MacroFab Blog
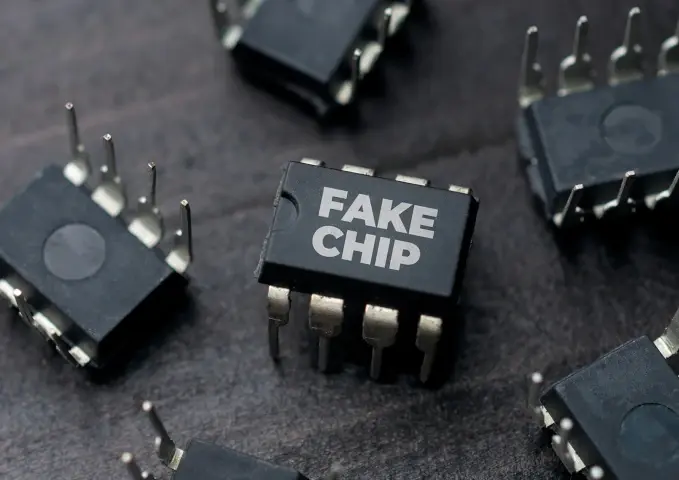
In electronics, counterfeiters have become more sophisticated, making it difficult for companies to identify fraudulent parts. In the midst of the shift, electronics developers face major challenges, particularly as they recover from a period when traditionally-sourced components were difficult to find.
Experts believe that counterfeit goods cost the global economy as much as $250B every year. It was reported in 2011 that 15% of the spare and replacement parts purchased by the Pentagon were counterfeit, not only jeopardizing national security but possibly putting American lives at risk.
Today, one in ten IT products sold may be counterfeit. It is common for counterfeit products to enter the legitimate sales stream; in fact, about two-thirds of counterfeit electronics are sold by reputable companies, with little awareness of the problem.
Curious how PCBA manufacturing contributes to national security? Read Securing the Nation: The Role of PCBA Manufacturing in the US} now.
Key Takeaways
• Counterfeit electronics parts cost the global economy up to $250B per year.
• 1 in 10 IT products sold may be counterfeit, with about two-thirds of counterfeit electronics sold by reputable companies.
• Counterfeit parts can be integrated into circuit boards due to complex and opaque electronics supply chains, lack of quality control, time pressures, availability issues, cost, or misrepresentation.
• Counterfeit components pose risks such as increased product failures, safety hazards, intellectual property infringement, and loss of revenue.
• Engineers must take an active role in blocking counterfeit components from entering the production process.
How do Counterfeit Parts Get Purchased?
As a result of the complex and opaque nature of the electronics supply chain, counterfeit parts can be integrated into circuit boards in a variety of ways. This is due to a number of factors, including
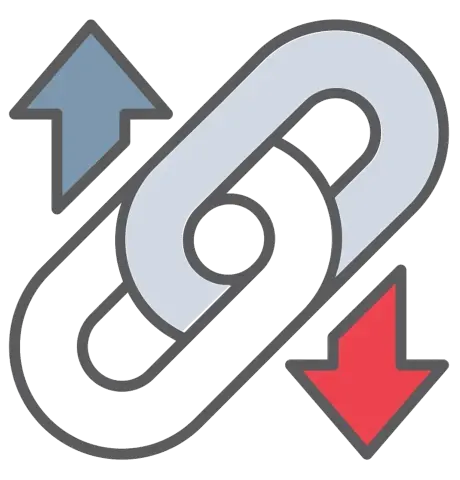
- Supply chain complexity. Multi-tier supply chains make it difficult to understand where parts originate from.
- Lack of quality control. Leaving testing and quality control to others can result in undesirable results. By enforcing proper QC standards, counterfeit electronic parts can be avoided.
- Time pressures. Buying parts under time pressure may lead some to consider buying from unvetted sources.
- Availability issues. During periods of shortage, counterfeit parts may become the only option available. Many may fall into the trap of believing that what they don’t know can’t harm them.
- Cost. The cost-conscious buyer finds counterfeit parts appealing because they are usually cheaper than genuine parts.
- Misrepresentation. Often, fake parts look and behave just like the real thing, so it is difficult for buyers to distinguish between the two. Sometimes visual inspections can prevent counterfeits, but other times electrical testing or X-ray inspection are required.
As counterfeits have become more prevalent, engineers are being asked to do more to prevent them from entering product builds. In this article, we’ll first touch on why counterfeit components are a serious problem for modern electronics developers. Then we’ll discuss ways to avoid counterfeit components in electronics manufacturing across product development.
The Dangers of Counterfeit Components
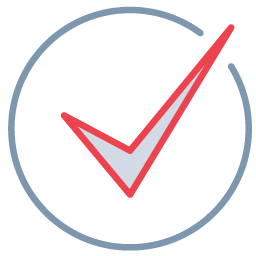
Checkpoint
There is a real and growing threat of counterfeit products in the electronics industry.
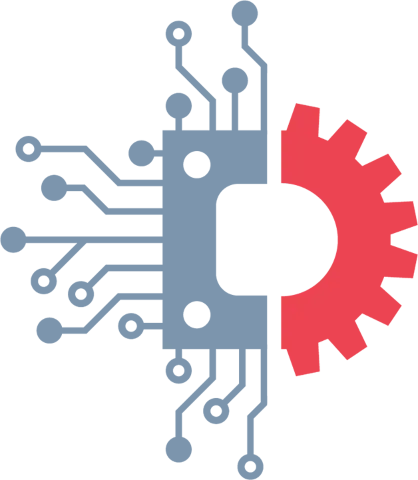
Counterfeit components are dangerous to companies and consumers for several reasons. These reasons include:
- Increased rate of product failures
- Safety hazards
- Intellectual property infringement (IP)
- Loss of revenue
Therefore, avoiding counterfeit components is not only financially beneficial – it’s paramount for long-term enterprise success. Let’s take a closer look at each issue.
Product Failures
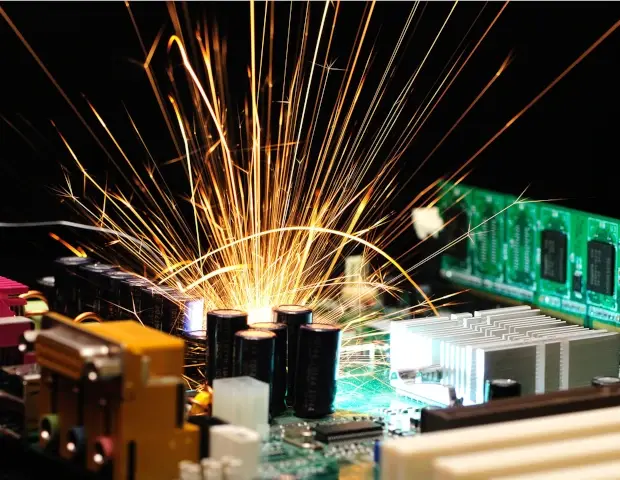
One of the more obvious downsides of counterfeit components is that they lead to product failures. This poses a commercial risk to business customers who depend on these products to deliver their own services. Moreover, it poses a financial risk to the company developing the technology because of reputational damage, litigation, warranty claims, and recall expenses.
To offset product failures caused by counterfeits, companies must produce higher volumes of goods in exchange for no incremental gain. Production efficiency comes down, and procurement teams must source additional components within a short period of time, which may further increase the chance that counterfeits enter the process. Such product failures lead to increased production costs and decreased profit margins as the company absorbs costs associated with fixing problems caused by counterfeit parts.
Safety Hazards
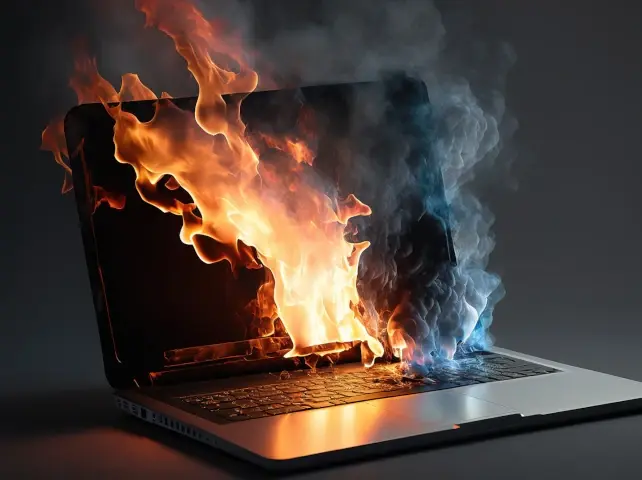
Depending on the nature of a product, counterfeit components can cause physical harm to users. Take counterfeit laptop batteries, for example. These parts can overheat and ignite, posing a clear threat to unsuspecting users and even to factory workers on production lines.
Additionally, the use of counterfeit components in medical devices and equipment can pose a serious risk to patient health and safety, as these products are used in critical medical procedures and treatments. In the worst-case scenario, the failure of a counterfeit component could result in serious injury or death, further emphasizing the importance of ensuring the quality and authenticity of all components used in these products.
In the third quarter of 2022, the number of US product recalls across all categories reached a 20-year high, according to Sedgwick Claims Management. As part of this report, the FDA provided guidance on how to protect advanced medical technology from cyberattacks, which could result in the death of a patient. There is a real and growing problem here.
Intellectual Property Infringement
Counterfeiting also falls under the IP infringement umbrella. IP theft is already a huge issue in the electronics world. Many countries, like China, don’t offer robust IP protections like the U.S., Canada, and Mexico do.
And yet, IP and brand protection are inexorably linked. Counterfeit parts can alter the final performance of a product, thereby deceiving consumers and detracting from the original intention of a product’s design.
Loss of Revenue
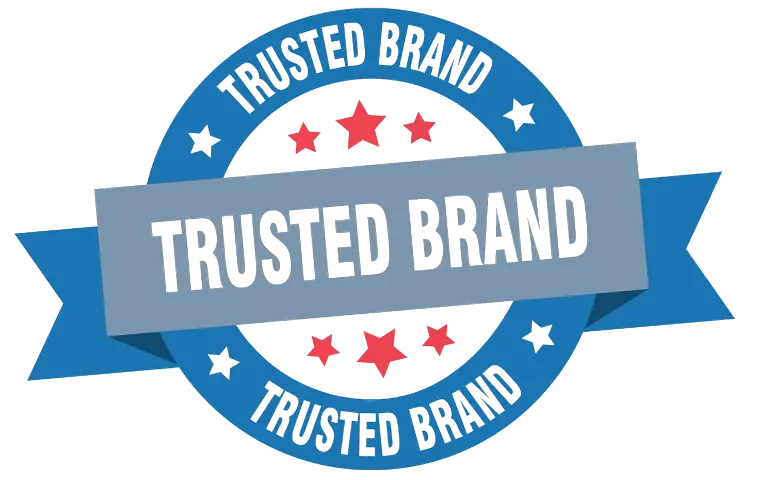
Counterfeiting is a major issue for electronics companies and can lead to significant financial losses. The use of counterfeit parts can result in product failure, which can have a negative impact on a company’s reputation and brand image.
Faulty counterfeit electronics can make customers lose trust in a brand, leading them to switch to competitor products. This leads to a decrease in sales and top-line revenue for the company, which can have a domino effect on the company’s financial performance.
The decrease in sales can impact a company’s operating margin, making it more difficult for the company to invest in high-quality electronics. This can further erode the company’s competitiveness, leading to a continuation of the downward spiral.
With fewer customers choosing their products, the company may struggle to maintain its market position, leading to long-term financial losses and a reduction in overall revenue.
Where Counterfeits Cause Harm
Counterfeits cause harm in three specific areas related to the electronics production process:
- Engineering design workflow
- Product viability
- Enterprise reputation
All three must be protected to ensure maximum product performance and efficiency.
Engineering Design Workflow
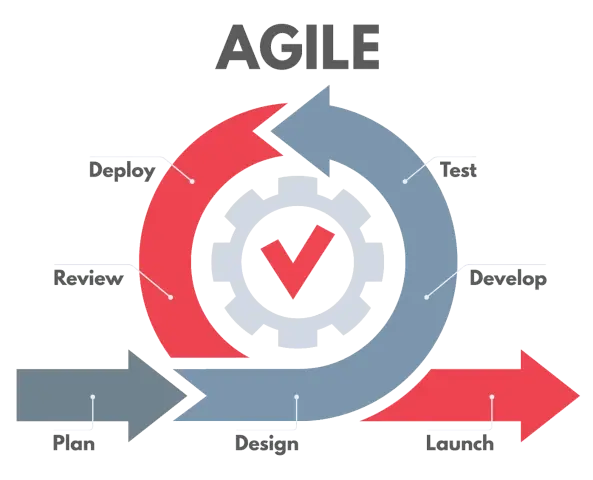
The engineering design workflow should be transparent, collaborative, and proactive. Stakeholders across the product development lifecycle should be in regular communication about marketplace conditions, enterprise goals, and current developments. This is how production remains agile and resilient in the age of disruption.
But counterfeit parts add chaos to the equation. They force teams to take shortcuts and go outside their standard operating procedures, increasing risk dramatically.
Product Viability
The use of counterfeit parts can also pose a risk to a product’s viability. It’s challenging to determine whether a product meets market demand and customer expectations when counterfeit parts are present within the design. A counterfeit part is more likely to fail, so it increases the likelihood of a product malfunctioning.
With the presence of counterfeit components, it becomes difficult to accurately assess the product’s success, as the product’s reliability and performance have been compromised.
Enterprise Reputation
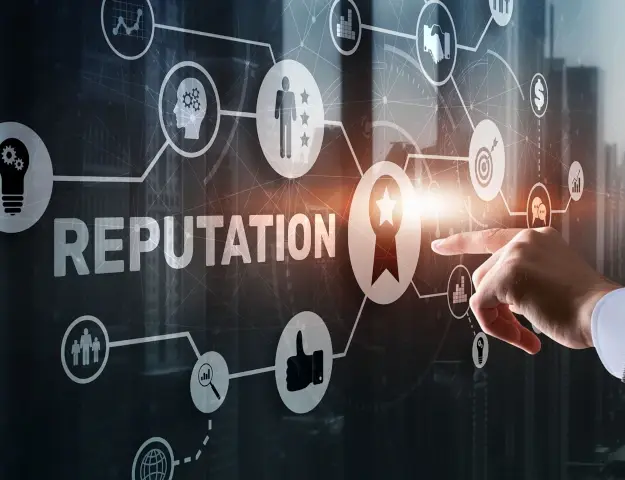
Finally, counterfeit components can hurt a company’s reputation. As alluded to previously, counterfeit parts lead to more product failures and safety hazards. When a product fails to fulfill its intended function, it is a mark against the company. And in the modern era, this information spreads quickly.
It’s getting harder for organizations to protect their reputations, and few enterprises work within markets free from competition. With so much data and so many substitute products available, it’s easier for potential customers to find a replacement product. The process of repairing a tarnished reputation is time-consuming, expensive, and difficult. Counterfeit components can set an electronics business back and even catalyze its downfalls.
How to Keep Counterfeit Components out of Company Designs
For all the reasons above, engineers involved in the electronics design process must take an active role in blocking counterfeit components from entering the production process. This primarily includes design, component, and purchasing engineers.
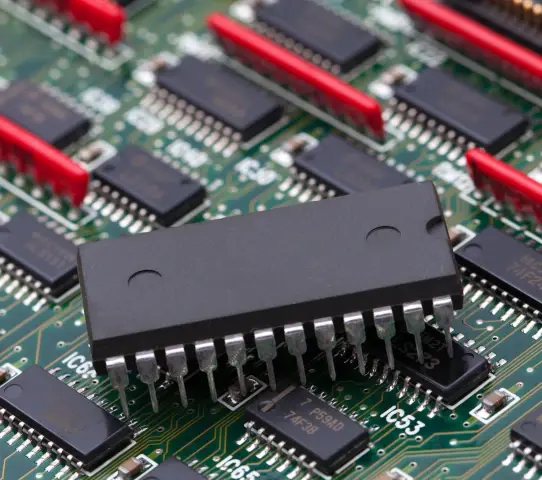
Especially for products with short life cycles, design engineers can reduce counterfeit risk by incorporating flexibility and modularity into designs. The more flexible and modular a design is, the easier it is to slot in a replacement part when the end-of-life stage approaches or if counterfeits find their way into production. As a result of a proactive approach like this, counterfeit components have less impact on the final outcome.
Component engineers can also mitigate counterfeit risk by informing design engineers of component options, alternatives, and availability. Knowing what’s on the market and planning ahead allows component engineers to make sure their organizations use reliable and accessible parts. They prevent businesses from having to make difficult future decisions should component supply dry up.
Additionally, purchasing engineers or procurement specialists should use authorized suppliers and allow sufficient time to conduct a thorough purchase process. While this isn’t always possible, encouraging component and design engineers to share designs early can alleviate the need for purchasers to explore options outside of trusted channels.
Partnering with an experienced supplier or trusted contract manufacturer who can also source components safely makes sense, as well, and provides a safe procurement channel. The key here is to look for organizations with ERAI membership that have access to risk assessment tools and reports on the current counterfeit marketplace. MacroFab is a proud member of ERAI.
There is a real and growing threat of counterfeit products in the electronics industry. To address this issue, design engineers, component engineers, and purchasing engineers must take proactive measures to ensure that the components used in their products are authentic. From implementing stricter supplier selection criteria to utilizing technology for product traceability, these key players can play a significant role in keeping counterfeit parts out of the supply chain and ensuring the quality and reliability of end products.
Related Topics
Preparing for Potential Supply Chain Disruptions During Lunar New Year
This blog discusses on how to prepare for unexpected events for global supply chains such as the dockworker strike in preparation for Lunar New Year.
Avoid PCBA Component Counterfeits: Questions to Ask Suppliers
A discussion on providing essential inquiries to make when selecting a component supplier, along with additional information to consider for each question.
Mapping Out a PCBA Supply Chain Strategy in Five Moves
Companies should create unique vendor relationships with numerous international suppliers due to the necessity of having to source components globally.
Learn More About Reducing Counterfeits in PCBA
Watch the On-Demand Webinar:
How to Maximize PCBA Design Efficiency with Reduced Redesign
About MacroFab
MacroFab offers comprehensive manufacturing solutions, from your smallest prototyping orders to your largest production needs. Our factory network locations are strategically located across North America, ensuring that we have the flexibility to provide capacity when and where you need it most.
Experience the future of EMS manufacturing with our state-of-the-art technology platform and cutting-edge digital supply chain solutions. At MacroFab, we ensure that your electronics are produced faster, more efficiently, and with fewer logistic problems than ever before.
Take advantage of AI-enabled sourcing opportunities and employ expert teams who are connected through a user-friendly technology platform. Discover how streamlined electronics manufacturing can benefit your business by contacting us today.