Circuit Break Podcast #141
It Depends – An In Depth Look at MLCCs with James Lewis
Related Topics
The Mega IIe: A Vintage Computing Adventure with James Lewis
Tune in for a fascinating journey from the past to the future, bridging vintage computing with modern technology with James Lewis, aka the Bald Engineer.
Entropy Rules Everything
Circuit Break welcomes back James! His expert insights on component aging - 5 years? 20 years? Calculations?! - sparked a convo we couldn't miss. Tune in!
Starting From The Beginning
When did you start listening to the podcast? Have a favorite episode? Let Stephen and Parker know which is your favorite.
Other Resources
Circuit Break Podcast
Webinars
Videos
Tour MacroFab's ITAR-Compliant Facility
October 10, 2018, Episode #141
- James Lewis
- Our guest this week may or may not be an Engineer or may or may not have Hair!
- James Lewis’ passion for teaching non-engineers has led to him to create the Bald Engineer Blog and the AddOhms video tutorial series
- With 15 years of experience in electronics, marketing, sales, and teaching James boils seemingly difficult concepts down to the core, so that anyone can learn what they need to finish that next great project
- Worked at Agilent as an FAE for oscilloscopes (for about 10 years), then as an FAE and marketing at KEMET for about 7 years
- Now working as oscilloscope product manager at Rohde and Schwarz
- MLCC – Multi – Layer Ceramic Capacitors
- Where did all the MLCCs go?
- Looking back, it was obvious we were headed towards a shortage but companies didn’t see it coming
- What are they?
- Common uses?
- 4 ways Ceramics lose capacitance
- Temperature
- Tolerance
- DC Bias
- Aging effect
- What to consider when choosing an alternative dielectric/technology for capacitors
- Where did all the MLCCs go?
- Questions from the Slack Channel
- Insights into selecting bootstrap caps for high-frequency, high-voltage H-bridges
- What footprint should we be designing with, going forward? Presumably different sizes for decoupling vs bulk on the power inputs for getting different ESRs?
- Is MLCC cracking due to pcb flex something that still gets seen in 0402 and below?
- General rules of thumb on choosing appropriate packages based upon desired voltage rating and capacitance?
- What *is* the fundamental physical mechanism behind this voltage-dependent capacitance drop?
- Why does the Y5V dielectric exist?
- Notes
- SL0 ceramic capacitor dielectrics
- SMT Soldering Guide for Capacitors
- Yoga Poses May be Good For You, But not Your Ceramic Capacitors
- Murata Article on Aging
Visit our Slack Channel and join the conversation in between episodes and please review us, wherever you listen (PodcastAddict, iTunes). It helps this show stay visible and helps new listeners find us.
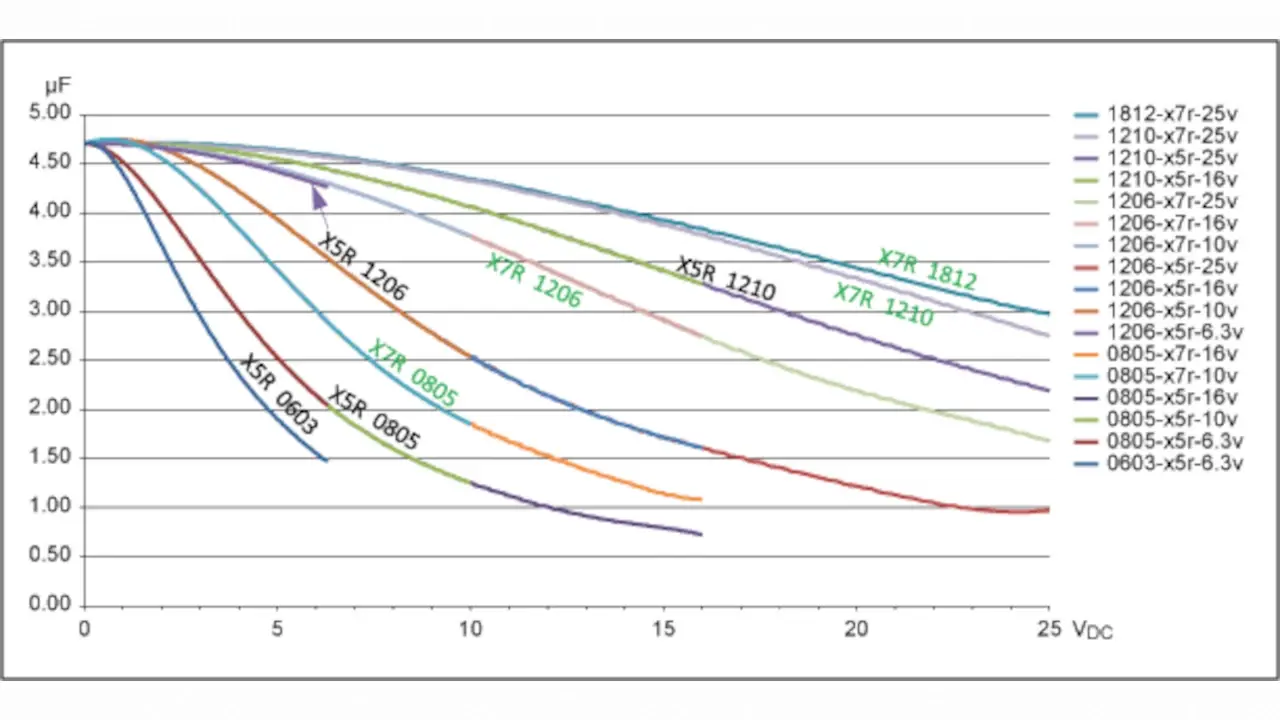
DC Bias graph for different dieletrics from Maxim.
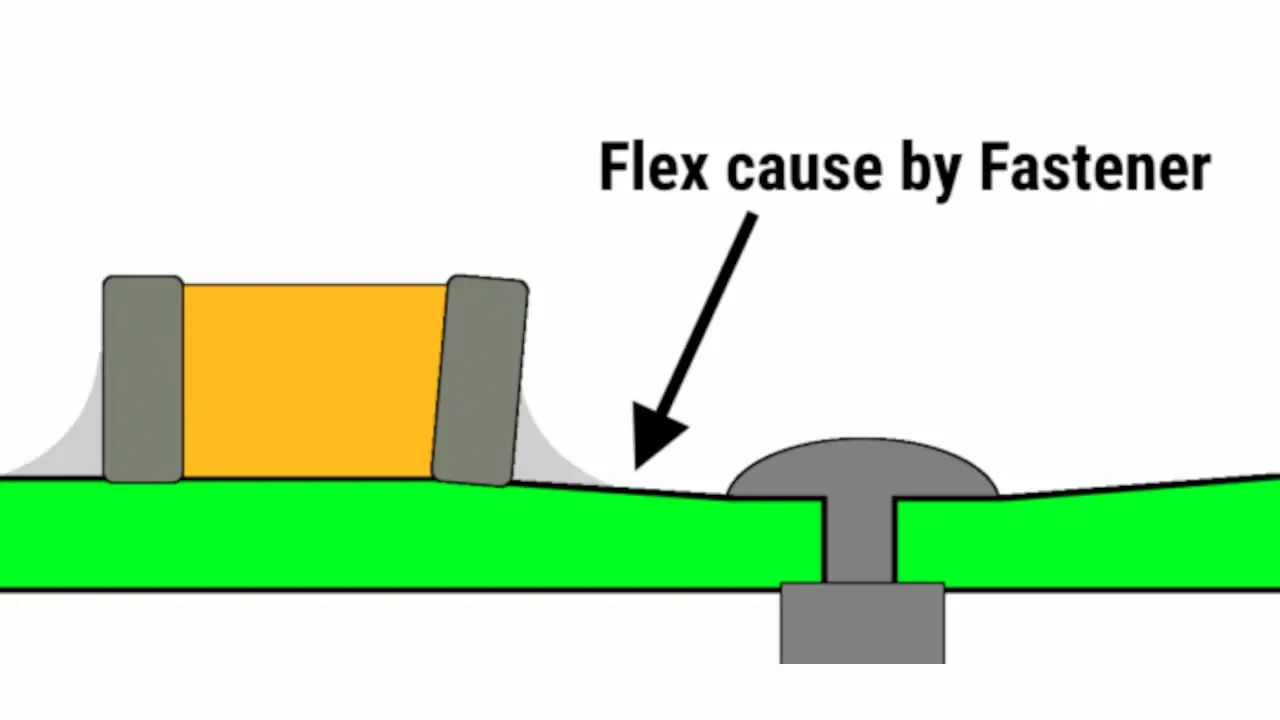
Drawing of capacitor flex due to PCB to enclosure fasteners.
About the Hosts
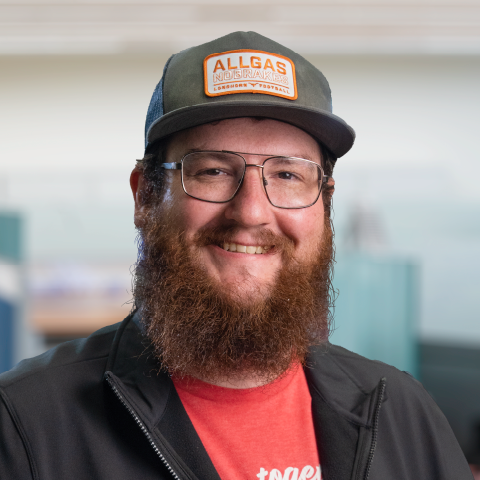
Parker Dillmann
Parker is an Electrical Engineer with backgrounds in Embedded System Design and Digital Signal Processing. He got his start in 2005 by hacking Nintendo consoles into portable gaming units. The following year he designed and produced an Atari 2600 video mod to allow the Atari to display a crisp, RF fuzz free picture on newer TVs. Over a thousand Atari video mods where produced by Parker from 2006 to 2011 and the mod is still made by other enthusiasts in the Atari community.
In 2006, Parker enrolled at The University of Texas at Austin as a Petroleum Engineer. After realizing electronics was his passion he switched majors in 2007 to Electrical and Computer Engineering. Following his previous background in making the Atari 2600 video mod, Parker decided to take more board layout classes and circuit design classes. Other areas of study include robotics, microcontroller theory and design, FPGA development with VHDL and Verilog, and image and signal processing with DSPs. In 2010, Parker won a Ti sponsored Launchpad programming and design contest that was held by the IEEE CS chapter at the University. Parker graduated with a BS in Electrical and Computer Engineering in the Spring of 2012.
In the Summer of 2012, Parker was hired on as an Electrical Engineer at Dynamic Perception to design and prototype new electronic products. Here, Parker learned about full product development cycles and honed his board layout skills. Seeing the difficulties in managing operations and FCC/CE compliance testing, Parker thought there had to be a better way for small electronic companies to get their product out in customer's hands.
Parker also runs the blog, longhornengineer.com, where he posts his personal projects, technical guides, and appnotes about board layout design and components.
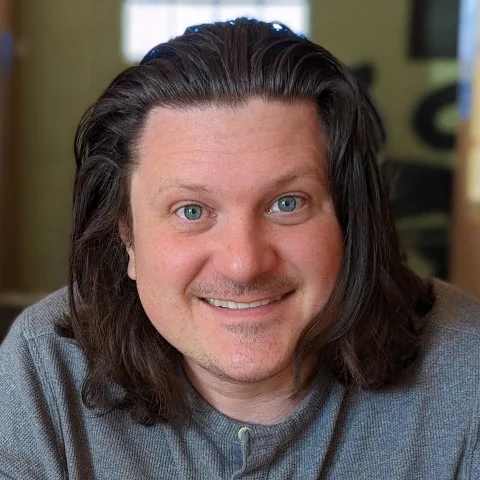
Stephen Kraig
Stephen Kraig is a component engineer working in the aerospace industry. He has applied his electrical engineering knowledge in a variety of contexts previously, including oil and gas, contract manufacturing, audio electronic repair, and synthesizer design. A graduate of Texas A&M, Stephen has lived his adult life in the Houston, TX, and Denver, CO, areas.
Stephen has never said no to a project. From building guitar amps (starting when he was 17) to designing and building his own CNC table to fine-tuning the mineral composition of the water he uses to brew beer, he thrives on testing, experimentation, and problem-solving. Tune into the podcast to learn more about the wacky stuff Stephen gets up to.
Special thanks to whixr over at Tymkrs for the intro and outro!
Related Podcasts
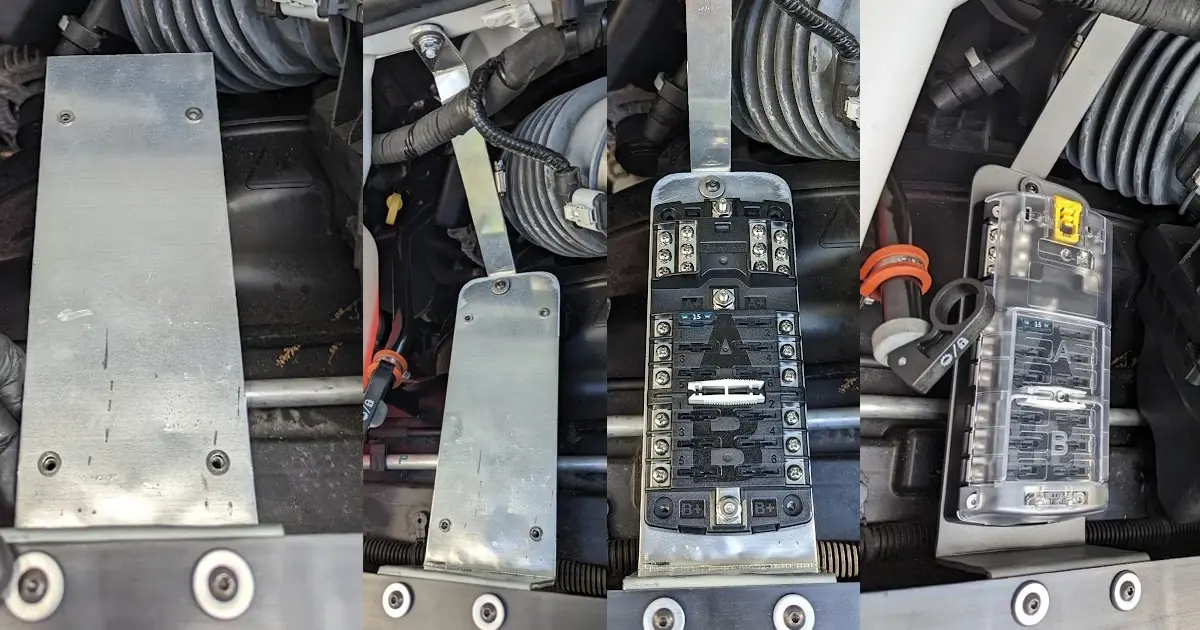
Starting From The Beginning
When did you start listening to the podcast? Have a favorite episode? Let Stephen and Parker know which is your favorite.
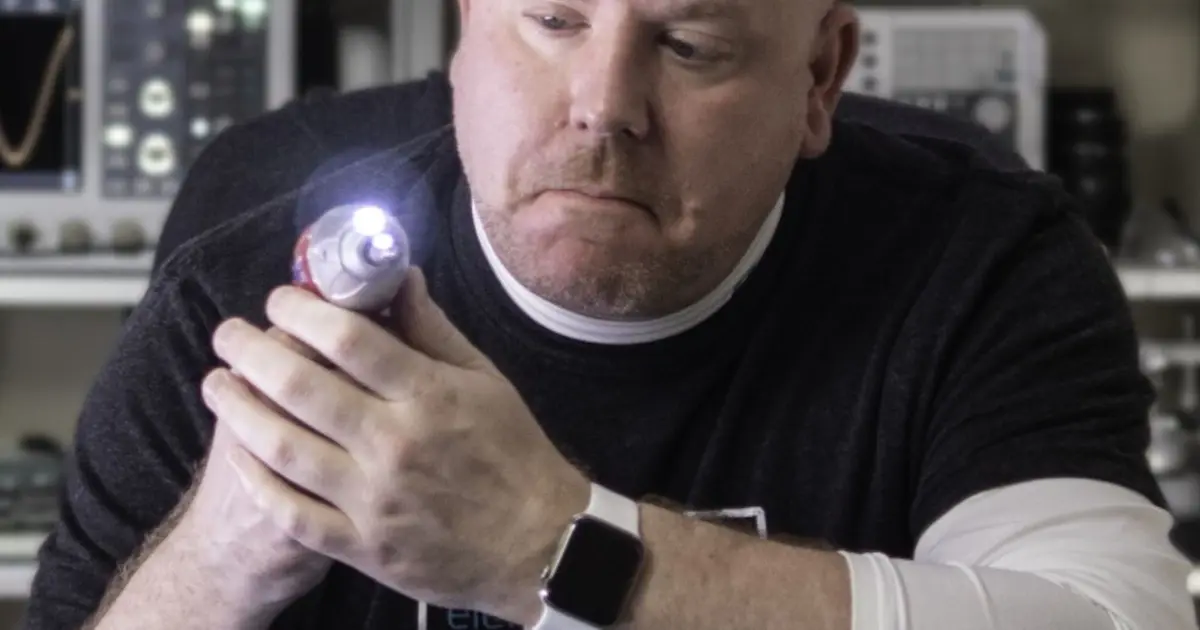
Turning It On – New Design Checklists with James Lewis
James Lewis is back to discuss testing and validating your new PCB Assembly design and what to look for in electronic lab equipment.
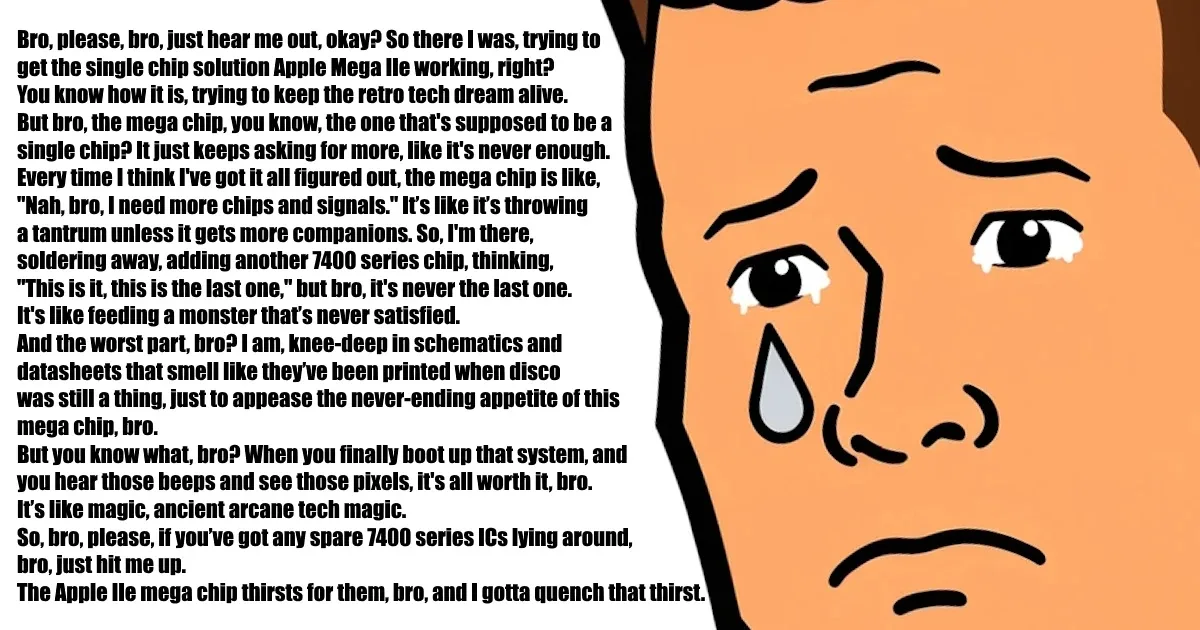
The Mega IIe: A Vintage Computing Adventure with James Lewis
Tune in for a fascinating journey from the past to the future, bridging vintage computing with modern technology with James Lewis, aka the Bald Engineer.
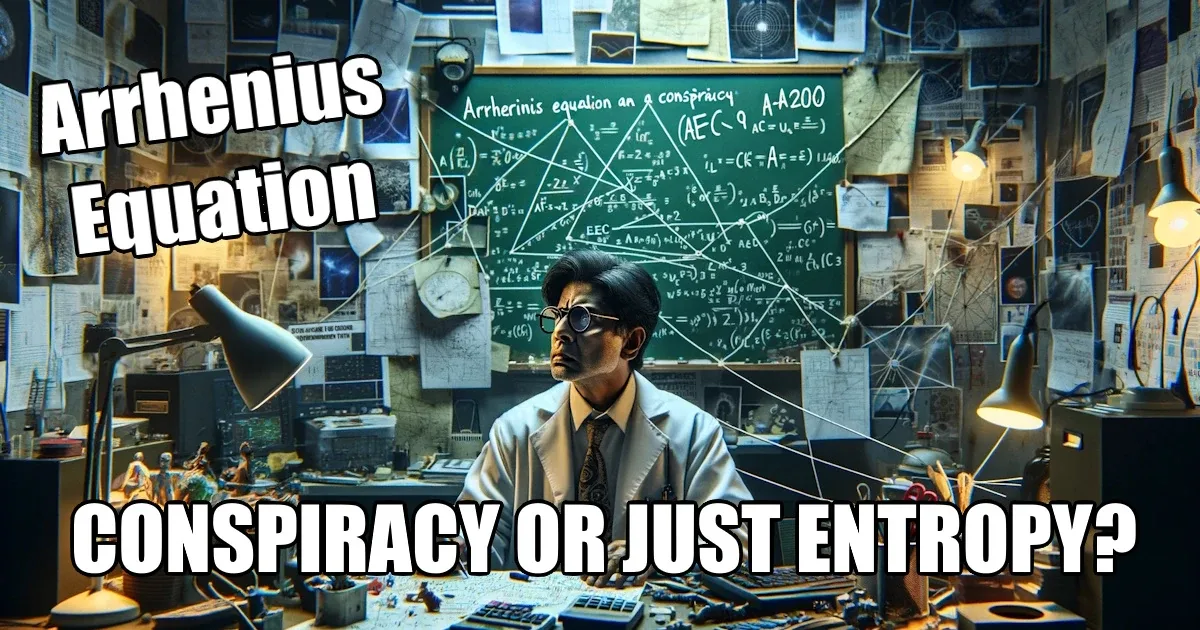
Entropy Rules Everything
Circuit Break welcomes back James! His expert insights on component aging - 5 years? 20 years? Calculations?! - sparked a convo we couldn't miss. Tune in!
About MacroFab
MacroFab offers comprehensive manufacturing solutions, from your smallest prototyping orders to your largest production needs. Our factory network locations are strategically located across North America, ensuring that we have the flexibility to provide capacity when and where you need it most.
Experience the future of EMS manufacturing with our state-of-the-art technology platform and cutting-edge digital supply chain solutions. At MacroFab, we ensure that your electronics are produced faster, more efficiently, and with fewer logistic problems than ever before.
Take advantage of AI-enabled sourcing opportunities and employ expert teams who are connected through a user-friendly technology platform. Discover how streamlined electronics manufacturing can benefit your business by contacting us today.