MacroFab Blog
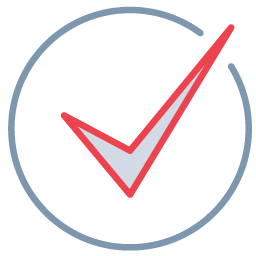
Checkpoint
Reshoring offers a solution to persistent problems of instability, lending companies the resilience needed to succeed now and into the future.
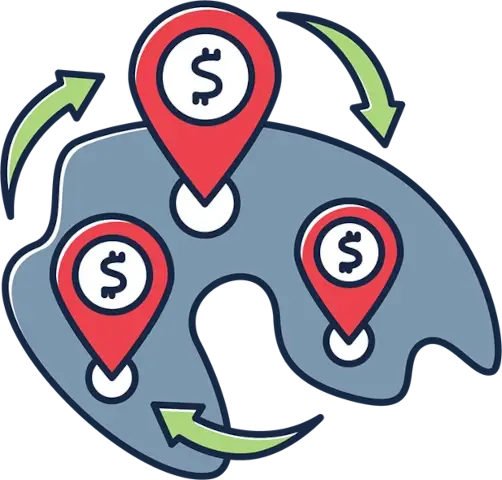
The idea of “Made in America” is once again appealing to many electronics companies. Today, manufacturers in China, India, and other nations have tremendous power over U.S. organizations. But by reshoring electronics production, leaders can regain control and fortify operations for the future.
But one big challenge stands in the way of reshoring – labor shortages. Although the worker shortage has affected many industries, skilled electronics manufacturing labor is particularly scarce right now. Labor shortages in the shipping, railroad, and logistics industries also make it hard for companies to deliver finished goods to customers.
Why, then, is reshoring gaining so much traction? Leaders know that reshoring offers a solution to persistent problems of instability, lending companies the resilience needed to succeed now and into the future.
The strategy is powerful for those who can implement it successfully. The key is knowing how to navigate around the labor issue – and other common reshoring difficulties – with minimal risk and complexity.
Reshoring Electronics: Why Companies Are Doing It
Offshoring no longer offers the cost savings it once did. The wage gap between what manufacturing workers get paid in the U.S. and what they are paid in foreign countries has closed significantly. In fact, the APAC region is the only place in the world where real salaries are projected to grow in 2023 despite global inflation.
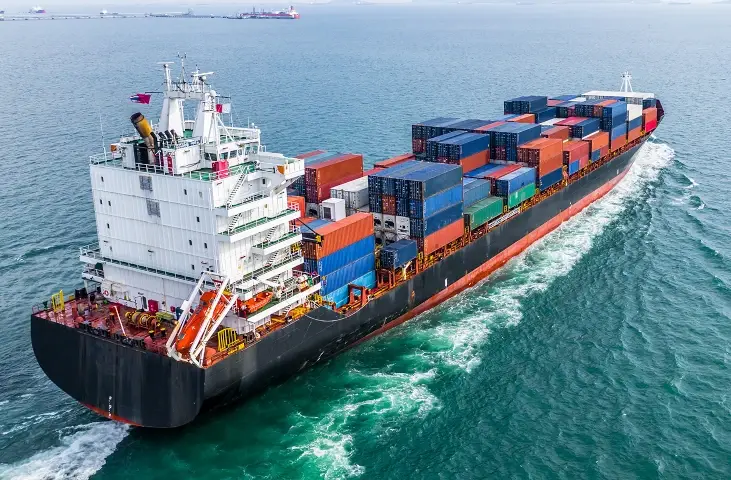
Offshoring also comes with many indirect and hidden costs. For one, companies have to ship finished goods across large oceans. This means paying for shipping containers, transportation, fuel, and logistics skills. To protect over longer distances, export packaging must be stronger and more robust than domestic packaging, increasing shipping costs through additional weight across the package’s entire journey.
Also, supply chain professionals have to place orders far in advance to secure production volumes. As a result, real-time demand can be less precise. It’s easy to end up with too much or too little supply when orders lead real-world activity so far. Forgetting to plan ahead for something like the Chinese New Year can be detrimental to top-line revenue.
Furthermore, offshoring comes with higher quality control risk. It’s hard to monitor production across many time zones and thousands of miles. U.S. companies have to put more trust in their outsourced vendors while circumventing known ( like expected cargo delays) and unknown (like extreme weather events) risks.
Easier Returns and RMAs
Sometimes, products aren’t up to par, and companies have to place additional orders or go back to the drawing board. Returns and RMAs can become complicated and take too much time when working with offshored manufacturing partners. By reshoring, organizations cut down on time and expense while shifting labor costs back to North America.
Better IP Protection
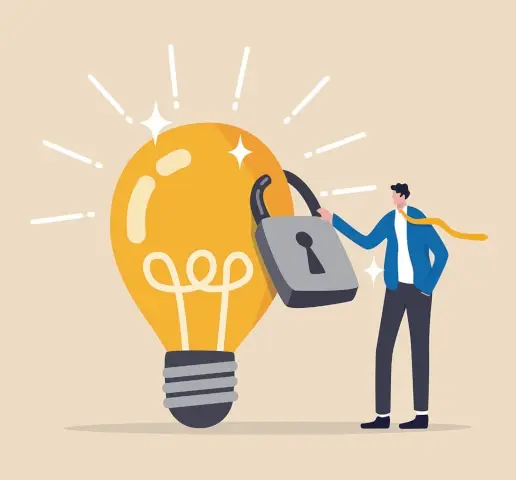
Another reason companies are reshoring is to find better protection for intellectual property (IP). The U.S. is committed to maintaining a legal environment that rewards innovation and punishes theft. Some foreign countries don’t share this vision, including many APAC countries where so much electronics production happens today.
Reshoring brings electronic IP back under the purview of the U.S. government. This empowers U.S. companies to pursue bad actors and protect their most valuable secrets.
Finally, reshoring is a viable answer for global supply chain disruption. Reshoring reduces operational complexity and decreases the number of layers between raw materials and finished goods. It also helps mitigate problems related to geopolitical turmoil, extreme weather, and other black swan events that can delay production.
What reshoring doesn’t automatically solve, however, is our current labor shortage. Finding workers to keep production lines online requires a more nuanced approach.
Thinking about reshoring but not sure what to factor in? Read Should You Reshore? 5 Helpful Graphs now.
Finding Workers is a Challenge
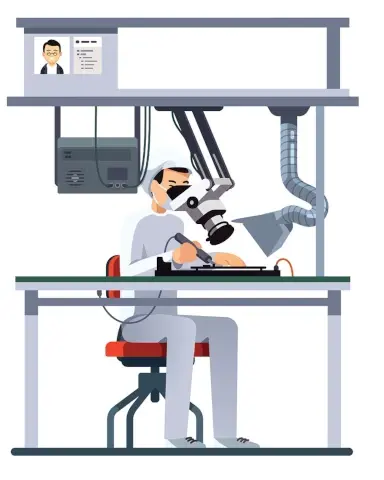
Manufacturing hiring is hot right now in the United States. The September jobs report from the U.S. Bureau of Labor and Statistics found that manufacturers added more than 20,000 workers during the month. Today, almost 13 million people are employed in U.S. factories.
Despite this, the labor department notes 800,000 job openings remain. Companies struggle to find people with adequate experience and talent. One IPC survey found that eight in ten companies are dealing with hiring problems today. Those who are able to acquire workers on the job market must pay them more.
The trucking and railroad industries also suffer from labor shortages, increasing logistical challenges for electronics companies. The COVID-19 pandemic motivated many workers in these industries to take early retirement, leaving these industries with fewer experienced workers.
Due to aging workforces, the devastating effects of lost knowledge and experience are expected to continue. Moreover, backfilling for talent has proved challenging due to the long hours and challenging working conditions commonly associated with sectors that rarely have chances for remote work as other fields have.
Although working with domestic contract manufacturers won’t eliminate all problems, they will reduce them. Build closer to your customers, and logistics will become simpler by default. At MacroFab, we make this easy.
Find Reliable Electronics Manufacturing Labor Through MacroFab
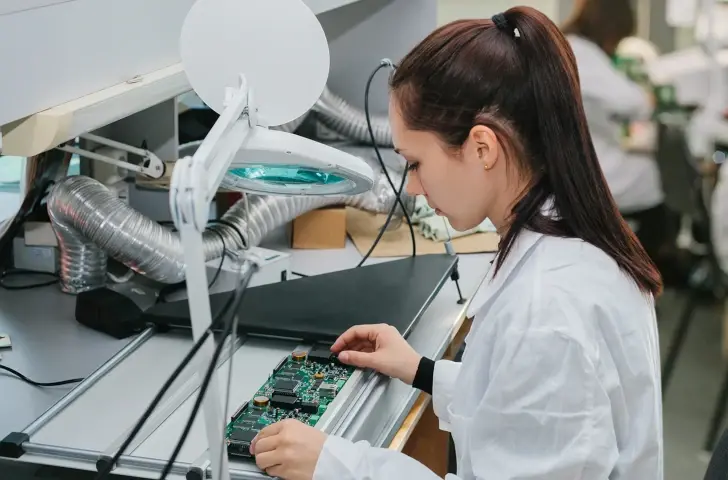
MacroFab is a cloud manufacturing company with an established network of North American-based contract manufacturers. We partner with US electronics manufacturing facilities as well as ones in Mexico, and Canada that have been thoroughly vetted for their skill and capacity. We know who has the right capacity and capabilities to take on new orders, whether for prototypes or full-scale production runs.
Labor availability is always guaranteed because we funnel your job to the right production line at any given time. Access to our factory network is highly elastic. You can scale up and down quickly and even assign different parts of your production lifecycle to different countries or factories. No minimum volume commitments, spikes in demand, or capacity limitations apply.
For example, many of our clients will prototype in the U.S. to iterate on new designs quickly. Then, they will mass produce in Mexico where labor is still cost-effective and available. Mexico has a burgeoning manufacturing industry. The country graduates more engineers per capita than the U.S. every year. The population is also younger overall, giving electronics companies more flexibility when it comes to manufacturing in Mexico.
We’ve already done the hard work of building relationships and understanding the regulatory and labor environments in Mexico and in the USA. You don’t have to build new factories, lease property, or recruit workers. Instead, your electronics engineers can focus on designing better products, and your supply chain leaders can pick the ideal vendors for your production needs, allowing you to prosper despite America’s labor shortage.
Related Topics
Companies Bring Electronics Production Home From Asia
Lately, numerous companies have begun reassessing their global value chains and moving electronics production closer to home.
What’s Changing in US Electronics Manufacturing
In the coming years, reshoring electronics manufacturing may be the key to maintaining the US economy's stability.
Surviving the Warehousing Squeeze
The warehousing crunch has put a strain on electronics companies that rely on quick delivery of electronic components or PCBAs, especially from overseas.
Ready to Come Home to America?
Reshore with MacroFabAbout MacroFab
MacroFab offers comprehensive manufacturing solutions, from your smallest prototyping orders to your largest production needs. Our factory network locations are strategically located across North America, ensuring that we have the flexibility to provide capacity when and where you need it most.
Experience the future of EMS manufacturing with our state-of-the-art technology platform and cutting-edge digital supply chain solutions. At MacroFab, we ensure that your electronics are produced faster, more efficiently, and with fewer logistic problems than ever before.
Take advantage of AI-enabled sourcing opportunities and employ expert teams who are connected through a user-friendly technology platform. Discover how streamlined electronics manufacturing can benefit your business by contacting us today.