Project Background
MacroFab helped Somewear Labs understand and evaluate costs between two design options so they could quickly make the right business decision for their product launch.
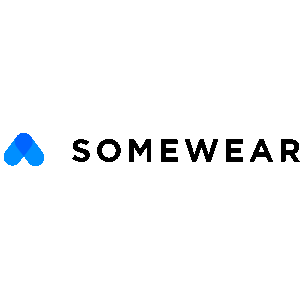
Get to Know the Work
Somewear Labs develops modern satellite communication tools. The Somewear Global Hotspot turns your phone into a satellite phone, so you always have reliable communication no matter where you are. It allows you to send and receive text messages; download weather reports; share your location and in case of emergency and has an onboard SOS button.
Assessment
As Somewear Labs was finalizing their initial prototype and getting ready to move into production, they realized that they had an opportunity to improve the antenna performance which meant a totally new via design in their PCB. Not only did this discovery happen pretty late in the prototyping process, but they realized their new design was going to result in a big cost difference, not to mention delays in getting their product to market.
Challenge
The Somewear Labs team discovered that the new circuit boards were going to cost 2x-3x more than what their original design needed and they didn’t know of a PCB fabrication shop that could manufacture the new boards. Somewear Labs needed to vet the quality and capabilities of a new PCB fabrication shop, they needed to reconcile the cost difference and they also needed to determine if going with the new design was the best decision, moving forward.
Process
MacroFab’s manufacturing expertise with multi-layer, high-density PCB assembly allowed Somewear Labs to ensure their design went through a review process identifying issues like size constraints, signal integrity and via routing. Because MacroFab has a large network of suppliers, we were able to source a highly reliable PCB fabrication facility that we knew would be able to handle the unique requirements of their new design. As MacroFab and Somewear Labs moved towards a finalized design, the next challenge was assuring high quality and low manufacturing cost at scale.
Alan Besquin, Co-Founder and CTO
Somewear Labs
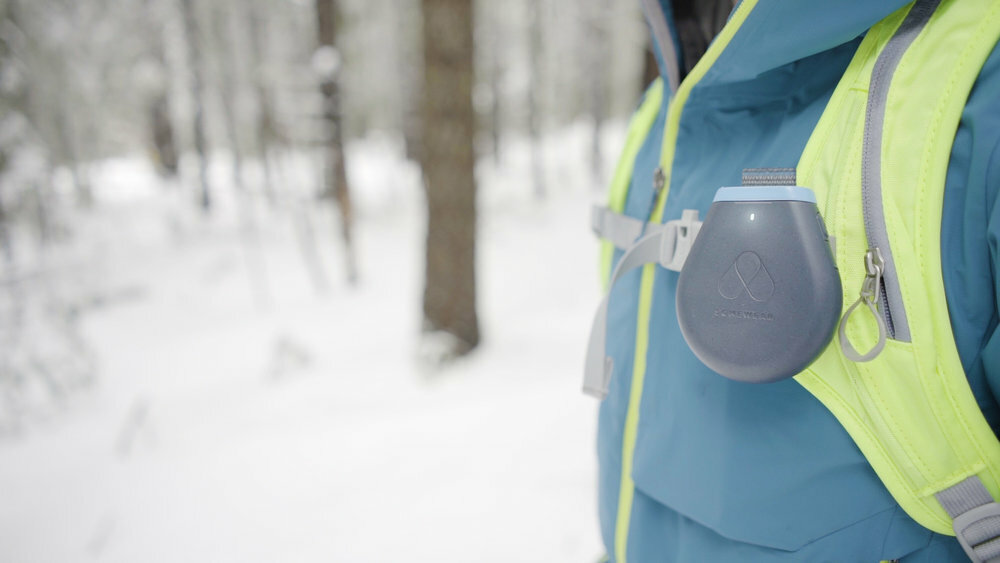
Our Solution
Both MacroFab’s team and platform helped Somewear Labs to make important business decisions and keep their files organized when redesigning their boards, respectively. The two teams worked together on cost optimization analysis and were able to determine that moving to the new design was best to move forward rather than making post-manufacturing modifications on the first design.
As Somewear Labs was going through design changes and iterations, they found that uploading and easily organizing their design files on MacroFab’s platform was extremely helpful. They were able to create labels for each design, which reduced confusion and made it much easier to keep quotes separated, rather than sending and receiving emails with different design versions, which commonly happens with traditional manufacturers.
The Somewear Labs product is designed for all-weather environments, which required managing a complex BOM with several parts reaching End of Life and a number of mechanical components with price escalations due to materials shortages and tariffs. To solve the cost challenges, the MacroFab supply chain team identified best suppliers to meet the price targets and secured long term volume commitments, allowing Somewear Labs to ultimately lower overall costs and improve unit economics.
A significant portion of the savings will ultimately come from an improved assembly process. Using MacroFab’s Factory Portability, Somewear Labs was able to structure a production process that centered on US factories during earlier stages of production, seamlessly moving to a lower-cost manufacturing region in Mexico at high scale. The agility of US factories and the ability of the MacroFab manufacturing engineering team to improve the assembly process is an essential step on the way to high-volume production – a process that typically takes multiple rounds of supplier selection and several New Product Introduction (NPI) process as production moved between factories. Working with MacroFab as a manufacturing platform, Somewear Labs will save significant time and effort to achieve their at-scale objectives, giving them an edge on the competition.
Alan Besquin, Co-Founder and CTO
Somewear Labs
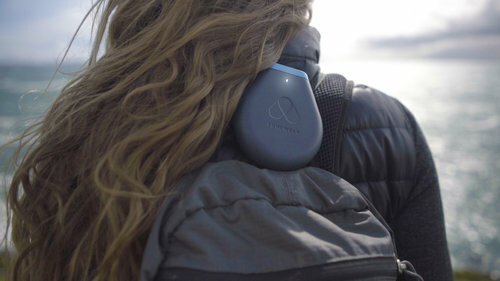
Summary
The decision to go with the new PCB design improved their product quality immensely, and even though it delayed their timeline, ultimately, it was the right decision. It was worthwhile to have a design that they fully trusted and gave Somewear Labs the best results from a product performance standpoint at the crucial launch stage.
Because MacroFab built a relationship with Somewear Labs early on in the prototyping process, it meant that we were familiar with their product and could help them evolve it and source the right partners to help them have the most successful launch possible.
For Somewear Labs, the biggest benefits of working with MacroFab have been a direct line of communication, dedicated Account Management services, and the ability to work 100% within North America while achieving their low-cost manufacturing objectives. Somewear Labs engineers and purchasing managers can talk to anyone on our team that is directly working on their product, making it easy to get the answers they need.