MacroFab Blog
When you hear the word “drone,” you likely imagine an airborne device the size of a hat box that uses propellers to fly and is controlled remotely by someone in the immediate vicinity, perhaps in a park or another open area. Recreational drones like these have become increasingly popular in recent years.
But if you expand your definition of drones to include all unmanned aerial vehicles (UAVs), ranging from long-range drones used in military applications, to transport vehicles, to insect-sized drones, their potential applications expand exponentially. Imagine commercial airliners without pilots, drones capable of transporting shipping containers like those now delivered by trucks and ships, or even tiny, dexterous drones that fly into narrow gaps like insects.
While there are many obstacles for developers to overcome before these innovations can become a reality, the technology is evolving quickly – much faster than you might expect. This blog discusses where the technology currently stands and where it may go.
High-Capacity Drones: Autonomy and Engine Innovations
Scaling up drones to carry larger payloads, fly at higher altitudes, and travel greater distances presents major challenges for developers. Currently, semi- and fully autonomous large-scale drones (classified as UAVs that can carry a payload of greater than 1320 pounds and operate at altitudes greater than 18,000 feet) are most commonly implemented by military organizations to replace aircraft piloted by human operators.
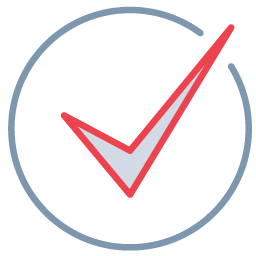
Checkpoint
Semi-autonomous features like the ability to return to their starting point unaided underscores the ongoing evolution and increasing sophistication of UAV technology.
Unlike smaller counterparts that rely on electric motors, larger drones use more robust internal combustion or jet engines. Not just a matter of size scaling, this means enhanced efficiency, reduced weight, and optimized fuel consumption, while also delivering precision control crucial in moving large loads.
By removing the human pilot and the various systems needed to support him, most large-scale drones are lighter and are usually built from lighter materials like plastics or carbon fibers. This increases the range of the vehicle. It can also reduce engine weight without compromising strength.
This is especially true for high-altitude long-endurance (HALE) drones. HALE drones must stay airborne for extended periods, sometimes days, at various altitudes and temperatures, and are often solar-powered. They are ideally suited for reconnaissance. In 2021, the U.S. Forest Service began testing HALE drones to locate and fight wildfires.
However, UAVs that operate at higher altitudes have more difficulty dissipating heat in the thinner atmosphere where they fly. Printed circuit boards for larger UAVs require additional heat transfer and use additional metal to connect to heat sinks to maximize performance at higher altitudes. This must be taken into consideration at the design stage. Simulating heat generation, flow, and dissipation in the development process is a valuable tool for these types of designs.
In terms of operational control, remotely piloted ICE (internal combustion engine) or jet aircraft aren’t significantly different from their traditional onboard piloted counterparts. A human operator guides the drone from a station with controls and monitors that are similar to the ones in airplane cockpits while cameras and radar-based imaging systems provide the visuals.
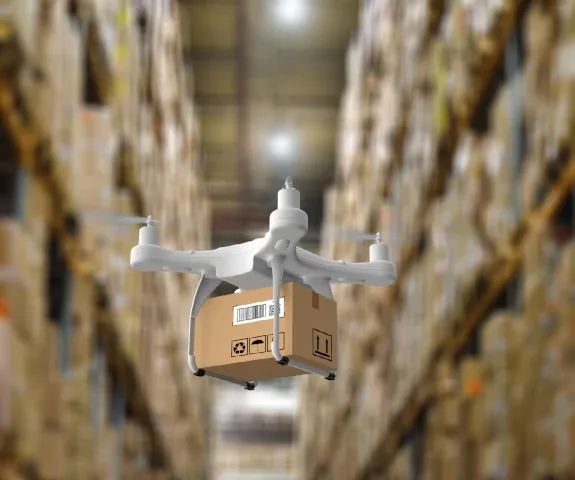
“Flying cars,” or “air taxis,” are already a reality, with China approving the first self-driving air taxi late in 2023. Similar air taxis are being planned in the USA, though they will initially require a pilot on board for safety.
However, a significant hurdle in designing UAVs for human transportation or valuable cargo lies in bridging the information gap. While current sensors can track weather conditions, altitude, and airspeed, they cannot do so with the speed and sensitivity necessary. Onboard pilots can sense subtle changes in an aircraft’s behavior intuitively, a nuance challenging to replicate with sensors. By 2030, 6G wireless networks should significantly alleviate this issue by enabling ultra-low latency and improved data reliability, enhancing sensor responsiveness.
Lastly, many UAVs today boast semi-autonomous features like the ability to return to their starting point unaided. Autonomous or semi-autonomous flight software must be capable of dynamically adjusting flight paths in response to changing conditions, akin to how commercial airline pilots maneuver to avoid turbulence. This capability underscores the ongoing evolution and increasing sophistication of UAV technology in adapting to complex operational environments.
Compact Drone Engineering: Revolutionizing Small-Scale UAVs
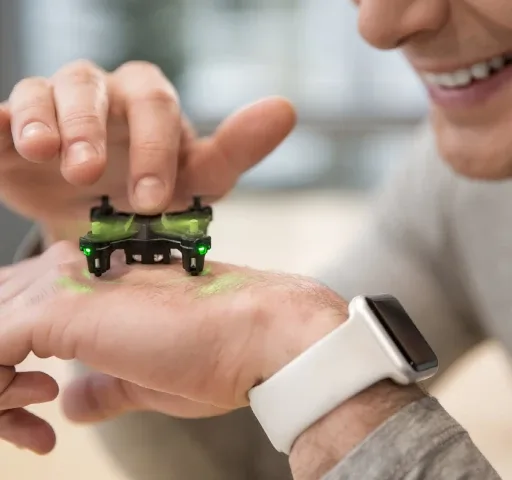
Every drone, from super large to shoe-box sized, relies on motors or engines to propel itself. In contrast to making drones larger, which requires increasing their power while reducing their overall weight, making them smaller necessitates removing motors altogether.
Using actuators to mimic how an insect flaps its wings plays a role in “micro drone” design. Early versions of this technology used ceramic materials to conduct and store electricity, but their inherent fragility made them unsuitable for repeated use.
The most recent innovations implement soft actuators composed of rubber cylinders surrounded by carbon nanotubes. Applying voltage causes the rubber cylinders to expand and contract repetitively and at high frequency (as much as 500 times per second), causing the drone “wings” to flap up and down.
These tiny drones, with their soft actuators, are resilient and capable of withstanding mid-air collisions, making them suitable for various tasks, including agricultural monitoring and pollination. Future uses may include structural inspection, search and rescue, surveillance, and data collection.
PCB designs for smaller, more malleable devices have to consider factors like weight, rigidity, and resistance to impact and vibration. As in the case of larger UAVs, software simulation to test mechanical reliability in smaller UAVs is a valuable development tool.
The Future of UAVs Great and Small
In the future, UAV commercial passenger flights or large material transport using entirely autonomous flights still have some design challenges to overcome. Regulations, however, are more likely to hinder their long-term progress. Like self-driving cars, the adjustment period will require examining and discussing the risks and rationale of flying without a human pilot, with safety always taking precedence.
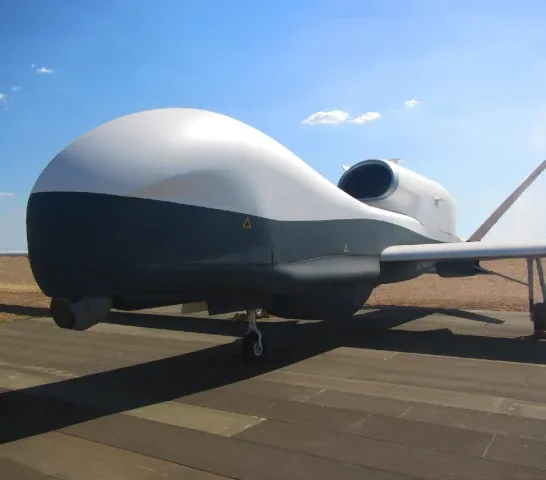
On a smaller scale, however, UAVs may have more immediate practical applications. With micro drones with cameras that relay images back to a human operator, inspecting intricate mechanisms is possible in small spaces that are otherwise impossible to reach without dismantling the entire mechanism, such as industrial motors or airplane engines. Drones can even be used during natural disasters to locate missing or injured people who cannot be reached by rescue workers.
As UAVs shrink and grow, it will alter how we define them. Along with providing previously difficult-to-obtain images and delivering small payloads, UAVs will become a practical and labor-saving alternative to traditional means of transportation, cultivation, and commerce.
Related Topics
How Drones are Transforming Offshore Wind Turbine Inspections
Maintaining Turbines, often located miles out at sea, can present some challenges. Drone technology can offer a solution for offshore turbine inspections.
Drone PCBAs: Tackling Sensor Integration for Defense & Beyond
Understanding the challenges and best practices in creating sophisticated sensors for real-time data collection for different industries.
How to Combat Signal Integrity Issues in High-Speed Drone PCBAs
Learn how to prevent signal integrity of drones that could compromise circuit stability and overall performance.
Need UAV PCBAs Manufactured?
Check out MacroFab’s PCBA production services.
About MacroFab
MacroFab offers comprehensive manufacturing solutions, from your smallest prototyping orders to your largest production needs. Our factory network locations are strategically located across North America, ensuring that we have the flexibility to provide capacity when and where you need it most.
Experience the future of EMS manufacturing with our state-of-the-art technology platform and cutting-edge digital supply chain solutions. At MacroFab, we ensure that your electronics are produced faster, more efficiently, and with fewer logistic problems than ever before.
Take advantage of AI-enabled sourcing opportunities and employ expert teams who are connected through a user-friendly technology platform. Discover how streamlined electronics manufacturing can benefit your business by contacting us today.