MacroFab Blog
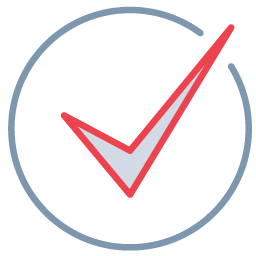
Checkpoint
E-bikes combine the physical capabilities of traditional bicycles with the data-centric advantages of connected devices.
Electric bicycles (e-bikes) are gaining traction as a key tool in reducing greenhouse gas (GHG) emissions in the urban environment. They provide an eco-friendly option that aligns with the ambitious climate goals set by many cities and regions.
The Role of PCBAs in E-bike Technology
Prof. Nicola Bianchi defines e-bikes as light hybrid vehicles that combine human and electric power. An e-bike's design includes system, mechanical, and electrical components. Within the electrical aspect, the PCBA is crucial for managing motor controls and battery operations while providing the necessary infrastructure for smart connectivity and advanced safety features.
The surge in e-bike popularity is not just because of their innovative designs but also due to a combination of efficiency, affordability, and health benefits. Projections estimate that e-bike sales will reach an impressive USD 62.3 billion by 2030.
This article explores how electronics, especially PCBAs, contribute to the success of e-bikes today.
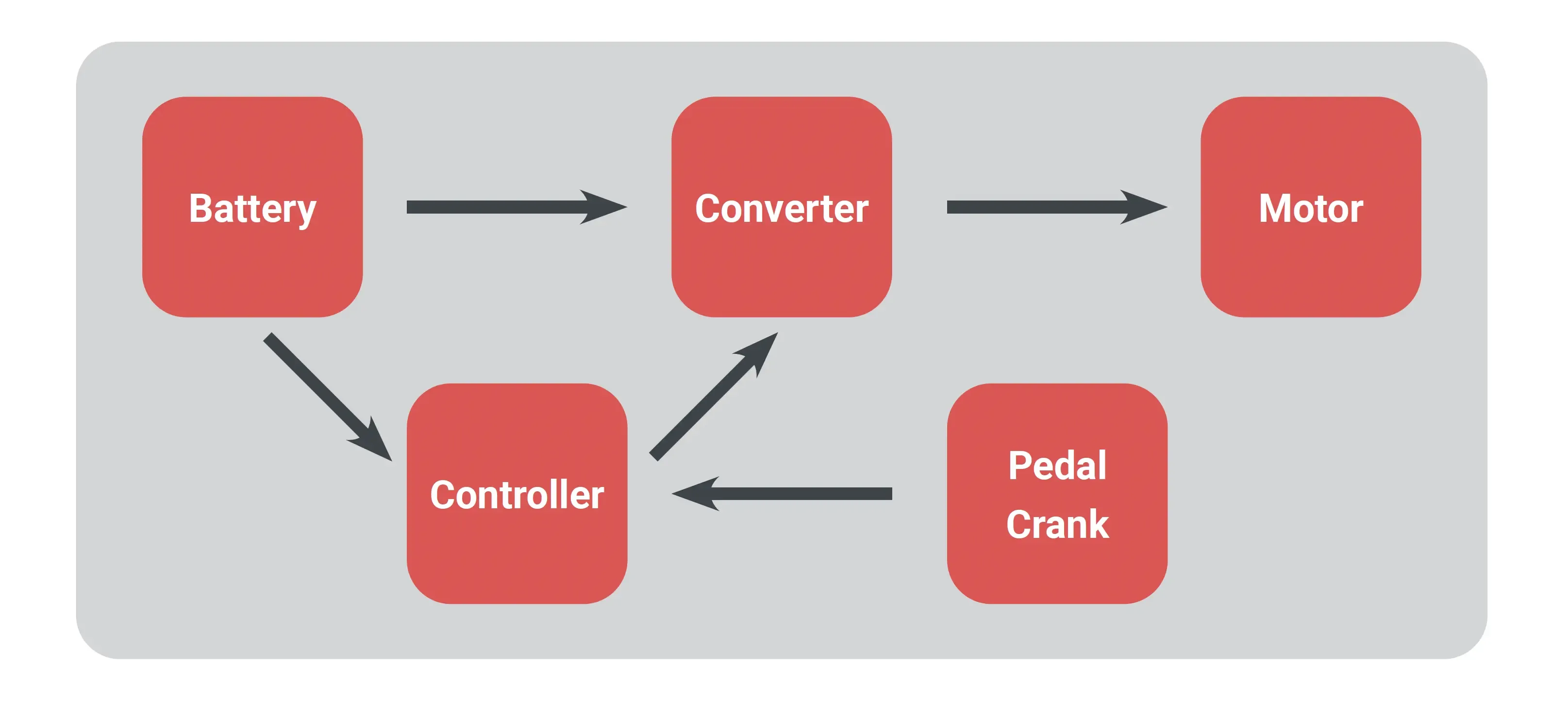
Understanding E-bike Components and Their PCBAs
The e-bike system primarily comprises four components: the battery, power converter, controller, and electric motor.
E-bike Battery and Battery Management System
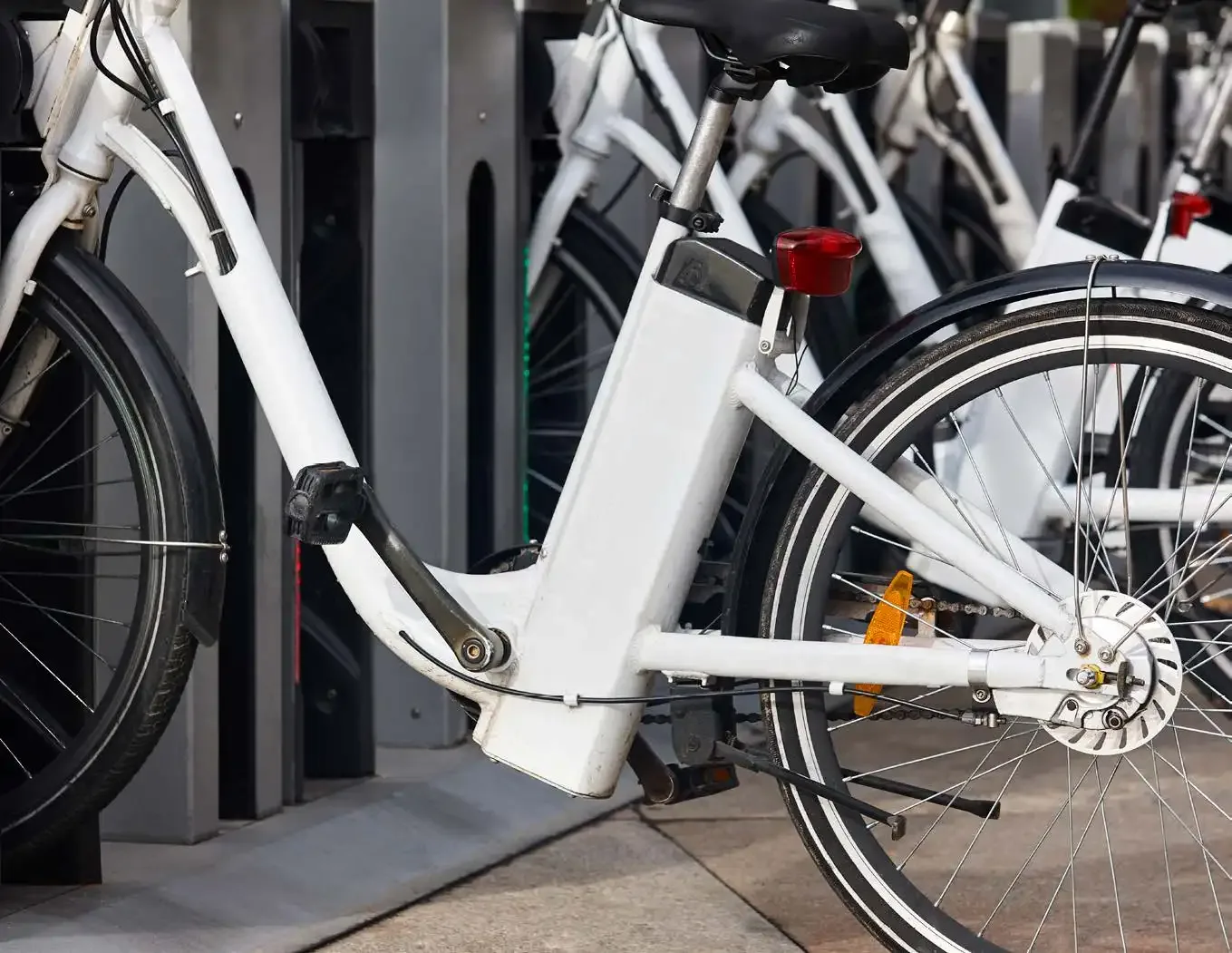
E-bikes mostly use lithium-ion batteries due to their power density, efficiency, and long life. Typical battery packs used by e-bikes provide voltages between 36 V and 48 V. Modern designs integrate the battery into the bicycle frame, enhancing durability by shielding it from external conditions such as moisture and dust.
Given the lithium-ion battery's sensitivity to temperature and charging limits, a battery PCB protection board, or a PCB-based Battery Management System (BMS), is essential. The BMS oversees charging and discharging, monitors the state of charge (SOC) and health, and maintains battery balance, thereby optimizing its lifespan.
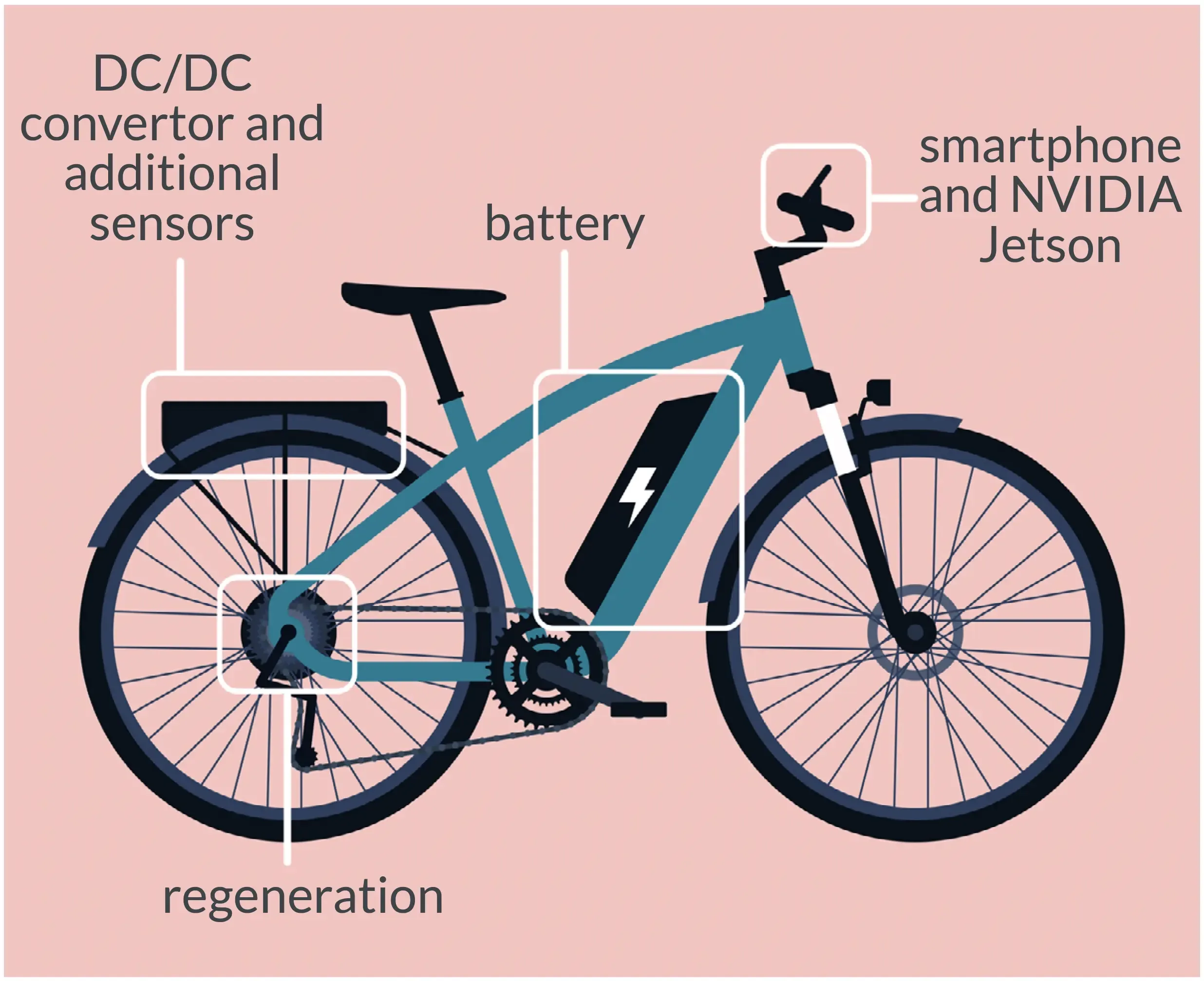
E-Bike Power Converter (ESC)
The power converter, often referred to as the Electronic Speed Controller (ESC), is a vital component in the e-bike's electrical system. The ESC connects to both the battery and the motor. It converts the battery's DC output into a three-phase AC waveform suitable for the brushless DC motor.
Modern ESC PCBAs may also support regenerative braking, allowing energy captured during braking to be fed back into the battery.
Electric Motors
E-bikes use electric motors for propulsion, mainly brushless DC motors (BLDC) and brushless AC motors.
The PCB box-build for the BLDC system includes the control logic driven by a microcontroller, a power stage with switching devices like power MOSFETs and IGBTs, and sensors necessary for closed-loop control.
BLDC motors offer several advantages: they have an extended lifespan, emit lower electromagnetic interference (EMI), operate quietly, and provide a favorable torque-to-size ratio.
There's also a rising interest in permanent magnet synchronous motors (PMSMs). These AC motors stand out as high-performance traction solutions for e-bikes, notably for their superior torque density, especially at reduced speeds.
E-Bike Control Units
In e-bikes, the control unit is the "brain." A core component of the control unit's PCBA is a microcontroller. It integrates inputs from the user (through control buttons or a display interface), sensors, and feedback from the motor to determine how much power to deliver to the motor.
For instance, the microcontroller interfaces with hall-effect sensors in the motor, obtaining real-time data on motor position or rotor angle. Using this data, the microcontroller directs power MOSFET switches to effectively drive the motor.
The e-bike controller governs power distribution, ranging from zero up to the motor's peak rating. It supports various modes—from energy-conserving 'eco' to high-performance 'sport'—adjusting power assistance based on rider preference. Additionally, riders can access data like battery status, distance covered, and diagnostic features via a dedicated display.
Motor performance depends on the control logic adopted. Two prevalent methods are:
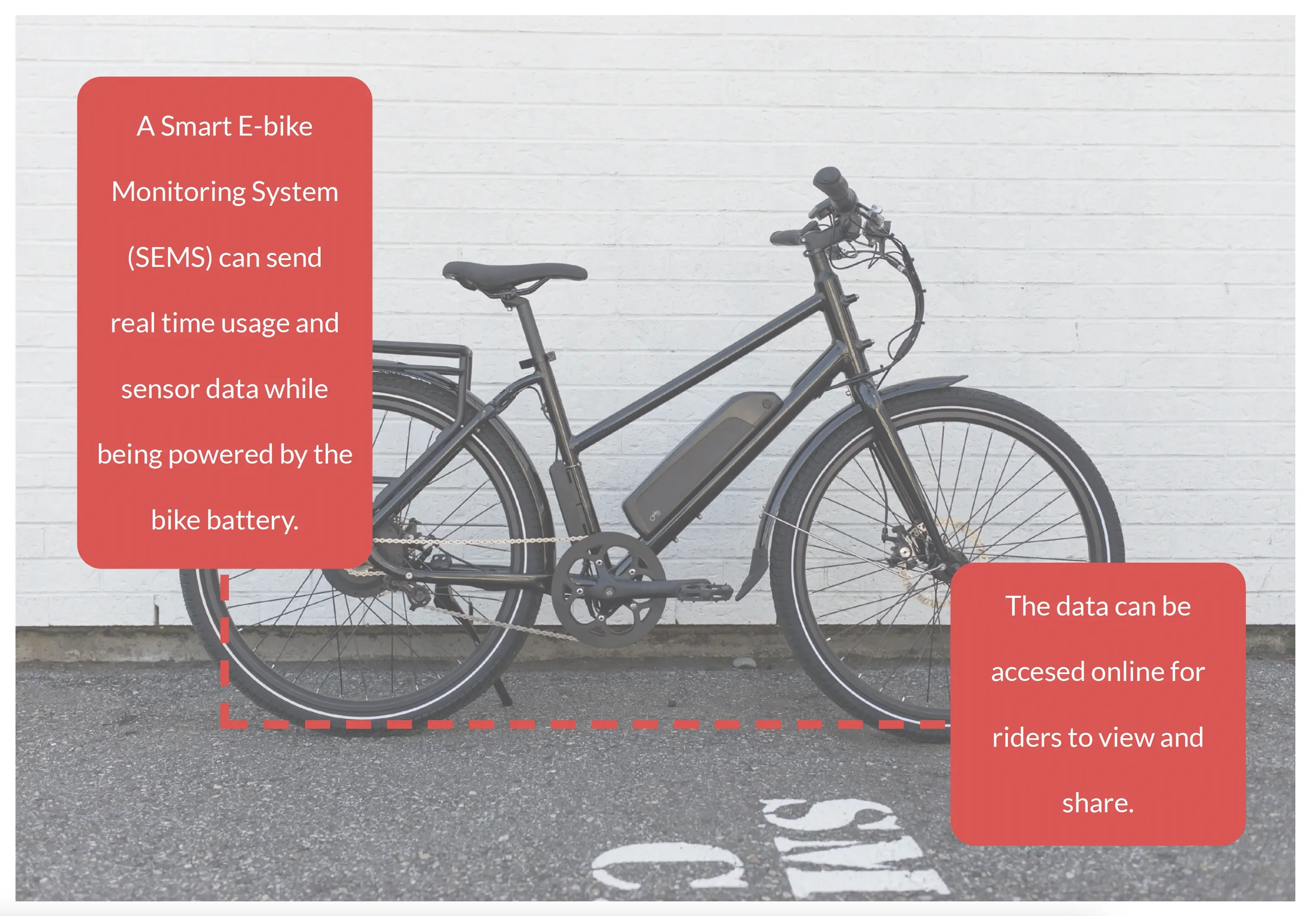
Control-Assisted Power Method:
In this method, the motor lends a helping hand by providing constant, predetermined power once a certain pedal torque (the effort exerted by the rider) is sensed. It's straightforward to implement, but there's a downside: the motor delivers the same level of assistance no matter the terrain or the rider's physical state. This lack of adaptability might result in a less comfortable ride or safety concerns, especially if the conditions change.
Proportion-Assisted Power Method:
This approach adjusts the motor's assistance based on the e-bike's speed. When traveling below a certain speed threshold, the motor matches the rider's effort. However, as the bike's speed increases and approaches its maximum limit, the motor gradually dials back its support. At top speeds, the motor refrains from assisting altogether.
Integration with IoT: Smart E-bikes in Smart Cities
Modern PCBAs integrate specialized chips and modules, enabling e-bikes to connect to larger networks through Wi-Fi, Bluetooth, or cellular connections, thus transforming them into smart bikes. A smart bike is considered an object (Thing) that is linked to the internet, or an “Internet of Things” (IoT).
IoT refers to the vast network of interconnected devices that communicate and exchange data with each other over the internet. IoT's real power lies in the data it collects. When analyzed, this data can provide insights, drive decision-making, or automate processes without human intervention.
In essence, e-bikes embedded with IoT functionalities combine the physical capabilities of traditional bicycles with the data-centric advantages of connected devices.
Consider this: You leave your smart bike outside a café. Upon locking it, the security mode engages. If someone attempts to tamper with the lock while you're away, the bike's motion sensors pick up the unauthorized activity.
The bike's processing unit interprets this as a potential theft and sends an alert signal to a cloud server using its WiFi module. The cloud server then pushes a notification to your smartphone app, also using WiFi technology. Concurrently, the bike's GPS starts sending its location to the server, updating your phone in real time.
With the alert, you're prompted to check on your bike. If, by chance, the bike were taken, the GPS data would aid you or authorities in its retrieval.
This example underscores how an IoT-integrated smart bike can seamlessly communicate and share data with another device, like your smartphone, over the internet.
Some use cases, such as bike-sharing systems transmitting large data sets to a central cloud server for processing, can introduce unacceptable delays. In such cases, the smart bikes are equipped with highly integrated PCBAs to perform edge computing.
Edge computing allows data processing directly on local devices, or "at the edge.” It's possible to make swift, real-time decisions without waiting for distant servers to respond.
AI and Machine Learning in E-bike Technology
Artificial Intelligence (AI) involves designing machines to execute tasks that typically require human intelligence. A key aspect of AI, Machine Learning (ML), empowers computers to learn from data without direct programming. Rather than coding for every possible scenario, ML systems use algorithms to parse data, learn from it, and then perform predictions or data categorizations they have not seen before.
The backbone of AI and ML is the specialized electronic hardware that runs these advanced algorithms. Major corporations and emerging start-ups alike have unveiled Application-Specific Integrated Circuits (ASICs), Graphics Processing Units (GPUs), and Tensor Processing Units (TPUs) to meet ML's unique needs.
Custom PCBAs are then integrated with these specific components to offer a compact and efficient solution for devices that require AI capabilities. A prime example is e-bikes. Modern e-bikes that use these highly integrated PCBAs with edge-machine learning capabilities can now:
- Optimize battery usage by analyzing the rider's behavior and route terrains (Adaptive Battery Management).
- Forecast when parts need attention using both historical and real-time data (Predictive Maintenance).
- Modify settings, such as pedal-assist levels, based on the rider's preferences (Personalized Riding Profiles).
Numerous studies emphasize the transformative role of AI-based PCBAs in the e-bike industry. One study shows how acceleration data, when processed by an AI algorithm, can detect early signs of brake wear in smart bikes.
Another study uses AI to convert e-bikes into advanced health monitoring tools. E-bikes already play a role in promoting physical activity during commutes. They help riders meet the WHO's weekly recommendation of 150 minutes moderate exercise. Building on this health-centric feature, many contemporary e-bikes have sensors that record detailed health metrics.
This collected data can be processed directly on the e-bike through edge computing using AI modules. Alternatively, via IoT technology, e-bikes can transmit the raw sensor data to remote servers for data analysis.
This intricate data processing enables the e-bike to access the rider's vital health information. Based on the e-bike's intended purpose, this data can then be shared with stakeholders such as medical professionals, researchers, and athletic trainers.
The Future of E-bike Technology: AR, VR, and Beyond
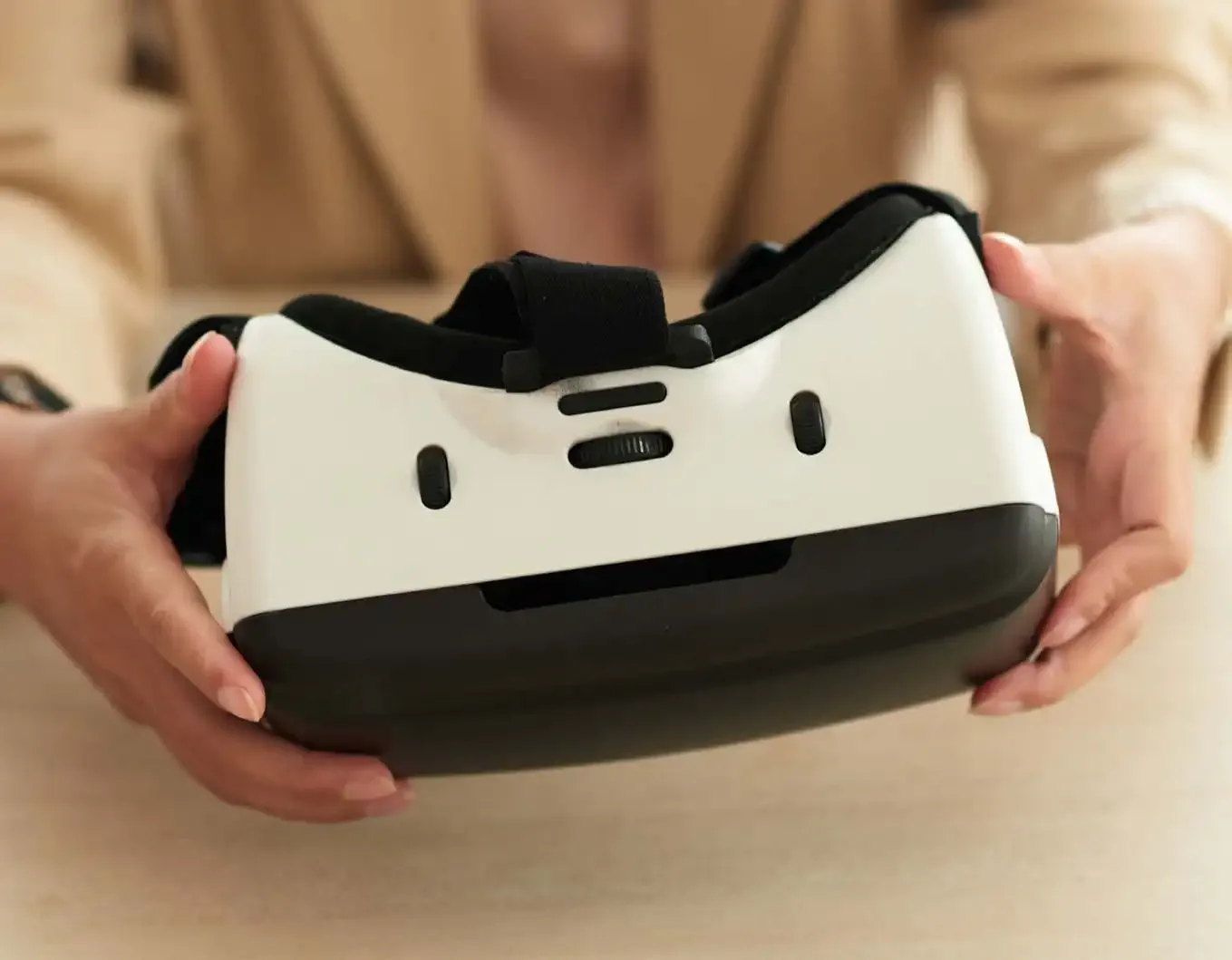
When an e-bike malfunctions, diagnosing the issue can be a time-consuming process. With Augmented Reality (AR), mechanics can overlay real-time diagnostic data on the e-bike's components using AR glasses or mobile devices. For instance, by just looking at the battery or motor, mechanics can view real-time voltage, current, or temperature readings.
For intricate repairs, AR provides direct, step-by-step instructions on the e-bike, from animated component replacements to immediate feedback on connections. In especially challenging situations, an engineer can leverage AR to share their viewpoint with a remote expert, receiving guidance through annotations or overlaid instructions.
Virtual Reality (VR) offers engineers immersive training modules, enabling them to virtually disassemble an e-bike, recognize parts, and grasp their functions, thus preventing real-world damage. Moreover, VR scenario-based training immerses engineers in varied fault simulations, offering hands-on troubleshooting experiences—a marked improvement over conventional classroom training.
Conclusion
E-bikes represent the forefront of eco-friendly transportation, integrating cutting-edge technologies like IoT, AI, edge machine learning, AR, and VR. These technologies enhance the user experience and reshape e-bike repair and training.
Highly integrated PCBAs are fundamental to e-bike advancements, integrating modern technologies. Yet, as e-bike functionalities grow, the demands on these PCBAs intensify, making their design, installation, and maintenance increasingly intricate.
Engineers and designers face a challenge. Staying current with these evolving technologies, constantly pushing the envelope, and innovating is essential. E-bikes will thrive in the future if we combine technology with sustainability.
Related Topics
How to Shorten PCBA Production Lead Times with MacroFab
In the rapidly evolving electronics sector, extended production lead times are no longer tolerable, and minimizing these lead times is crucial for success.
From Garage to Growth: How Startups Scale with MacroFab
Scale your hardware startup smarter with MacroFab—prototype to production, U.S. manufacturing, instant quoting, and expert support every step.
PCBA Order Lead Time Report: Guidance for Lunar New Year 2025
With Lunar New Year coming up, MacroFab wants to ensure they give the best guidance when planning orders to continue meeting delivery guidelines.
Do You Need PCBAs for Your E-bike Project?
Get an instant quote nowAbout MacroFab
MacroFab offers comprehensive manufacturing solutions, from your smallest prototyping orders to your largest production needs. Our factory network locations are strategically located across North America, ensuring that we have the flexibility to provide capacity when and where you need it most.
Experience the future of EMS manufacturing with our state-of-the-art technology platform and cutting-edge digital supply chain solutions. At MacroFab, we ensure that your electronics are produced faster, more efficiently, and with fewer logistic problems than ever before.
Take advantage of AI-enabled sourcing opportunities and employ expert teams who are connected through a user-friendly technology platform. Discover how streamlined electronics manufacturing can benefit your business by contacting us today.