MacroFab Blog
Imagine this: your company's star product is humming along in production thanks to your contract manufacturer (CM). Production appears smooth, but there's a potential hidden risk: inconsistencies between documented procedures and the actual manufacturing process.
Yes, you’ve provided documentation to your CM. However, issues can occur if the manufacturing team deviates from your procedures. Several factors may contribute to this. Sometimes, a slight gap in the documentation creates ambiguity, leaving room for interpretation. Other times, experienced technicians may believe they've discovered a "better way" to achieve the desired outcome. You may, in fact, receive boards that work exactly as you want them to.
So what's the problem?
The problem is, when deviations from the documented process aren't captured, reviewed, and formally revised, the product relies on tribal knowledge – the tacit understanding of specific technicians. This creates a significant vulnerability for your company.
The Trouble With Tribal Knowledge
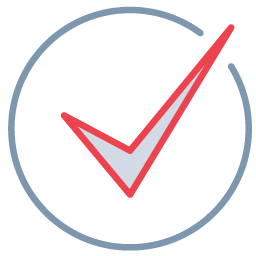
Checkpoint
Deviations may seem minor at first, but over time, they can snowball into quality issues, production delays, and even potential safety hazards.
Companies may unknowingly rely on tribal knowledge within their CM's workforce. This knowledge lives and dies with key employees. If they leave and the CM experiences turnover, a critical gap opens in how your product is made.
This lack of documented processes creates a situation of dependence. Without clear documentation reflecting real-world production tweaks, you’re left exposed. This scenario creates a chain reaction of issues:
- Vendor Lock-In: You become dependent on the specific CM, unable to consider other partners with potentially better pricing or capabilities.
- Innovation Roadblocks: Introducing new product features becomes challenging if the core manufacturing process is shrouded in mystery.
- Quality Control Challenges: Deviations from documented procedures can introduce inconsistencies, potentially leading to quality issues down the line.
- Troubleshooting Nightmares: When problems arise, pinpointing the root cause becomes a time-consuming exercise, as the documented process may not reflect reality.
The consequences become even more severe if the CM ceases operations altogether. You'll face a sudden scramble to secure a new manufacturing partner. This means restarting the entire New Product Introduction (NPI) process from scratch to replicate a product critical to you and your customers. This scramble translates into lost time, wasted resources, and a potential derailment of your entire product roadmap.
The Chain Reaction of Errors
Undocumented processes are a breeding ground for errors and inconsistencies. Without clear, step-by-step instructions, there's room for misinterpretations and deviations from the intended production flow. Deviations may seem minor at first, but over time, they can snowball into quality issues, production delays, and even potential safety hazards.
Consider the costs associated with resolving a complex manufacturing problem lacking a documented baseline. Sending engineers halfway across the world to decipher the production line in real time is a logistical nightmare and a significant financial drain.
The Solution: Owning Your Manufacturing Knowledge
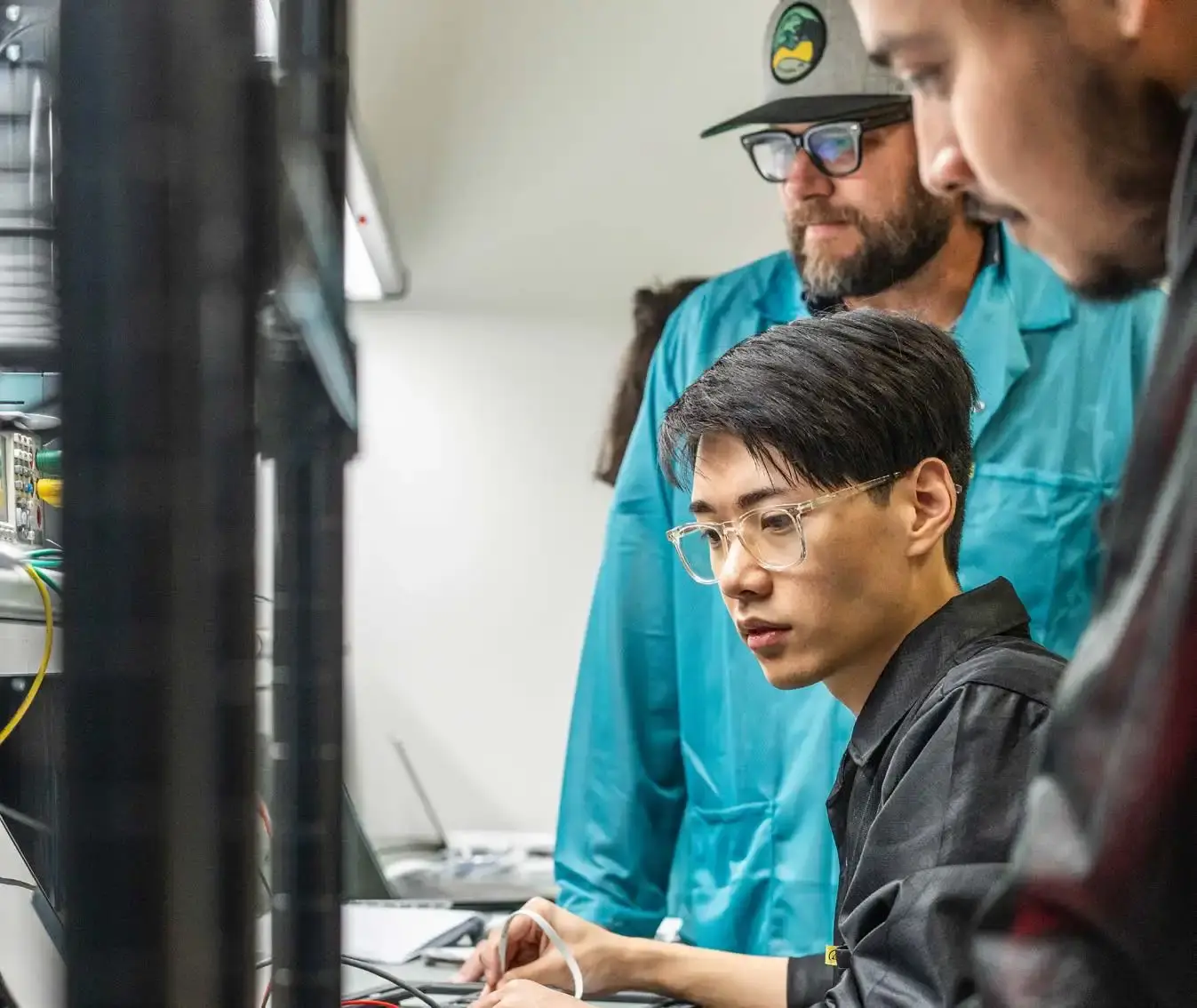
You don't have to be dependent and vulnerable. To maintain control over your manufacturing knowledge, comprehensive documentation must remain yours. This involves meticulously capturing every step of the production process, from component selection and assembly to testing and quality control. Connected technology platforms keeping you tethered to your document management accomplish this goal.
By creating detailed documentation, you gain a deep understanding of your product manufacturing process, thus enabling you to make informed decisions. Further, it gives you factory portability, allowing you to move from one factory to another without dealing with the issues mentioned earlier.
The Power of a Connected Partnership
The ideal solution, however, goes beyond simple documentation. Look for a CM that embraces a collaborative approach built on clear communication and a shared platform for managing manufacturing data. This platform should give you real-time access to production information, allowing you to monitor progress, keeping you abreast of potential issues, and ensuring technicians follow your specifications to the letter.
In essence, you're moving away from a reliance on tribal knowledge and towards a data-driven, transparent partnership. This reduces the risk of errors and fosters trust and collaboration, leading to continuous improvement in the manufacturing process.
Building a Sustainable Future
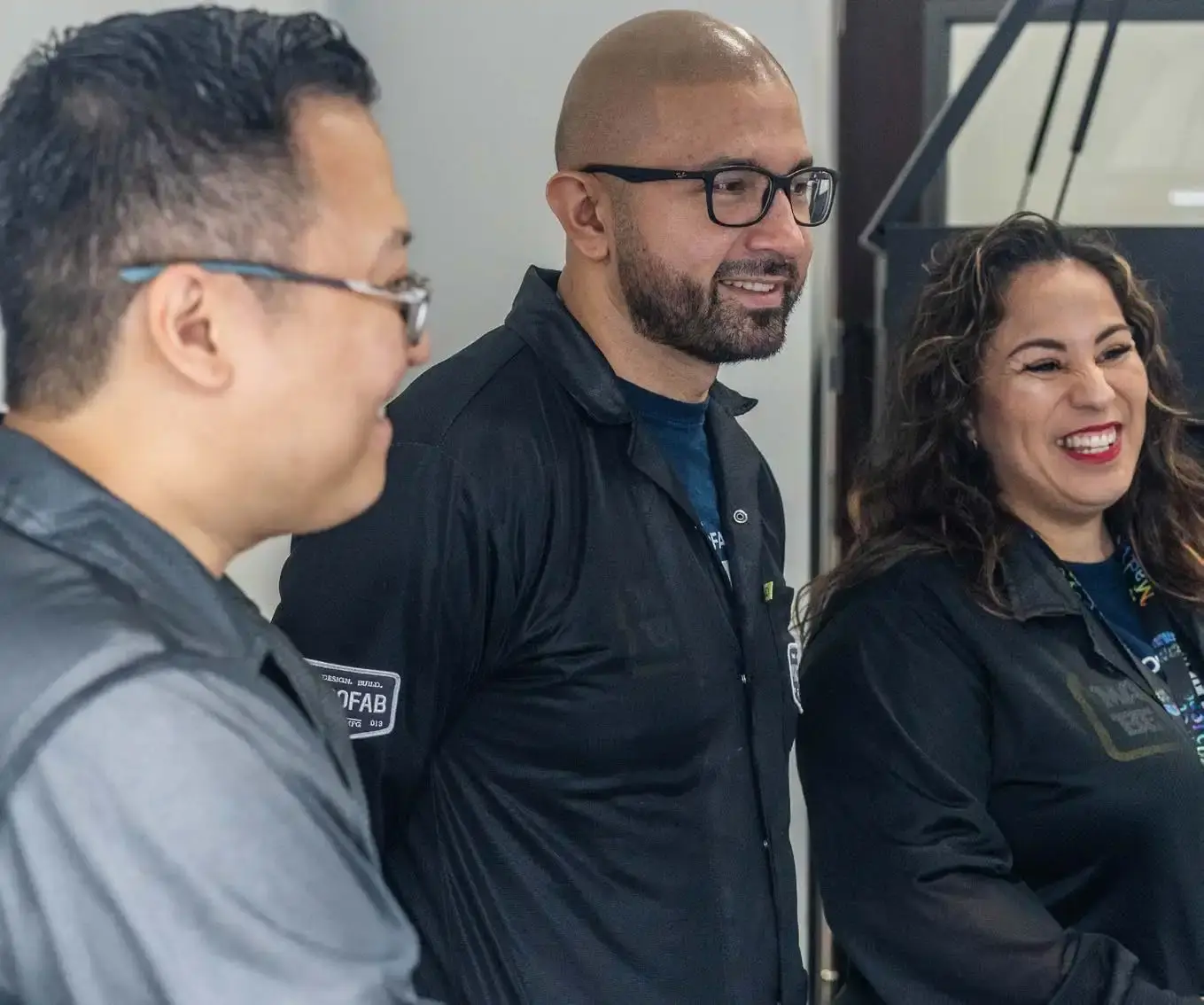
Your company's future depends on comprehensive documentation and a collaborative CM partnership. By taking ownership of your manufacturing knowledge, you gain the agility and flexibility to adapt to changing market conditions. You can seamlessly switch manufacturing lines when necessary, introduce new product features with minimal disruption, and ensure consistent quality throughout your product lifecycle.
In today's dynamic tech landscape, controlling your manufacturing destiny is paramount. Don't let undocumented processes become a hidden liability. Take charge, document your knowledge, and forge a partnership built on shared data and clear communication. This is the path to a sustainable competitive advantage and long-term success.
Related Topics
How to Shorten PCBA Production Lead Times with MacroFab
In the rapidly evolving electronics sector, extended production lead times are no longer tolerable, and minimizing these lead times is crucial for success.
PCBA Order Lead Time Report: Guidance for Lunar New Year 2025
With Lunar New Year coming up, MacroFab wants to ensure they give the best guidance when planning orders to continue meeting delivery guidelines.
How Opaque Electronics Manufacturing Costs Stifle Innovation
This blog discusses how MacroFab as a partner can give you the power to launch a groundbreaking product with confidence in this fast-paced world.
Try MacroFab's Technology Platform Today.
Get an instant quote nowAbout MacroFab
MacroFab offers comprehensive manufacturing solutions, from your smallest prototyping orders to your largest production needs. Our factory network locations are strategically located across North America, ensuring that we have the flexibility to provide capacity when and where you need it most.
Experience the future of EMS manufacturing with our state-of-the-art technology platform and cutting-edge digital supply chain solutions. At MacroFab, we ensure that your electronics are produced faster, more efficiently, and with fewer logistic problems than ever before.
Take advantage of AI-enabled sourcing opportunities and employ expert teams who are connected through a user-friendly technology platform. Discover how streamlined electronics manufacturing can benefit your business by contacting us today.