Circuit Break Podcast #134
Injection Molded Enclosure Design with John Teel
Related Topics
Top Features to Add to Your Next Prototype
Tune in as we share insights, anecdotes, and maybe a few confessions from our own prototyping adventures.
Magical Semiconductors of Pixies
We’re joined by Alexander Vartanov, an electrical engineering student with a knack for hands-on projects.
Connector Catalogs
This is the last installment of Stephen's 'Adventures in Injection Molding'. We are going to recap the entire two year sage and close the book on it.
Other Resources
Circuit Break Podcast
Webinars
Videos
Tour MacroFab's ITAR-Compliant Facility
August 22, 2018, Episode #134
- John Teel
- Founder of Predictable Designs, a company which helps startups, makers, and small companies develop new electronic products
- Previously, John was on Episode 106 of the MacroFab Engineering Podcast where John spoke about making the product development process as predictable as possible
- Injection Molding Enclosure Design
- What is the general process of injection molding?
- Challenges of Injection Molding: Why does it have this “mystic” aura around it?
- Designing enclosures for injection molding?
- Difference between designing for 3D printing and Injection molding
- What should you look for if you need to get a design done correctly
- What files will I need to have created?
- Do I design the mold or does someone else?
- Design is done. Who do I look for to get my design built?
- What questions should I have answered before contacting someone?
- Who do I talk to to get it done?
- How do I find a manufacturer locally or overseas?
- Who owns the mold?
- Should I go with a more expensive/larger mold or cheaper/smaller?
- How much should I be prepared to spend?
- Prototyping
- TL;DR for prototyping an injection molded enclosure
- Protolabs online DFM
- What if I want a sample?
- How do I pick the right material?
- Protolabs online DFM
- TL;DR for prototyping an injection molded enclosure
Visit our Slack Channel and join the conversation in between episodes and please review us, wherever you listen (PodcastAddict, iTunes). It helps this show stay visible and helps new listeners find us.
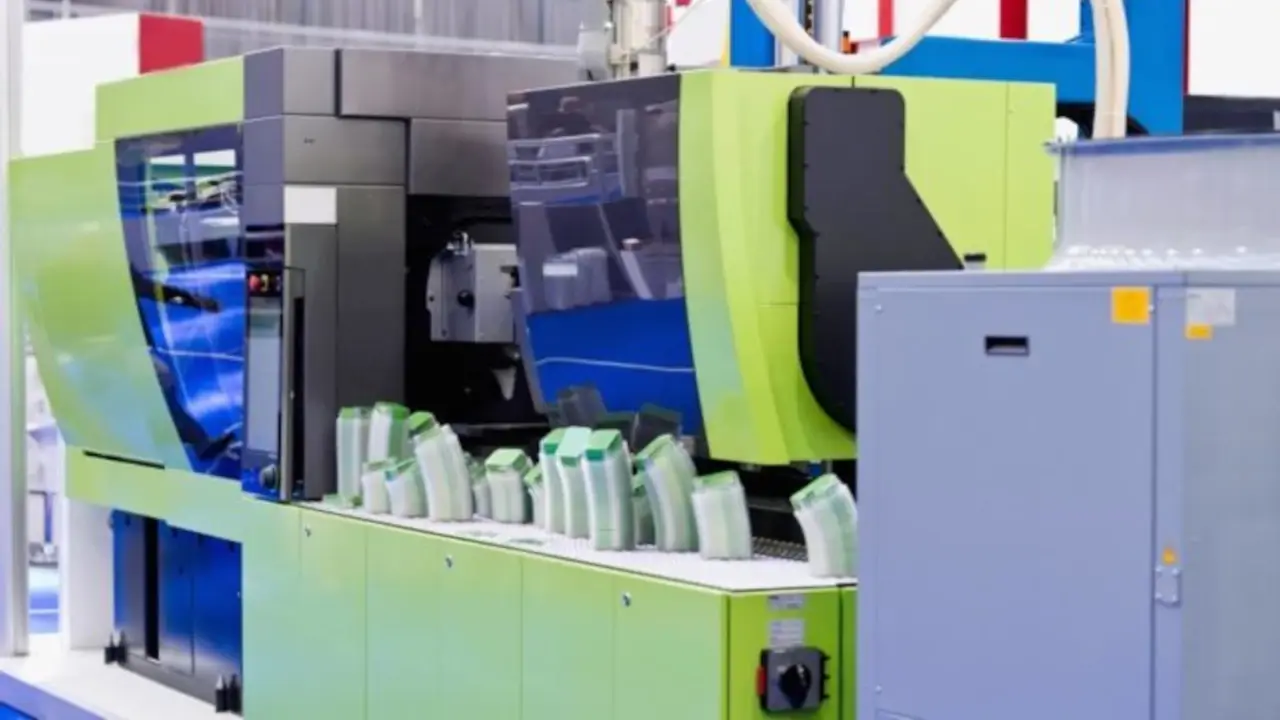
Injection molding machine.
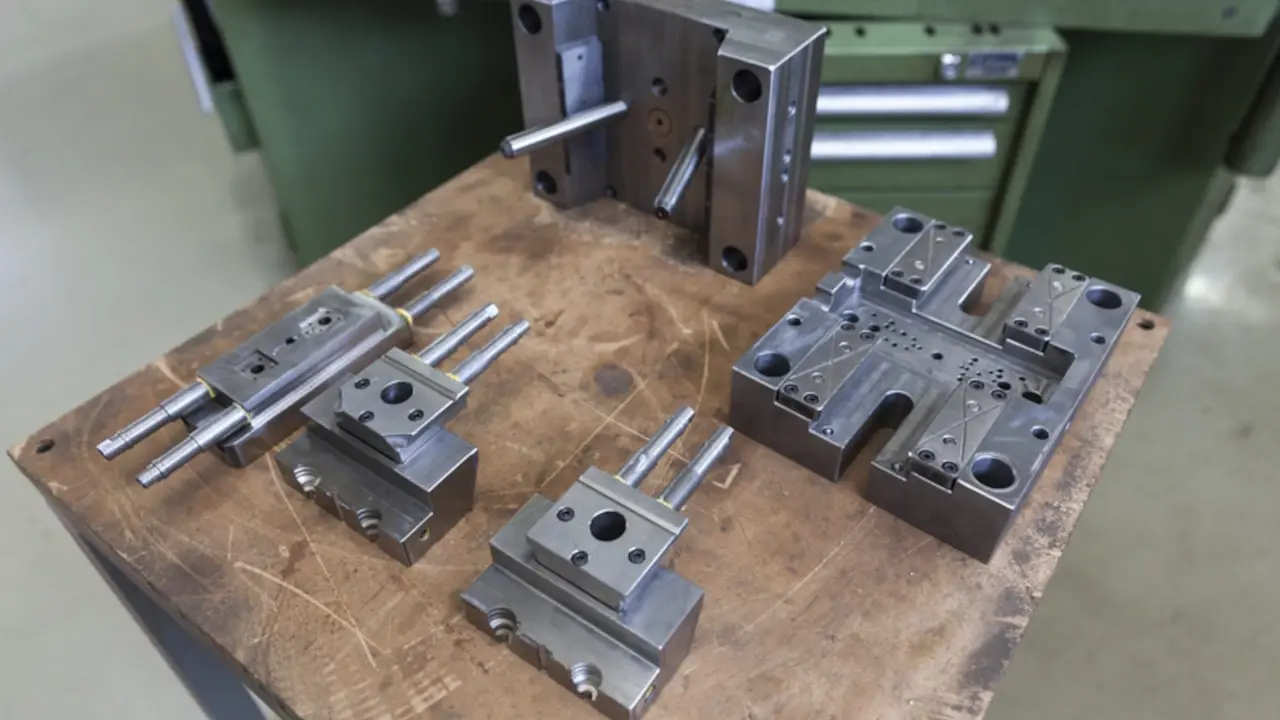
Molds for use in the injection molding process.
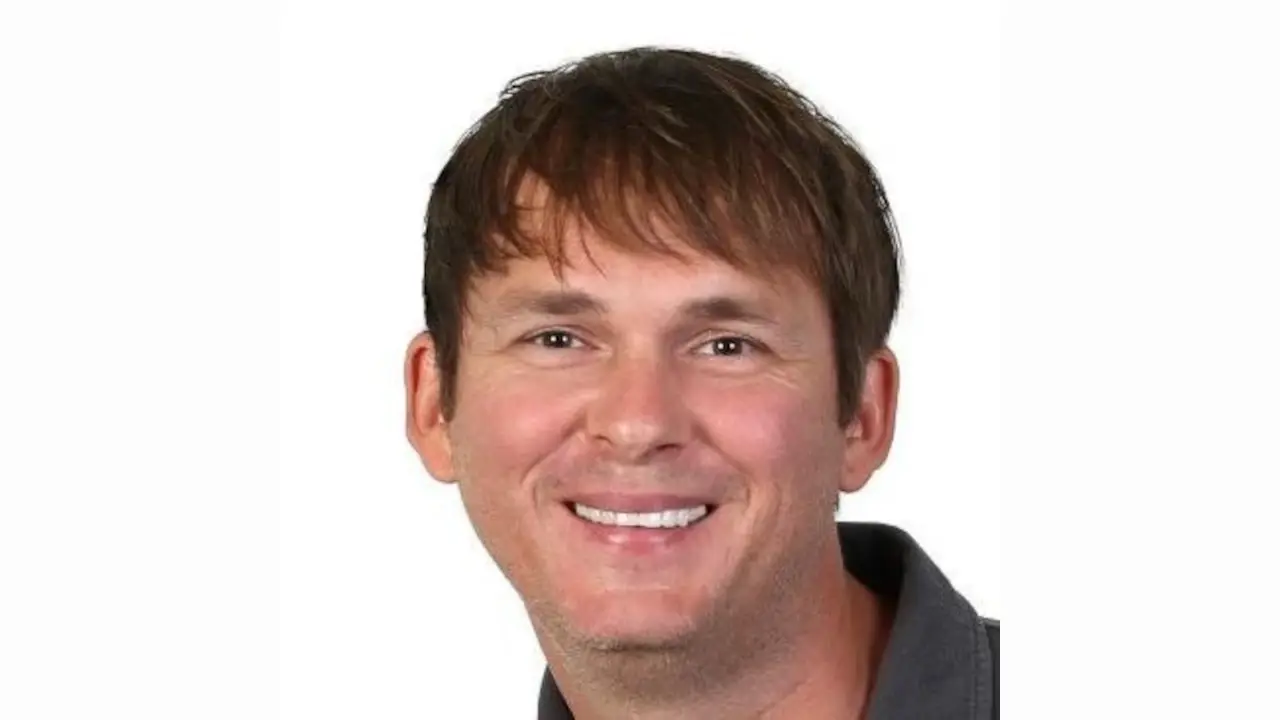
John Teel of Predictable Designs.
About the Hosts
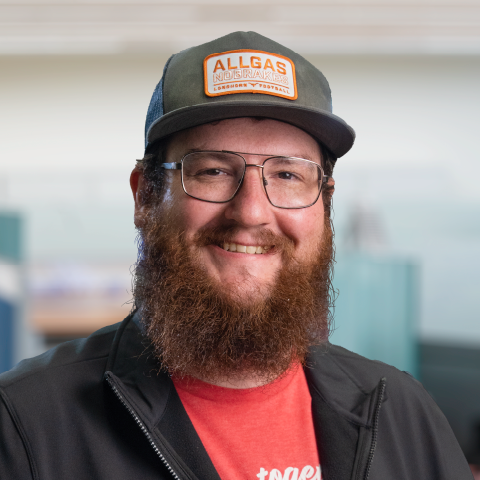
Parker Dillmann
Parker is an Electrical Engineer with backgrounds in Embedded System Design and Digital Signal Processing. He got his start in 2005 by hacking Nintendo consoles into portable gaming units. The following year he designed and produced an Atari 2600 video mod to allow the Atari to display a crisp, RF fuzz free picture on newer TVs. Over a thousand Atari video mods where produced by Parker from 2006 to 2011 and the mod is still made by other enthusiasts in the Atari community.
In 2006, Parker enrolled at The University of Texas at Austin as a Petroleum Engineer. After realizing electronics was his passion he switched majors in 2007 to Electrical and Computer Engineering. Following his previous background in making the Atari 2600 video mod, Parker decided to take more board layout classes and circuit design classes. Other areas of study include robotics, microcontroller theory and design, FPGA development with VHDL and Verilog, and image and signal processing with DSPs. In 2010, Parker won a Ti sponsored Launchpad programming and design contest that was held by the IEEE CS chapter at the University. Parker graduated with a BS in Electrical and Computer Engineering in the Spring of 2012.
In the Summer of 2012, Parker was hired on as an Electrical Engineer at Dynamic Perception to design and prototype new electronic products. Here, Parker learned about full product development cycles and honed his board layout skills. Seeing the difficulties in managing operations and FCC/CE compliance testing, Parker thought there had to be a better way for small electronic companies to get their product out in customer's hands.
Parker also runs the blog, longhornengineer.com, where he posts his personal projects, technical guides, and appnotes about board layout design and components.
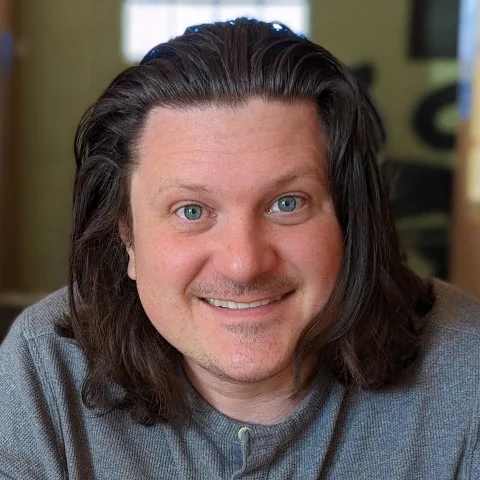
Stephen Kraig
Stephen Kraig is a component engineer working in the aerospace industry. He has applied his electrical engineering knowledge in a variety of contexts previously, including oil and gas, contract manufacturing, audio electronic repair, and synthesizer design. A graduate of Texas A&M, Stephen has lived his adult life in the Houston, TX, and Denver, CO, areas.
Stephen has never said no to a project. From building guitar amps (starting when he was 17) to designing and building his own CNC table to fine-tuning the mineral composition of the water he uses to brew beer, he thrives on testing, experimentation, and problem-solving. Tune into the podcast to learn more about the wacky stuff Stephen gets up to.
Special thanks to whixr over at Tymkrs for the intro and outro!
Related Podcasts
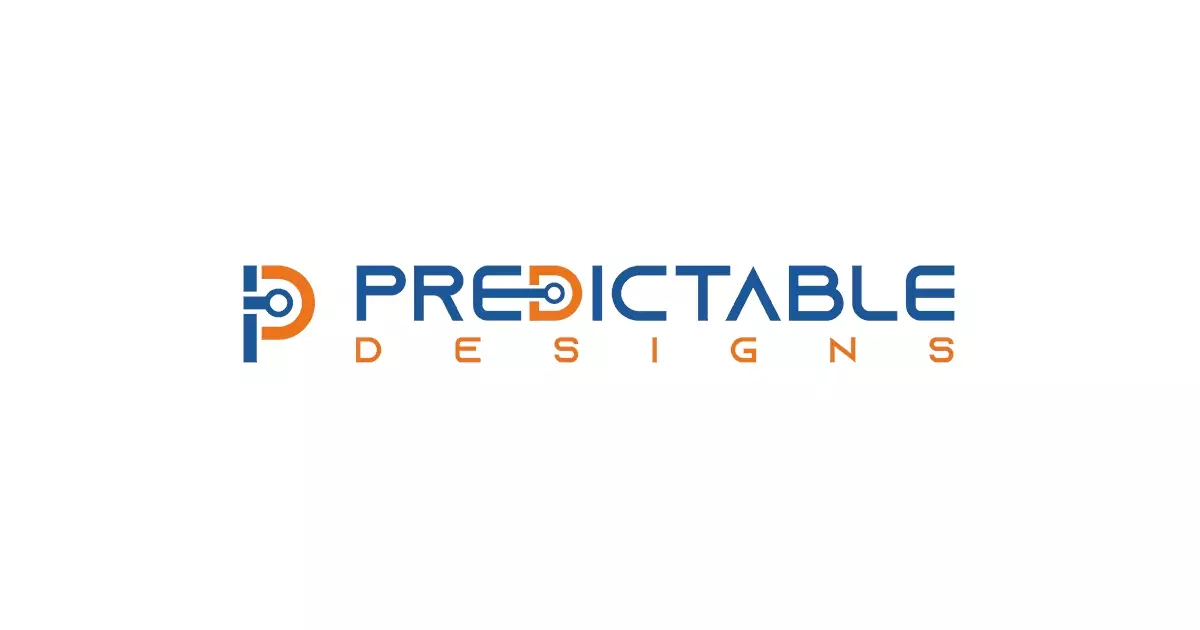
John Teel of Predictable Designs
Guest John Teel talks about how to make new hardware projects more predictable for manufacturing.
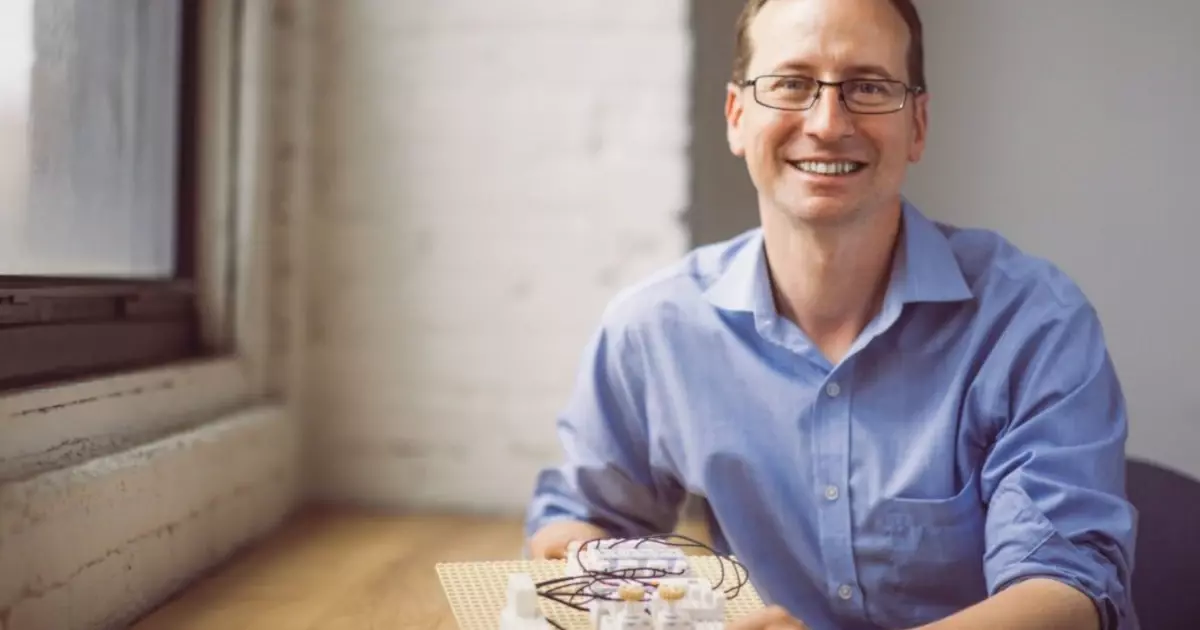
The Brick That Shall Not Be Named: A Joe Broms Story
Guest Joseph Broms talks about his experience in prototyping and designing his product ProtoBricks.
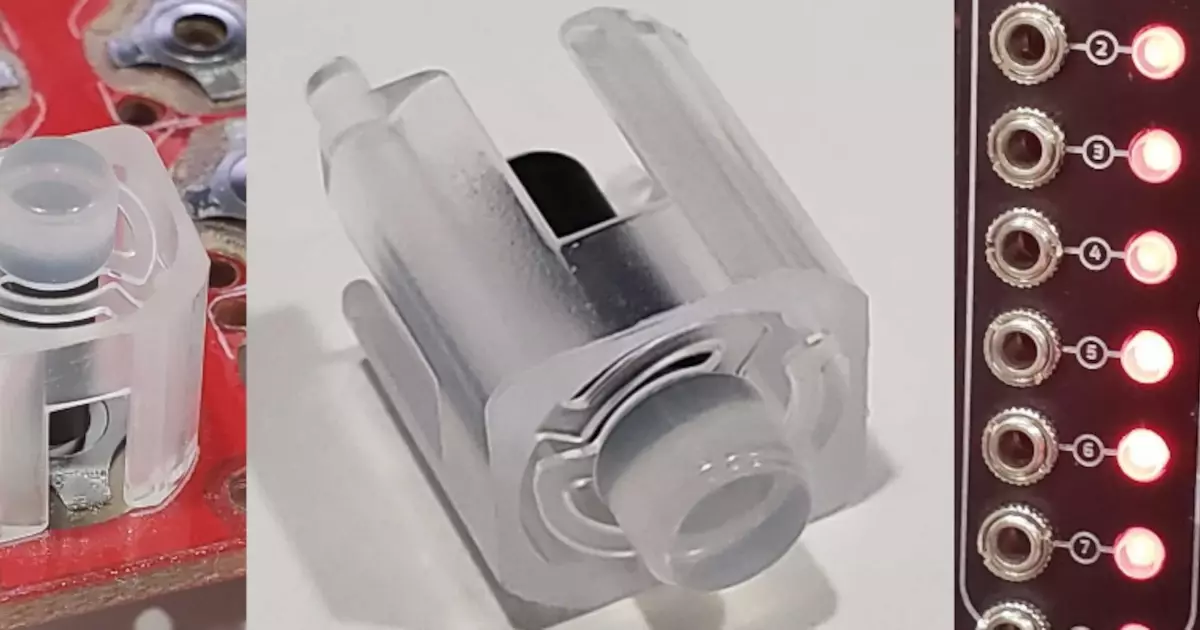
Connector Catalogs
This is the last installment of Stephen's 'Adventures in Injection Molding'. We are going to recap the entire two year sage and close the book on it.
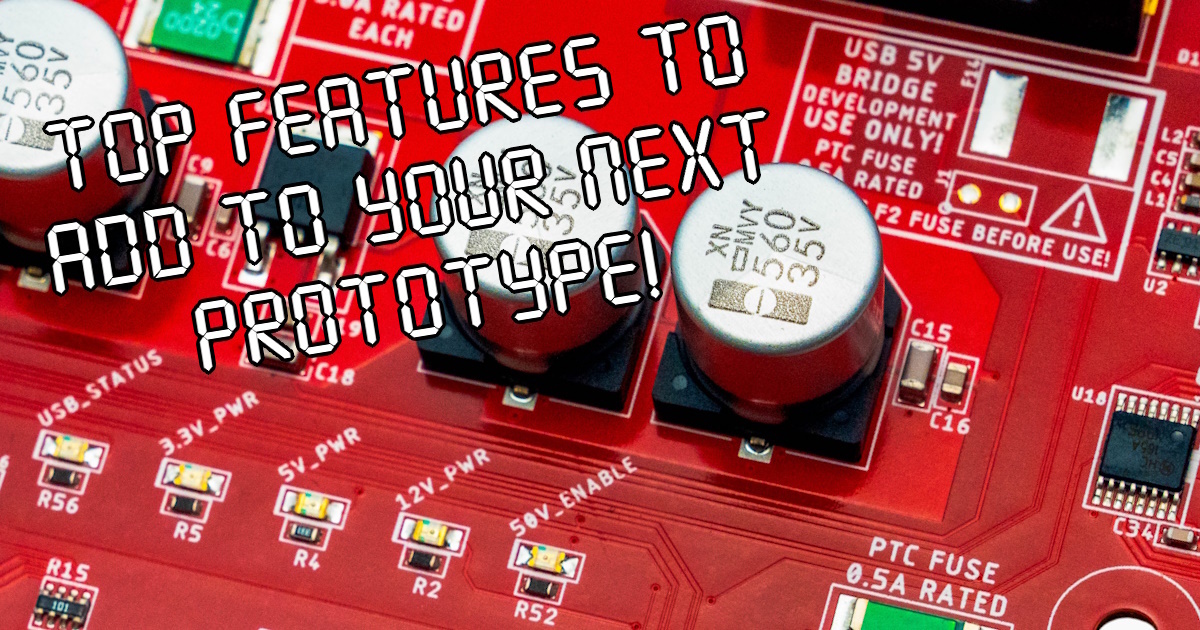
Top Features to Add to Your Next Prototype
Tune in as we share insights, anecdotes, and maybe a few confessions from our own prototyping adventures.
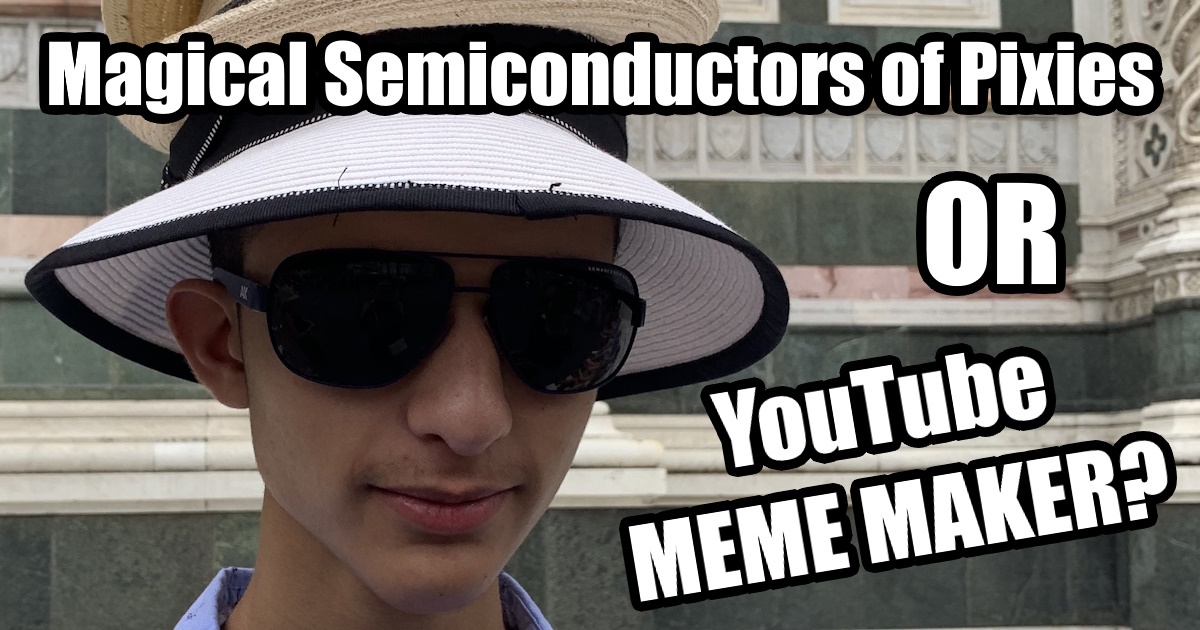
Magical Semiconductors of Pixies
We’re joined by Alexander Vartanov, an electrical engineering student with a knack for hands-on projects.
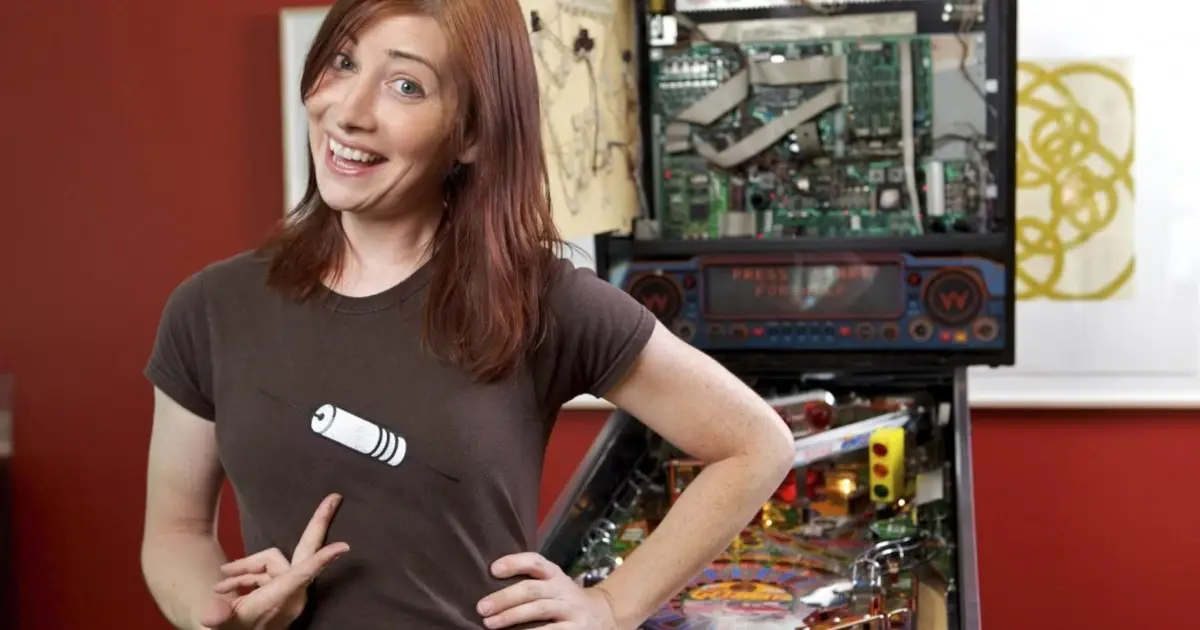
Adult Supervision Not Required – Tilt 5 With Jeri
Jeri Ellsworth joins the podcast to discuss the development of Augmented Reality technology and the process of bringing consumer devices to market.
About MacroFab
MacroFab offers comprehensive manufacturing solutions, from your smallest prototyping orders to your largest production needs. Our factory network locations are strategically located across North America, ensuring that we have the flexibility to provide capacity when and where you need it most.
Experience the future of EMS manufacturing with our state-of-the-art technology platform and cutting-edge digital supply chain solutions. At MacroFab, we ensure that your electronics are produced faster, more efficiently, and with fewer logistic problems than ever before.
Take advantage of AI-enabled sourcing opportunities and employ expert teams who are connected through a user-friendly technology platform. Discover how streamlined electronics manufacturing can benefit your business by contacting us today.