quantum scale with
Kyle McLeod
Basically I've learned as a product manager just to give him, you know, free reign over our file imports. Say, what bugs you, Collin? And go you go Just go do it. Just go. And then he'll be like, I've improved this part about, you know, 5 x speed.
Kyle McLeod
And I'm like, that's
Parker Dillmann
That sounds too low.
Stephen Kraig
Yeah. You're not giving him enough credit.
Kyle McLeod
No. It's just Well, I'm sandbagging. I had okay. I promised I promised myself I wouldn't come in here and over promise our anyone product features and improvements. So I'm gonna stick with 5 x and hope it's sounds good.
Nick Lundgaard
But yeah. Yeah. Working with Con is is a is a is a humbling experience to say the least. He's he's just, just brilliant to see what he brings to the table, on the on the platforms. And we have some pretty exciting stuff coming up, I mean, even in the next few weeks.
Nick Lundgaard
So nothing that you'll nothing that you'll see, you know, just right away. Just some platform enhancements, that are gonna make the the performance of the, the design view in particular, but really just platform wide some performance enhancements to the web page.
Parker Dillmann
So I wanna talk about this intelligent overage logic because that implies that our logic before was stupid.
Kyle McLeod
No. I mean, so, you know, part of you know, our job is to, you know, give factories the Enough parts, you know, these parts are tiny. Like, they lose, you know, they need a little extra if it's a real, product to to load it in the feeders, you know, and they always ask us for for more more parts in case they, you know, lose something or, you know have issues on the floor and so, you know, our customers like we don't want to charge them for more parts because you know, I don't want to pay for
Parker Dillmann
more than than you you want. I ordered 10, I want you to buy 10. Yes. Exactly.
Kyle McLeod
Put 10 on the boards. Yes. And so we're, you know, we want to have as much of a balance as we can there and part of that is, you know, for a while we were saying, you know, small packages, we're gonna use, you know, standard overage of 50, or, you know, for those really tiny cheap resistors. Most of our customers don't care about that. We found, you know, some places in the middle where it's, you know, starting to get into your more expensive, real parts.
Kyle McLeod
We just started pulling in more variables, you know, into that calculation. We say, you know, okay, like, as a customer, you know, you wanna not pay for a ton 50 overage if it's a, you know, a dollar part, because that can start to add up. And so we, you know, started just putting in more variables into that calculation. You know, trying to think of what does our factory really want? You know, and what can we be like, hard on and be like, you know, hey, like, you're Like, I know you wanna run this through Pick n Place but it's a, you know, $5 part, like, you're gonna hand You're gonna hand place it.
Kyle McLeod
We're not gonna charge for a 100 of So we've basically taken our overage calculations and just kind of added some more intelligence. We say intelligence, it's it's more around, like, the margins of It's more if if else loops now?
Nick Lundgaard
Yeah. Absolutely. I mean, we we we are comparing, you know, the the cost of of hand placement with the cost of the overage that the pig in place would want. And, you know, if if we determine that you come out ahead with with hand placement, we will go with the hand placement amount of overage, which is typically quite a bit smaller, right, by percentage. The, the overage also just scales neatly with the cost of the parts.
Nick Lundgaard
And, which is how it's always been. But this yeah. The as as Kyle mentioned, the the package overage is is the main feature, the main headline function that we added, last year. And then we've we've been iterating on that over the over the last year to to add even more intelligence. And then the other the other piece of this puzzle is really the quality of the data that we're able to get, you know, whether whether we have those those package identifications for parts that we haven't seen before in the platform.
Nick Lundgaard
And so we are working this year on improving our our part data sources. So we will be just enhancing the number of packages that we've identified so that we get more accurate overage calculated for your BOM, which is gonna result in, you know, faster order processing and and just better deal for the customer.
Stephen Kraig
So so does does the platform indicate to the user, you know, here's here's your price for parts, but here's your overage. Does it tell you, oh, you're also purchasing an additional 5, or does that just kind of get I shouldn't say swept under the rug, or does it just kind of get combined in with all your other parts?
Kyle McLeod
Yep. We do it as If you look at your BOM, view or even the components breakdown on the quote and order tab of your PCBE, you'll see the overage. So we're very transparent about overage. We'll tell you if you're getting 50 overage, like, it's there on your bomb and on, the quote and order, page for you to see, so we're transparent about it. I I I think it's I mean, I don't think we break it out as a separate, like, line item summary for your order, but it's pretty easy to get at.
Kyle McLeod
If, I can tell you from receiving customer feedback, our customers know how much over just costing them.
Stephen Kraig
Yes.
Kyle McLeod
Because I've gotten those emails and I appreciate them because it's You know, oh yeah that Oops. Like that's that's a corner case that you know we can dig into a little bit more and enhance our calculation based upon.
Stephen Kraig
Well and and that's just the thing. If you're going to manufacture something, we all know that it's going to that overage is just a part of the equation. Mhmm. And one of the more difficult things, honestly, that I've experienced with with CMs is trying to guess what their overage is. And and I've certainly got it wrong before where, you know, they wanted a 100 extra parts and I bought them 80 or something like that.
Kyle McLeod
Yeah.
Stephen Kraig
And and then there's a whole conversation around that. So it's nice to have automated where you guys make the decision. I just give you the bomb and you tell me, we're we need to buy this this few extra. Now now, working in aerospace is kind of interesting because sometimes, you know, if it's if it's a if it's a 10¢ 0402 resistor, yeah, sure. Buy 300 extra.
Stephen Kraig
I don't care. Right? But, you know, the just the other day, I got some quotes for some transistors. They were $1700 apiece, and they have a lead time of 32 weeks. So if one of them falls on the floor, I want you guys to tell me that it fell on the floor.
Stephen Kraig
You you your overage is 0. I need you to place every single one of these because I have to go to my boss and say, hey, we consume too many. So so yeah. I I don't know. It scales with the part.
Stephen Kraig
Right? It it it it
Kyle McLeod
it all depends.
Stephen Kraig
But but yeah. You have
Parker Dillmann
told me that I'm gonna be, like, digging through the vacuum cleaner.
Stephen Kraig
Yeah. Yeah. Yeah. Yeah.
Parker Dillmann
Or the bag.
Stephen Kraig
I want you to sweep the floor, put it in a bag, and send me everything you found.
Parker Dillmann
Vacuum cleaners are allowed on the floor. No.
Stephen Kraig
They shouldn't be. Yeah. Yeah. Excuse me. So please don't do that.
Stephen Kraig
That was entirely a joke. Do not do that. So how about this customer furnished material option? I'm curious what that is in relation to.
Kyle McLeod
Yeah. We used to, you know, as you're building out your bomb, make you designate, am I going to supply this from inventory? Am I going to consign it? And we found that, you know, our customers don't want to necessarily make that decision at that point. You don't want to be uploading a bomb and think, Do I have enough inventory to supply this part?
Kyle McLeod
You just want to build a bomb and then say, you know what, I'm gonna supply, you know, these, this list of parts and then after you order, that's really what, we don't need that information to place your order. We just need you to tell us which parts that you're going to buy, which parts that we're going to buy and then, you know, after you place your order, you can go in and say, well, I've got these in inventory. Take those from my inventory. I wanna consign these parts, you know. I'll send them to you.
Kyle McLeod
So we basically have moved around some of the decision making flows to where, like, we thought and got feedback that our customers, you know, wanted to make those decisions. So, you know, it's a lot of it was, you know, on the, on the manufacturing side is, you know, similar like, we still, you know, let you pick inventory or consignment, let you, you know, have some flexible sourcing. We just moved a lot of the decision making pieces to where where where it made the most sense.
Parker Dillmann
Yeah. Basically broke out sourcing is now separate from a bill material.
Kyle McLeod
Yeah. Exactly.
Nick Lundgaard
Yeah. Separate from the bill of material. And even I mean, of course, the turnkey, you know, macro fab buying your parts or you supplying them, decision you do need to make right up front. But, you know, whether you supply from inventory or consignment, you can you can wait days after your order to make that decision if if you have a need to for any reason. The the decision is is fully after order placement happens.
Nick Lundgaard
And and we're already processing your order, reviewing it, sourcing the parts that you want us to source. So maximum flexibility.
Stephen Kraig
So So so I guess that gives 3 different places where your components can come from. Right? You can either have Macrofab go out and buy them. They can either come from an existing inventory that's there, or I could supply them to you, me being whatever the customer is. So so that brings up a question.
Stephen Kraig
Let's say, I did a run with Macrofab. I'd I'd manufactured x amount of boards and parts returned to inventory. If I go and produce those boards again, I can pull from that inventory if there's excess parts. Correct?
Kyle McLeod
Yeah. If there's enough, like, inventory, like, we don't typically store, like, overage in inventory. Yeah. That kind of stuff, because that's typically, like, just too hard to find, but if you have, like one of the benefits of storing inventory with us is you can do exactly what you said, if you go to build with us and we don't use all the overage, or you know, like, you have a giant reel, we don't have to, like, you know, lop off 50 parts every time we run that job to to, you know, run the feeders to the machine. So, yeah.
Kyle McLeod
The customers do the benefit of being able to put that back in inventory when they're done.
Stephen Kraig
Yeah. I like that. I like that from a long lead time perspective. If you have parts that take forever to get, put those in inventory and then get your jelly bean resistors and caps closer to the actual build date.
Kyle McLeod
Yeah. Exactly.
Parker Dillmann
So what about this complete I I actually know a lot about this because I worked on it yeah completed board photo updates yeah we talked about that Yeah. I didn't do any of the back end or the customer facing, but I did all the back end work, I guess. So this is for QA, our quality assurance team.
Kyle McLeod
Mhmm.
Parker Dillmann
And it allows our quality assurance team to basically take photos full resolution photos of the boards and then securely uploads first article that the QA team has approved. And so then you as a customer can view basically the first article that the QA team has approved. And so the the whole initiative idea was to allow customers to see their boards faster so we can if there was an issue, let's say, there was an issue assembling the boards, you can catch it faster before we ship them out to you.
Stephen Kraig
Does does the customer have the option to also approve before shipping based off that
Parker Dillmann
image? Good idea. The problem with that is it would halt the
Stephen Kraig
Oh, yeah. That would gum up the mix like crazy. I'm just wondering if if you guys had already tackled that.
Parker Dillmann
No. That that's something we've tossed around. It's just the it halting the line and Yeah.
Kyle McLeod
If you reply to that email, we will jump on that order and stop it
Parker Dillmann
ASAP. We could jump it gets jumped on really fast. The the main thing is it prevents the back and forth of shipping everything.
Kyle McLeod
Yeah. It's just a nice I mean, you think of I don't know. Amazon getting, like, the picture of your package on your door when it comes in just, you know, most of the time I I don't know if we've actually had any customers, like, jump in and say, Hey, you did something wrong. But, we've had a lot just really like that they can see their board's progress and just, you know, see that we're doing a good job. And just, you know, see the product because it's it's not, again, not something that like a traditional Centimeters is necessarily gonna provide.
Kyle McLeod
You know, unless they're like, unsure about how how your board's being built. But we just do that on, you know, any board that comes through because like, we I mean, honestly, because we we have the the AOI machine taking photos. We have smart people who can get those photos into a database, and then we have smart people who can build workflows to put those in front of our customer. And so we're like, well our customers would like this. Let's like go build it and make it something that's a nice extra feature for them.
Kyle McLeod
So the
Parker Dillmann
I won't name the names, but we've already have other CMs copy that feature. Is that right?
Stephen Kraig
That that
Parker Dillmann
it happened very fast. You you see
Stephen Kraig
you see what what first came to mind was the the Domino's pizza tracker
Parker Dillmann
where,
Stephen Kraig
you know, like, what what when when you're at the end, it's, hey. Your pizza's ready for for pickup. Well, why don't they send They they don't send you a picture of your pizza because I'd I'd open it up and be like, yep. That's a pizza. Cool.
Stephen Kraig
Thanks.
Parker Dillmann
No. I'd love to see that picture.
Stephen Kraig
But why is
Parker Dillmann
that why is it missing a pepperoni right there?
Stephen Kraig
Yep. Yep. Send it back.
Nick Lundgaard
Why doesn't that look like the ad copy?
Stephen Kraig
Yeah. Yeah. True. Yeah. There you go.
Stephen Kraig
That's why they don't send you the picture.
Nick Lundgaard
Yeah. I mean, you know, there's there's a one point for PCBs. They they do look like the ad copy.
Parker Dillmann
Yeah. The that was such a the the initial version of that uploader was a really it's a it's a really old MerTech. It's called Speed Demon MerTech. It's before they were numbered MERTEC AOIs, and there there's a Python script. Oh, oh, and that that AOI runs Windows XP.
Stephen Kraig
Wait. Was was this the MerTech that was there when I was there?
Parker Dillmann
Yes.
Stephen Kraig
Oh, okay. Yeah. I remember this.
Parker Dillmann
Yeah. And so and that that thing's just been collecting dust forever since we got our new MerTech sixes, and they didn't want me to start messing with the new ones because they were using them for all the runs. And so I'm like, oh, I can just use this old AOI to experiment on. And the I think the most interesting thing was getting Python to run on Windows XP. Yep.
Parker Dillmann
It's Python 2.6. Yeah. You can't
Nick Lundgaard
run That is ancient.
Parker Dillmann
You can't run
Stephen Kraig
And and wait but but but Python 2.6 is what are we at now? 3.4?
Nick Lundgaard
3.13 or something like that?
Stephen Kraig
Something like that. Okay. Yeah. See, I don't even know. But but 2.6 is so completely different than that.
Stephen Kraig
Like, are you are you still porting that over to the Numeretec machines?
Parker Dillmann
No. It was all rewritten for the newer machines, but the it it basically drove the mouse around to click click on the MerTech interface and then scan boards and stuff. Nice. And then to, like, safely transfer, it had its own local network go where it needed to go. But, yeah, it it's definitely was like I'm so glad we had we could turn that off because it was definitely,
Stephen Kraig
a club
Parker Dillmann
but I think when because we had Brendan on who's the engineering director on the podcast and I I had to show him how that thing worked when he when he started. Yeah. The newer machines have a lot higher resolution and everything like that. So Mhmm. Yeah.
Parker Dillmann
That that was my extent. It was like I did the groundwork on the floor, and then Kyle was just like, yeah. Just point it to this location, and maybe it'll work. Oh, and then we had to make an like, a tool so we can transfer the photos.
Kyle McLeod
Yes. We have a very Well, it's it's it's very good. Steady. No. It's not our most steady product.
Kyle McLeod
So if it goes down, product at macofab.com if you're not getting your board photos. But,
Parker Dillmann
well, because the other tool I also wrote, but that's in JavaScript.
Kyle McLeod
Yeah. We we we wrote a lot of There's a theme here.
Parker Dillmann
Me writing code
Kyle McLeod
and not
Parker Dillmann
being good.
Stephen Kraig
Alright. So how about this PCB file view? What is what is new with
Kyle McLeod
that? Yeah. I covered that a little bit. It is where you can see so we say PCB files we just mean like the
Stephen Kraig
the oh this this was the additional files right
Kyle McLeod
this is the additional files yeah okay Yeah.
Parker Dillmann
Yeah. And exposing it to the I guess it was always technically exposed to the customer, but you had to know if in the URL you could put so if you're looking at your PCB, you could just put in slash files, and it would navigate you there. There's actually a link now, and we expose more files and also allowed more files to be uploaded.
Kyle McLeod
Yeah. And you have a nice detailed view where you can see who uploaded this file, you know, when did I upload this, which you'd be surprised because we we have, you know, our support team comes in and helps sometimes. So we wanna sure that we're, like, tracking all that stuff.
Nick Lundgaard
Yeah. That was absolutely the genesis of of the the view, initially. Right? And why we didn't initially show it to customers because we thought it was mainly useful for for our internal support teams. But, you know, realizing that that it that it does provide customer value and that we could add on this this facility to upload some extra files.
Kyle McLeod
Yeah. Is that Yeah. With with with Itar actually, we're like, trying to figure out how we could transfer files, like you said, Steven. You know, sending encrypted keys and all that, and we were like, we already have a gov cloud s 3 bucket here. What if we just made that a place where people could put their files?
Kyle McLeod
And that was actually, like, easier than us, you know, going in at buy, you know, buying a subscription to secure file transfer service or something like that. So Right.
Nick Lundgaard
Yeah. And fully integrated with our with our platforms Yeah. That you have one place to go to get it all.
Kyle McLeod
Exactly.
Parker Dillmann
So what's next? What's we're already it's already April. We're we're full quarter 3 months into 2024. What's down the horizon?
Kyle McLeod
Yeah. I mean, we we've been doing a lot of work on the the PCB screen, you know, besides, like, the the, you know, ease of uploading files, like, we just wanna make that UI, like, really nice and clean, both for, you know, existing customers who are used to using microfab, but also for new customers who aren't really used to, like, working with a, you know, Centimeters or platform that just takes their data and imports it and, you know, a lot of them used to emailing back and forth and and getting a little more, or actually having to do a lot more, like, communication and and so we're trying to make that process feel a little more like natural for for both for both new users and for existing users. So we've had some UI improvements so far and we've got a lot more planned, a lot of stuff focused on your your bill of materials. We know we know that, You know, for someone who had a really clean, you know, bomb with all their parts selected, like, it's a pretty nice experience. You know, if if if you're managing that bomb and and keeping it up to date with, you know, parts that are, you know, still being manufactured, for instance, like, you get a great bomb experience.
Kyle McLeod
But we've gotten like a lot of, you know, feedback that people who are like still building out their bomb, we don't really help them like we could for people who, you know, have aren't really wanting to, you know, make sure that all their components are still being manufactured or are highly available. We don't serve them as well as we'd like, so we're, you know, doing a lot of work on, you know, updating our part information and like, pulling in just like, as much part information as we can get so that we can say, you know, maybe recommend, you know, all of your jelly beans for you. If you can give us, you know, the values you're looking for. You know, provide some tools to help you build out that bomb. Because that's like, our, you know, our expertise is like, we have all these parts.
Kyle McLeod
We know it's available. We know it's out there in the market. And we want to help people, like, who are, you know, like, selecting passives. Like, sometimes it's, like, that's not where we want designers to spill their time, I don't think. We haven't got the exact
Parker Dillmann
How many times have you gone to a Mouser Digi Key and went, I need a 0 80510 k resistor. I don't care what it is. And you always sort by the cheapest price and if it's a real of it or not. Yeah.
Kyle McLeod
And so, like, we we wanna make that easy for because we we get a lot of people who just upload, I mean, everyone knows, like, what, you know, what capacitance value or what resistance value goes at that at that designator but they just don't have a part selected. And so we're working on You know, we wanna be able to provide that for our designers in a way that, like, helps them spend time on activities that are important and not have to, like, you know, manually select part numbers for those those materials. And then we wanna help people just like, with with that information, you know, be able to like, get get feedback on their bombs. That's more like proactive, So that you don't have to think about, you know, oh, am I picking the right parts from a, you know, manufacturability perspective. You just have to think about, is this part have the right specs for my board and we'll handle, you know, is it, you know, gonna be end of life in a few years.
Kyle McLeod
We'll provide recommendations for how to, replace that part. Or if it's, you know, has an availability risk, we'll provide that insight. And so, those are a few of the things, that we're working on right now. And then and then really just like our our pricing and and lead times, like, you know, we we have I I think we provide a pretty good range of things that you can build on our platform. We have, you know, a pretty good selection of stack ups that you can automatically price, you know, compared to what's out there, but we wanna get get even better at, you know, automatically quoting more a little bit more exotic PCBs.
Kyle McLeod
Whether it's, you know, proper weights or, you know, layers or stack up thicknesses. We wanna be able to give you, you know, better options for selecting pricing and and lead times. I guess, quantities and lead times. Hope you still have to pick your prices. That would be interesting.
Kyle McLeod
Yeah, quantities and lead times and quoting data and we've kind of relied on on vendors in the past and we're gonna keep, you know, using like panel vendors that we feel are good quality panel vendors, but start to, you know, use some some data and are, you know, whatever you would call it, AI, or you would just like data interpolation just to build out a more intelligent pricing matrix that gives you, you know, more automated quotes.
Parker Dillmann
And Excel best fit line?
Kyle McLeod
Excel best fit line. Yes. It's it's I I have done a decent amount of the data stuff like that and yeah. It'll be more than an Excel best fit line. It'll be But I don't want to oversell her.
Kyle McLeod
Go into, like Yeah.
Stephen Kraig
I I I love the idea that there's intelligence behind it that goes beyond saying, hey, we've detected an issue. Like you were mentioning end of life kind of thing. That's Yeah. That's great when it says, okay, here's your part. We we say we sense that it's end of life.
Stephen Kraig
I love the idea that there may also be, hey, it's end of life. Here's a suggested or here's 3 other suggested. Maybe you can pick one of these. Just make your life way easier as, you know what what was the word that that was always used? Stiction.
Stephen Kraig
Right? Like, just make it make it so that it's easy for people to use your platform and by removing the friction and adding stiction.
Kyle McLeod
Right?
Parker Dillmann
That's that's another cofounder word.
Stephen Kraig
Oh, yeah. Oh, yeah.
Kyle McLeod
That's nice.
Parker Dillmann
I've used that word before.
Stephen Kraig
Yeah. Oh, yes. Also, completely randomly, something I don't know why my brain came up with this. Maybe it's just ADD. It would be fun one day.
Stephen Kraig
You know, Digi Key and Mouser, they have, I don't know, a a 1000000 different line items. It would be fun to know how many of those you have purchased. Not in quantity in terms of, like, how much money you've spent at Digi Key, but have you purchased 250,000 unique parts from Digi Key or Mouser or whatnot. Yeah. It'd be a fun statistic.
Parker Dillmann
I bet you it's over that.
Stephen Kraig
I bet you it's a lot. I bet you it's a done.
Parker Dillmann
Well, last year alone, we built 900,000 PCBs.
Stephen Kraig
Right. Right. So what what size of the catalog have you purchased?
Parker Dillmann
Yeah. I think each one I think on average, it's 30 something line items per board. Yeah. Yeah. So yeah.
Parker Dillmann
It's crazy.
Kyle McLeod
We need
Nick Lundgaard
to get some custom badges for that.
Kyle McLeod
We'll probably know in a little bit.
Parker Dillmann
Gotta go stay up really late doing some MySQL. Steven just stepped out editor.
Nick Lundgaard
Should we talk about the the improvements from from February well, from March?
Stephen Kraig
Oh, yeah. The I don't
Nick Lundgaard
I think I don't know that we we got into the details of of just not requiring placements and and the reorganization of the tabs.
Kyle McLeod
Yeah. Let's go and do that.
Parker Dillmann
Applications improvements. We'll talk about that next. I think his headset died. Oh, dear. You guys there?
Parker Dillmann
Are you back in the land of the hearing?
Stephen Kraig
Yeah. That hasn't happened in
Parker Dillmann
a hot minute. Editor Steven is now back. Oh, and then I we talked about all the releases in 23, but what about the last 3 months?
Kyle McLeod
Yeah. Yeah. I kinda mentioned the updates to the workflow, but, editor, you can cut that out.
Parker Dillmann
We're gonna keep that in.
Kyle McLeod
What's up? It's okay. Yeah. So in the last few months, we've made a lot of changes to the PCB screen. And one of those, you'll you'll notice is, like, our court in order page, you know, now gives you different indicators.
Kyle McLeod
We wanted to split out our our ready check. Yep. What we call ready check is basically, is your PCB, you know, ready to order? If we gave it to our, you know, not quite ready to build but ready for our order review team to check the design. And so, it's usually, are your design files there in any good order, is your bomb complete?
Kyle McLeod
You know, can someone take a look at this and and check if it's actually manufacturable? And and previously, we just gave you, like, a big red aggressive error that was just like, you can't order this board. And we found it to be a pretty bad experience. 1, because it didn't really tell you why and then also because we actually required some stuff that we don't really need to to quote you on. And so, like, placement placement data is one of those things.
Kyle McLeod
Like, we do need placement data to, you know, go ahead and build the board. But you don't actually need to have your placement data all sorted out. Or your Gerbers, you know, all sorted out to, get a valid a valid quote and place that order with a good price. We can let you place that order and then we can go in with our support team and they can clean up your your placement data and any, you know, missing files. We've had a lot of orders go through this process and it's really quick and easy.
Kyle McLeod
Our support team's used to doing this so they're like, you know, I usually I like click on the alerts, you know, like, an hour after they come up and they're already resolved because our placement or review team's already fixed it. So, we started just requiring less less data to be like in that perfect state for you to get a price and place that order. And we've also just split out those warnings, unquote, in order to like, really more of checks. Hey, like, you have design data, you know, do we give you a thumbs up on that or is, are you gonna need to like get support to help you after you place your order? You've got a bomb.
Kyle McLeod
Do you have you know, your parts defined? Are they MPNs that are recognized by our market databases? Or is there some stuff in there that like, we need to to work on, like, our communication of what does this part actually mean? And then, or is it like, or do you have a great bomb that's just got some pieces of availability in there. And and, you know, and within that like, window, oh, you've got availability issues like, here's the 6 parts that are missing availability.
Kyle McLeod
You can designate them as, you know, customer fringe material right there and just You you provide them or you can, you know, go in your BOM and add those alternates yourself or if, honestly, if you like, know that it's a part that we're just not pulling for some reason, from a source that you know of, that you know, isn't Digikey or or Mouser, you can request sourcing help and just tell us, like, hey, like, I'm trying to place an order for a 100 PCBs. I've got these parts. Here's a link to them. Like, you guys just go quote these and we'll quote them and you know I don't know. It's a pretty like, quick quote turn around.
Kyle McLeod
It's not a custom quote, you know, 3 day window. It's We get Slack alerts. We go in there and we say, oh, you've got these parts. Let's go let's go quote these and get your order taken care of. So we're just trying to make it like, and then we have that custom quote window still.
Kyle McLeod
If you have some custom quote specs, we'll tell you what's what's kind of blocking that, you know, automatic order and order now capability. So, we're just focused on, it's a pretty big overhaul for our platform and that, you know, like, not requiring placement data, requires us to do a lot of work. We did a lot of UI work to make that, you know, feel Try to feel as smooth as possible. Even like when you start your board, like, if you don't want to upload design files, you can start from your specs quote. And you can just tell us, like, how wide, you know, how wide longer board is and and we will build your quote from there and then if you wanna provide us files later, you can.
Kyle McLeod
So it it was a big, you know, UI overhaul, but we think it gives us, you know, especially for those new users, like a really nice experience of as you're designing your board, you can use Macrofab. You don't have to have it all figured out to take advantage of our, you know, quoting platform or our part services. Like, you can use the platform to get quotes, you know, as you're working through those designs rather than, like, having to have every Gerber layer figured out and all of your placement data in there and and worked out. Yeah.
Nick Lundgaard
I'm really proud of of the the team's work on that UI overhaul that I, as Kyle mentioned, the centralization of of showing you the errors and not making you fish around for, oh, I have to go somewhere else in the UI to fix this problem. You know, centralizing it into one space where you can kind of see it. And also just differentiating things that are not material to, you know, to you getting an accurate quote and placing an order. Things that we can help you with after the fact. Marking those clearly as warnings that aren't that aren't blocking you and marking the things that do in fact block you from getting an accurate quote as you need to fix this.
Nick Lundgaard
This is this is a red warning. I find it makes the platform a lot more approachable to to users who are not as initiated.
Stephen Kraig
You know, it's really fun to hear all of this because it seems like Macrofab has has certainly gotten to that level where the data can really help drive your decisions and it sounds like there's a lot of really close attention to the fine detail of what does it mean for to at MacFab that that, you know, one day MacFab would get to that point and it's just really fun to see you guys there now, and see you at that point where you get to turn those little knobs and see how how that affects well, the the what what is it? O e, the operation experience? Order experience. Ordering experience. That's what it is.
Stephen Kraig
Oh, that's fun.
Kyle McLeod
Yeah. It's a lot of fun. It's I'm a huge data nerd SQL query guy. So I'm just anytime I can dig into our, you know, I use it as an indicator for how we're doing, so it's fun to see. I mean, sometimes it's frightening to see where we are missing the mark, but it's it's fun to have that data and to, like, really try to attack some of those problems.
Kyle McLeod
Yeah. And and, you know, get to see, like, it's a a fun experience every day on the team.
Nick Lundgaard
You know, we we, we it's a fun experience every day on the team. You know, we we, we have a real fast development cycle. You know, we use agile development. We are, you know, pushing improvements to the platform multiple times a day in in our microservices architecture. And you know, that is, those things are seamless to the user experience and, things just get better and better, you know, every couple of weeks.
Nick Lundgaard
It's, it's, it's fun to see. It's fun to, to plan ahead and keep these guys busy, you know, building whatever Kyle dreams up.
Parker Dillmann
Do y'all have anything else? Or you wanna wrap up the podcast? These 2 wanna go hang out with the rest of the team. I'm I'm actually keeping them from, like, their their, like, monthly hang out with the rest of the developers team, drinkathon, I guess.
Nick Lundgaard
Yeah. Dreaming of drinking beers while we're sitting here drinking beers with you.
Stephen Kraig
Yes. Oh, man.
Parker Dillmann
Yeah. But it's with me, not with the rest of your team. So Well, thank you
Stephen Kraig
so much for spending your evening with us. We really appreciate it. Yeah. It's been a ton
Kyle McLeod
of fun. I mean, keep uploading your designs.
Nick Lundgaard
Yeah. Thank you.
Kyle McLeod
Use the use the little red chat. It's way underrated. Can we check the icon? Product? Atmacafab.com.
Kyle McLeod
What would you like the icon to be, Parker? Mac. Oh wait oh Mac the PCB guy yeah oh man we have a unofficial mascot unofficial mascot that's clippy right the the old Yeah. Microsoft Word.
Stephen Kraig
Mac has been on a t shirt and some stickers. Right?
Parker Dillmann
About that. Yeah.
Nick Lundgaard
He's kind of the love child of, of Clippy and Mickey Mouse.
Kyle McLeod
Yeah. Yeah. We could make that.
Nick Lundgaard
That that might need to be an Easter egg just for you.
Stephen Kraig
Yeah. Oh.
Kyle McLeod
I accept. I'm logged in. I like that.
Nick Lundgaard
Yeah. Yeah.
Kyle McLeod
Unlock Mac the the the the Macafab Macafaba.
Parker Dillmann
Mac the PCB guy.
Nick Lundgaard
Maybe a secret preference user management page.
Parker Dillmann
Yeah. Well, thank you, Nick, and thank you, Kyle, for coming on our podcast to talk about the software releases. Probably have y'all back on next year
Kyle McLeod
yeah we'll look forward
Parker Dillmann
to that. See if y'all see if y'all have hit all those marks
Kyle McLeod
yeah I know
Nick Lundgaard
you're gonna yeah you're gonna come here with a checklist yeah
Kyle McLeod
we haven't hit those by next year. I'll be probably not available for the podcast.
Parker Dillmann
Thank you for listening to circuit break and mock yeah. Thank you for listening to circuit break, a Mac or Fab podcast. We are your hosts,
Stephen Kraig
Parker Dillmann And Steven Kraig. Later, everyone. Take it easy.
Parker Dillmann
Thank you. Yes. You are listener for downloading our podcast. Tell your friends and coworkers about circuit break, the Macrofab podcast. If you have a cool idea, project, or topic, or a feature you want us to implement, let Steven and I and the community and Kyle know through our forms.
Parker Dillmann
It's forum.macfab.com, where we talk about personal projects, discussions about the podcast, engineering topics, and news about MacroFab.
Related Podcasts
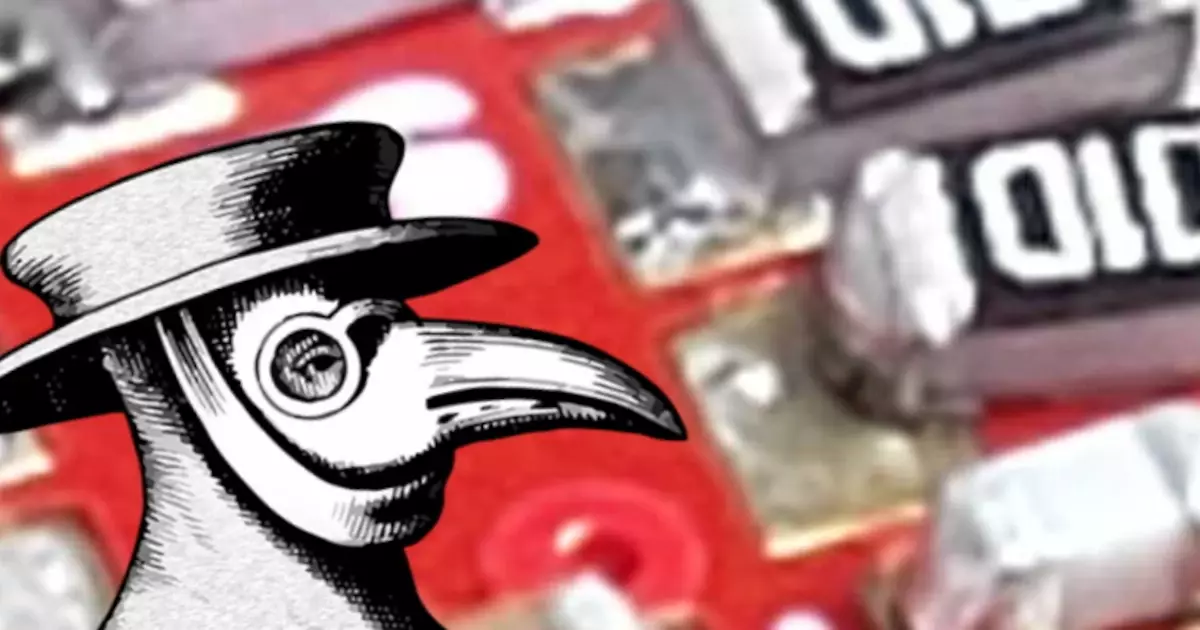
The PCB Plague
Ever have PCBs that solder just will not wet and solder to? You probably thought it was improper soldering technique but that was probably not it!
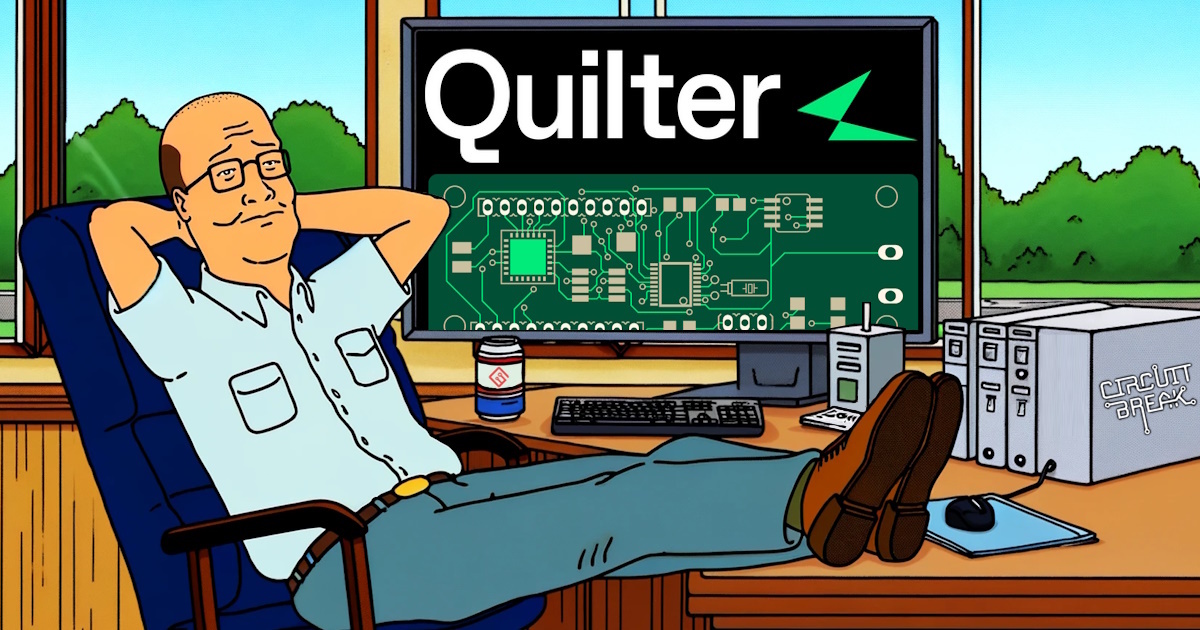
Tracing a Path for PCB Design Automation with Sergiy Nesterenko
Sergiy Nestorenko, founder of Quilter and former SpaceX engineer, discusses revolutionizing PCB design automation.
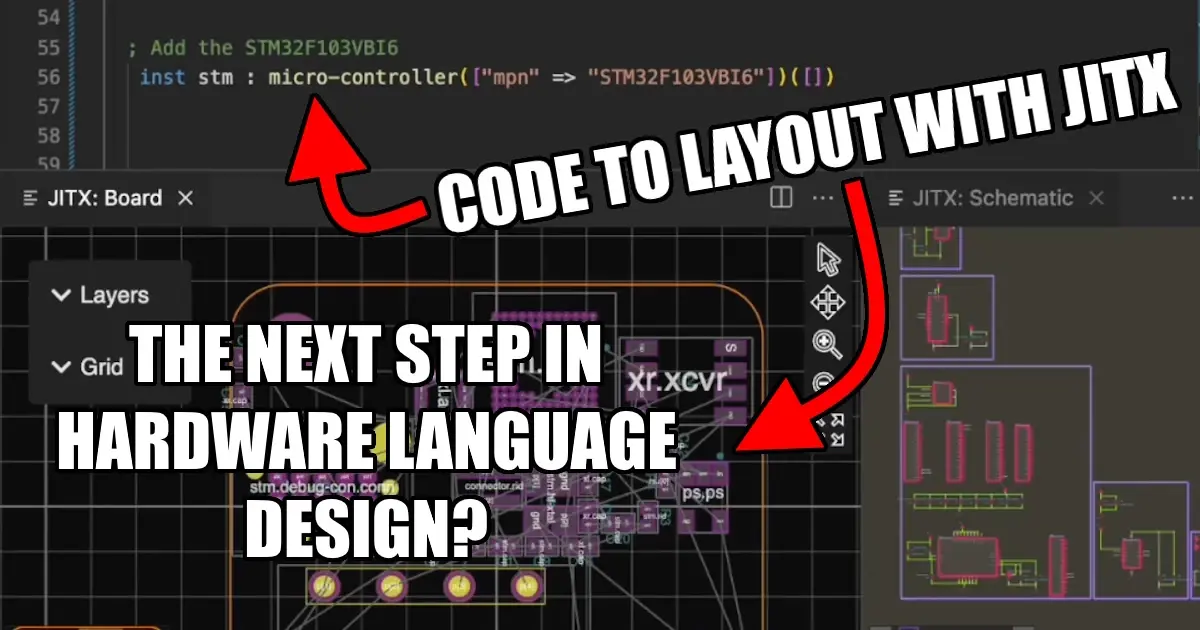
Dr. Duncan Haldane from JITX on Automating Circuit Design
Dr. Haldane on his background, the problems JITX is trying to resolve, & new auto-router plans. What's the deal with the "hyper-aggressive pogo-stick"?
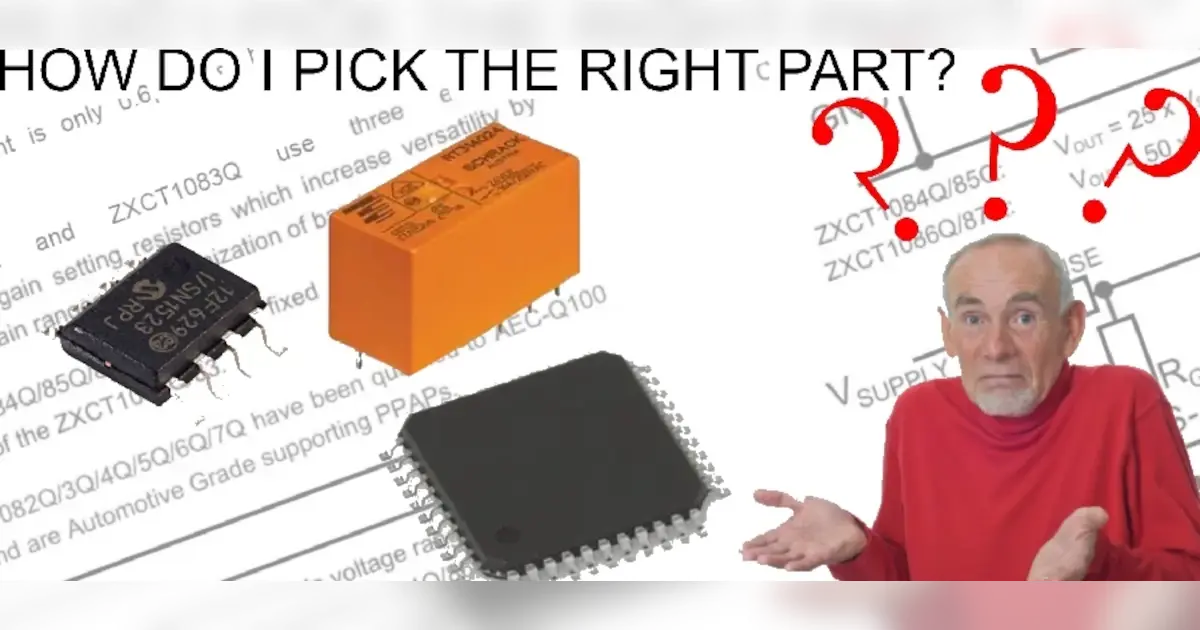
Datasheet Lore
What lore have you discovered in component datasheets? On this episode, Parker talks about how he picks electrical components and risk management.
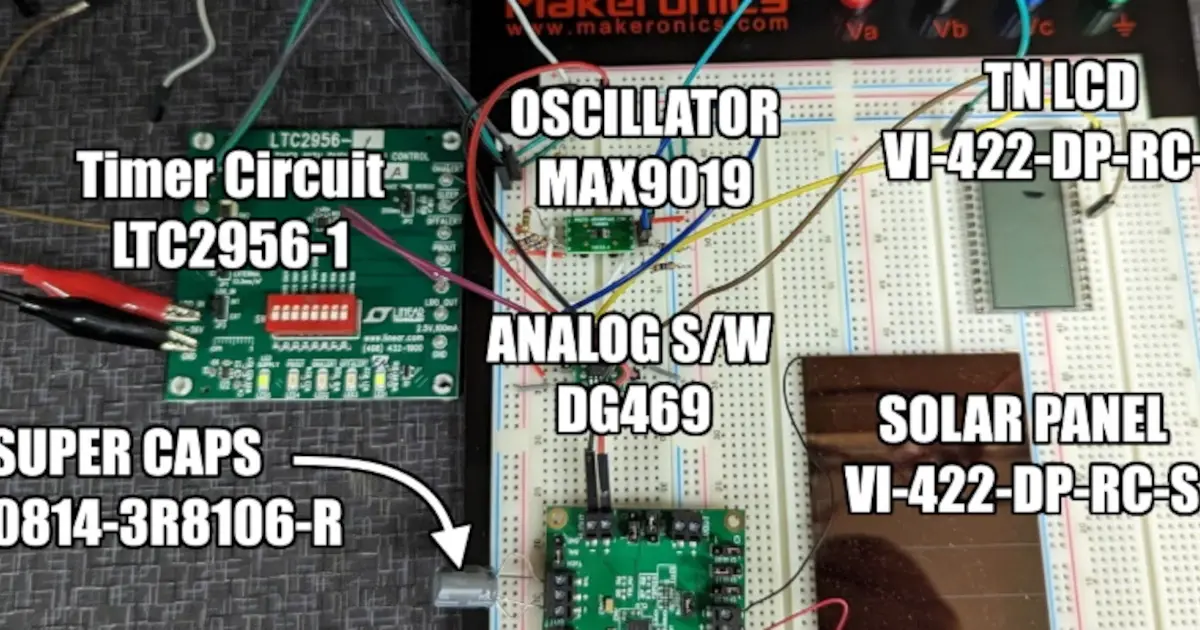
Breadboarding for Success
This week we are talking about Breadboards. Is breadboarding a circuit or design still applicable in today's SMT component dominated world?
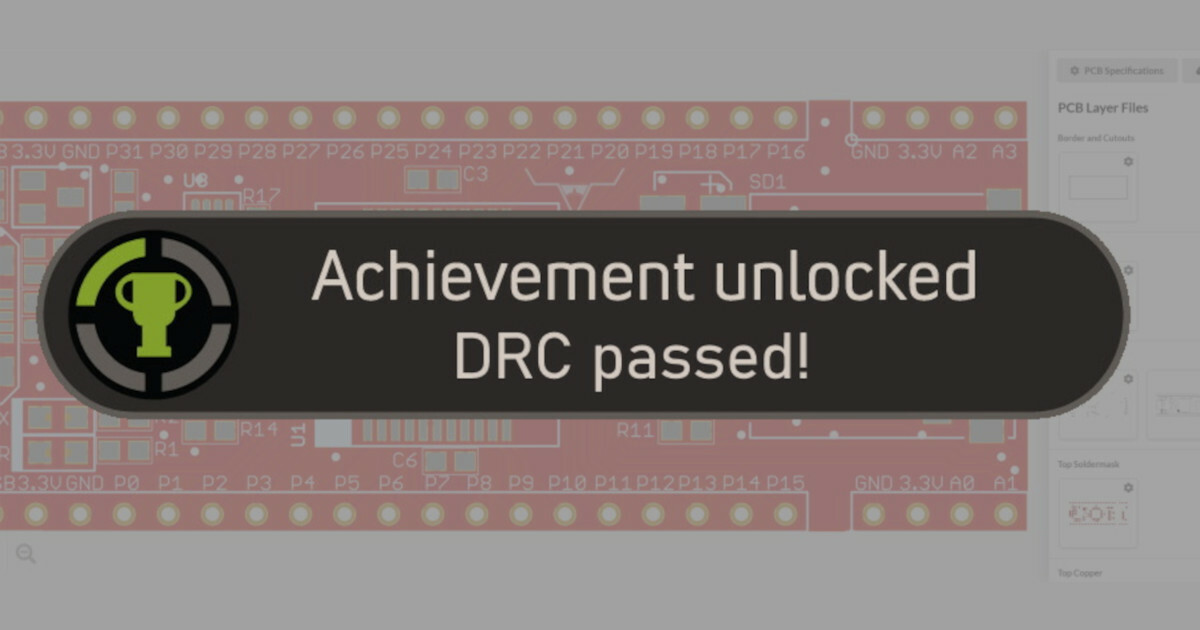
The Gamification of PCB Assembly
One faithful evening, Parker received a marketing email about gamifying the MacroFab platform and thought it might be a good podcast topic.
About MacroFab
MacroFab offers comprehensive manufacturing solutions, from your smallest prototyping orders to your largest production needs. Our factory network locations are strategically located across North America, ensuring that we have the flexibility to provide capacity when and where you need it most.
Experience the future of EMS manufacturing with our state-of-the-art technology platform and cutting-edge digital supply chain solutions. At MacroFab, we ensure that your electronics are produced faster, more efficiently, and with fewer logistic problems than ever before.
Take advantage of AI-enabled sourcing opportunities and employ expert teams who are connected through a user-friendly technology platform. Discover how streamlined electronics manufacturing can benefit your business by contacting us today.