MacroFab Blog
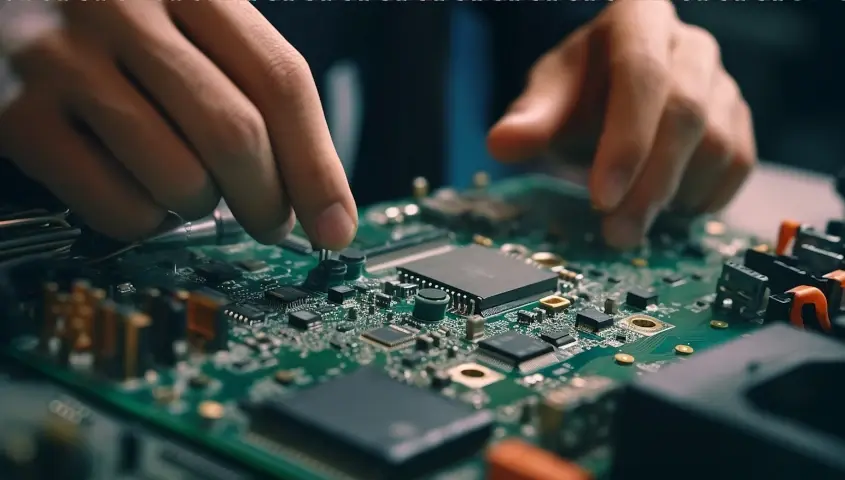
Every great electronics product stems from a visionary idea.
What happens next varies depending on the business. Savvy electronics developers prioritize a thorough development process, focusing on creating high-quality PCB prototypes using trusted manufacturing partners to identify and resolve potential issues early. These teams understand that prototypes are critical not just for testing functionality but for setting the foundation for production-ready designs.
However, some companies focus more on meeting aggressive turnaround times than ensuring quality in PCB fabrication. While this might seem efficient, it often results in hidden expenses in cheap prototypes—expenses that emerge through redesigns, failures, or missed deadlines, ultimately overshadowing any initial cost savings.
PCB prototypes are more than just early iterations of an idea; they are the first physical representation of your product. Prototypes should reflect the same quality standards you expect in production. A strong prototyping process enables rapid, low-volume iteration cycles while maintaining the integrity required for scaling to high-quality manufacturing.
Yet not all manufacturers have the expertise or willingness to support these early-stage efforts. Some specialize only in prototyping and cannot transition to production, leaving you without a clear path forward. Others attract business through cost-cutting measures that compromise quality, leading to significant issues later.
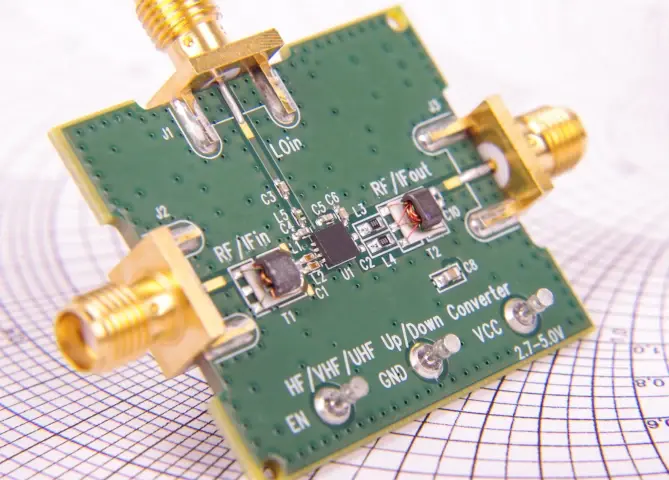
The Risks of Price-Cutting Tactics
Price-cutting strategies are common in prototype-only manufacturing facilities aiming to maximize low-volume orders quickly. However, the age-old triple constraint triangle—fast, good, or cheap—holds true: you cannot have all three simultaneously.
This explains why cutting corners during the PCB prototyping phase can cause problems in the future. A fast, cheap prototype won’t have the quality you’re looking for. These prototypes frequently fail to account for the cost analysis of PCB prototypes, where overlooked costs—such as additional testing, rework, or production delays—quickly escalate.
Besides the manufacturing process, cheap PCB prototypes can pose enormous obstacles for companies in the market – resulting in poor brand reputation, decreased brand loyalty, and a shrinking market share. Customers remember subpar products, and once you’ve lost a customer, regaining their trust is challenging. Electronics companies must carefully evaluate the quality vs. cost in PCB design to avoid sacrificing long-term reliability for short-term savings.
In this article, we’ll dive into why it’s crucial to construct high-quality PCB prototypes from the start. We’ll highlight specific areas where electronics manufacturers tend to fall short, encompassing:
- Material quality
- Testing and verification
- Design detail
- Soldering quality
- Compatibility
There is little margin for error on any of these fronts. Success in electronics manufacturing requires being both careful and agile, a combination that is difficult to achieve. But investing in this, even if it implies spending more upfront on appropriate materials and robust processes, is worth it to avoid the pitfalls of a cheap PCB prototype.
Where Cheap PCB Prototypes Fall Short
Material Quality
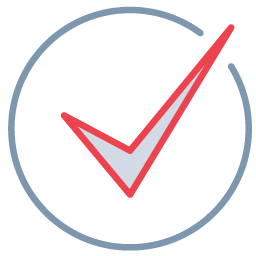
Checkpoint
Customers remember subpar products, and once you’ve lost a customer, regaining their trust is challenging.
The first area where electronics manufacturers may compromise during prototyping when creating a cheap PCB prototype is material selection. A less experienced PCB designer may be led to choose substandard materials during prototyping to minimize costs. This could translate into choosing inferior or even counterfeit components. Furthermore, if your cheap prototyping shop does not offer DFM (design for manufacturing), then you may unknowingly choose materials that create performance or reliability issues, or that do not meet your end regulatory requirements.
Interestingly, these subpar materials may not expose their limitations right away. They might suffice in limited use cases or short-term applications but may falter over time. Attributes like durability and thermal resistance can decline, increasing the likelihood that your PCBA will overheat with regular use. These issues will likely only surface after you have completed full production and shipped your product.
Moreover, electrical performance can deteriorate when inferior materials are employed. Thus, components have to work overtime to compensate. This overcompensation results in extra heat generation, leading to a multitude of subsequent problems.
Listen to this classic episode of Circuit Break to find out ways of controlling your design costs while keeping quality to the max.
Lack of Testing and Verification
Skimping on testing during the prototyping phase is another major source of hidden expenses in cheap prototypes. It’s easy for electronics engineering teams to overlook testing and verification as they focus on achieving certain functionality. By failing to test a PCB in its entirety across multiple iterations, design errors can slip through, resulting in less reliable designs. A reliable manufacturing partner emphasizes testing and verification across all stages of development. Design tweaks—even seemingly minor ones—can impact functionality elsewhere in the board.
Design for Manufacturability (DFM) checks and other iterative testing should be prioritized. This prevents issues from compounding, saving both time and money.
Design Shortcomings
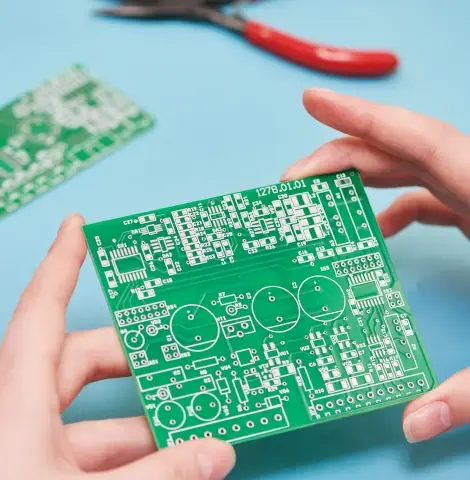
Design shortcomings are another common problem of cheap PCB prototyping. How likely is it that the least expensive fab house will point out design problems to you? Not likely. The cost of that service cuts into their profits.
PCBs should be of proper thickness for the anticipated use case. They should have wide enough trace widths to handle the projected electrical activity across the board. Design considerations should also incorporate testing and ensure that testing equipment can efficiently access all critical points.
Thermal management is another aspect that warrants careful thought - designers must proactively consider how to maintain the optimal temperature of their boards and components during peak usage. A fab house with an expert team may be able to point out thermal issues that you may have overlooked.
When left unchecked, design issues can cause damage to circuits or devices as a whole. Even in the early stages of materializing new product ideas, meticulous design reviews are vital. Engineering teams should evaluate and reevaluate designs constantly as things change, even during prototyping.
Soldering Challenges
Soldering challenges are a recurring theme with PCB prototypes. It’s not uncommon to encounter difficulties due to a complex soldering process, potentially resulting in compromised components and connection issues. The prototyping stage is not exempt from challenges such as cold soldering and moisture intrusion during the soldering process.
Weak connections between components, an inherent risk in any intricate electronics work, can lead to electrical shorts and circuit malfunctions. In some instances, soldering irregularities could even create safety hazards for end users.
Ensuring that this doesn’t occur at scale is critical and highlights the importance of meticulous soldering during prototyping. Furthermore, working with the same CM for both prototyping and production at scale is advantageous, since any issues that surface can be resolved before moving to those higher production levels.
Compatibility Issues
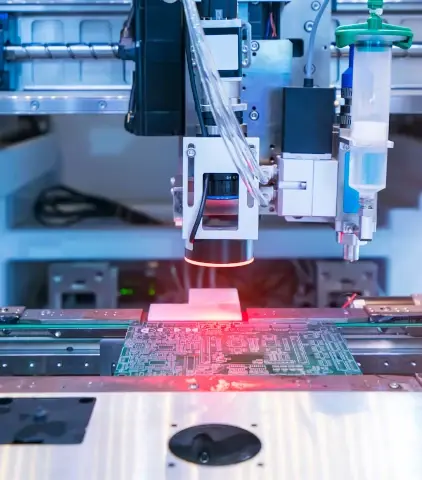
Additionally, managing compatibility can pose a formidable challenge during PCB prototyping. Overlooking compatibility factors might sometimes result in significant rework or redesign as the production process unfolds. Having to reassess and modify PCB designs can be resource-intensive in numerous ways.
It’s imperative from the outset that electronics designers evaluate factors such as electromagnetic compatibility and interference to confirm their PCBAs effectively manage electromagnetic energy. It’s also important that the selection of materials aligns with the intended use case, especially when the PCBAs are designed for harsh environments. Compact PCBAs destined for smaller enclosures require a balance in the selection of components and cooling parts.
In the end, working with an expert team that can identify and fix these problems during prototyping is beneficial to your product and leads to a faster and more cost-effective prototyping process.
The Ultimate Cost of a Cheap PCB Prototype
A low-cost PCB prototype might seem like a smart financial decision initially, but the hidden expenses in cheap prototypes—poor material performance, inadequate testing, design flaws, and production delays—can quickly outweigh any upfront savings. These oversights lead to wasted resources, increased development times, and long-term brand damage.
By focusing on quality from the beginning, companies can avoid the pitfalls of cheap prototypes. A comprehensive cost analysis of PCB prototypes—factoring in design, material selection, and production readiness—reveals that investing more upfront leads to better outcomes, including lower total costs over the product lifecycle.
High-quality prototypes build confidence in your product's safety and reliability, creating a strong foundation for success. The most expensive prototype is often the one you thought was "cheap." Instead, work with a quality team invested in your success and ensure your new electronics products are built correctly from the start.
Related Topics
MacroFab vs. PCB Manufacturing Brokers: Why Direct Matters
This blog explores the key differences between MacroFab and manufacturing brokers, and why direct manufacturing is the optimal choice for PCBA needs.
Ultimate Guide To PCB Schematics: Concept to Prototype
A comprehensive guide for navigating early design phases and utilizing schematics alongside Gerber and drill files during the PCB creation process.
How MacroFab Uses Clear Communication to Improve Your PCB Production Experience
This blog will discuss how MacroFab can help customers in their PCB production experience through clear communication in a high-octane environment.
Get Quality Prototypes from MacroFab
Turnkey PCBA PrototypingAbout MacroFab
MacroFab offers comprehensive manufacturing solutions, from your smallest prototyping orders to your largest production needs. Our factory network locations are strategically located across North America, ensuring that we have the flexibility to provide capacity when and where you need it most.
Experience the future of EMS manufacturing with our state-of-the-art technology platform and cutting-edge digital supply chain solutions. At MacroFab, we ensure that your electronics are produced faster, more efficiently, and with fewer logistic problems than ever before.
Take advantage of AI-enabled sourcing opportunities and employ expert teams who are connected through a user-friendly technology platform. Discover how streamlined electronics manufacturing can benefit your business by contacting us today.