Circuit Break Podcast #194
Adult Supervision Not Required – Tilt 5 With Jeri
Related Topics
Top Features to Add to Your Next Prototype
Tune in as we share insights, anecdotes, and maybe a few confessions from our own prototyping adventures.
Magical Semiconductors of Pixies
We’re joined by Alexander Vartanov, an electrical engineering student with a knack for hands-on projects.
Injection Molded Enclosure Design with John Teel
John Teel of Predictable Designs returns to the podcast to discuss designing for Injection Molded Enclosures for MFG.
Other Resources
Circuit Break Podcast
Webinars
Videos
Tour MacroFab's ITAR-Compliant Facility
October 16, 2019, Episode #194
Episode 200 is Coming Up!
- Question / Answer setup like Episode 100
- Send them via Audio Format to podcast@macrofab.com
- Self-taught electrical engineer and entrepreneur with over 20 plus years experience designing and building mass market consumer electronics
- Assembled the initial hardware R&D team for the Valve Software and was a key contributor to the technology used in the popular HTC Vive
- While at Valve, she began work on the AR technology that would later become the basis for the technology behind Tilt Five, where Jeri serves as CEO and Co-Founder
Topics
- What is Tilt Five?
- Kickstarter Campaign
- How does it function?
- The Industrial design behind the project?
- How important was getting the weight to < 90 grams?
- How did you do it?
- You have brought lots of products to consumer markets:
- Prototyping your “finalized” product or first article
- Parts with High NRE fees like Injection molding
- Electronics
- Selecting and sourcing the projectors?
- Retro reflective material for the game mat
- How long is the typical timeline for development?
- What is something people don’t think about when they start designing a product?
- War Stories
- Prototyping your “finalized” product or first article
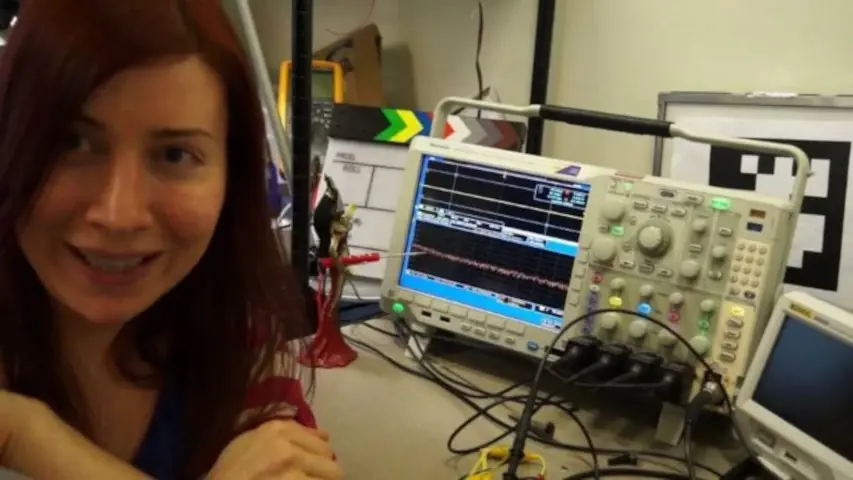
Jeri debugging some hardware with her oscilloscope.
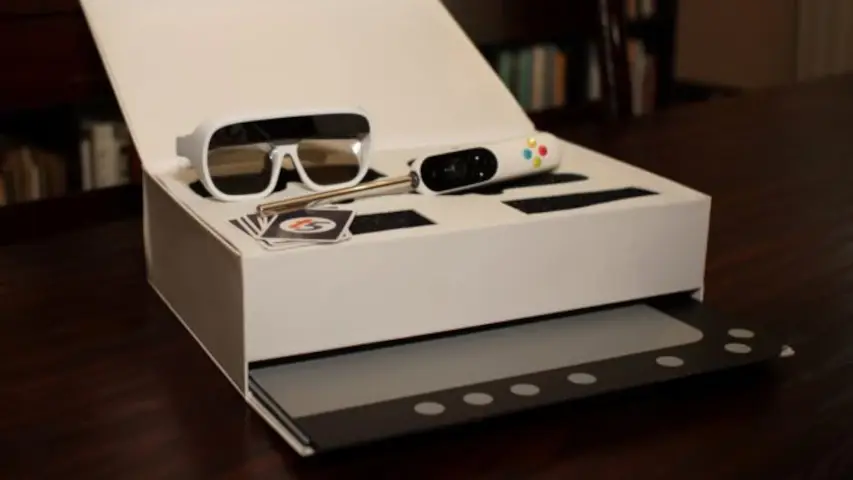
Tilt Fives’s Augmented Reality gaming set.
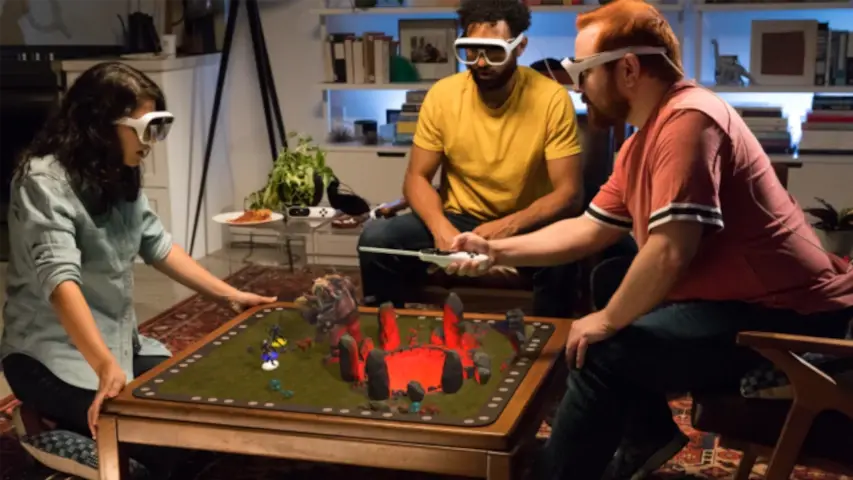
Reminds me of the holo chess from Star Wars!
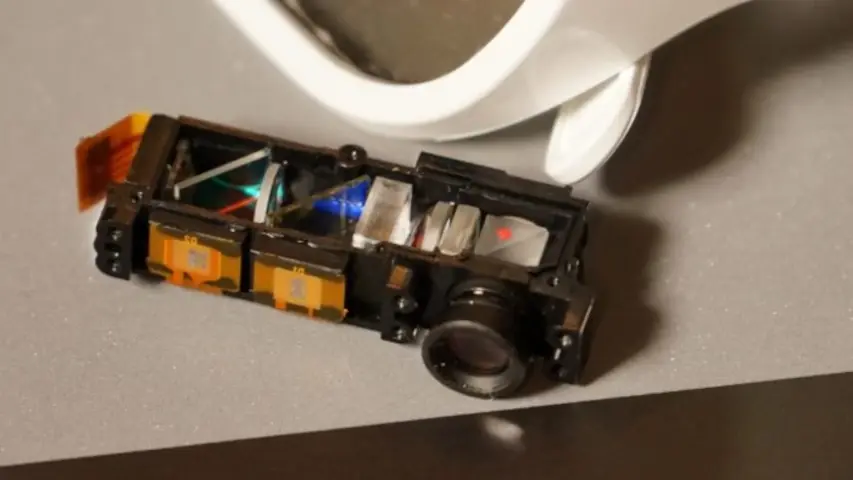
The projectors inside the Tilt Five glasses that enable the image to appear on the retro reflective material.
About the Hosts
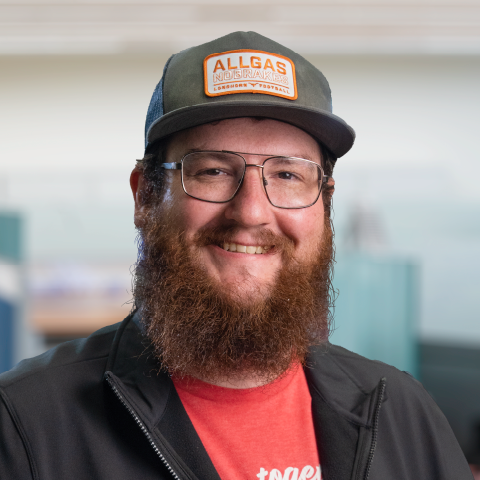
Parker Dillmann
Parker is an Electrical Engineer with backgrounds in Embedded System Design and Digital Signal Processing. He got his start in 2005 by hacking Nintendo consoles into portable gaming units. The following year he designed and produced an Atari 2600 video mod to allow the Atari to display a crisp, RF fuzz free picture on newer TVs. Over a thousand Atari video mods where produced by Parker from 2006 to 2011 and the mod is still made by other enthusiasts in the Atari community.
In 2006, Parker enrolled at The University of Texas at Austin as a Petroleum Engineer. After realizing electronics was his passion he switched majors in 2007 to Electrical and Computer Engineering. Following his previous background in making the Atari 2600 video mod, Parker decided to take more board layout classes and circuit design classes. Other areas of study include robotics, microcontroller theory and design, FPGA development with VHDL and Verilog, and image and signal processing with DSPs. In 2010, Parker won a Ti sponsored Launchpad programming and design contest that was held by the IEEE CS chapter at the University. Parker graduated with a BS in Electrical and Computer Engineering in the Spring of 2012.
In the Summer of 2012, Parker was hired on as an Electrical Engineer at Dynamic Perception to design and prototype new electronic products. Here, Parker learned about full product development cycles and honed his board layout skills. Seeing the difficulties in managing operations and FCC/CE compliance testing, Parker thought there had to be a better way for small electronic companies to get their product out in customer's hands.
Parker also runs the blog, longhornengineer.com, where he posts his personal projects, technical guides, and appnotes about board layout design and components.
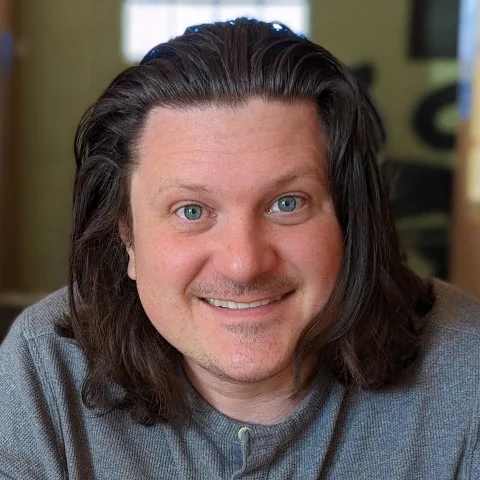
Stephen Kraig
Stephen Kraig is a component engineer working in the aerospace industry. He has applied his electrical engineering knowledge in a variety of contexts previously, including oil and gas, contract manufacturing, audio electronic repair, and synthesizer design. A graduate of Texas A&M, Stephen has lived his adult life in the Houston, TX, and Denver, CO, areas.
Stephen has never said no to a project. From building guitar amps (starting when he was 17) to designing and building his own CNC table to fine-tuning the mineral composition of the water he uses to brew beer, he thrives on testing, experimentation, and problem-solving. Tune into the podcast to learn more about the wacky stuff Stephen gets up to.
Special thanks to whixr over at Tymkrs for the intro and outro!
Related Podcasts
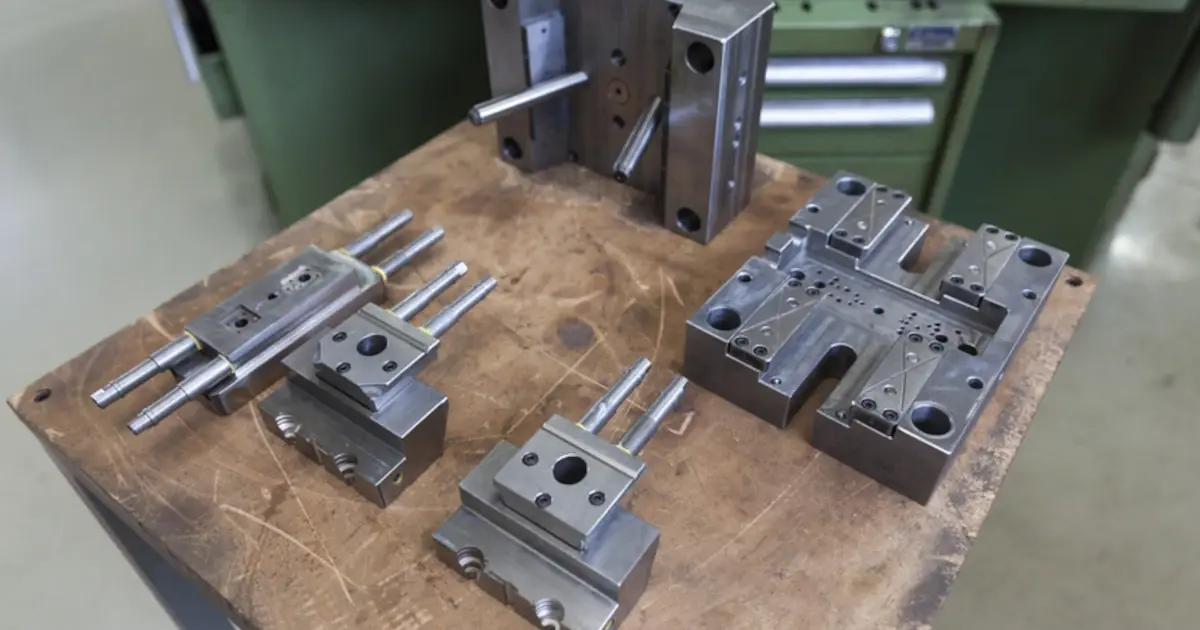
Injection Molded Enclosure Design with John Teel
John Teel of Predictable Designs returns to the podcast to discuss designing for Injection Molded Enclosures for MFG.
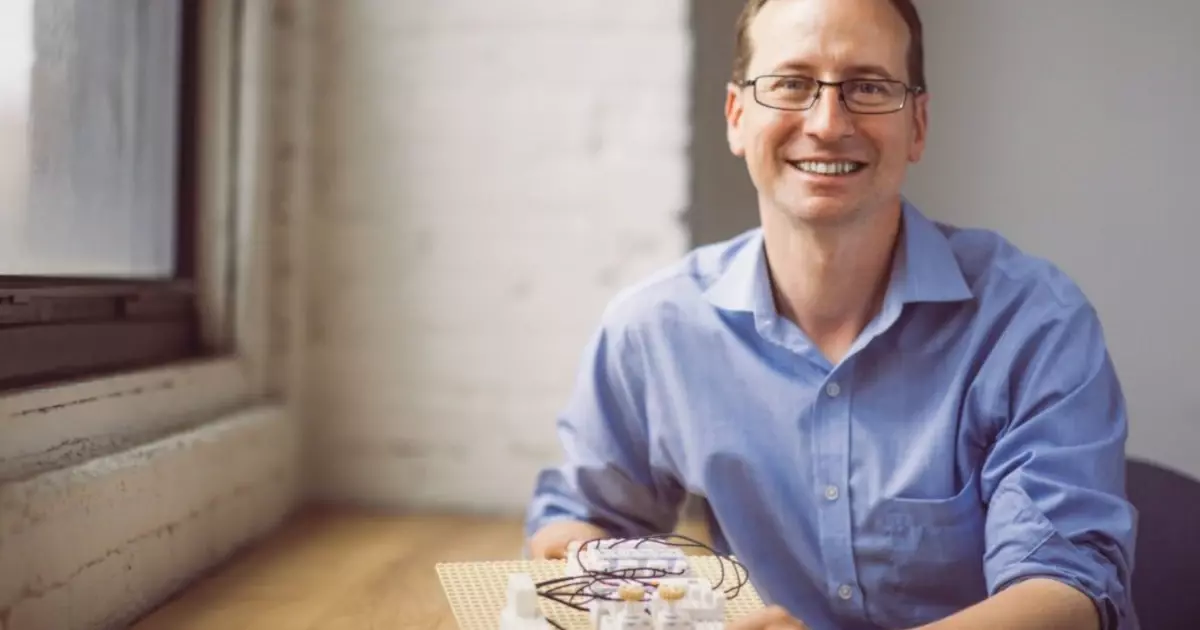
The Brick That Shall Not Be Named: A Joe Broms Story
Guest Joseph Broms talks about his experience in prototyping and designing his product ProtoBricks.
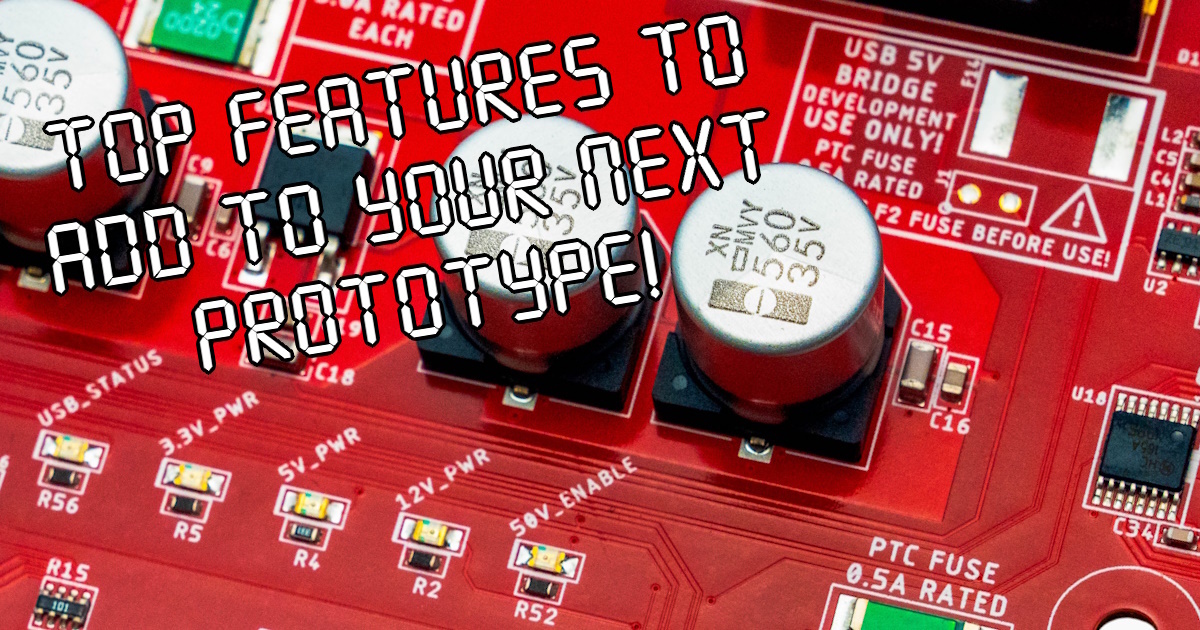
Top Features to Add to Your Next Prototype
Tune in as we share insights, anecdotes, and maybe a few confessions from our own prototyping adventures.
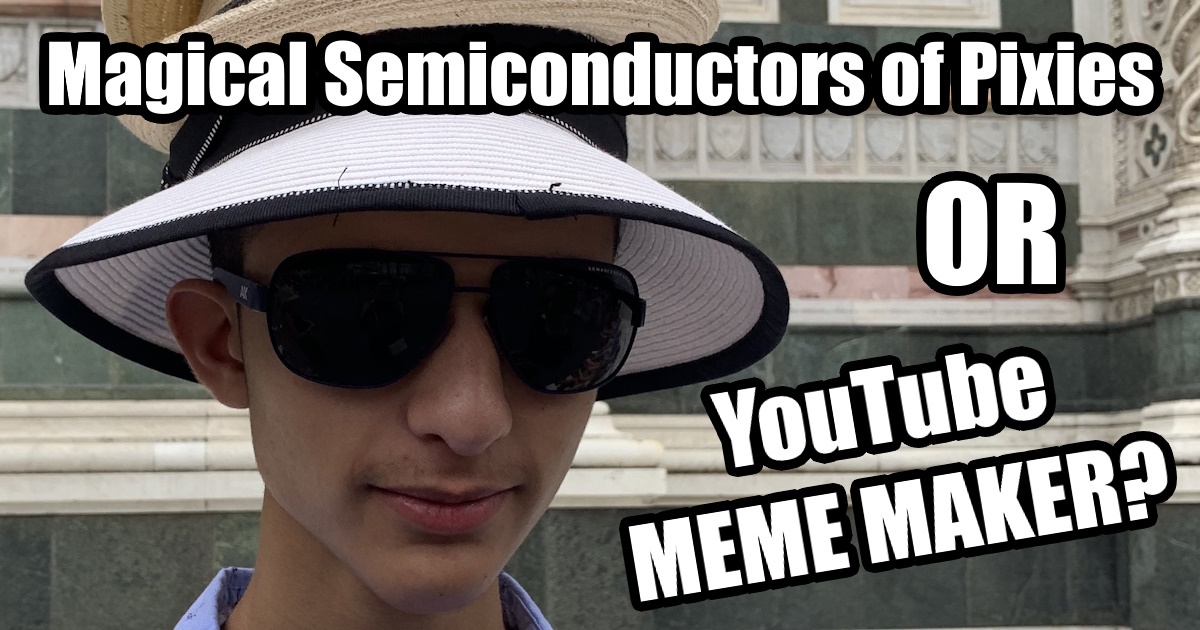
Magical Semiconductors of Pixies
We’re joined by Alexander Vartanov, an electrical engineering student with a knack for hands-on projects.
About MacroFab
MacroFab offers comprehensive manufacturing solutions, from your smallest prototyping orders to your largest production needs. Our factory network locations are strategically located across North America, ensuring that we have the flexibility to provide capacity when and where you need it most.
Experience the future of EMS manufacturing with our state-of-the-art technology platform and cutting-edge digital supply chain solutions. At MacroFab, we ensure that your electronics are produced faster, more efficiently, and with fewer logistic problems than ever before.
Take advantage of AI-enabled sourcing opportunities and employ expert teams who are connected through a user-friendly technology platform. Discover how streamlined electronics manufacturing can benefit your business by contacting us today.