MacroFab Blog
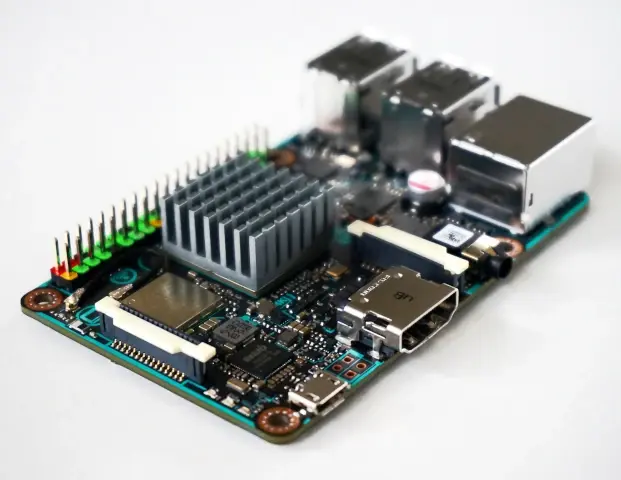
Whenever PCBA electronics are operated, heat results – high-power components consume electricity in order to function, and this electricity generates heat. But in the absence of adequate thermal conductivity control, heat can get trapped in PCBA enclosures if not handled properly. In fact, modern electronics are highly dependent on how PCBAs deal with thermal byproducts, and engineers must design PCBA systems to dissipate heat efficiently.
In spite of this, it’s becoming increasingly difficult to keep PCBAs at the correct temperature. As designs decrease in size, more parts must be fitted into smaller spaces. Additionally, today’s components are more powerful, producing more heat despite taking up less space.
Due to these two trends - miniaturization of electronics along with their increasing power - heat dissipation has become a major factor in PCBA design.
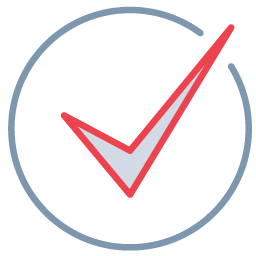
Checkpoint
As electronics become smaller and more powerful, heat dissipation has become a major concern.

In this article, we will explore key strategies and best practices for designing efficient heat dissipation in compact PCBA systems. We will begin by discussing the factors that affect heat generation in PCBA systems and the importance of accurate thermal analysis and simulation.
We will then delve into various design strategies for efficient heat dissipation, including materials selection and layout optimization, the use of heat sinks, cooling techniques, and the placement of cooling components.
Also, we’ll discuss strategies for overcoming the challenges of designing for heat dissipation in compact and space-constrained systems. Among these strategies are shrinking and lightening cooling components, utilizing innovative cooling technologies, and leveraging custom fabrication and design.
Understanding PCBA Heat Generation
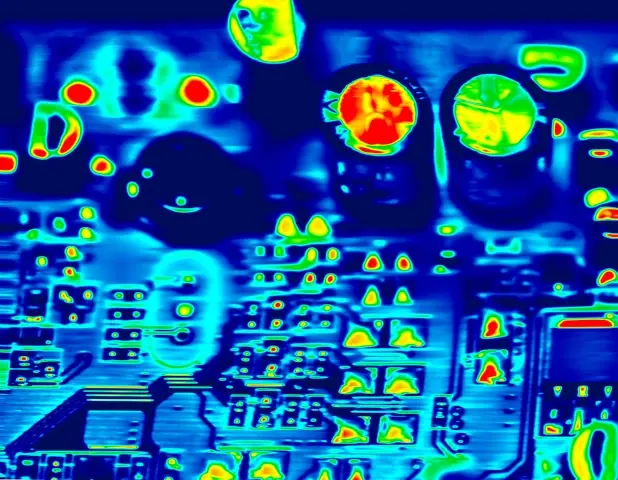
Understanding how heat is generated in PCBA systems is essential for optimal thermal performance. Recognizing the unique aspects of every board drives the necessity of a customized approach to thermal management rather than a universal one. A reliable, heat-resistant PCBA system is born from accurate data analysis, robust forecasting, and strategic planning.
Below are the key factors to consider when improving heat dissipation in PCBA systems:
- Physical characteristics of the board
- Component selection
- Anticipated operating environment
- Heat dissipation and cooling strategies applied
We’ll dive into each of these in more detail below.
Board Physical Attributes
The makeup of printed circuit boards matters greatly in thermal management. Factors like board size, thickness, layer stack-up, and soldering uniformity can significantly influence heat dissipation. Thicker boards, traces, and copper padding generally enhance heat distribution. Additionally, more board surface area provides more room for heat to spread out between high-power components, and as this shrinks, thermal management can become trickier.
Component Utilization
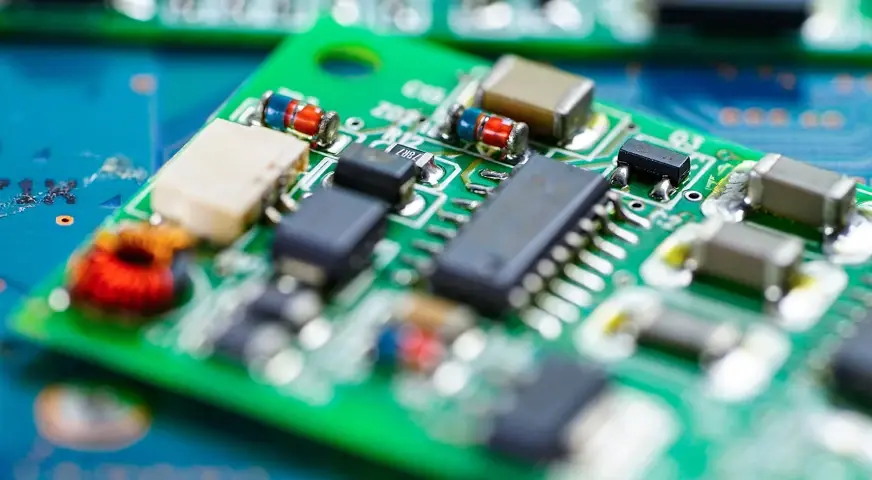
The specific components mounted on a PCB also impact thermal performance. The number and placement of high-power components and where those components are mounted on a board can dramatically shape a device’s thermal characteristics. PCBAs rely on components to operate, but they can also introduce thermal management complications.
Environmental Considerations
PCBA designers and electronics engineers have to think carefully about the environments their devices will exist in after deployment. Warm external temperatures can make it harder to keep PCBAs cool. Consequently, devices that will be used in hotter environments may require more specialized thermal management.
Heat Dissipation and Cooling
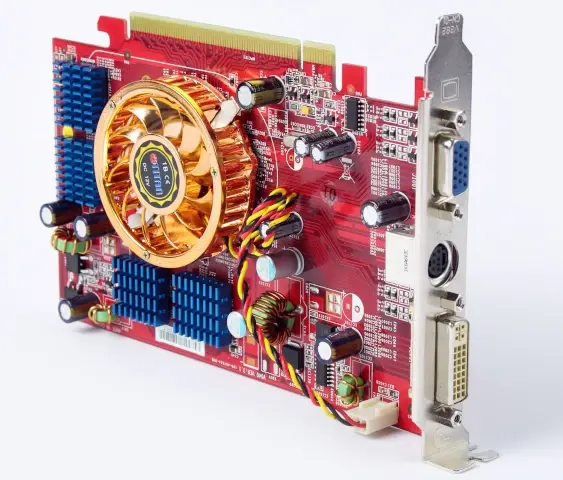
Electronics engineers and PCB designers can’t control every factor involved in PCBA thermal management. However, they can follow design principles and best practices that take heat dissipation into account early. These encompass both active strategies, such as the integration of cooling fans and heat pipes, and passive methods, like optimizing board layout for improved airflow or using heat sinks and thermal vias. With careful planning, both active and passive heat dissipation strategies can be seamlessly incorporated within the same PCB to ensure optimal thermal performance.
The Imperative of Thermal Analysis and Simulation
Thermal analysis, or thermal modeling, is an essential process in identifying heat generation sources on a PCBA, such as the central processing unit (CPU) or power supply circuits, and formulating effective heat management strategies. By modeling the heat produced by these components, engineers can make informed decisions about heat transport mechanisms, especially in densely-packed PCBA designs where space for thermal management components is limited.
The application of this analysis helps to strategically position thermal management parts like fans and heat sinks. For instance, in an industrial controller with a high-performance microcontroller, heat sinks might be positioned in proximity to this component to efficiently dissipate the generated heat.
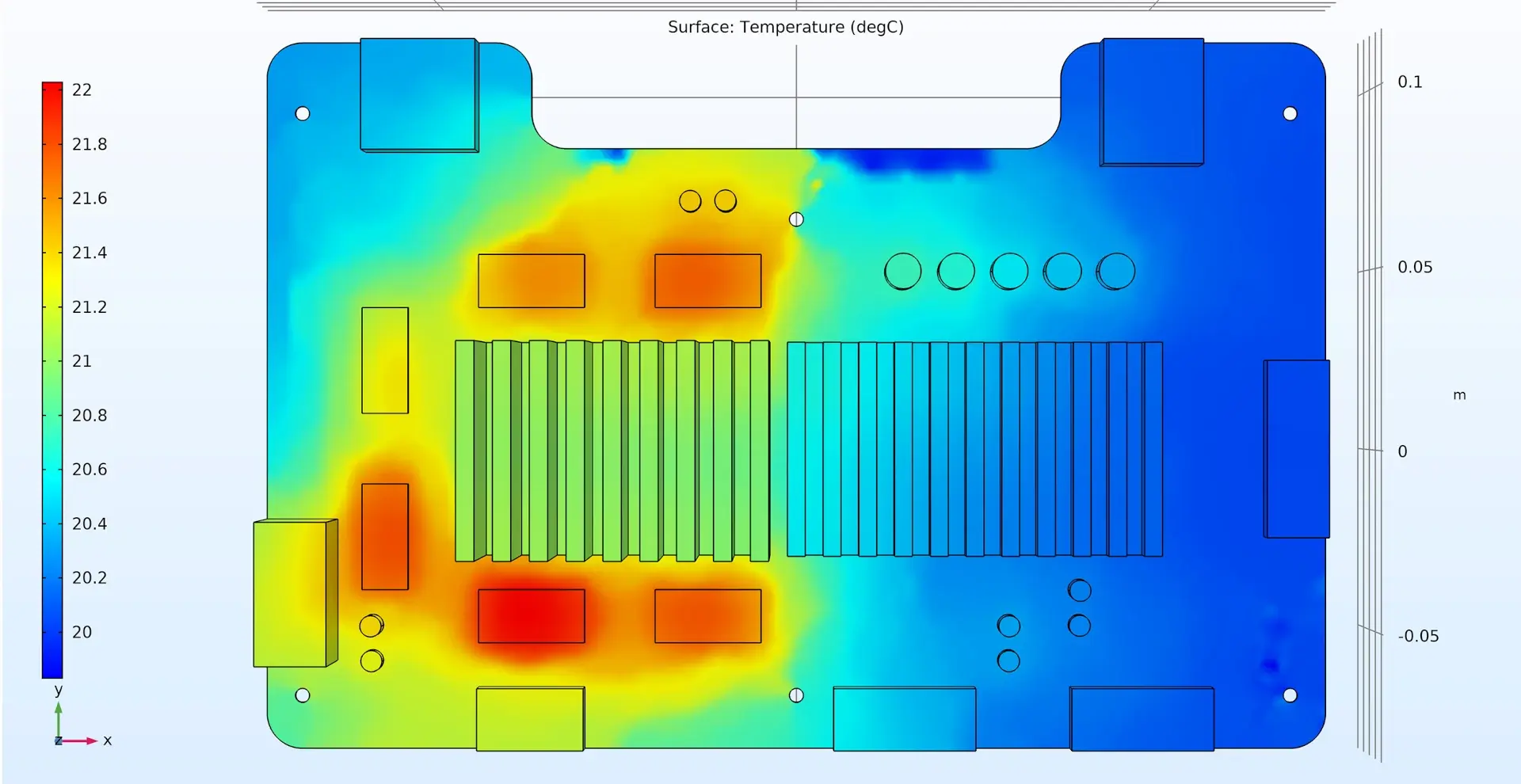
The simulations generate color-coded thermal maps that correspond to specific areas on the PCBA surface. In a network router’s PCBA, for example, these maps can help identify potential heat zones around power-intensive components, such as a Wi-Fi chipset operating at high transmission rates.
Hence, thermal simulation software becomes invaluable in creating efficient heat dissipation methods, predicting material and product reliability, thereby impacting significant business factors, including product longevity and customer satisfaction.
The role of comprehensive thermal analysis and simulation cannot be overstated in modern PCBA design. These methodologies offer an invaluable opportunity for design validation prior to the costly stages of fabrication and manufacturing, mitigating the risk of encountering thermal issues later on. Without the proper thermal analysis tools, visibility into PCBA heat characteristics can be greatly reduced.
This lack of insight can potentially lead to manufacturing hold-ups, extended product release cycles, and ultimately, subpar product quality. For instance, without proper thermal analysis, an IoT device could overheat and fail prematurely, causing customer dissatisfaction and product returns.
Design Strategies for Efficient Heat Dissipation
Ensuring the longevity and optimal performance of your devices starts with effectively managing heat dissipation through strategic PCBA design. It all comes down to the choices you make:
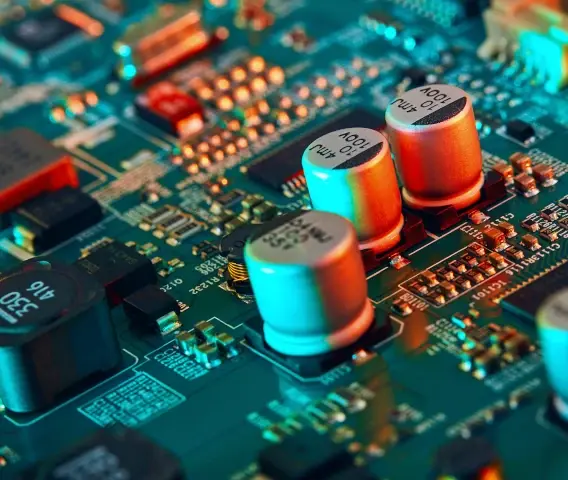
- Optimized Material Selection and Layout: Material selection is a vital aspect of controlling heat within compact PCBA designs. While FR-4, the standard PCB substrate material, has commendable mechanical and electrical properties, it has a low thermal conductivity rating which makes it less efficient at dispersing heat rapidly across the board. More heat-resistant options, such as ceramic and metallic-based substrates, are excellent thermal conductors and are better suited for high-temperature applications, enabling a more even heat distribution across PCBs.How components are arranged and connected significantly impacts heat dissipation. Placing high-power components towards the center of PCBs encourages even heat distribution across the board. Conversely, clustering high-power components near board edges or close to each other can lead to localized overheating, potentially resulting in device failures and even safety issues.
Utilization of Heat Sinks and Spreaders: The deployment of thermal management components such as heat sinks, heat spreaders, and thermal vias can significantly enhance your device’s thermal performance.
Heat sinks absorb heat from high-power components and spread it over a larger surface area, allowing the component to dissipate heat faster and more efficiently. Some heat sinks are equipped with built-in cooling fans for enhanced performance.
Heat spreaders are another efficient tool for heat dissipation. They use a large, flat surface to transfer heat to an even larger external metal surface. They’re particularly beneficial in applications subjected to excessive vibrations or shocks.
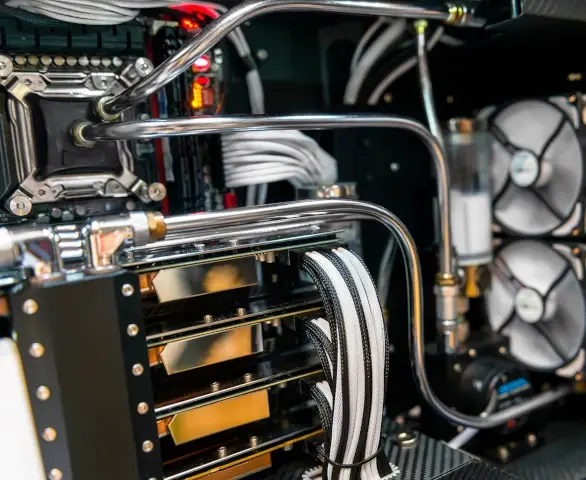
- Incorporating Air-cooled and Liquid-cooled Systems: When passive methods of heat dissipation aren’t sufficient, cooling fans and liquid-cooled systems may bethe answer. Cooling fans, especially when used in conjunction with heat sinks,quickly force heat away from source components, effectively lowering the board temperature. However, these are best suited to larger enclosures with ample air volume.The placement of cooling systems and components is a strategic decision, relying on thermal analysis and simulation data. These cooling systems should facilitate quick heat transfer from high-temperature areas to low-temperature areas, ensuring their effectiveness.
The right combination of these elements leads to a reliable, efficient, and long-lasting device that meets your specific requirements. It all starts with understanding the heat generation and dissipation characteristics of your device, then applying the right techniques to manage it effectively.
Overcoming Space Constraints in PCBA Design
Modern electronics are getting smaller, yet more powerful. While this creates better user and customer experiences, it makes PCB designers’ jobs harder when it comes to heat dissipation. Knowing how to overcome space constraints in PCBA design is now a crucial skill.
Strategies For Reducing the Size and Weight of Cooling Components
Below are some tips to keep cooling component footprints down.
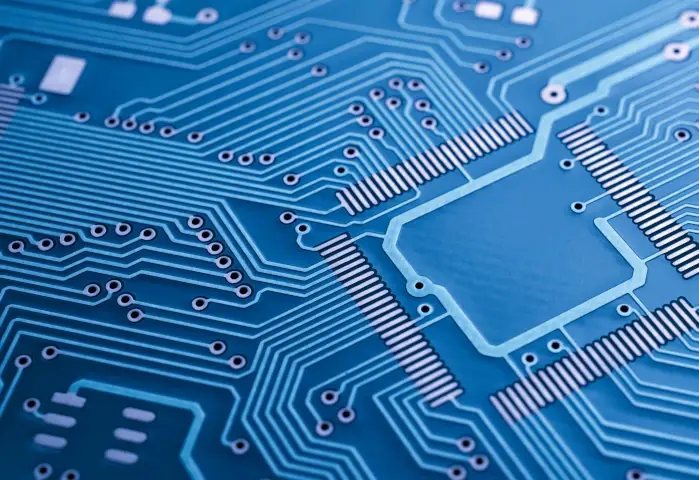
- Apply solder evenly to ensure that thermal management components, like heat sinks,have clean contact with active components.This reduces the need for additional cooling components.
- Keep traces wide enough to promote low impedance and minimal power loss. Boards that experience power loss are more prone to heat generation, as components have to work harder to compensate for the lack of power. This extra work leads to excess heat. Having wide enough traces reduces the burden on mounted cooling components.
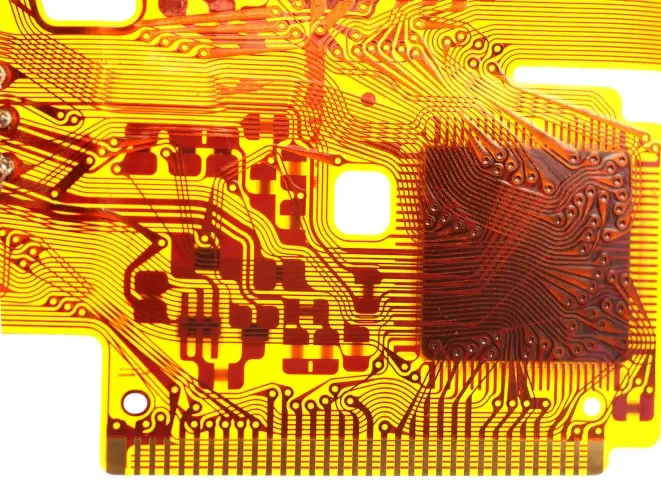
- Increase board surface area by using flexPCB designs. These designs have much higher surface area-to-volume ratios than rigid boards, which is helpful in heat dissipation.
- Use thermal vias to direct heat away from the top PCB copper layer. Thermal vias are low-resistance pathways composed of conductive epoxy resin that come from below high-power components to carry heat away. They span the PCB substrate and combine well with copper layering in multi-layer PCBs. Again, this takes some heat dissipation off the surface of the board that would otherwise require bulkier fans or heat sinks.
Utilize TECs or Peltier Devices
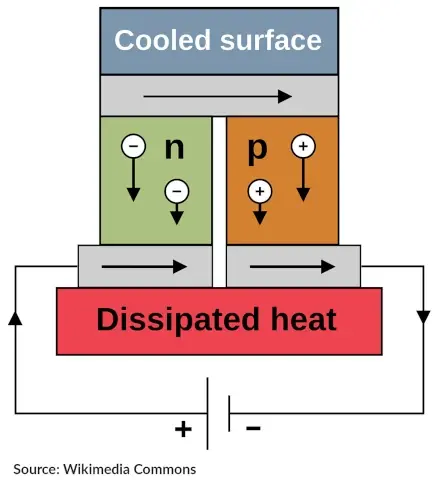
Thermoelectric cooling (TEC) is a newer technique that has the ability to lower component temperatures below ambient board temperatures without the need for fluid. Engineers have better control over temperature with thermoelectric cooling, and the technique works well in smaller spaces due to its reliance on electricity, rather than on liquid and its subsequent infrastructure.
Thermoelectric coolers. or Peltier devices work on the principle of the Peltier effect. When an electric current is passed through two dissimilar metals or semiconductors connected at their ends (forming a closed circuit), heat is absorbed at one junction and released at the other. This
creates a temperature difference, with one side cooling down while the other heats up. Essentially, these devices can cool or heat an object depending on the direction of the current.
TECs offer an innovative solution for heat management in PCBA designs, especially when board surface area is limited. With these devices, you can employ integrated cooling strategies involving direct contact between the TEC and the heat sink to more efficiently remove heat.
The Role of Custom Design and Fabrication in Overcoming Space Constraints
Finally, those who have advanced custom design and fabrication abilities should take full advantage. Customization opens up the doors to reliability and testing-based design. Engineers can build layouts that both fulfill business needs and promote scalable production. Choosing a supplier who can handle PCBA manufacturing and external enclosures will ensure the best possible results.
Custom design and fabrication also facilitate more open collaboration between various groups involved in the production – from PCBA designers to mechanical engineers and procurement specialists. Bringing all groups together early in the product development process allows for more creativity in overcoming space constraints and anticipating manufacturing challenges.
Listen to this classic Circuit Break Podcast to learn more about designing in compact spaces.
Mastering Heat Dissipation in Modern PCBA Design
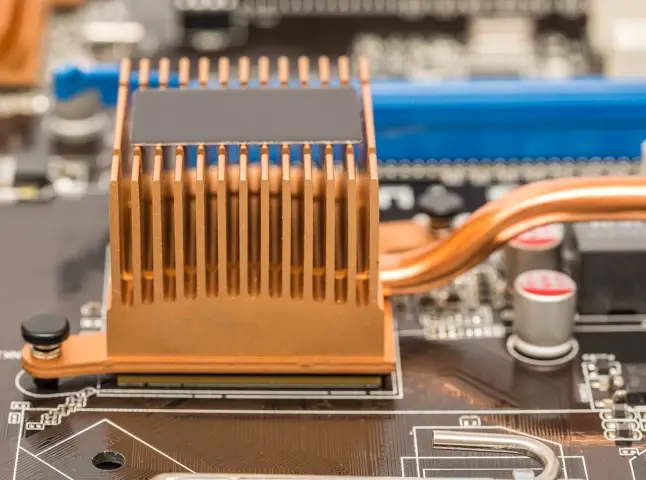
Heat dissipation in compact and space-constrained PCBA systems is a complex endeavor. Fortunately, engineers have tools and technologies at their disposal that make thermal management easier.
Improving thermal performance starts with advanced thermal analysis and simulation. These solutions are what enable engineers to make intelligent decisions about heat dissipation, like what materials to use and how to design PCB layouts. Engineers should also use thermal management components, like heat sinks and heat spreaders, effectively. When more active forms of heat dissipation are required, air-cooled and liquid-cooled systems can work well.
Overcoming space constraints through x, innovative cooling techniques, like thermoelectric cooling, and custom fabrication can also help. These strategies will only become more valuable as electronics get smaller and denser. The good news is that making heat dissipation improvements is as easy as keeping these best practices in mind and incorporating some new design techniques during the next production run.
Related Topics
PCB Antenna Design: A Step-by-Step Guide
Step-by-step guide to the PCB antenna design process, providing practical tips to help you successfully integrate the antenna into your wireless product.
For Electronics Engineers: Top 10 Circuit Break Episodes
Enjoy these handpicked episodes designed to spark your imagination and fuel your passion for electronics.
MacroFab's Certifications Benefit PCBA Production
Your PCBA production must be secure and reliable for your products to compete in the market. We have listed our certifications and how they benefit you.
Optimize Your PCB Assembly Process with MacroFab
End-to-End Assembly CapabilitiesAbout MacroFab
MacroFab offers comprehensive manufacturing solutions, from your smallest prototyping orders to your largest production needs. Our factory network locations are strategically located across North America, ensuring that we have the flexibility to provide capacity when and where you need it most.
Experience the future of EMS manufacturing with our state-of-the-art technology platform and cutting-edge digital supply chain solutions. At MacroFab, we ensure that your electronics are produced faster, more efficiently, and with fewer logistic problems than ever before.
Take advantage of AI-enabled sourcing opportunities and employ expert teams who are connected through a user-friendly technology platform. Discover how streamlined electronics manufacturing can benefit your business by contacting us today.