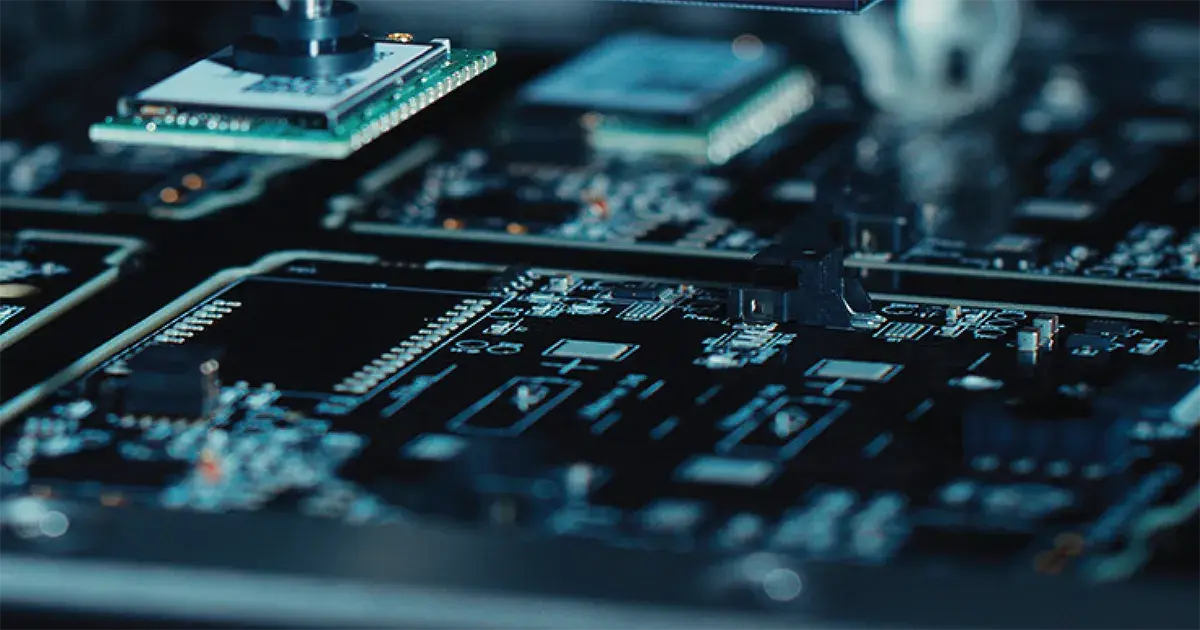
MacroFab Blog
Understanding and Implementing Mil-Spec Standards in PCB Assemblies
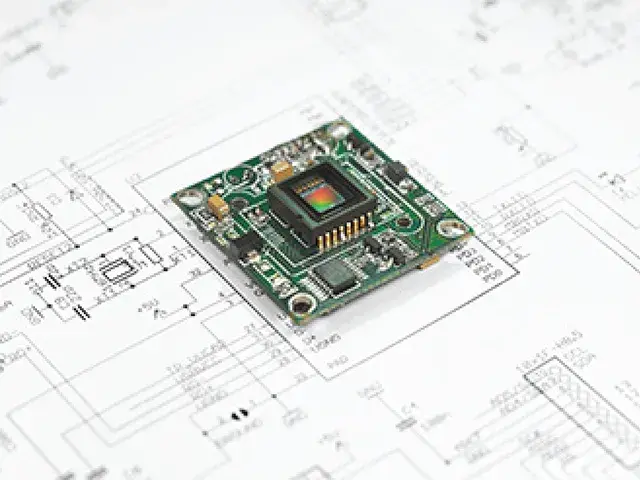
Mil-Spec, an abbreviation for ‘military specification’’ or military spec, outlines the rigorous standards the U.S. Department of Defense (DoD) sets to describe the physical and functional requirements for products and systems it purchases. The term mil-spec simply means that something has met military standards. It is similar to mil-STD and can be used in the same way.
Within the realm of PCB assemblies, Mil-Spec denotes a certification, indicating that a PCB design has met the exacting requirements established by the military for quality, durability, and performance. PCBAs are thus guaranteed to meet defense specifications and hold up in harsh environments.
While Mil-Spec standards for PCBAs accommodate commercial PCBA manufacturing techniques, the primary objective remains uncompromised: ensuring PCBAs can withstand the demanding conditions of military operations.
This article will guide you through standards relevant to Mil-Spec PCB assemblies, compare the unique attributes of military-grade PCBAs with other PCB assembly classes, outline essential design principles for these high-performing boards, and highlight the critical testing areas required for Mil-Spec certifications.
Understanding Mil-Spec
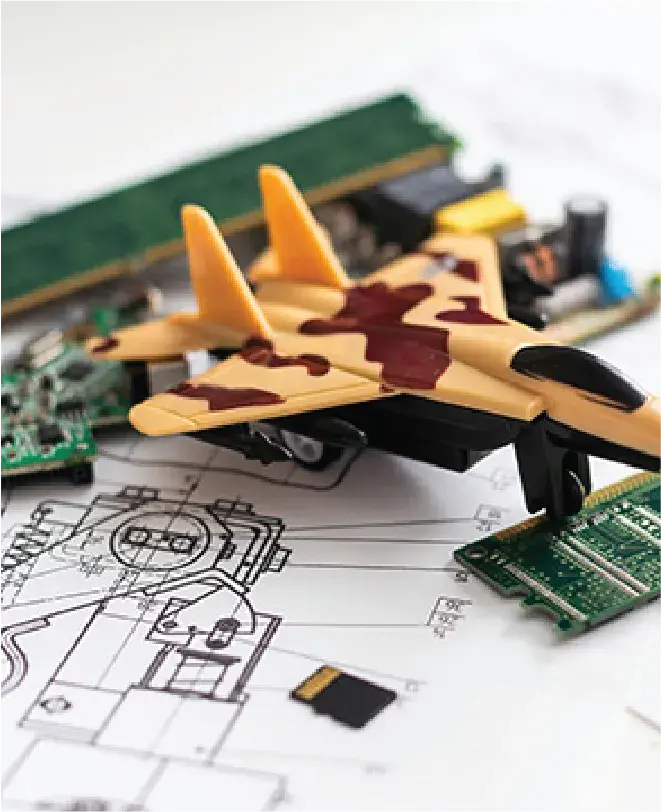
Mil-Specs are stringent standards pivotal to the U.S. defense procurement process, ensuring that every piece of military equipment, from fighter jets to printed circuit board assemblies, functions reliably under high-stakes conditions.
Mil-specs are standardized documents. Standardization ensures equipment from different manufacturers is interoperable, and that replacement parts are consistent and dependable. This is especially important given the global scope of military operations and the need for reliable, predictable tools in various environments.
Though initially developed for military applications, Mil-Spec components and assemblies are not unique to the military and may be used in other high-stakes industries such as aerospace and medicine. Many companies in these sectors now opt for using components from the Mil-Spec Qualified Product List (QPL) and also choose to work with certified manufacturers on the Mil-Spec Quality Manufacturer List (QML).
Military Specifications Applicable to PCBAs
Here, we delve into some of the most commonly cited Mil-specs for military-grade PCBs and what they entail:
Difference Between IPC Class 3 PCBs and Others
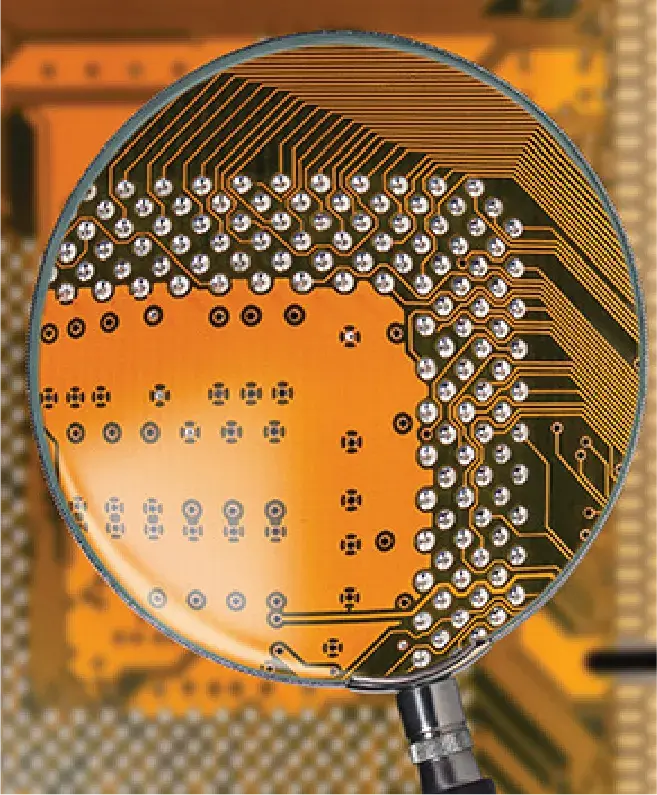
IPC—formerly known as the Institute of Printed Circuits—is a global trade association serving the printed board and electronics assembly industries. IPC classifies PCBs into three main categories based on their reliability and the quality assurance processes they must undergo:
IPC Class 1: Commercial Grade
IPC Class 1 is geared towards consumer electronics and products where cost is a significant factor. These PCBs undergo basic quality control tests and are designed for general use under standard conditions. They typically have a shorter lifespan and are
not built for high-stress environments.
IPC Class 2: Industrial Grade
If your project needs something more robust—maybe for industrial or some medical applications—you’ll be looking at IPC Class 2 PCBs. You get more extensive quality testing with these, and they’re built to last longer than Class 1.
IPC Class 3: Military Grade
If your application is mission-critical, like military or aerospace use, where a failure could be catastrophic, you’ll need IPC Class 3 PCBs. These are the best of the best. They undergo the most stringent quality tests and are engineered to work in the harshest, most demanding environments. They’re what you choose when reliability and performance can’t be compromised.
Prior to assembly, the bare board must meet or exceed the desired post-assembly class. To put it another way, you cannot create a Class 3 PCB assembly from a Class 2 board.
Quality processes, cleanliness standards, and defect reduction are all key to determining IPC assembly classes. To ensure they can withstand harsh conditions, Class 3 assemblies go through rigorous testing and inspection processes.
Discover the intrinsic benefits of working with an ITAR-registered and compliant manufacturer like MacroFab.
Key Design Considerations for Mil-Spec PCBAs
When designing or procuring PCBAs that comply with military specifications, there are a number of vital considerations to keep in mind:
- Ensure full compliance with relevant military specifications.
- Ensure trace widths and materials can handle high currents.
- Separate high-frequency and low-frequency components to minimize noise interference.
- Shield and isolate clock signals to prevent interference.
- Route traces at angles of 45° or less for better signal integrity.
- Incorporate heat sinks, thermal vias, and layouts that promote efficient heat dissipation due to possible drastic temperature shifts.
- Use protective coatings or encapsulation to shield against factors like moisture, salt spray, and chemicals.
- Mil-Spec PCBAs require the use of high-quality materials and components to ensure they can withstand extreme conditions such as high temperatures, moisture, and mechanical stress.
Testing Mil-Spec PCBAs
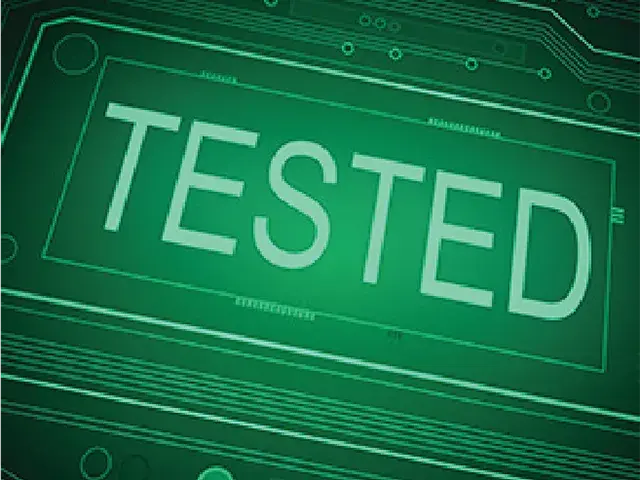
To ensure compliance with relevant requirements, military-grade PCBs undergo a battery of tests. Knowing these test areas can guide PCBA designers to focus on key aspects that are crucial for the assembly to meet military standards. The primary test areas are as follows:
Chemical Tests
Chemical tests ascertain the cleanliness and specific characteristics of the materials used, such as the plating. Under this, we have:
- Ionic Contamination: Assemblies are tested for levels of ionic contamination. For instance, the MIL-PRF-31032 requires that the ionic contamination must not exceed 1.56 micrograms/square centimeter prior to the application of a solder mask.
- Copper Plating Characteristics: Elongation and tensile strength of copper plating are tested and must meet minimum standards of the relevant MIL-Spec.
Physical Tests
Physical tests are conducted to evaluate the integrity of the PCBA in terms of adhesion and structural stability. Under this, we have:
- Adhesion Marking: Tests look for missing or smeared markings, any of which would constitute a failure.
- Adhesion, Plating: These tests ensure no part of the conductor pattern or copper plating is removed.
- Adhesion, Solder Mask: Criteria are set for the maximum percentage of solder mask that can lift from the board’s surface.
- Bow and Twist: The extent of any deformity in the printed boards is measured.
- Rework Simulation: This test ensures printed boards still meet specifications after simulated rework processes.
- Solderability: Boards requiring soldering during assembly processes are tested for solderability, depending on their design.
- Surface Peel Strength: It measures the peel strength of surface conductors, ensuring they meet specific standards.
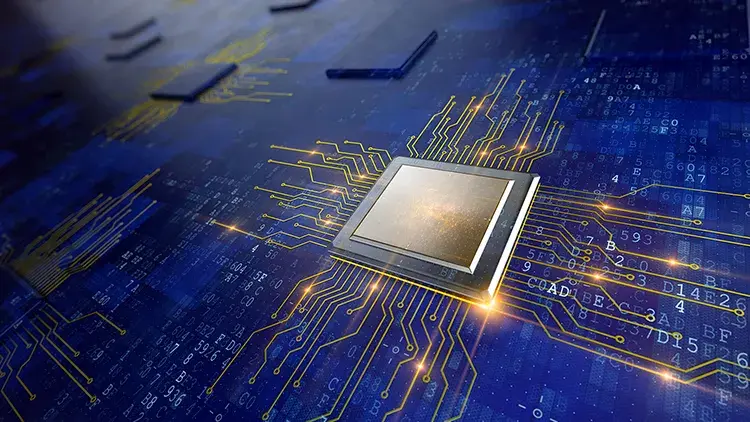
Electrical Tests
Electrical tests focus on ensuring proper conduction and insulation within the PCBA. Under this, we have:
- Continuity: Checks the resistance between end-points of conductor patterns, ensuring no resistance limits are exceeded.
- Isolation: Tests are conducted to measure insulation resistance between mutually isolated conductors
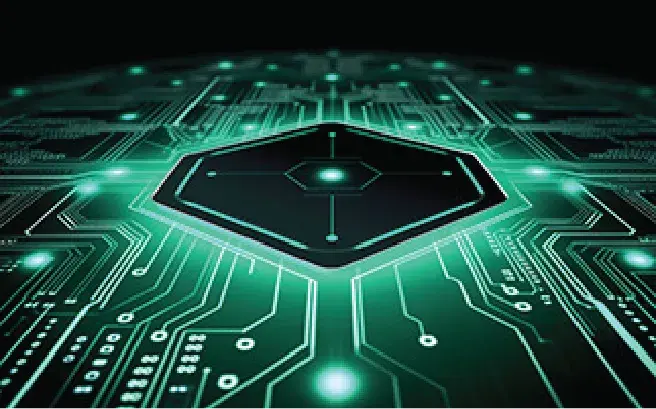
Environmental Test Methods
Environmental tests evaluate the PCBA’s resilience against environmental stressors like moisture and heat. Under this, we have:
- Moisture and Insulation Resistance: These tests demonstrate that PCBAs perform well under humid conditions.
- Resistance to Soldering Heat: These tests assess the board’s ability to withstand thermal stress during soldering processes
Conclusion
The design and manufacturing of military-grade PCBs demand strict adherence to a set of rigorous standards. These standards govern everything from the quality of materials used to the thermal management systems in place, and they serve to ensure the ultimate reliability and safety of electronic components in critical military applications.
Moreover, an understanding of the basic tests mandated by military specifications can significantly guide the design process.
As the landscape of technology evolves, staying up-to-date with MIL-Spec standards is vital to ensure ongoing excellence in both compliance and performance.
Related Topics
Cable Assemblies vs Wire Harnesses: Their Role in PCBA Box Builds
A discussion on cable assemblies and wire harnesses and their role in box builds.
Mapping Out a PCBA Supply Chain Strategy in Five Moves
Companies should create unique vendor relationships with numerous international suppliers due to the necessity of having to source components globally.
New Inventory Features Streamline Material Management at MacroFab
A display of some new features for the platform that enhances the the management of inventory and material at MacroFab.
Flexibility Matters. Get It With MacroFab.
Get a Quote TodayAbout MacroFab
MacroFab offers comprehensive manufacturing solutions, from your smallest prototyping orders to your largest production needs. Our factory network locations are strategically located across North America, ensuring that we have the flexibility to provide capacity when and where you need it most.
Experience the future of EMS manufacturing with our state-of-the-art technology platform and cutting-edge digital supply chain solutions. At MacroFab, we ensure that your electronics are produced faster, more efficiently, and with fewer logistic problems than ever before.
Take advantage of AI-enabled sourcing opportunities and employ expert teams who are connected through a user-friendly technology platform. Discover how streamlined electronics manufacturing can benefit your business by contacting us today.