MacroFab Blog
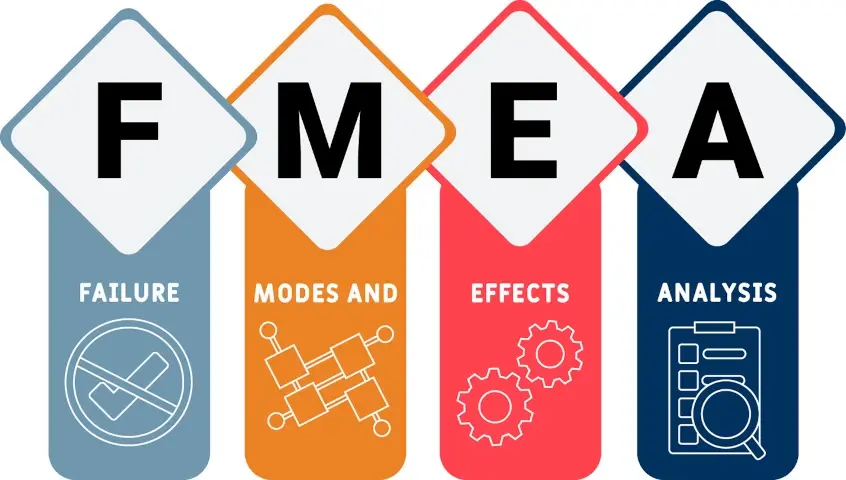
Electrical engineers are no strangers to the challenges posed by printed circuit board assembly (PCBA) processes. From complex manufacturing steps to strict industry standards and tight deadlines, every stage presents an opportunity for failures to emerge, impacting both product reliability and cost efficiency.
Fortunately, a powerful tool can help you address these challenges head-on: Failure Modes and Effects Analysis (FMEA). FMEA is a systematic approach used to identify, prioritize, and manage potential failure modes in a product or process before they occur.
By integrating FMEA into the lifecycle of a PCBA project, teams can strengthen their risk management strategies, streamline resources, and ultimately deliver a more reliable, safe, and costeffective product to market.
Let’s dive in and explore how FMEA analysis can make a significant difference in managing risks and reducing PCBA failures and product rejection ratios.
Key Points
• Failure Modes and Effects Analysis (FMEA) is a powerful tool that can help manage
potential failure modes in a product or process before they occur.
• By integrating FMEA into the lifecycle of a PCBA project, teams can strengthen their risk management strategies and deliver a more reliable, safe, and cost-effective product to market.
• FMEA is a systematic, proactive method to identify potential failure modes in a product, process, or system and their causes.
• FMEA involves assessing each failure mode based on its severity, occurrence, and detection ratings to calculate a Risk Priority Number (RPN).
• FMEA helps improve quality, reduce costs, enhance design, boost company image and competitiveness, define corrective action, and list all possible failures and their effects on operational success.
• Failure modes can occur at every stage of the PCBA process and can have severe consequences for the final product’s quality and reliability.
Understanding FMEA Analysis
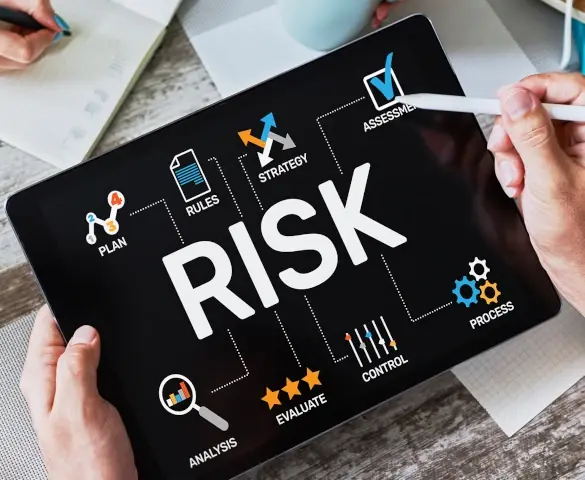
Risk analysis is a critical process for any project. It aims to answer two questions: “ What can go wrong?” and “If something does go wrong, what is the probability of it happening and what are the consequences?” FMEA is a powerful methodology used to tackle these questions. It was originally developed by the U.S. military and then adopted by NASA. Manufacturing industries commonly use it today.
FMEA is a systematic, proactive method to identify potential failure modes in a product, process, or system and their causes. Once identified, each failure mode is assessed based on its severity, occurrence, and detection ratings. These ratings are then combined to calculate a Risk Priority Number (RPN), which helps prioritize actions to reduce risk.
- Severity: the impact of a failure on the system, customer, or end-user.
- Occurrence: The probability of the failure mode happening.
- Detection: The likelihood of detecting the failure mode before it impacts the system or enduser.
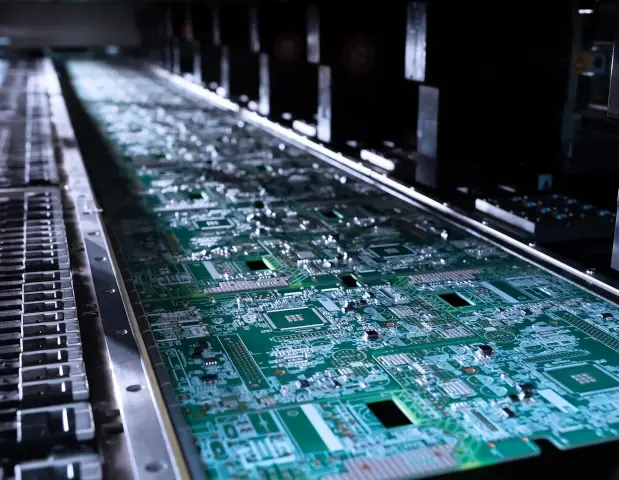
You might think of FMEA as a weather forecast for product development—it gives you a headsup on potential storms brewing, allowing you to prepare and adapt your strategies accordingly.
To uncover these potential failure modes or “storms,” you’ve got two main strategies at your disposal. First, you can turn to historical data, analyzing similar products, warranty data, customer complaints, and any other relevant information to define failures.
Secondly, you can employ techniques like inferential statistics, mathematical modeling, simulations, and reliability engineering to pinpoint and define those failures.
Start by assessing the risks of identified failure modes based on these factors:
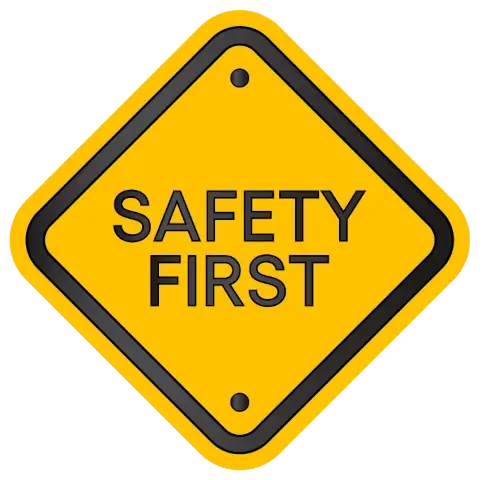
- Safety: Prioritize risks that could lead to injuries, as they are the most severe consequence of failure.
- Downtime impact: Evaluate the effects of failure on system downtime.
- Repair planning: Consider repair time, maintainability, costs, and necessary tools.
- Accessibility: Think about hardware items that need to be removed to access a failed component, keeping in mind evolving environmental laws and regulations.
So, why should you conduct FMEA? Embracing this approach offers several key advantages:
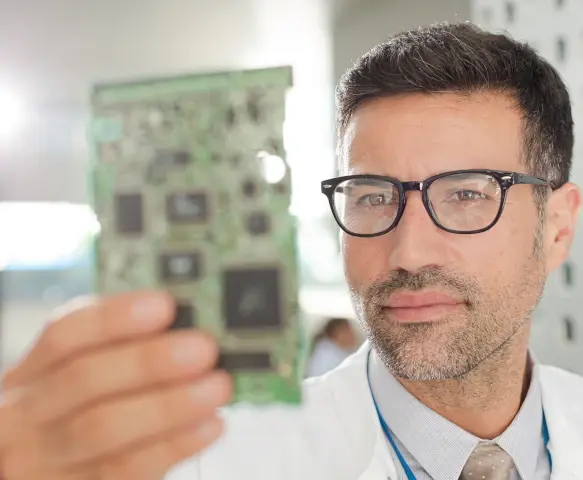
- Improved Quality: FMEA spotlights areas where controls and detection methods can be reinforced, leading to higher quality and greater customer satisfaction.
- Reduced Costs: Catching potential issues before they escalate saves time and money on redesigns, rework, and warranty claims.
- Enhanced Design: FMEA helps you choose the best system design and identifies alternatives with high reliability and safety potential early on.
- Boosted Company Image and Competitiveness: A solid risk management process can improve your reputation and give you an edge over competitors.
- Defined Corrective Action: FMEA helps outline the necessary steps to rectify identified issues.
- Comprehensive Failure Listing: This method ensures all possible failures and their effects on operational success have been considered, which aids in error identification and prevention.
With a more solid foundation of FMEA analysis under your belt, let’s go over the specific potential failure modes that can occur in a typical PCBA process.
Overview of Typical PCBA Process Functions
Manufacturing PCBAs is a complex process that consists of multiple stages, each with its unique potential failure modes and causes.
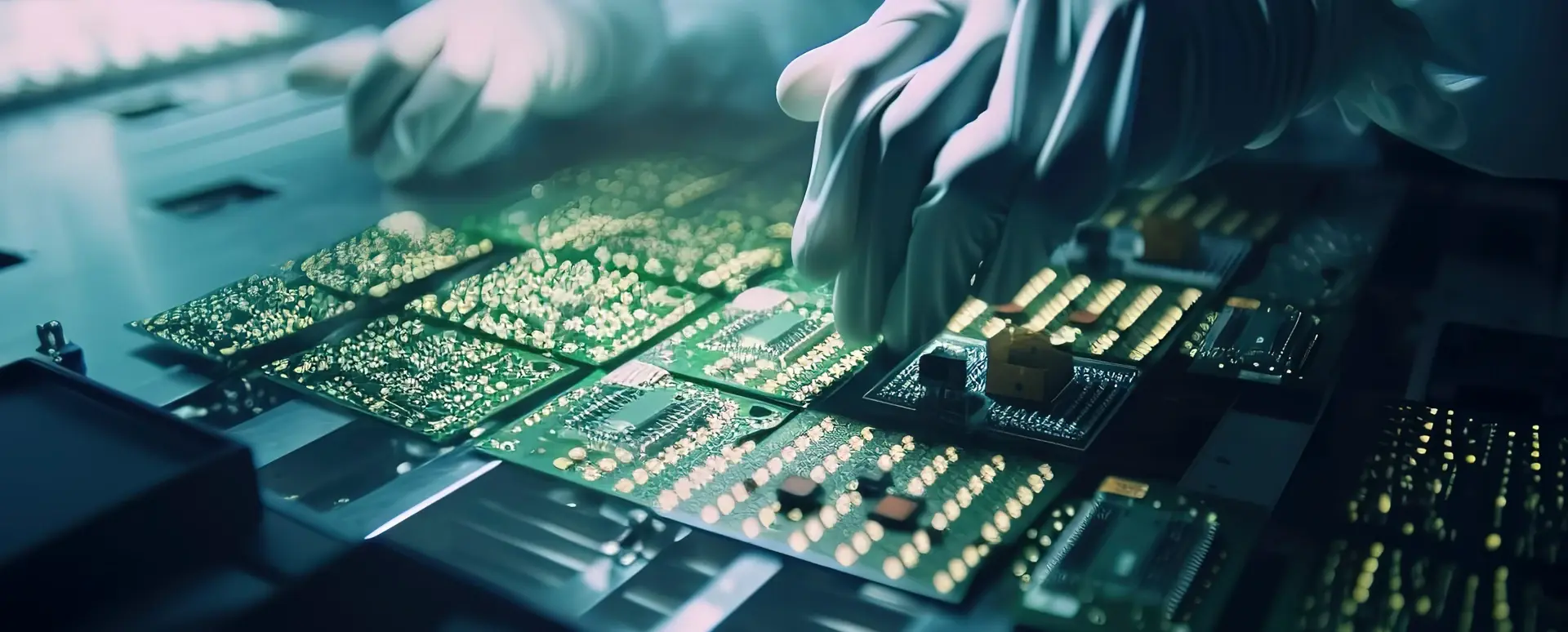
Let’s take a closer look at each stage’s significance in the overall PCBA process:
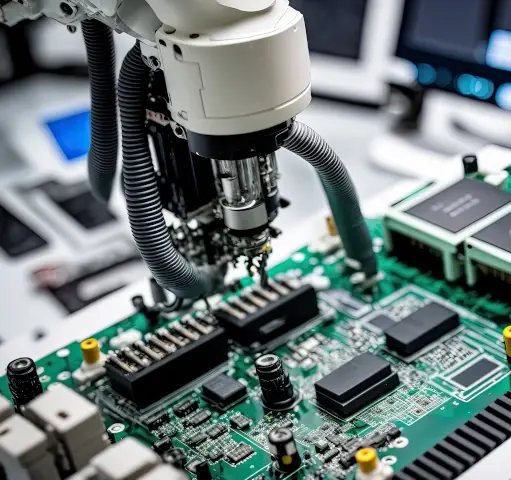
- Design and material procurement: The design stage involves developing a schematic of the circuit, selecting components, and determining how the circuit will be assembled.
- Fabrication: The PCBA is manufactured using the design specifications.
- Assembly: Components are added to the PCB design according to the specifications.
- Inspection: This involves visually inspecting the PCB assembly to ensure it meets the design specifications and standards.
- Testing: Here, the PCBA undergoes various tests to ensure it works correctly and meets the required standards.
Identification of Potential Failure Modes for Each Process Function
A failure mode refers to a component or system failing to perform its intended function. In the context of PCBA, failure modes can occur at every stage of the process. They can have severe consequences for the final product’s quality and reliability.
Let’s take a closer look at the types of failure modes that can occur in each stage of the PCBA process:
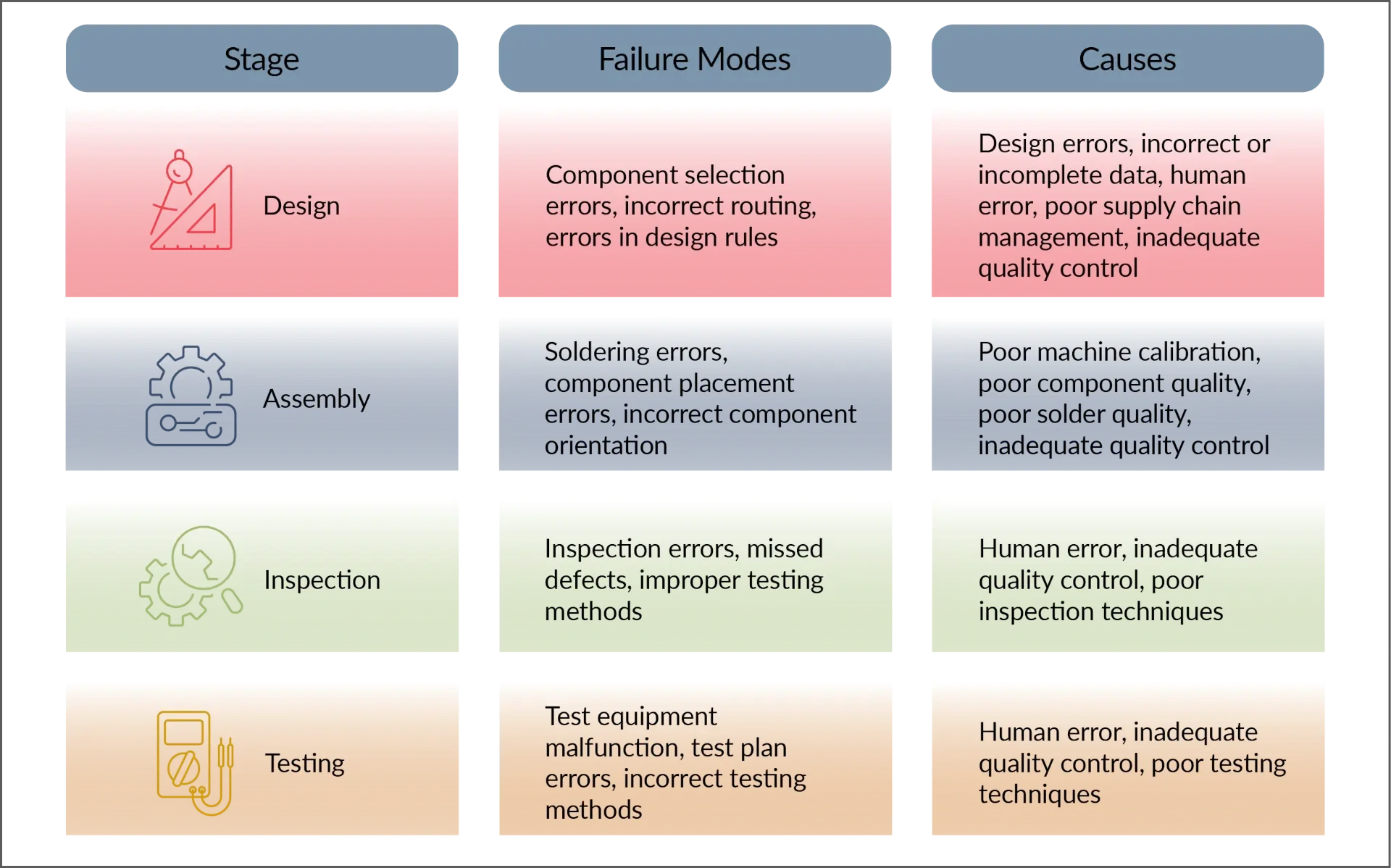
With the help of FMEA, you can list all possible failure modes and their causes at each process step during PCB manufacturing and evaluate their impact on product performance. And by considering the causes of each failure mode and designing appropriate solutions, you can significantly reduce the likelihood of these issues occurring during production.
When aiming to ensure quality and reliability in the production process, partnering with a contract manufacturer that emphasizes quality analysis is crucial. A proficient contract manufacturer will deploy rigorous process controls, including Statistical Process Control (SPC) and Design for Manufacturability (DFM) analysis, to enhance product quality and reduce the likelihood of defects.
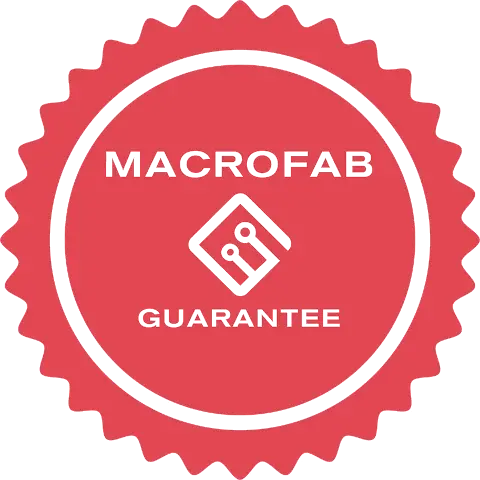
Further, a CM dedicated to quality will invest in advanced inspection technologies like Automated Optical Inspection (AOI) and X-ray inspection, to identify and rectify defects during the production process. The implementation of stringent quality management systems, such as ISO 9001 is also essential in meeting and maintaining required industry standards.
By collaborating with a manufacturer that consistently demonstrates a commitment to quality through continuous process improvement and the adoption of industry best practices, you can trust that your products will meet the highest performance benchmarks and offer enduring value to your customers.
Managing Risk
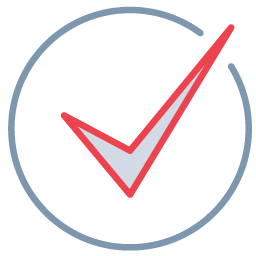
Checkpoint
Fostering a culture of continuous improvement encourages team members to contribute ideas and solutions that lead to better products.
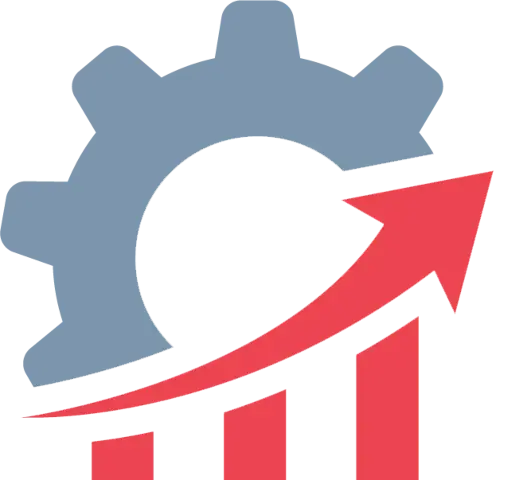
Understanding and addressing risks in the PCBA process is critical for delivering high-quality and reliable products. FMEA is a well-rounded approach to risk management that involves four main steps:
- Identifying and Understanding Failure Modes
A comprehensive understanding of each failure mode’s potential causes and effects is key to implementing appropriate mitigation strategies at every stage of the PCBA process. Thorough research, consultations with experts, and analysis of data gathered from past projects contribute to building a solid foundation for risk management. - Prioritizing Failure Modes
It’s essential to prioritize failure modes based on their potential impact on the final product, considering cost implications, customer dissatisfaction, and safety concerns. By assigning a risk priority number (RPN) to each failure mode, it becomes easier to categorize and prioritize potential issues, enabling a focused and efficient approach to risk management. - Choosing a Strategy
Various strategies can be employed to manage the risk associated with each failure mode. Process improvements, design changes, and material modifications are examples of actions that can be taken to minimize risks and ensure the quality and reliability of the final product.
Conclusion
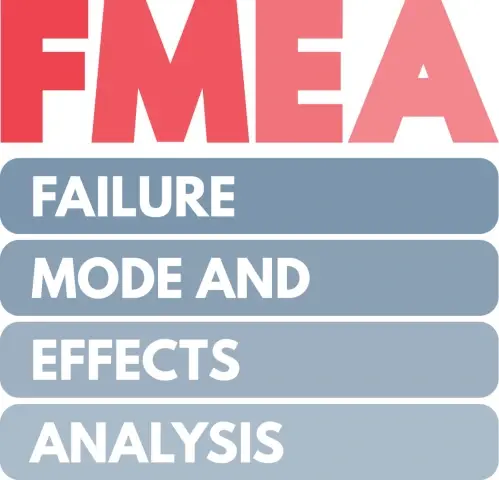
Navigating the potential pitfalls of running a business requires careful planning and risk assessment. One misstep can trigger a chain reaction of negative outcomes that threaten to capsize the entire enterprise. Just as a captain relies on a map to navigate uncertain waters, business leaders turn to FMEA for guidance in charting a safe course forward.
Embracing FMEA analysis in the PCBA process is not just an option but a necessity for organizations that genuinely care about quality and reliability.
By systematically identifying and addressing failure modes and their causes, companies can manage risks efficiently and reduce PCBA failures. This continuous improvement process demonstrates customer focus while adhering to industry standards, resulting in greater customer satisfaction and long-term success.
Related Topics
Struggling with Inflexible PCBA Manufacturing? MacroFab's Got Your Back.
Many electronics designers struggle with systems that demand complete data and specific formats upfront. Wouldn't it be great if there was a better way?
Fab Insights: HASL vs ENIG
Choosing the right surface finish for a PCBA can be tricky. HASL and ENIG differ in their methods of coating printed circuit boards.
How Do QFN Packages Compare to Other Surface Mount ICs?
This article aims to arm electrical engineers and PCBA designers with comprehensive insights into the QFN package.
Learn More About Risk Management.
Download “Engineering Essentials: The PCBA Design Handbook” Today.
About MacroFab
MacroFab offers comprehensive manufacturing solutions, from your smallest prototyping orders to your largest production needs. Our factory network locations are strategically located across North America, ensuring that we have the flexibility to provide capacity when and where you need it most.
Experience the future of EMS manufacturing with our state-of-the-art technology platform and cutting-edge digital supply chain solutions. At MacroFab, we ensure that your electronics are produced faster, more efficiently, and with fewer logistic problems than ever before.
Take advantage of AI-enabled sourcing opportunities and employ expert teams who are connected through a user-friendly technology platform. Discover how streamlined electronics manufacturing can benefit your business by contacting us today.