Circuit Break Podcast #197
Designing in Color – Greg Paulsen on 3D Printing
Related Topics
Platform Updates from Kyle McLeod and Nicholas Lundgaard
The episode provides insights into MacroFab's efforts to make PCB manufacturing more accessible and efficient for their customers.
Tracing a Path for PCB Design Automation with Sergiy Nesterenko
Sergiy Nestorenko, founder of Quilter and former SpaceX engineer, discusses revolutionizing PCB design automation.
Dr. Duncan Haldane from JITX on Automating Circuit Design
Dr. Haldane on his background, the problems JITX is trying to resolve, & new auto-router plans. What's the deal with the "hyper-aggressive pogo-stick"?
Other Resources
Circuit Break Podcast
Webinars
Videos
Tour MacroFab's ITAR-Compliant Facility
November 6, 2019, Episode #197
Episode 200 is Coming Up!
- Question / Answer setup like Episode 100
- Send them via Audio Format to podcast@macrofab.com
- The leader of the Application Engineering team at Xometry an online instant quoting platform for custom manufacturing projects, which utilize a professional network of thousands of manufacturers
- His background is in applied additive manufacturing, having experience as an engineer, running machines, and ultimately using the parts
- Was last on the podcast for episode 181 where we talked Xometry, Pizza, and digital manufacturing
- What is 3D printing, what makes it different from CNC, molding?
- Specifications for 3D printing
- How does the designer give the specifications/tolerance?
- Screws: 3d printing threads, self tappers, inserts
- Does and don’ts of designing stuff for 3D printing
- 3D printing in scale – how do you scale up?
- The pros and cons of running your own 3D printer versus say using a service to order things
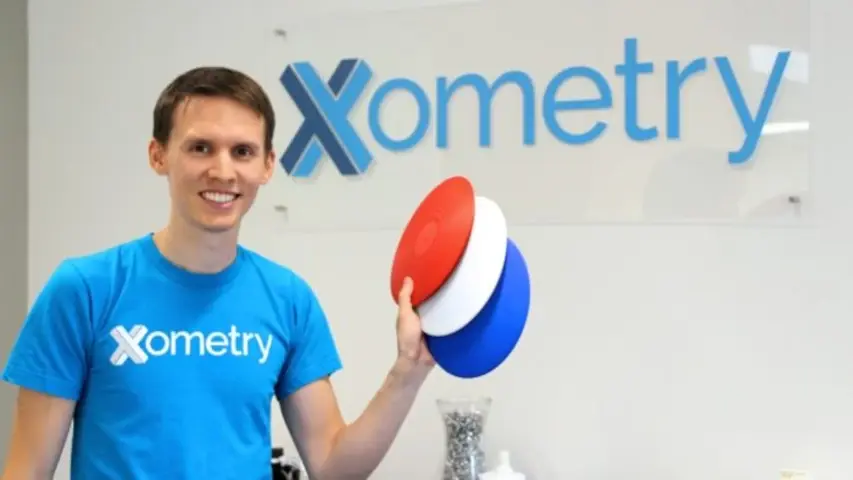
Greg Paulsen of Xometry holding what looks to be 3D printed frisbes.
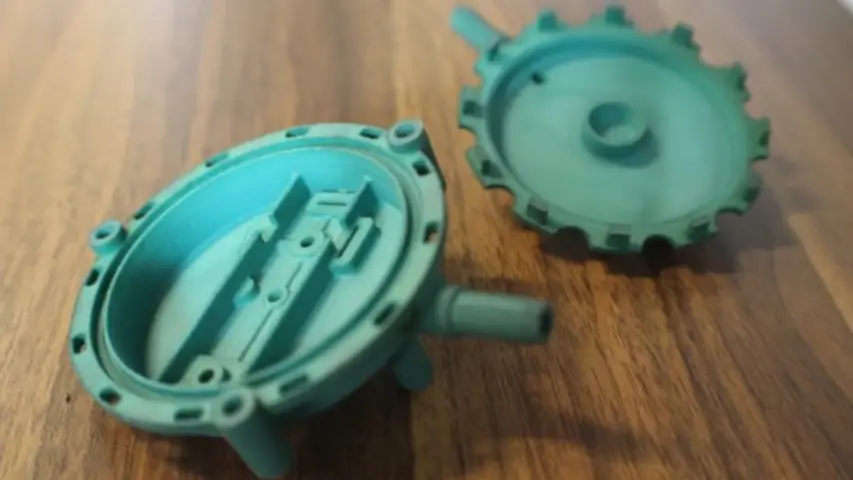
SLS printed enclosure dyed green.
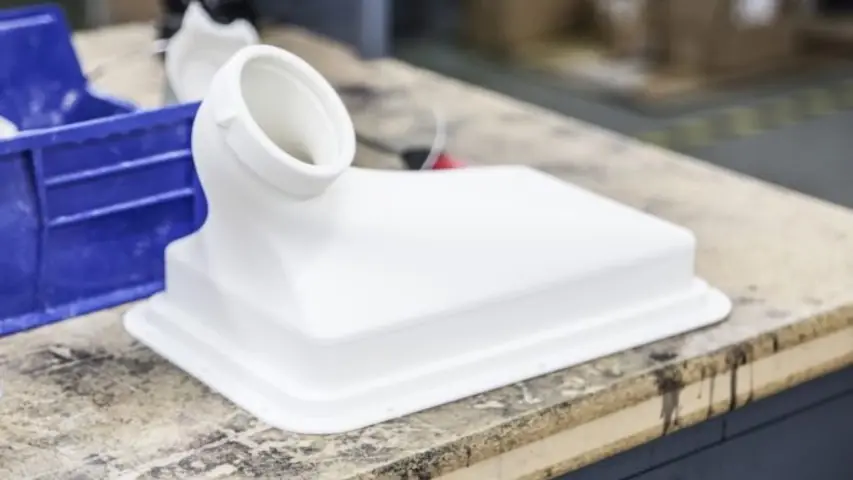
Prototype ducting printed with a SLS machine out of nylon material.

DMLS (metal 3D printing) aluminum alloy with support structures.
About the Hosts
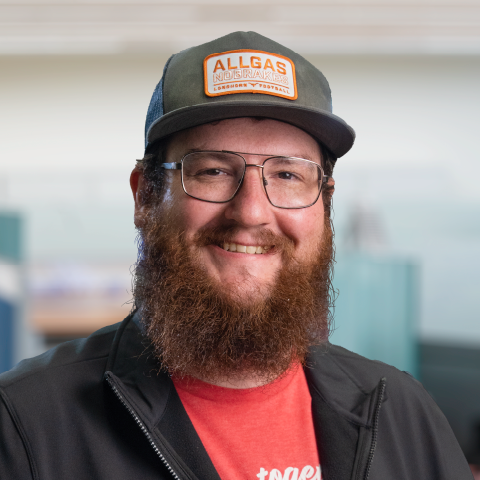
Parker Dillmann
Parker is an Electrical Engineer with backgrounds in Embedded System Design and Digital Signal Processing. He got his start in 2005 by hacking Nintendo consoles into portable gaming units. The following year he designed and produced an Atari 2600 video mod to allow the Atari to display a crisp, RF fuzz free picture on newer TVs. Over a thousand Atari video mods where produced by Parker from 2006 to 2011 and the mod is still made by other enthusiasts in the Atari community.
In 2006, Parker enrolled at The University of Texas at Austin as a Petroleum Engineer. After realizing electronics was his passion he switched majors in 2007 to Electrical and Computer Engineering. Following his previous background in making the Atari 2600 video mod, Parker decided to take more board layout classes and circuit design classes. Other areas of study include robotics, microcontroller theory and design, FPGA development with VHDL and Verilog, and image and signal processing with DSPs. In 2010, Parker won a Ti sponsored Launchpad programming and design contest that was held by the IEEE CS chapter at the University. Parker graduated with a BS in Electrical and Computer Engineering in the Spring of 2012.
In the Summer of 2012, Parker was hired on as an Electrical Engineer at Dynamic Perception to design and prototype new electronic products. Here, Parker learned about full product development cycles and honed his board layout skills. Seeing the difficulties in managing operations and FCC/CE compliance testing, Parker thought there had to be a better way for small electronic companies to get their product out in customer's hands.
Parker also runs the blog, longhornengineer.com, where he posts his personal projects, technical guides, and appnotes about board layout design and components.
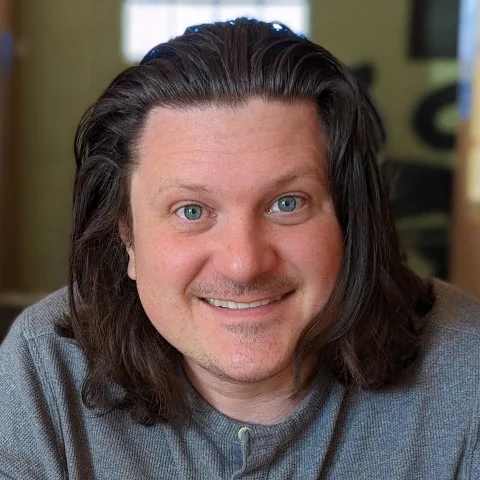
Stephen Kraig
Stephen Kraig is a component engineer working in the aerospace industry. He has applied his electrical engineering knowledge in a variety of contexts previously, including oil and gas, contract manufacturing, audio electronic repair, and synthesizer design. A graduate of Texas A&M, Stephen has lived his adult life in the Houston, TX, and Denver, CO, areas.
Stephen has never said no to a project. From building guitar amps (starting when he was 17) to designing and building his own CNC table to fine-tuning the mineral composition of the water he uses to brew beer, he thrives on testing, experimentation, and problem-solving. Tune into the podcast to learn more about the wacky stuff Stephen gets up to.
Special thanks to whixr over at Tymkrs for the intro and outro!
Related Podcasts
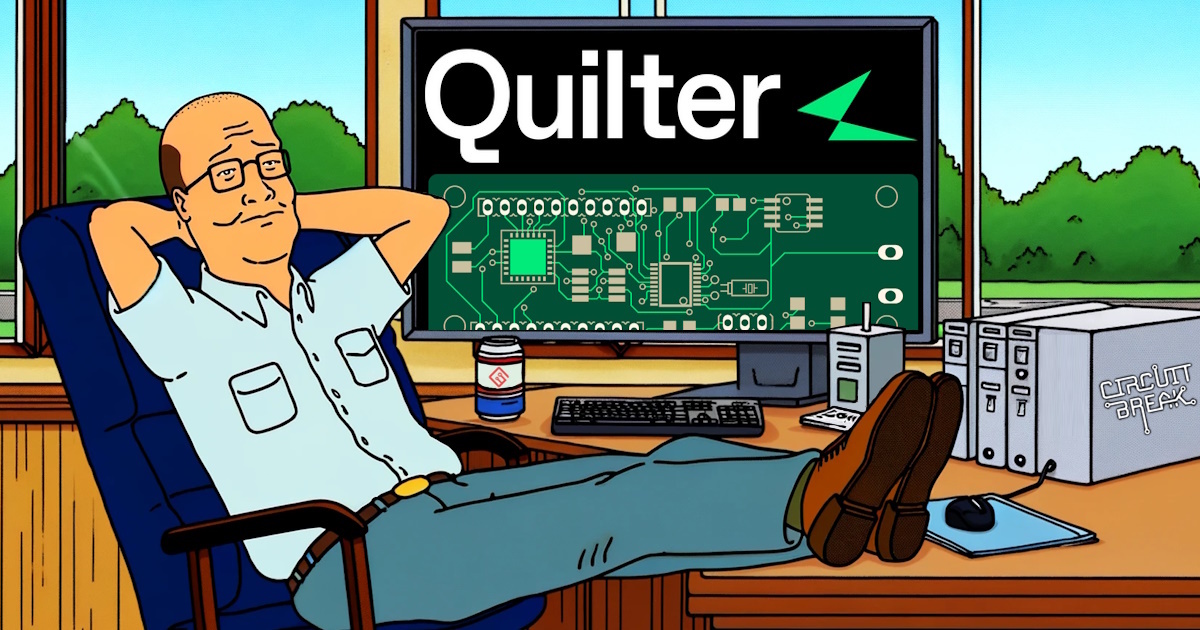
Tracing a Path for PCB Design Automation with Sergiy Nesterenko
Sergiy Nestorenko, founder of Quilter and former SpaceX engineer, discusses revolutionizing PCB design automation.
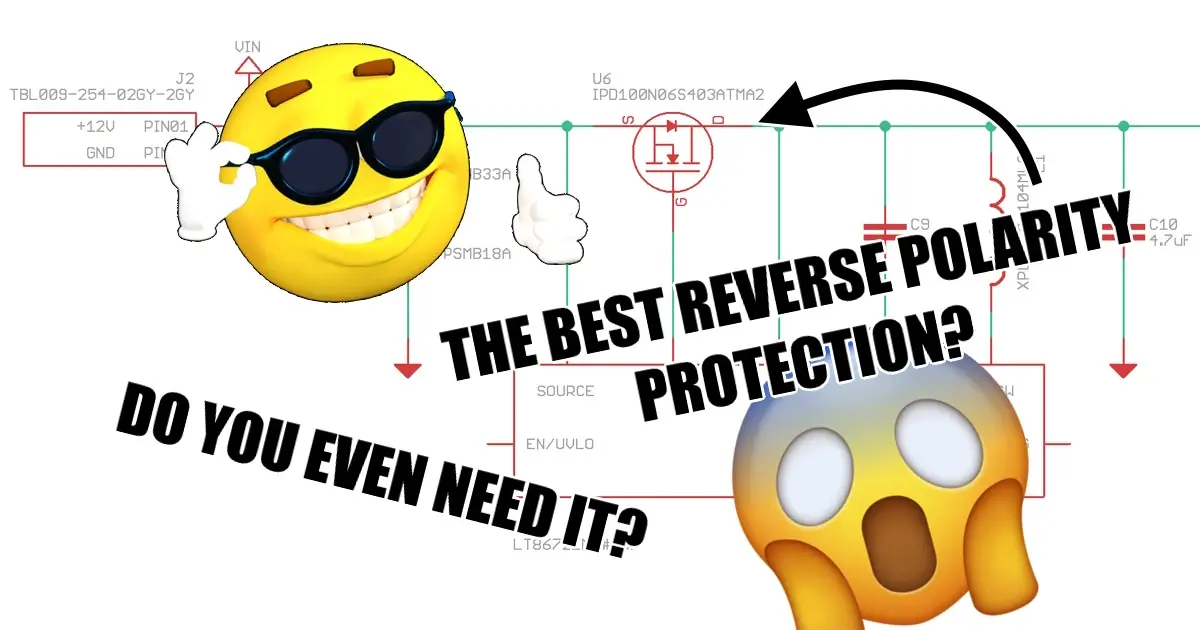
GPUs D.O.A, Reverse Polarity Problems, A 3D Printer Pickle
Dead on Arrival for high end GPUs. Why do so many consumer electronics not have reverse polarity protection?
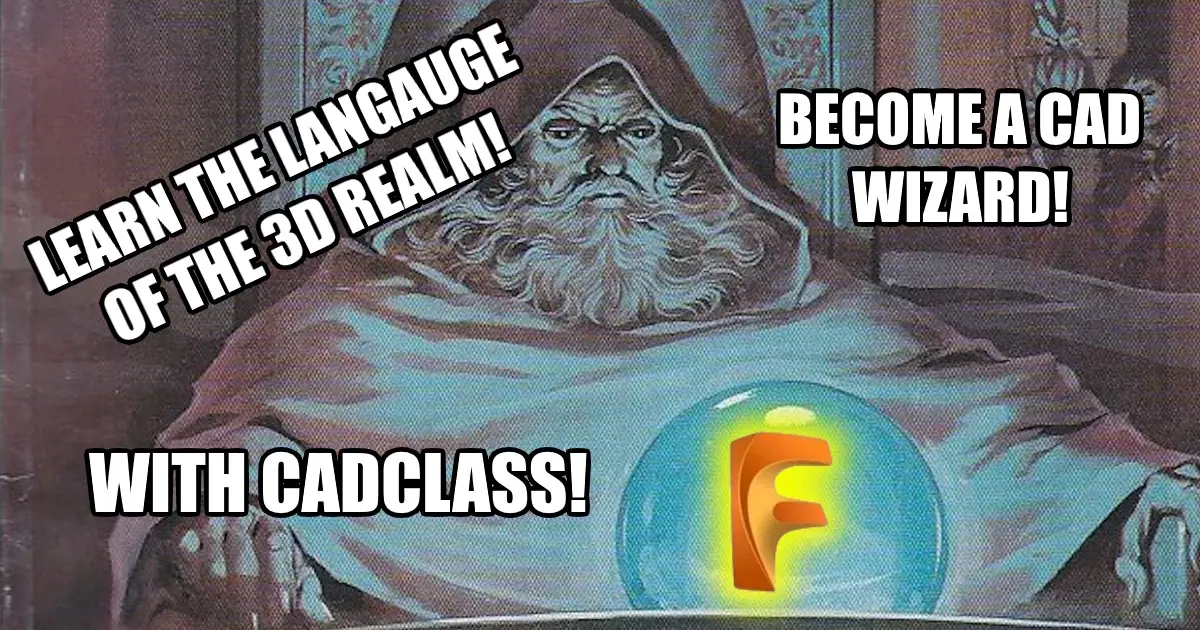
The aCADemy of Education - Joshua Manley of CADClass.org
This week, Josh Manley, Co-Owner & CEO of CADClass.org, shares their expertise in software and design education.
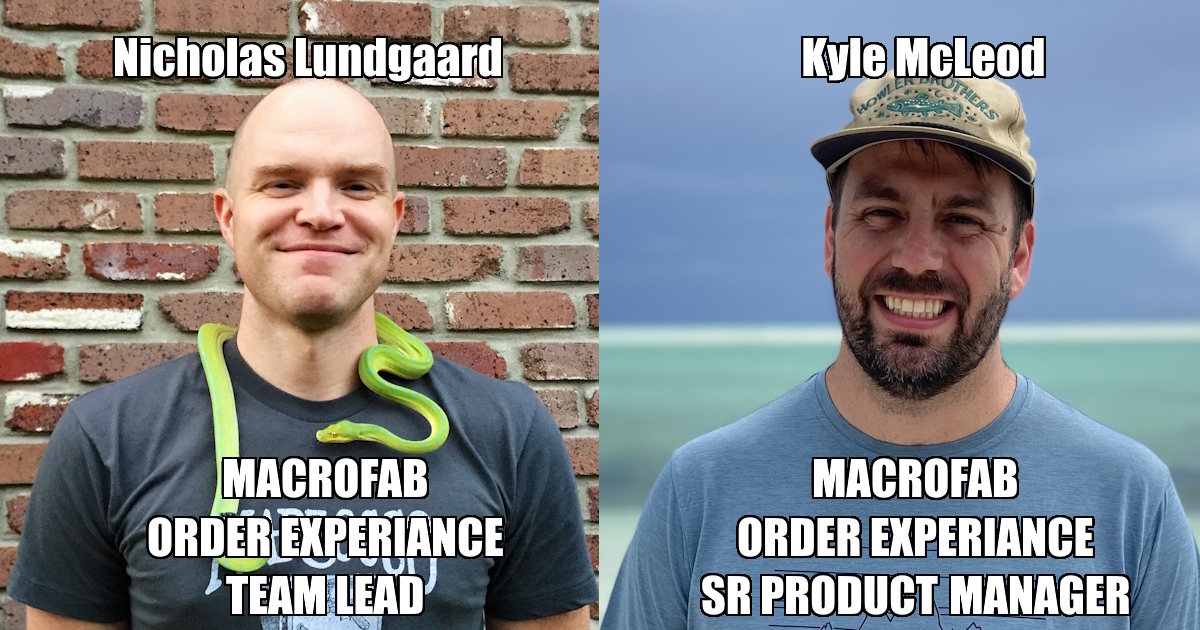
Platform Updates from Kyle McLeod and Nicholas Lundgaard
The episode provides insights into MacroFab's efforts to make PCB manufacturing more accessible and efficient for their customers.
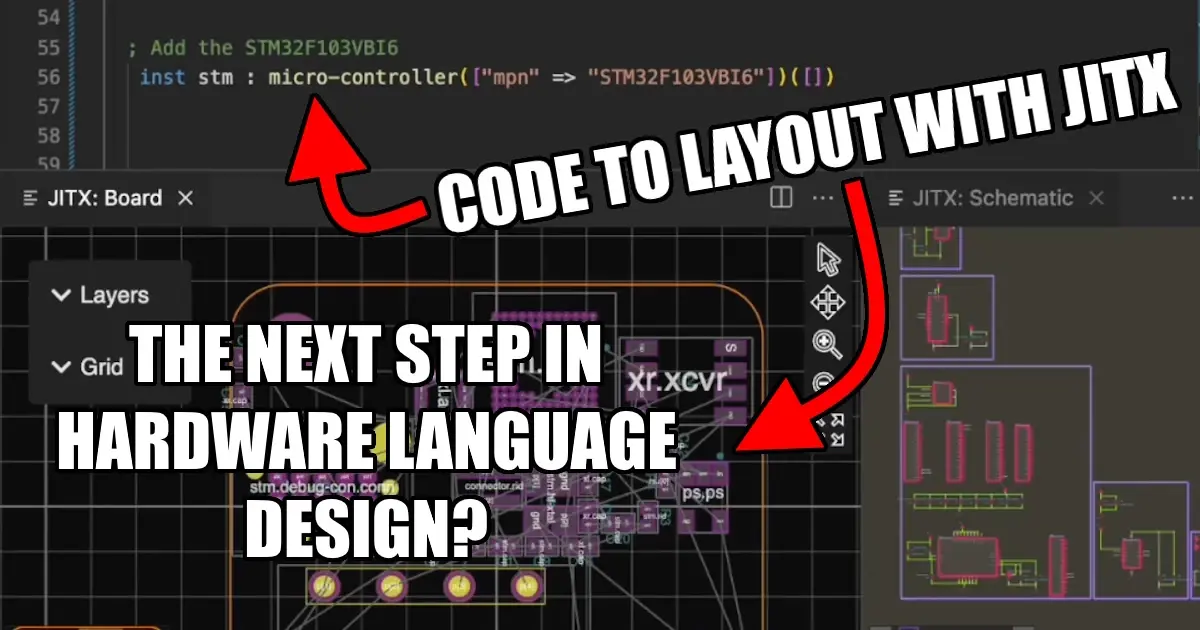
Dr. Duncan Haldane from JITX on Automating Circuit Design
Dr. Haldane on his background, the problems JITX is trying to resolve, & new auto-router plans. What's the deal with the "hyper-aggressive pogo-stick"?
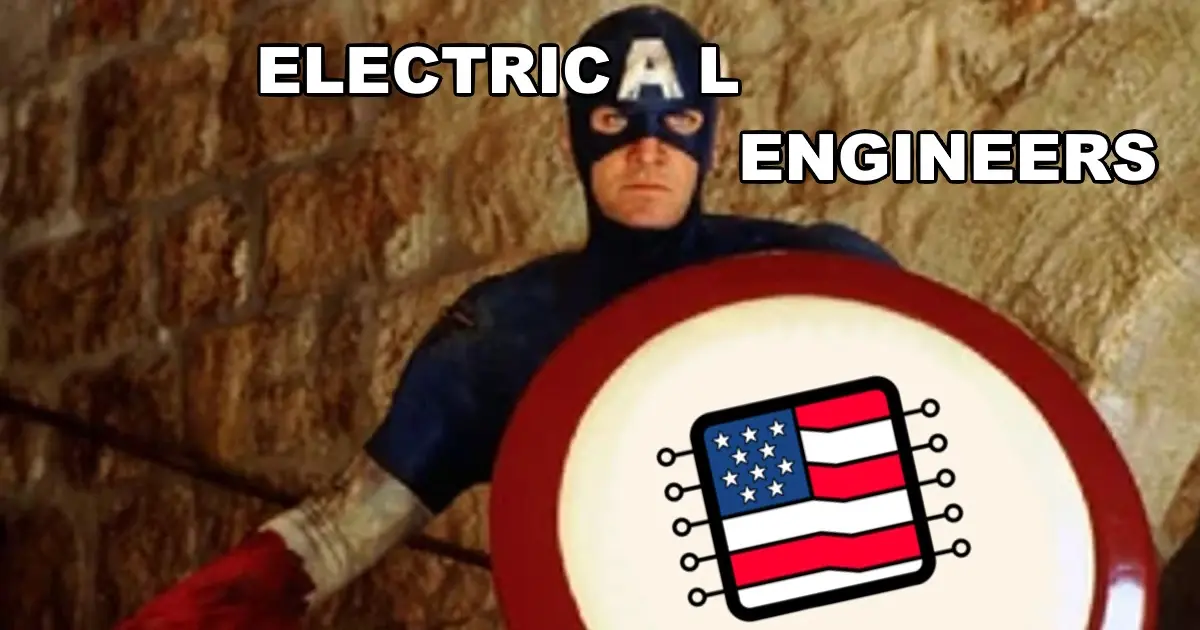
Guard the CHIPS, New Math for Double E’s
Community feedback that led Parker to order a Bambu X1 Carbon 3D Printer, arriving any day now, S to the L to the A, “guardrails” that the U.S.
About MacroFab
MacroFab offers comprehensive manufacturing solutions, from your smallest prototyping orders to your largest production needs. Our factory network locations are strategically located across North America, ensuring that we have the flexibility to provide capacity when and where you need it most.
Experience the future of EMS manufacturing with our state-of-the-art technology platform and cutting-edge digital supply chain solutions. At MacroFab, we ensure that your electronics are produced faster, more efficiently, and with fewer logistic problems than ever before.
Take advantage of AI-enabled sourcing opportunities and employ expert teams who are connected through a user-friendly technology platform. Discover how streamlined electronics manufacturing can benefit your business by contacting us today.