MacroFab Blog
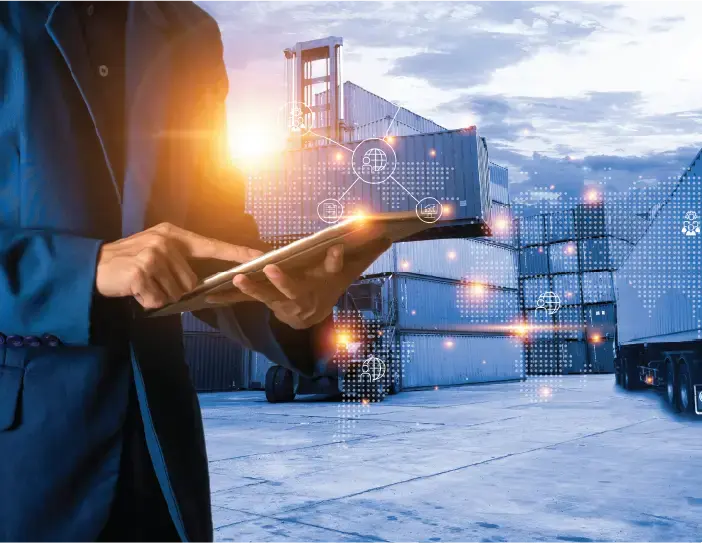
The reality of the global electronics supply chain has shifted dramatically in the past decade, but the supply chain workforce is struggling to catch up. Organizations are focused on being flexible, adaptive, innovative, and resilient, and younger or less traditional candidates, such as women and people of color, may be positioned to bring these traits to the table.
“The challenge I am facing is that we have a lot of jobs and I cannot get enough students into this area. It doesn’t have the same level of visibility to the young student,” said Daniel Lin, Director of the Supply Chain Management Institute and an Associate Professor of Supply Chain Management at the University of San Diego School of Business. “We need to agitate people that supply chain can be a career.”
Measuring the Gap
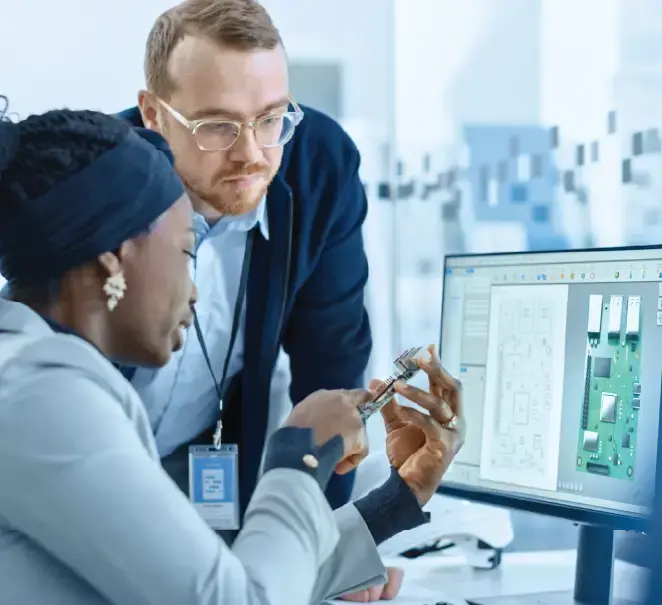
As an industry, we’ve been talking about a supply chain talent gap for at least a decade. As of 2018, one Deloitte study found that the skills gap may leave an estimated 2.4 million positions unfilled between 2018 and 2028, with a potential economic impact of 2.5 trillion.
There are reasons for that: supply chains are increasingly complex and global, and the role now entails having knowledge of an expanding array of digital and physical technologies.
As a function, the supply chain has gone through a metamorphosis from a primary focus on the cost and lead times of procuring goods to being a strategic function that proactively manages a variety of interconnected, non-linear issues. It is much bigger than simply getting the right product to the right location at the right time for the right price. For many organizations, a well-run supply chain is a strategic differentiator.
Further, recent research from iCIMS, a talent cloud company, demonstrates that manufacturing and technology jobs are the hardest to fill. The average number of days to fill a position is 47 days for manufacturing and 49 days for technology, compared to 43 days for finance and 39 days for healthcare.
On a brighter note, these positions also get more applications per job than any other. Specifically, manufacturing jobs get about 24 applications, technology gets 27, healthcare jobs get 15, and finance gets 23. Clearly, technology-driven manufacturing organizations have challenges but they also have some advantages.
Start Early, Talk Often
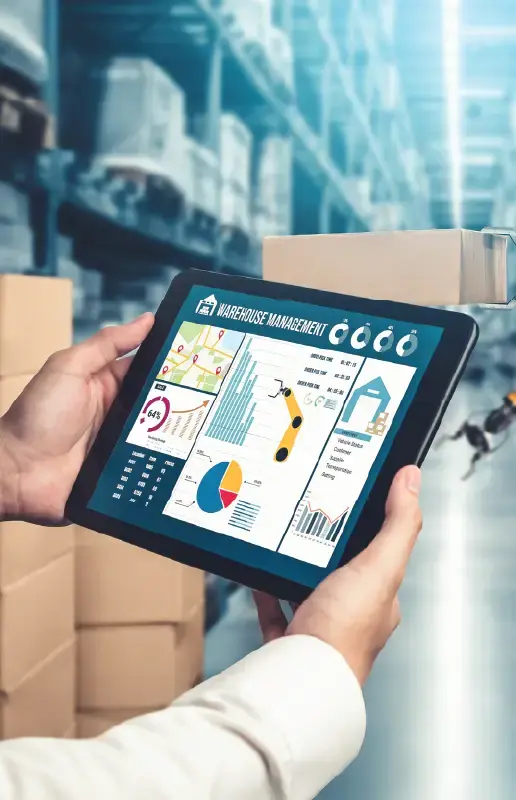
Organizations that want to build a strong supply chain need to start early and consider long-term strategy. “You have to start with the pipeline,” said Lin. “You need diverse input.” That means raising awareness among students early and often and encouraging them to focus on science, technology, engineering, and math (STEM) as early as middle school and high school.
For some organizations, sponsoring a robotics team at a local school may be an approach. As an example, since 2014 distributor Mouser Electronics has been a continuous sponsor of the FIRST Robotics Competition, an event that attracts 100,000 high school students across nearly 3,900 teams worldwide. Another option is to identify a local college or university with a supply chain program and offer internships. “It’s a great opportunity to show potential workers that you can do cool stuff in the supply chain,” said Lin.
Winning in a Competitive Race
So what can organizations do to secure the necessary talent? Currently, poaching from organizations with a strong supply chain roster seems to work as a go-to strategy. That, however, is not sustainable—and not really helpful to the industry overall. Instead, organizations need to think about more creative ways to identify and retain supply chain talent.
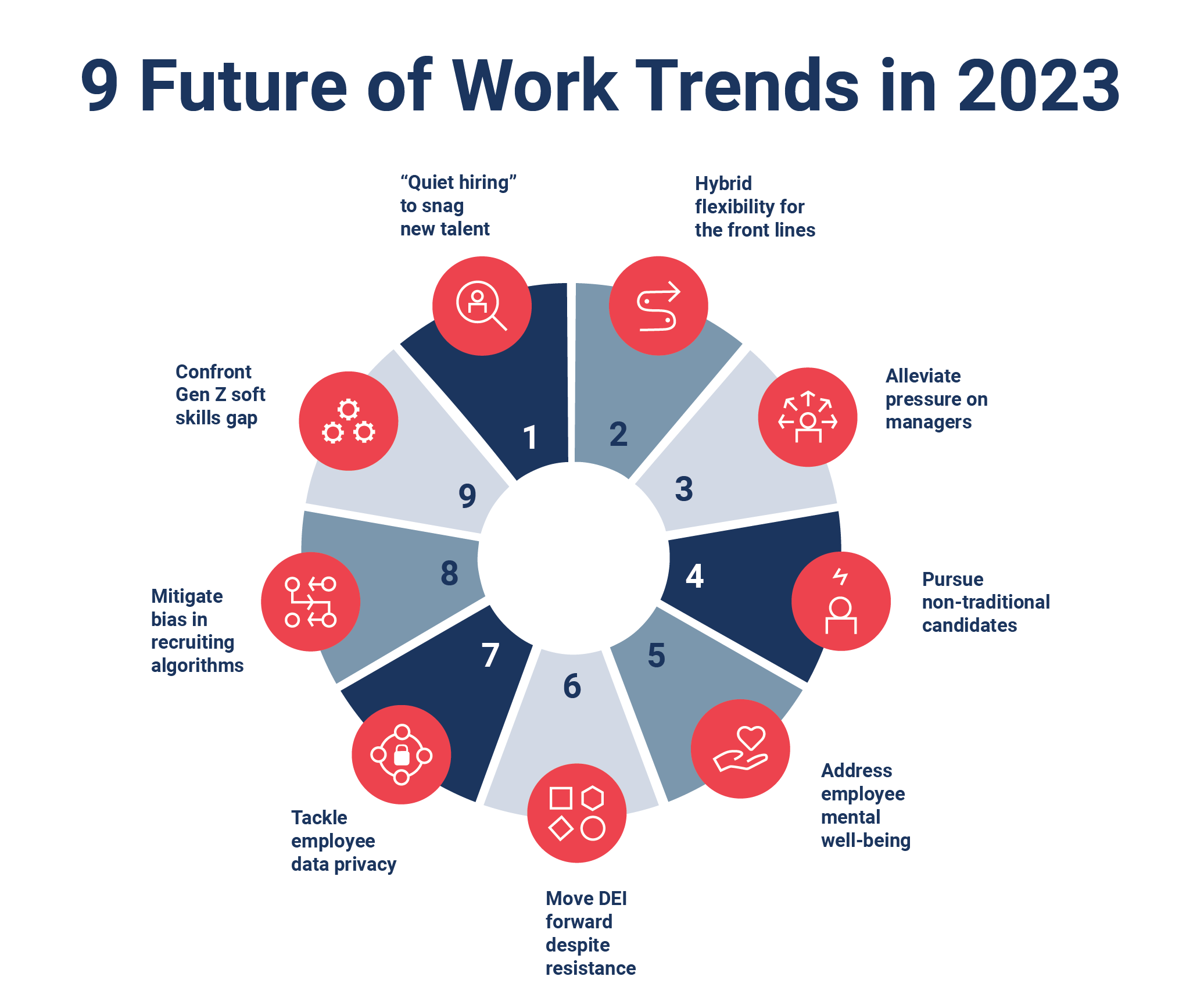
Figure 1: Many of the future work trends identified by recent Gartner intelligence point to the need to get smart about identifying and nurturing talent. This is particularly true for supply chain workers. (Image source: Garter )
Closing the supply chain gap will take time and sustained effort at both the industry and the organizational levels. It will require a multi-pronged set of best practices. Here are a few that need to be on the list.
Look both inside and outside the organization.
- Smart organizations should make sure that those who are interested in becoming supply chain professionals have clear internal pathways. If engineers are easier to find than supply chain pros, encouraging the tech-savvy to embrace a new career path can be a good way to go. This entails supporting training and skills acquisition. By keeping an eye out for those employees who want a new challenge, OEMs can build a strong supply chain.
Be a good place to work.
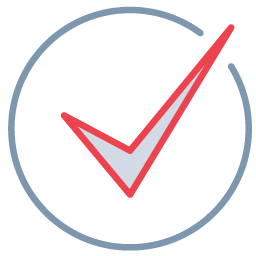
Checkpoint
Keeping a robust supply chain workforce entails not just hiring, but also retaining great talent.
- Keeping a robust supply chain workforce entails not just hiring, but also retaining great talent.
The newest waves of workers are striving for work/life balance, so they may have a different list of attributes they are looking for in a career. Consider being creative about flexible schedules, job sharing, working from home, and paid leave. These things matter. Recent research from McKinsey found that if given the opportunity for flexible work arrangements, 87 percent of employees took advantage of it.
Having a strong corporate culture and processes also goes a long way to making employees feel comfortable. Meanwhile, avoiding a “toxic” corporate culture (where disrespectful, non-inclusive, unethical, cutthroat, and/or abusive behavior is tolerated) is ten times more important to workers than compensation, according to Sloane MIT.
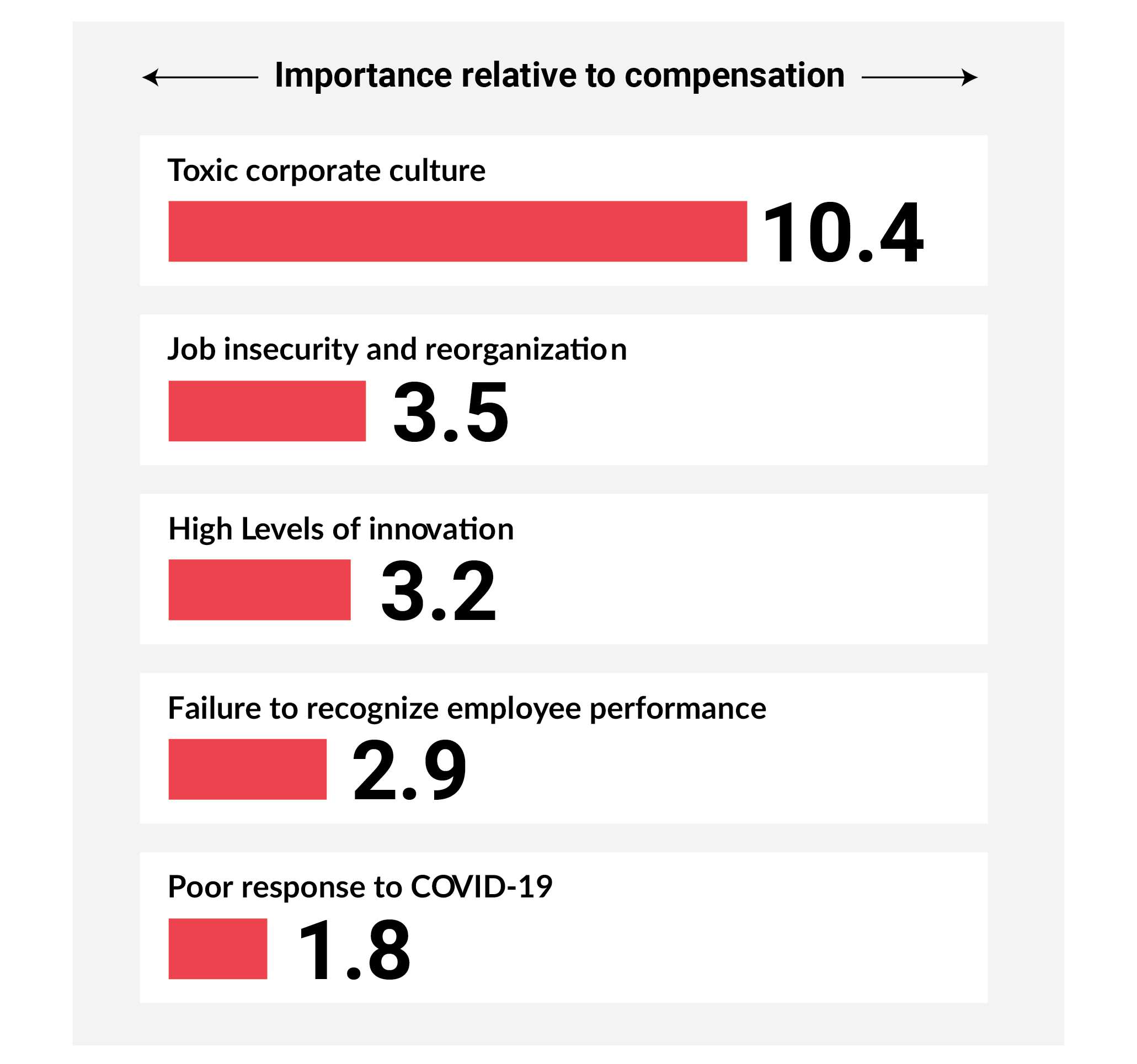
Figure 2: Shown are the top five drivers of attrition, based on a study by MIT Sloan researchers of more than 170 companies. (Image source: MIT Sloan)
Think outside the box.
- Increasingly, non-traditional paths are becoming…. more traditional.
Employees are more likely to consider a mid-career shift (see above). Some employers are also looking at new pipelines—whether it is partnering with universities that offer a supply chain degree to get priority with newly-minted graduates, or partnering with specific groups—such as military veterans—to find potential employees that have the requisite skills, even if they don’t have prior experience.
Raise the profile of supply chain opportunities.
- Supply chain as a career is more than bills of materials and spreadsheets. Organizations need to do a better job of helping potential employees know why a supply chain career is cool.
Invariably, supply chain positions play a crucial role in ensuring the success of an organization. Often, the field offers a chance to work with colleagues and partners in other countries and with various cultural backgrounds.
For those who want to make a difference in the world (of keen interest for many younger employees), supply chain managers are integrally engaged in supporting fuel-efficient shipping and eco-friendly product manufacturing. To this end, the supply chain is leveraging cutting-edge technologies, including artificial intelligence (AI), 3D printing, augmented reality, the Internet of Things (IoT), and blockchain, just to mention a few. Plus, there’s lots of opportunity for growth.
Conclusion
The supply chain is shifting and the means by which we hire has to evolve right along with it. Being a supply chain manager is exciting, strategic, and fulfilling as a career—and those with this skillset are critical to the success of the organization. It’s time to get the word out.
Related Topics
Preparing for Potential Supply Chain Disruptions During Lunar New Year
This blog discusses on how to prepare for unexpected events for global supply chains such as the dockworker strike in preparation for Lunar New Year.
How Opaque Electronics Manufacturing Costs Stifle Innovation
This blog discusses how MacroFab as a partner can give you the power to launch a groundbreaking product with confidence in this fast-paced world.
MacroFab vs. PCB Manufacturing Brokers: Why Direct Matters
This blog explores the key differences between MacroFab and manufacturing brokers, and why direct manufacturing is the optimal choice for PCBA needs.
Get Supply Chain support from MacroFab
MacroFab Supply ChainAbout MacroFab
MacroFab offers comprehensive manufacturing solutions, from your smallest prototyping orders to your largest production needs. Our factory network locations are strategically located across North America, ensuring that we have the flexibility to provide capacity when and where you need it most.
Experience the future of EMS manufacturing with our state-of-the-art technology platform and cutting-edge digital supply chain solutions. At MacroFab, we ensure that your electronics are produced faster, more efficiently, and with fewer logistic problems than ever before.
Take advantage of AI-enabled sourcing opportunities and employ expert teams who are connected through a user-friendly technology platform. Discover how streamlined electronics manufacturing can benefit your business by contacting us today.