MacroFab Blog
As part of electronics manufacturing and PCB production, planning for supply chain success is imperative. Without a cohesive plan, shortages of materials or components could cause a line-down situation.
Conversely, a burden of oversupply and inventory can induce large carrying costs that can be prohibitive on profits. Management of information, originating from the customer, all the way through inventory shipment is the key to winning logistics challenges.
Business Objectives Drive Inventories
Internal business objectives should determine the targets for inventory levels throughout the production process. This will include:
- BOM components
- Raw PCBs
- Mechanical housings
- Cabling harnesses
- Any assembly materials needed for the manufacturing process
The required financial metrics for your organization will drive the procurement orders and identify the number of materials that can be held on hand in a work-in-process point.
It is important to collaborate with your CM to identify what can be staged at different points of manufacturing – Raw materials, Partial/Sub-assemblies, and Finished Goods Inventory. A comprehensive logistics plan should consider the impacts involving all stakeholders – internal, CM, distributors, vendors, order fulfillment, shipping, and customers. Identify each partner's capabilities for shipments and schedules as well as the final expectations from customers. Many CMs can ship directly from their warehouse to your customers. Determine if this fits within your company’s objectives.
Develop a Logistics Plan
When planning logistics for components, review the entire BOM for long lead-time items and custom components. Each BOM item should have a lead time based on the manufacturer and the distributor. Once the longest lead times are identified, a worst-case logistics schedule can be developed.
Full kitting services by your CM can push the burden of this component logistics to their operations team, instead of owning this scheduling internally with your direct procurement.
The BOM should contain multiple substitutes for each component listed. If possible, identify as many substitutions that are as close to your inventory as possible for best planning purposes. In case of shortages, long lead times, or obsolescence, this will mitigate the unfortunate circumstance.
By kitting a system BOM through your CM, a list of viable substitute components can be made available for comparison and selection at the time of quotation. MacroFab's platform allows you to designate alternative substitutes at upload to keep your orders moving forward.
Scheduling and Forecasting
Logistics scheduling will be determined by order patterns based on end-customer demand. Demand forecasting is key to driving order rates and establishing a final logistics plan.
If you don't have accurate information, garbage in equals garbage out. An electronics manufacturing platform like MacroFab gives you access to real-time information so you can connect with available parts and current factory capacity at any given time.
The logistics of receiving materials into the inventory department at the factory should be reviewed with your CM. This will include how they receive material into their system and the time duration until component availability on the manufacturing floor. By planning to this detail, scheduling of new builds at the CM can be done with a single-day resolution. Keep in mind that there may be up to three part number designations to manage for a single component – the manufacturer’s part number, your internal part designation for your schematic, and the contract manufacturer’s number. All three have to be in agreement across the entire BOM within your business intelligence databases.
From the start of the manufacturing lifecycle, the lead time from end product forecast, order and delivery will determine the cycle time and these factors will dictate logistics:
- Ordering lead time
- Amount of inventory to be held
- Assembly schedule
- Intermediate shipment duration
To gain manufacturing insight advantage, work in collaboration with your CM for the best ways of sharing information across business intelligence tools. Forecasting, purchase orders, inventory count per stage, and order fulfillment by the CM are all analytics data that can be leveraged with your CM partner for logistics optimization.
Plan in Advance for Future Uncertainty
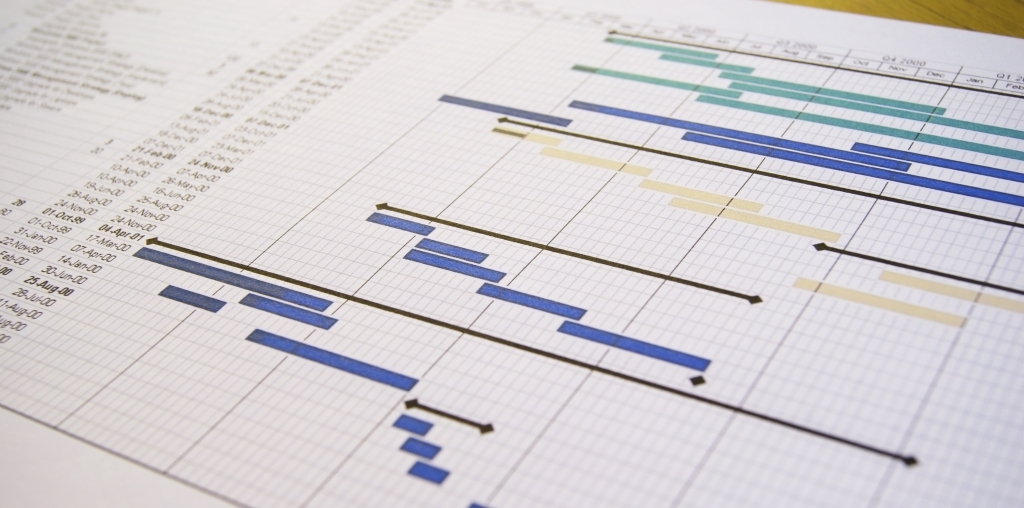
In some cases, very high-performance systems may exceed the US Commerce Department's technical limit for acceptable international sales. A clear set of technical thresholds is defined by the agency for determining what products are subject to export restrictions. If this is the case for your system, the first set of logistics defense is to have your business planning tools prevent any unauthorized movement of products that could be in violation. These criteria will include product model, geography within the world, and the final customer delivery point. However, manufacturing locations also need to be considered when planning for these products. Intermediate points in the manufacturing process may be considered a final product, so the qualification of the performance at a given factory location should be vetted.
When high demand creates limited available manufacturing capacity for a given time, it is important to establish product priorities with your CM. Otherwise, this decision is left up to unauthorized interpretation.
Part Obsolescence
For many reasons, a parts manufacturer may discontinue selling a particular component, rendering it obsolete. Sometimes they may offer a pin-for-pin substitute, but this scenario cannot be relied upon.
Typically, this situation involves “Last Time Buys” over a one to two-year time period. This creates a need to develop a plan with your CM to hold inventory and transition to a different BOM. A component obsolescence review plan should have a review owner that either gets automated alerts from manufacturers or intentional software tools that routinely checks for updates. Your CM may have access to this information across wide distribution channels. These verifications should have a known periodicity. Eventually, a final decision maker within the design team needs to be identified for a change to the BOM for obsolete part substitutions.
Read more about how component obsolescence affects the PCB supply chain now.
Maintain Authorized Distribution Channels
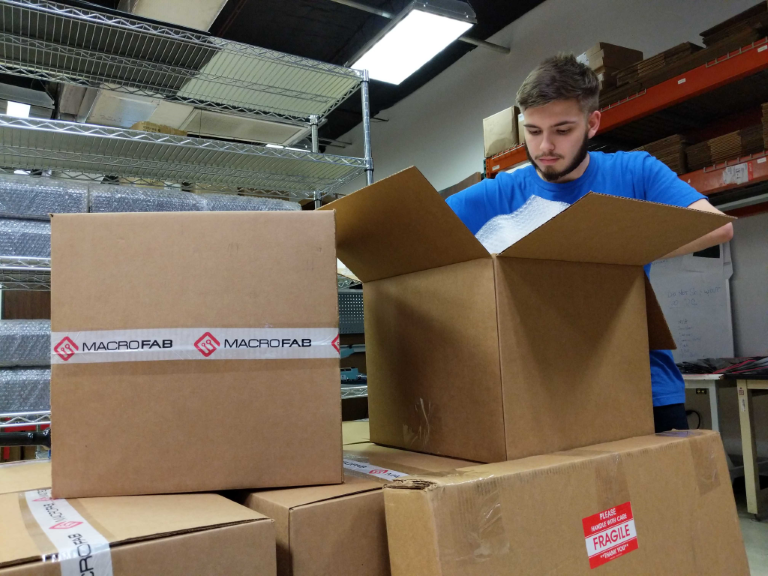
A MacroFab Team Member boxing up shipments.
The logistics of scrap material and yield loss is important to plan at the onset of production. These directions should be clear with the CM and any other distribution partner. Finished products or partial subassemblies that are unfit for sale due to electrical or mechanical non-conformance should be disposed of or destroyed in a proper method. Without clarity on this procedure, the material may be used in unauthorized ways and potentially could find its way to the gray market as a substitute for a real product, especially if the manufacturer is incentivized to take your ideas.
Similarly, gray market components for your system should be avoided with every effort. These spoof devices are maliciously inserted into channels with the intent of masquerading as their authentic electronic counterparts. The fake components may have come from the scrap bin of a semiconductor assembly supplier or re-marked grading from another entire product. Even worse, they may be completely empty packages. Nearly full price can often be charged for the devices with the unsuspecting buyer not becoming aware of the problem until weeks later during a final electrical test step. In times of long lead times, scarcity, or deep discounts, using unapproved channel distribution can seem enticing. Without purchasing materials through authorized channels sanctioned by the original manufacturer, there is no guarantee that the components are genuine. It is best to work with a CM that only source parts from reputable distributors.
Read Supply Chain Challenges Persist for Electronics Companies now to learn more.
End of Life
End-of-life planning should be done during the product development process. It should not be an afterthought during the late stages of its production. When a product reaches the end of its’ life, the logistics of the remaining inventory and work in process material must be planned for some type of disposition. Decide if any materials inventory can be repurposed to other products and reclaimed. If an obsolescence notice must be provided, then that’s the last time buys may be offered to customers from a vendor perspective. A finite amount of demand can then be planned for manufacturing over a fixed time horizon.
Logistics management planning should be integrated into the product development process. The fundamental underpinning is based on the financial goals of your enterprise for lead times and inventory. However, there will be no substitute for accurate scheduling and forecasting from internal business managers. This will ultimately drive the success of your logistics plan. Work with your CM partner that can offer many options to navigate the logistics from choosing the right factory site location, kitting and finished goods shipments.
Related Topics
Preparing for Potential Supply Chain Disruptions During Lunar New Year
This blog discusses on how to prepare for unexpected events for global supply chains such as the dockworker strike in preparation for Lunar New Year.
Mapping Out a PCBA Supply Chain Strategy in Five Moves
Companies should create unique vendor relationships with numerous international suppliers due to the necessity of having to source components globally.
MacroFab’s Modern Approach to Strategic Sourcing
Many Contract Manufacturers (CMs) and Original Equipment Manufacturers (OEMs) have some sort of procurement team. So what makes MacroFab so different?
SEE HOW MACROFAB'S PLATFORM DRIVES TRANSPARENCY
GET AN INSTANT QUOTE NOWAbout MacroFab
MacroFab offers comprehensive manufacturing solutions, from your smallest prototyping orders to your largest production needs. Our factory network locations are strategically located across North America, ensuring that we have the flexibility to provide capacity when and where you need it most.
Experience the future of EMS manufacturing with our state-of-the-art technology platform and cutting-edge digital supply chain solutions. At MacroFab, we ensure that your electronics are produced faster, more efficiently, and with fewer logistic problems than ever before.
Take advantage of AI-enabled sourcing opportunities and employ expert teams who are connected through a user-friendly technology platform. Discover how streamlined electronics manufacturing can benefit your business by contacting us today.