Related Topics
Remote Ownership
Tariffs hike hits electronics! Hear Parker analyze cost impact & debate chip kill switch ethics with Stephen. Plus, Parker's Python invoice hack!
Captured Pads
Parker & Stephen dive into Circuit Break Discourse, LT3073 regulator, Weldestroyer updates, Box Truk progress, and more!
We Are Circuit Break
Parker and Stephen celebrate episode 400 of the MacroFab Engineering Podcast and announce its relaunch as Circuit Break.
Other Resources
Circuit Break Podcast
Webinars
Videos
Tour MacroFab's ITAR-Compliant Facility
March 11, 2020, Episode #215
Parker
- Brewery Update
- Pump mount design completed
- 3D printed brackets
- Bending tubing this week!
- Need to finish the last bit of wiring in the electrical box
- Python PDF Creation
- Why do they all suck?
- Currently using fpdf
Stephen
- CNC Update
- Moving…mostly
- Still need to get the X-axis moving
- Sprockets to weld on
- Will try rotational tig welding
- Midi to G-Code
- Motor Cable
- Igus 16/4 plus braided shield
- Chainflex
- Best way to attach the shield?
- Rack Mount Amplifier
- Replaced the transformer last week to boost the votlage
- Went from a 12:230 to a 10:230 ratio for a 20% increase
- Output changed exactly by 20%….go figure!
- Moving…mostly
Rapid Fire Opinion
- 3D printed forms for sheet metal pressing?
- Sort of Worked…
- Interesting to see the progress but it still required a mill to get a usable form
- With more experimentation and proper design of the part to be bent this could be a real option
- 3D printed tool punches as well
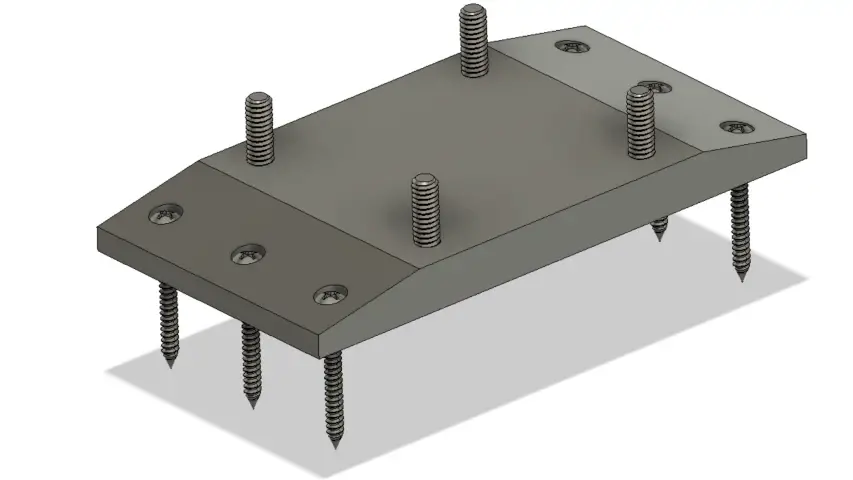
3D model of the pump bracket Parker design for his home brewing rig. Modeled with Autodesk Fusion 360.
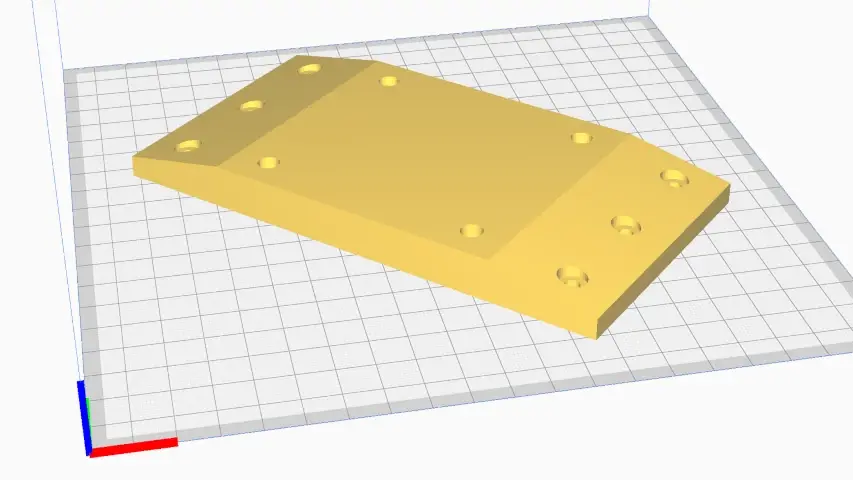
Slicing the STL file that was output from Autodesk Fusion 360. Parker uses Cura for the slicer currently.
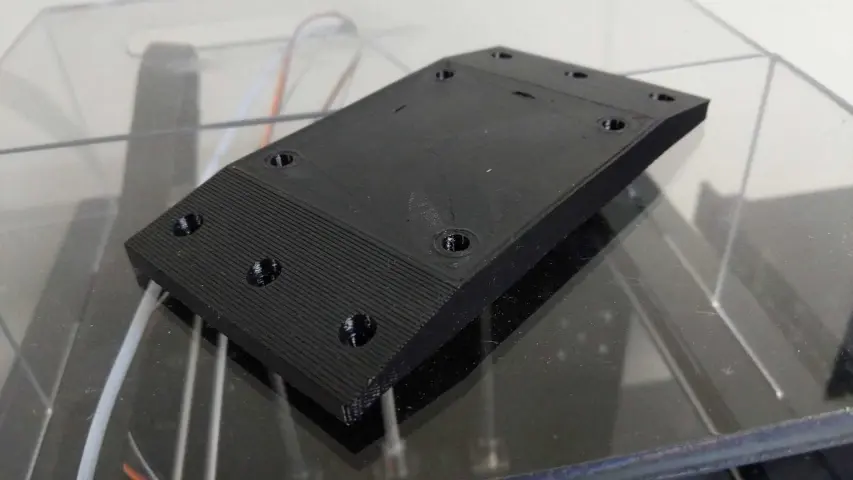
One over night session of printing and the first bracket is off the 3D printer! Turned out great so far!
The CNC Machine in Action!
About the Hosts
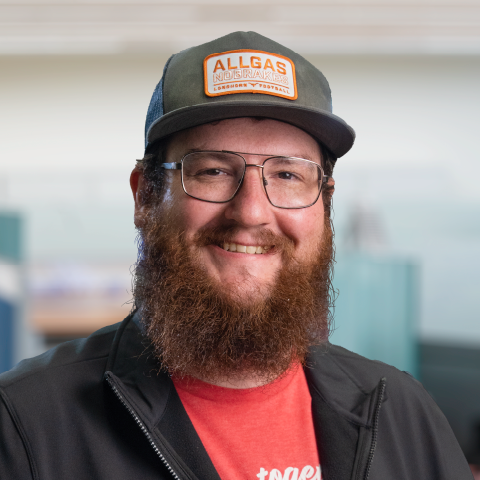
Parker Dillmann
Parker is an Electrical Engineer with backgrounds in Embedded System Design and Digital Signal Processing. He got his start in 2005 by hacking Nintendo consoles into portable gaming units. The following year he designed and produced an Atari 2600 video mod to allow the Atari to display a crisp, RF fuzz free picture on newer TVs. Over a thousand Atari video mods where produced by Parker from 2006 to 2011 and the mod is still made by other enthusiasts in the Atari community.
In 2006, Parker enrolled at The University of Texas at Austin as a Petroleum Engineer. After realizing electronics was his passion he switched majors in 2007 to Electrical and Computer Engineering. Following his previous background in making the Atari 2600 video mod, Parker decided to take more board layout classes and circuit design classes. Other areas of study include robotics, microcontroller theory and design, FPGA development with VHDL and Verilog, and image and signal processing with DSPs. In 2010, Parker won a Ti sponsored Launchpad programming and design contest that was held by the IEEE CS chapter at the University. Parker graduated with a BS in Electrical and Computer Engineering in the Spring of 2012.
In the Summer of 2012, Parker was hired on as an Electrical Engineer at Dynamic Perception to design and prototype new electronic products. Here, Parker learned about full product development cycles and honed his board layout skills. Seeing the difficulties in managing operations and FCC/CE compliance testing, Parker thought there had to be a better way for small electronic companies to get their product out in customer's hands.
Parker also runs the blog, longhornengineer.com, where he posts his personal projects, technical guides, and appnotes about board layout design and components.
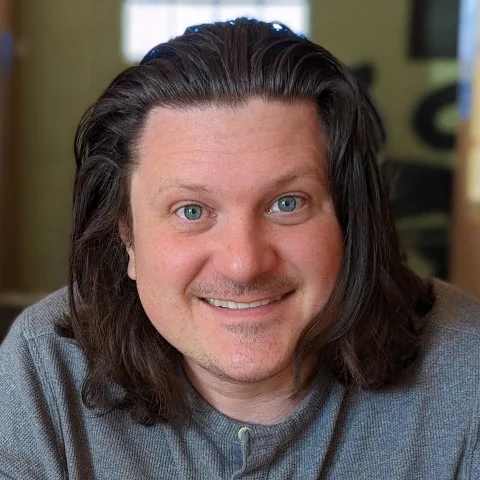
Stephen Kraig
Stephen Kraig is a component engineer working in the aerospace industry. He has applied his electrical engineering knowledge in a variety of contexts previously, including oil and gas, contract manufacturing, audio electronic repair, and synthesizer design. A graduate of Texas A&M, Stephen has lived his adult life in the Houston, TX, and Denver, CO, areas.
Stephen has never said no to a project. From building guitar amps (starting when he was 17) to designing and building his own CNC table to fine-tuning the mineral composition of the water he uses to brew beer, he thrives on testing, experimentation, and problem-solving. Tune into the podcast to learn more about the wacky stuff Stephen gets up to.
Special thanks to whixr over at Tymkrs for the intro and outro!
Related Podcasts
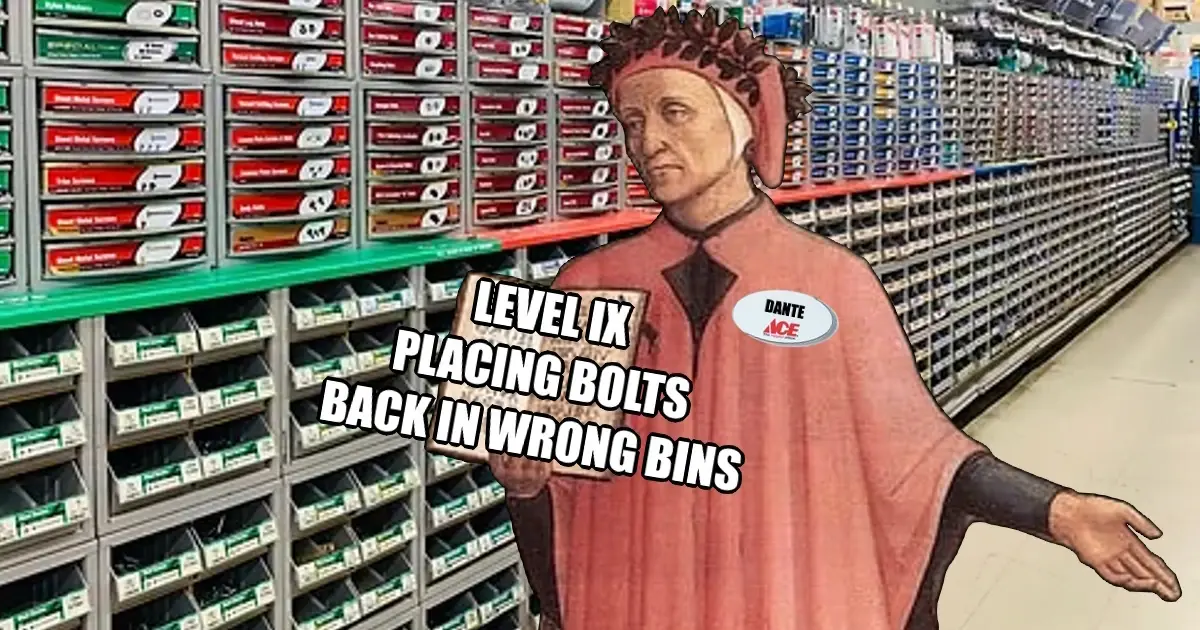
Mislabeled Levels of Hell
We kick off this week with a timely discussion of whether you can cook food on the engine of your car; how hot would your exhaust pipes even need to be?
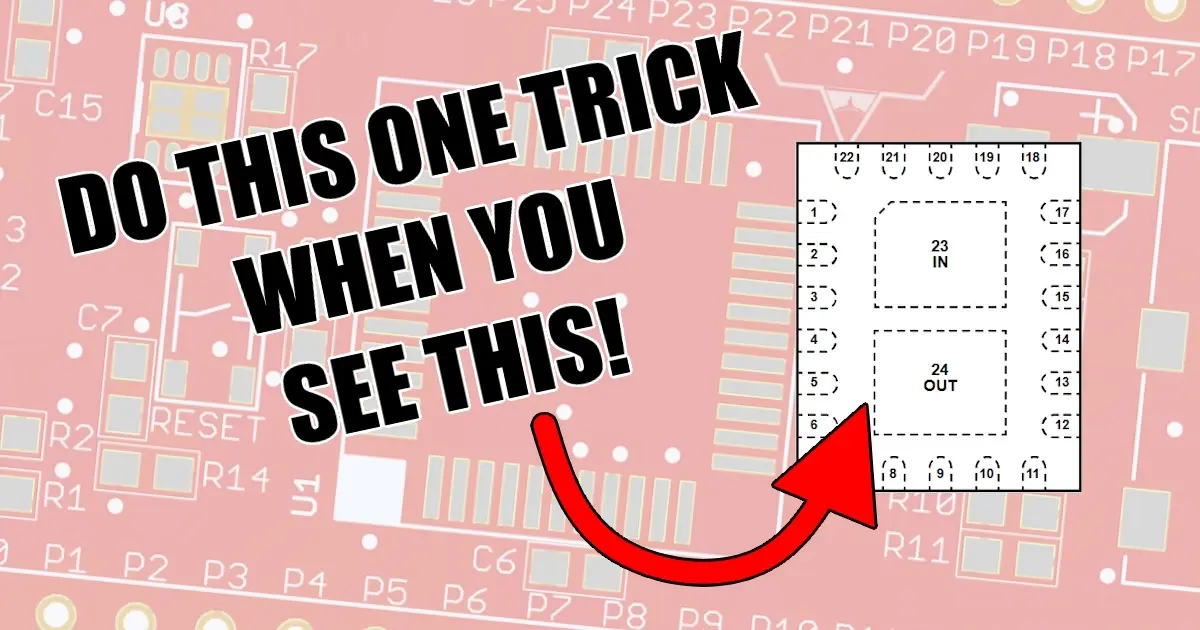
Captured Pads
Parker & Stephen dive into Circuit Break Discourse, LT3073 regulator, Weldestroyer updates, Box Truk progress, and more!
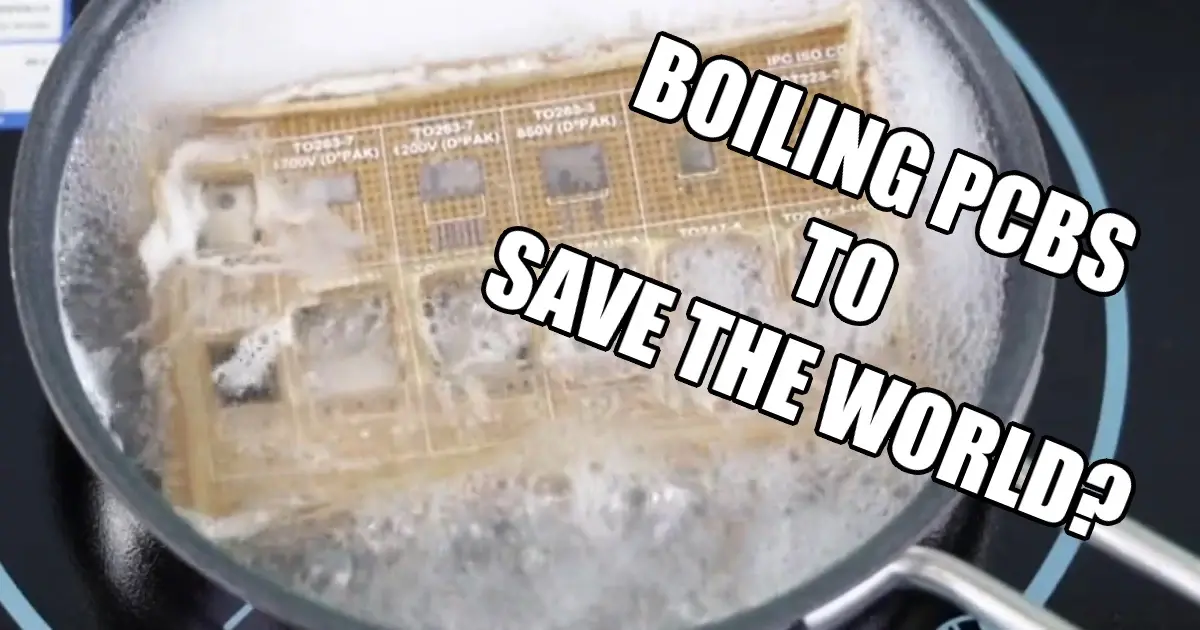
Recyclable PCBs, EOL Design, Cold Cuts
Infineon’s use of recyclable PCBs to create a soluboard. An examination of the new Arduino Uno, Minima and Wifi, plus a CNC and saw blade update.
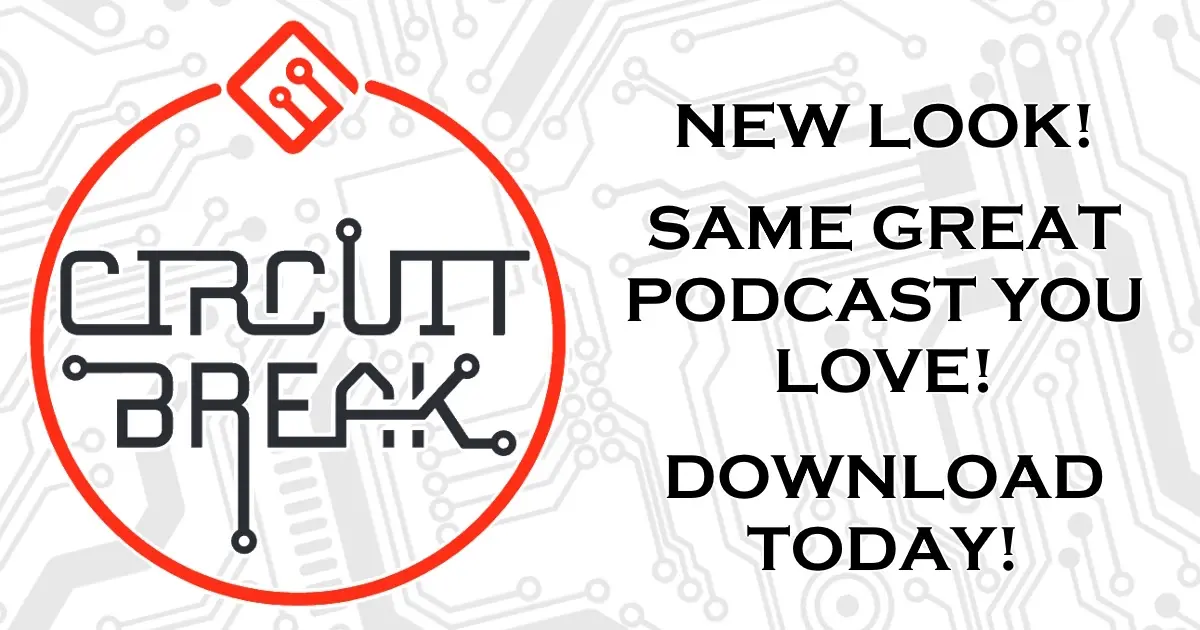
We Are Circuit Break
Parker and Stephen celebrate episode 400 of the MacroFab Engineering Podcast and announce its relaunch as Circuit Break.
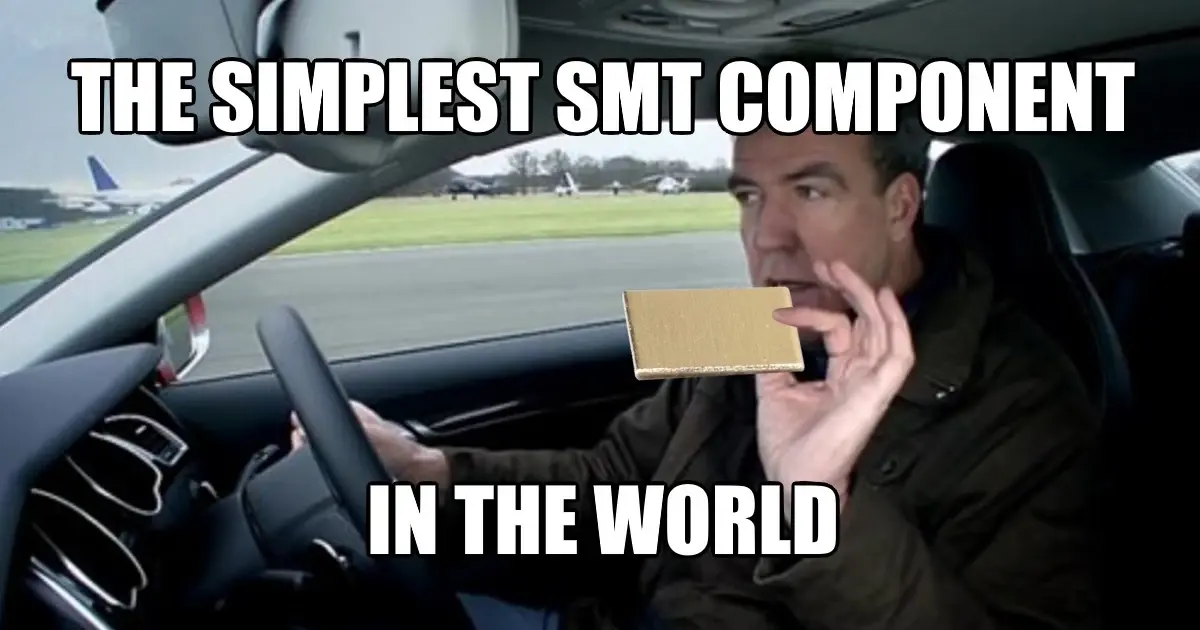
The Simplest SMT Component… In The World
Stephen’s CNC steps closer to being completed! Parker receives a newsletter that has the simplest SMT component in the world.
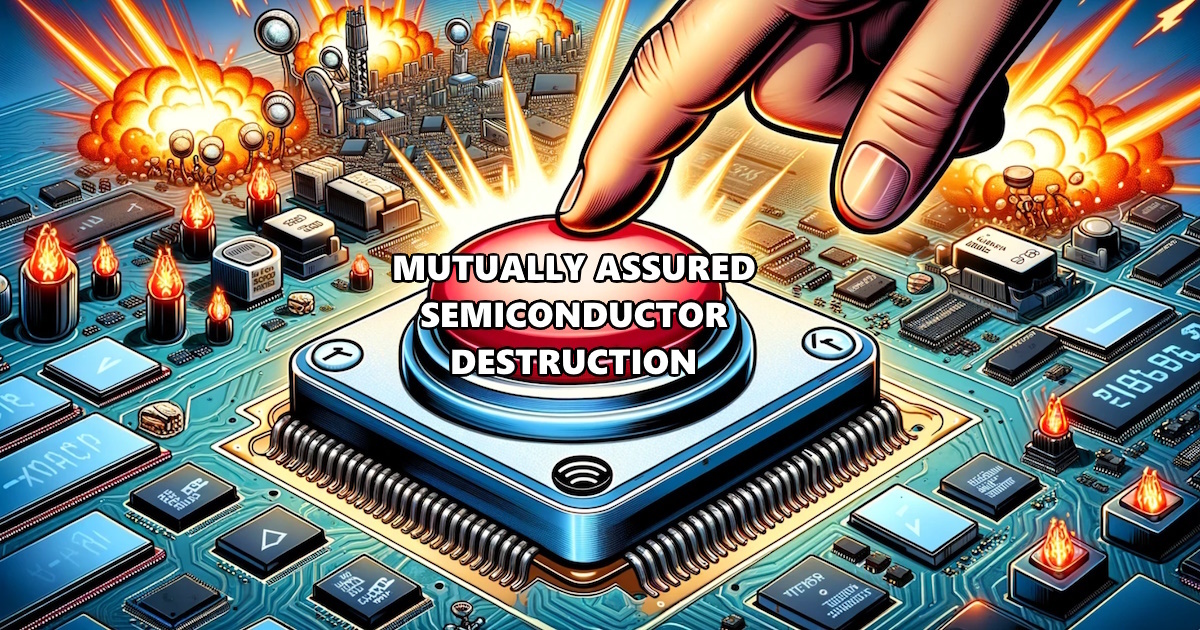
Remote Ownership
Tariffs hike hits electronics! Hear Parker analyze cost impact & debate chip kill switch ethics with Stephen. Plus, Parker's Python invoice hack!
About MacroFab
MacroFab offers comprehensive manufacturing solutions, from your smallest prototyping orders to your largest production needs. Our factory network locations are strategically located across North America, ensuring that we have the flexibility to provide capacity when and where you need it most.
Experience the future of EMS manufacturing with our state-of-the-art technology platform and cutting-edge digital supply chain solutions. At MacroFab, we ensure that your electronics are produced faster, more efficiently, and with fewer logistic problems than ever before.
Take advantage of AI-enabled sourcing opportunities and employ expert teams who are connected through a user-friendly technology platform. Discover how streamlined electronics manufacturing can benefit your business by contacting us today.