MacroFab Blog
The global push for renewable energy is undeniable. Fueled by a potent combination of international cooperation and escalating climate concerns, renewable energy is experiencing a surge. At the United Nations Framework Convention on Climate Change (COP28) in December 2023, over 130 countries committed to tripling renewable energy capacity to 11,000 GW by 2030. Underscoring this commitment, GWEC Market Intelligence projects a significant expansion of 791 GW of new wind energy capacity in the next five years under current policies. With a vast theoretical potential of up to 70,000 GW according to recent data shared by McKinsey, offshore wind is poised for significant growth.
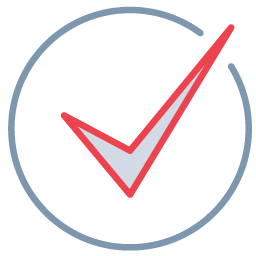
Checkpoint
Reliable and high-performance PCBAs are crucial for ensuring safe and efficient drone operation, ultimately contributing to the success of the offshore wind industry.
However, maintaining these colossal turbines, often located miles out at sea, presents a unique set of challenges. Traditional manual inspection methods relying on industrial climbers are risky, time-consuming, and expensive. This is where drone technology steps in, offering a game-changing solution for offshore wind turbine inspections.
Safety First: Reducing Worker Risk
Inspecting offshore wind turbines exposes workers to many dangers. From falls from heights and electrical shock to the perils of working in confined spaces, the risks are considerable. With ever-increasing turbine heights, like GE's Haliade-X reaching a staggering 850 feet, these hazards become even more pronounced.
Drone solutions can solve these challenges in a transformative way. By eliminating the need for human climbers, drones significantly enhance safety and reduce the risk of accidents. Additionally, drones can conduct inspections more frequently, enabling the early detection of potential issues and preventing costly downtime through more regular inspections.
Enhanced Efficiency: Faster, More Cost-effective Inspections
Time is money, especially in the offshore wind industry. Traditional inspections take hours, impacting turbine operations and productivity. Drones significantly reduce inspection time. Studies suggest a potential 80% reduction in inspection time compared to manual methods, leading to substantial cost savings.
Furthermore, drones offer a more comprehensive inspection approach. They can reach previously inaccessible areas and provide detailed, high-resolution images for thorough analysis. This allows for the identification of even minor defects before they become major problems, preventing costly downtime and repairs.
Technological Advancements: A Look at the Cutting Edge
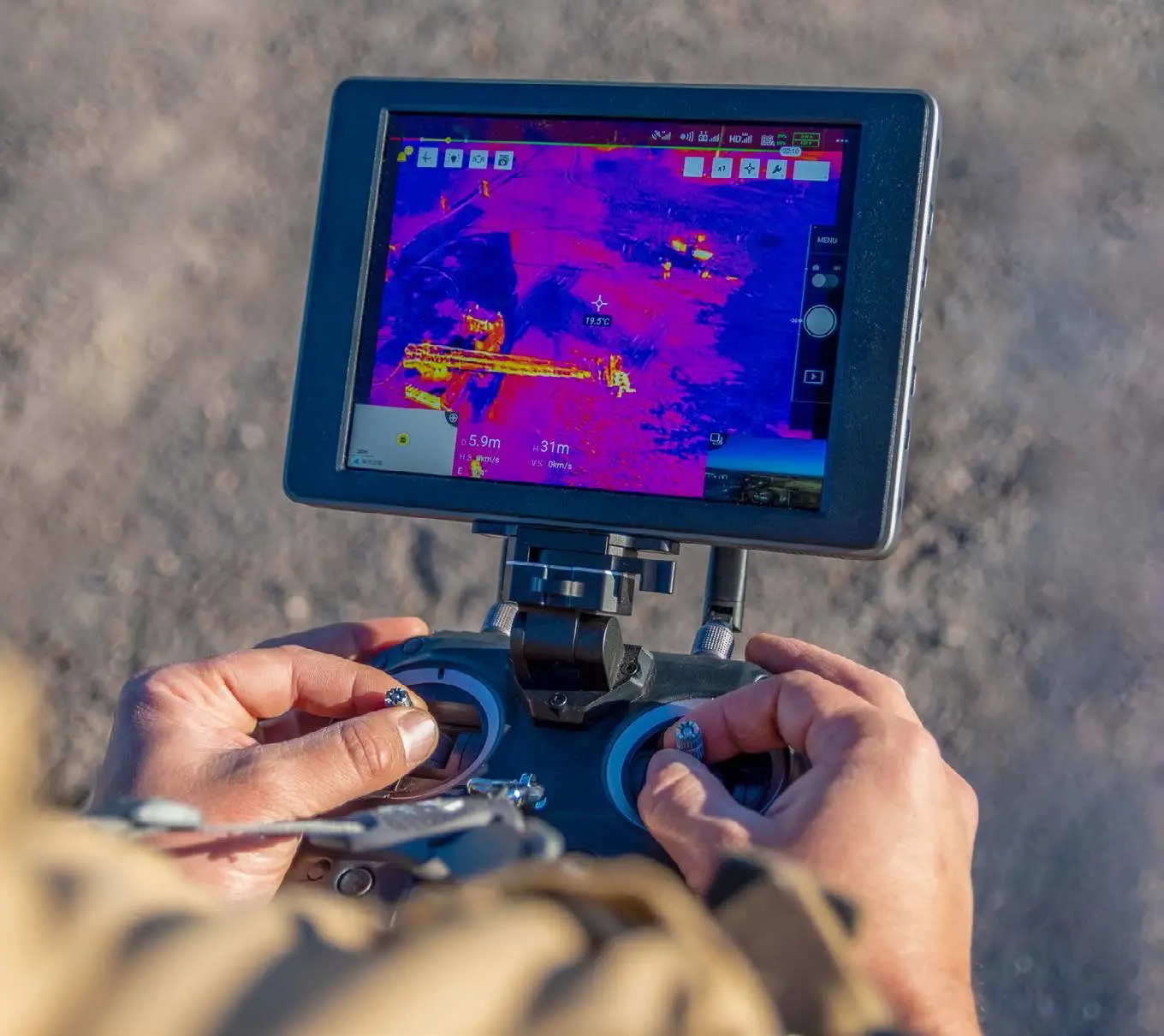
Drone technology constantly evolves, offering advanced solutions for wind turbine inspections. Here are some key areas of progress:
- Mobile Thermography: These drones use thermal imaging sensors to detect variations in heat flow across turbine blades. Areas with structural defects will show up as cooler spots, allowing for early detection of damage before it becomes critical.
- Lidar Inspections: Lidar (Light Detection and Ranging) technology provides visual inspections using high-resolution, 3D images of the turbine blades. While these inspections require slower, closer flybys, advancements in battery technology increases flight time, allowing drones to complete inspections of all blades without a recharge.
However, the offshore wind industry has recently faced challenges. Stakeholders have expressed concerns over a high rate of project cancellations following significant cost increases. Despite these setbacks, the long-term potential of offshore wind remains substantial, and the industry is actively seeking innovative solutions to overcome these hurdles.
Drones play a crucial role in addressing these challenges by optimizing operations and reducing costs. By collecting vast amounts of data, drones enable predictive maintenance strategies, allowing operators to schedule maintenance proactively, allocate resources efficiently, and extend turbine lifespan.
Learn more about sensor integration in drones now.
Data-Driven Decisions: Empowering Predictive Maintenance
Drones collect a wealth of valuable data during inspections. High-resolution images, thermal readings, and 3D point cloud data from Lidar scans can be analyzed using sophisticated software. This data allows for the creation of digital twins – virtual replicas of the turbines – that can be used to predict potential problems before they occur.
Predictive maintenance, enabled by drone data, empowers wind farm operators to:
Schedule maintenance proactively: Instead of waiting for a turbine to fail, inspections can be targeted based on the collected data, optimizing maintenance schedules and reducing downtime.
Optimize resource allocation: By identifying specific areas of concern, resources can be directed efficiently, reducing overall maintenance costs.
Extend turbine lifespan: Early detection and repair of minor issues can prevent them from escalating into major problems, ultimately extending the turbine’s lifespan.
A Collaborative Approach: Humans and Drones Working Together
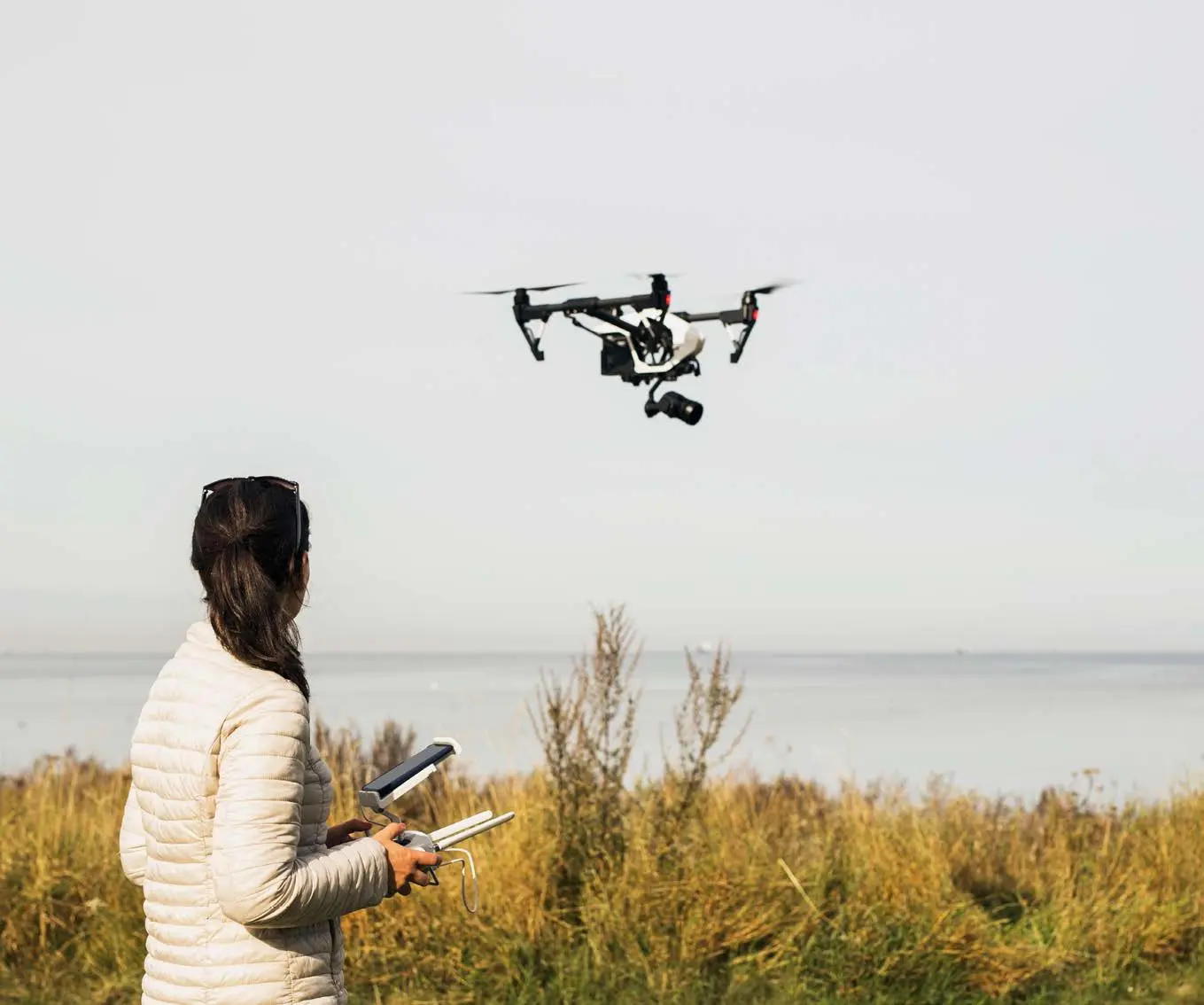
While drones offer significant advantages, they cannot replace human expertise completely. A successful drone inspection program thrives on a collaborative approach:
Skilled Drone Pilots: Experienced pilots are essential for safe and efficient operation in challenging offshore environments. Their expertise in navigating wind conditions and maneuvering around turbines ensures the integrity of the data collected.
Data Analysts: The vast amount of data collected by drones requires skilled data analysts. These professionals interpret the data, identify trends, and generate actionable insights for wind farm operators.
Maintenance Crews: Once potential issues arise, human technicians remain vital for repairs and maintenance activities. Drones provide the initial assessment, but human expertise is crucial for addressing the identified problems.
This collaborative approach leverages the strengths of both humans and machines. Drones handle the high-risk and repetitive aspects of inspections, while human expertise focuses on analysis, decision-making, and the complex tasks requiring manual intervention.
Challenges and Considerations
While drone technology offers immense benefits, there are still challenges to overcome. High winds significantly impact drone maneuverability and control, requiring experienced operators familiar with the specific challenges of flying around wind turbines. Salt spray from the ocean also affects drone components, making regular maintenance crucial.
Successful drone inspection programs emphasize careful planning and preparation. Autonomous flight capabilities minimize operator error and allow for precise control, especially in challenging weather conditions.
Read more about the challenges PCB assemblies in drones and other autonomous robotic systems face, including biofouling and other biological factors.
The Role of PCBAs in Drone Technology
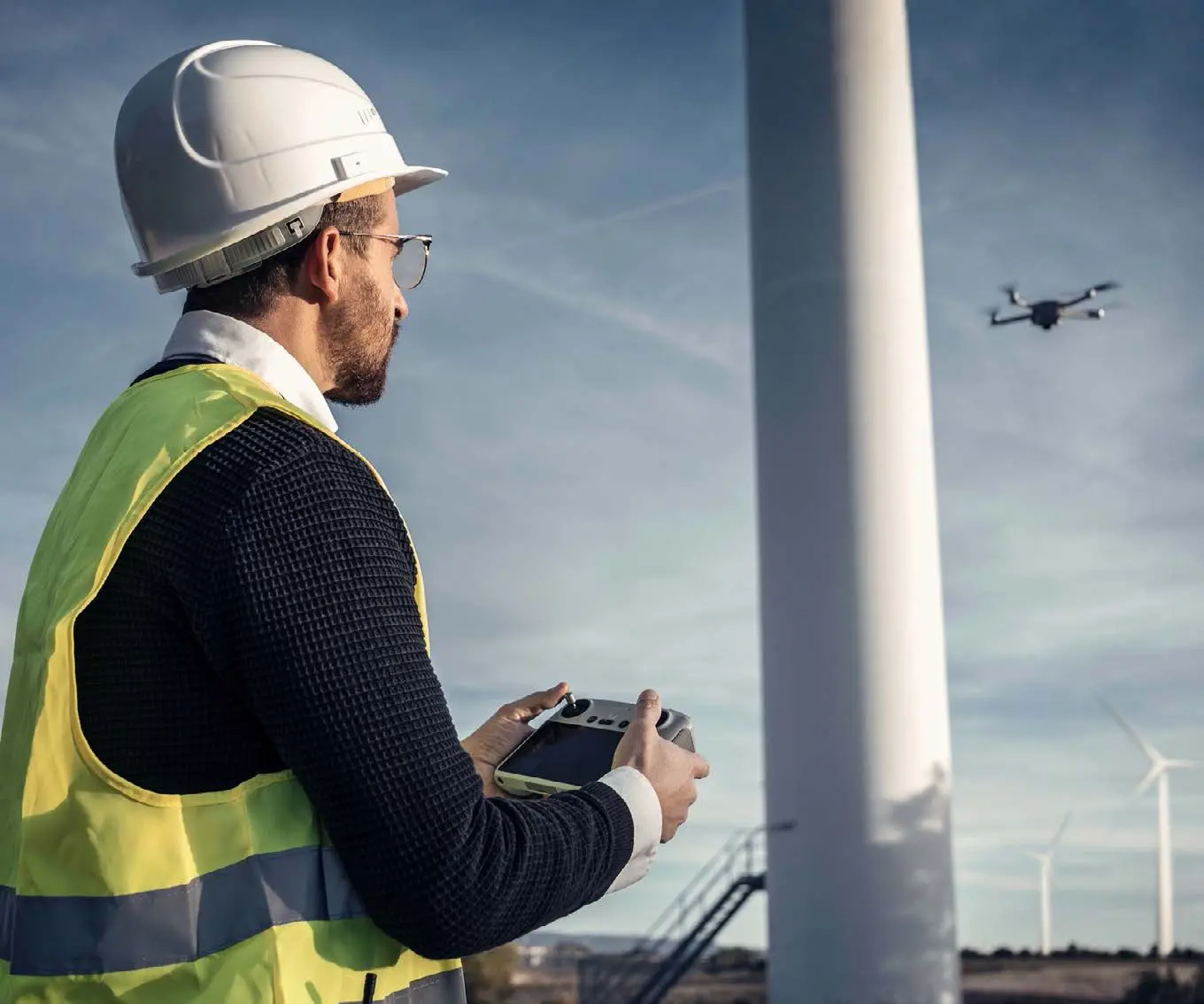
The widespread adoption of drones for offshore wind turbine inspections underscores the critical role of Printed Circuit Board Assemblies (PCBAs) in this rapidly growing industry. PCBAs serve as the "brain" of drones, integrating essential components like sensors, processors, and communication systems. These intricate boards enable drones to navigate complex environments, capture high-resolution images, and transmit data efficiently.
As drone technology advances, the demand for more sophisticated PCBAs increases. Features such as enhanced processing power, miniaturization, and improved durability are essential for meeting the rigorous demands of offshore wind turbine inspections. Reliable and high-performance PCBAs are crucial for ensuring safe and efficient drone operation, ultimately contributing to the success of the offshore wind industry.
The Future of Offshore Wind: A Symbiosis of Man and Machine
The synergy between drones and advanced PCBAs is driving innovation in offshore wind turbine inspections. As the industry continues to expand, the development of cutting-edge PCBAs will be instrumental in maximizing the potential of drone technology and accelerating the transition to a clean energy future.
Related Topics
Drone PCBAs: Tackling Sensor Integration for Defense & Beyond
Understanding the challenges and best practices in creating sophisticated sensors for real-time data collection for different industries.
How to Combat Signal Integrity Issues in High-Speed Drone PCBAs
Learn how to prevent signal integrity of drones that could compromise circuit stability and overall performance.
The Future of UAV Design
We'll discuss where unmanned aerial vehicles (UAVs) technology currently stands and where it may go.
Need high-quality PCBAs for your next drone build?
Get an instant quote nowAbout MacroFab
MacroFab offers comprehensive manufacturing solutions, from your smallest prototyping orders to your largest production needs. Our factory network locations are strategically located across North America, ensuring that we have the flexibility to provide capacity when and where you need it most.
Experience the future of EMS manufacturing with our state-of-the-art technology platform and cutting-edge digital supply chain solutions. At MacroFab, we ensure that your electronics are produced faster, more efficiently, and with fewer logistic problems than ever before.
Take advantage of AI-enabled sourcing opportunities and employ expert teams who are connected through a user-friendly technology platform. Discover how streamlined electronics manufacturing can benefit your business by contacting us today.