Related Topics
Solder Slugs
We'll dive into nuances of working with contract manufacturers, specifically focusing on the responsibilities of both the designer and the manufacturer.
Platform Updates from Kyle McLeod and Nicholas Lundgaard
The episode provides insights into MacroFab's efforts to make PCB manufacturing more accessible and efficient for their customers.
Other Resources
Circuit Break Podcast
Webinars
Videos
Tour MacroFab's ITAR-Compliant Facility
August 18, 2021, Episode #290
BGA vs. QFP – PCBA cost comparison
- Inspired by Tim Jager on the slack channel
- 48 pin QFP vs 56 pin BGA
- Escaping the package
- Layer count
- Increase in PCB tolerances
- Blind and buried vias required?
- Inspection costs
- Leaded packages like QFPs can easily be optically inspected
- BGAs typically require X-ray
- Tooling
- BGAs typically require small paste apertures and might require more expensive coatings and stencils
- Depending on lead spacing you may not need a stencil at your CM for a QFP
Using the MF platform to predict pricing
- Napkin math your PCB assembly cost the “easy” way
- Come up with a rough Bill of Materials
- Draw up a quick board outline that might be the size you require
- Enclosures dictate PCB sizes more often then not
- Upload to the platform
- Can change the bill of materials on the fly to make pricing considerations at prototype to high volume
- Ways to control pricing on your PCB Assembly
About the Hosts
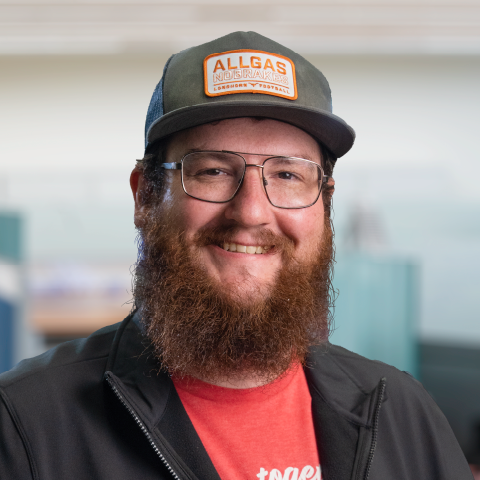
Parker Dillmann
Parker is an Electrical Engineer with backgrounds in Embedded System Design and Digital Signal Processing. He got his start in 2005 by hacking Nintendo consoles into portable gaming units. The following year he designed and produced an Atari 2600 video mod to allow the Atari to display a crisp, RF fuzz free picture on newer TVs. Over a thousand Atari video mods where produced by Parker from 2006 to 2011 and the mod is still made by other enthusiasts in the Atari community.
In 2006, Parker enrolled at The University of Texas at Austin as a Petroleum Engineer. After realizing electronics was his passion he switched majors in 2007 to Electrical and Computer Engineering. Following his previous background in making the Atari 2600 video mod, Parker decided to take more board layout classes and circuit design classes. Other areas of study include robotics, microcontroller theory and design, FPGA development with VHDL and Verilog, and image and signal processing with DSPs. In 2010, Parker won a Ti sponsored Launchpad programming and design contest that was held by the IEEE CS chapter at the University. Parker graduated with a BS in Electrical and Computer Engineering in the Spring of 2012.
In the Summer of 2012, Parker was hired on as an Electrical Engineer at Dynamic Perception to design and prototype new electronic products. Here, Parker learned about full product development cycles and honed his board layout skills. Seeing the difficulties in managing operations and FCC/CE compliance testing, Parker thought there had to be a better way for small electronic companies to get their product out in customer's hands.
Parker also runs the blog, longhornengineer.com, where he posts his personal projects, technical guides, and appnotes about board layout design and components.
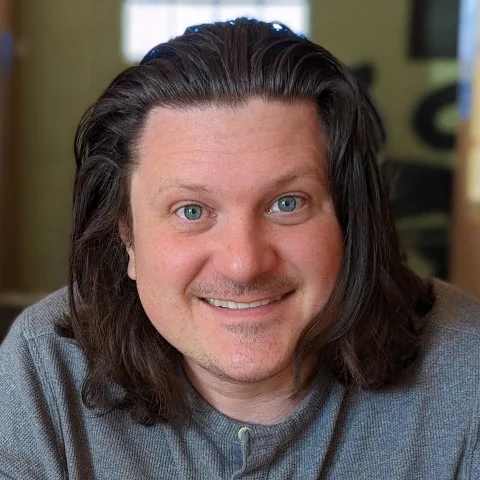
Stephen Kraig
Stephen Kraig is a component engineer working in the aerospace industry. He has applied his electrical engineering knowledge in a variety of contexts previously, including oil and gas, contract manufacturing, audio electronic repair, and synthesizer design. A graduate of Texas A&M, Stephen has lived his adult life in the Houston, TX, and Denver, CO, areas.
Stephen has never said no to a project. From building guitar amps (starting when he was 17) to designing and building his own CNC table to fine-tuning the mineral composition of the water he uses to brew beer, he thrives on testing, experimentation, and problem-solving. Tune into the podcast to learn more about the wacky stuff Stephen gets up to.
Special thanks to whixr over at Tymkrs for the intro and outro!
Related Podcasts
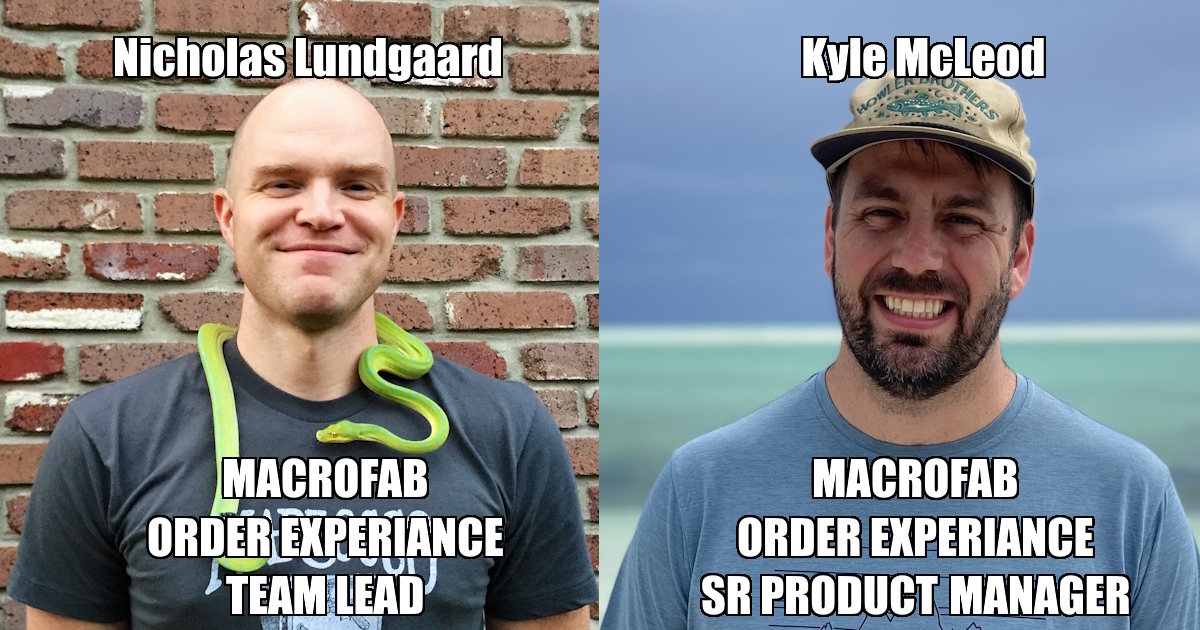
Platform Updates from Kyle McLeod and Nicholas Lundgaard
The episode provides insights into MacroFab's efforts to make PCB manufacturing more accessible and efficient for their customers.
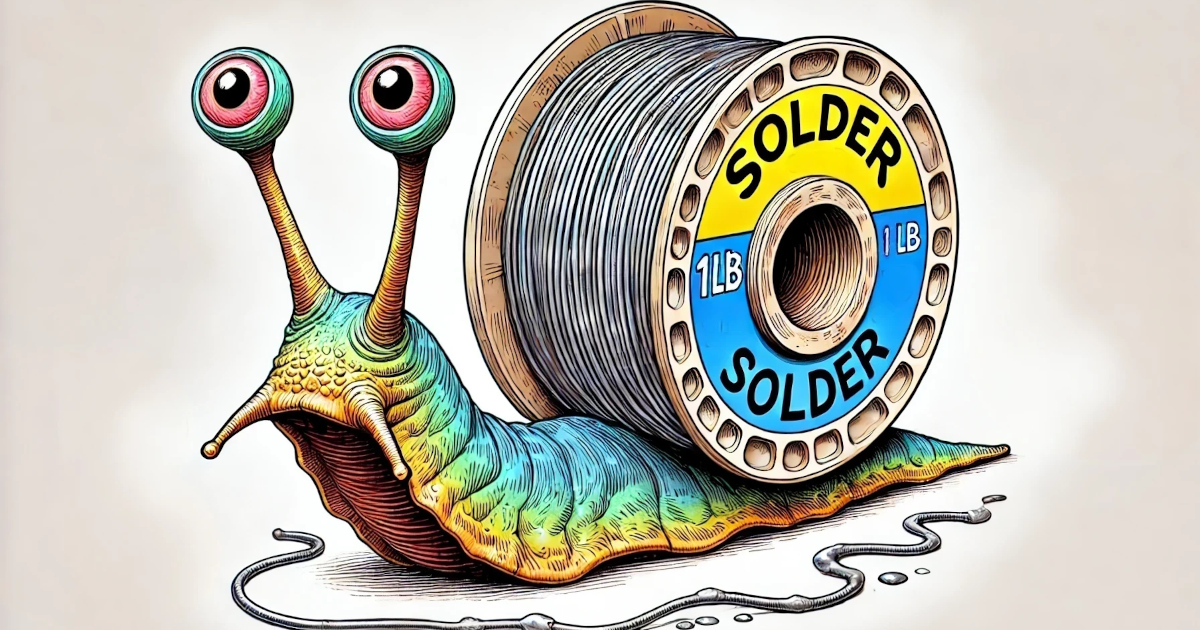
Solder Slugs
We'll dive into nuances of working with contract manufacturers, specifically focusing on the responsibilities of both the designer and the manufacturer.
About MacroFab
MacroFab offers comprehensive manufacturing solutions, from your smallest prototyping orders to your largest production needs. Our factory network locations are strategically located across North America, ensuring that we have the flexibility to provide capacity when and where you need it most.
Experience the future of EMS manufacturing with our state-of-the-art technology platform and cutting-edge digital supply chain solutions. At MacroFab, we ensure that your electronics are produced faster, more efficiently, and with fewer logistic problems than ever before.
Take advantage of AI-enabled sourcing opportunities and employ expert teams who are connected through a user-friendly technology platform. Discover how streamlined electronics manufacturing can benefit your business by contacting us today.