MacroFab Blog
Smart city applications are making a difference. For instance, Chattanooga's smart grid recently prevented power outages for 44,000 people. In San Diego, smart streetlights equipped with cameras provided video surveillance for the capture of car tags related to sex offenses or the identification of hit-and-run vehicles in traffic incidents, thereby improving crime detection and investigations. Meanwhile, Seoul's smart waste management system has reduced trash overflow by 66 percent and collection costs by 83 percent.
The Backbone of Smart Cities: Sensors and Actuators
Consider a city that adjusts traffic lights according to congestion or automatically sends air quality alerts. This is the power of smart cities, and at the core of it all are sensors and actuators. These tiny devices act as the city's nervous system, constantly collecting data and responding to environmental changes and citizen needs. In turn, this real-time information helps improve cities' services, from energy management to public safety.
The success of any smart city project hinges on the reliability and durability of its sensors and actuators. These electronic workhorses need to be tough. Frequent breakdowns and replacements can quickly become a budget nightmare.
Building Resilience: Ruggedized Electronics for Smart Cities
The good news is there are ways to make these components sturdier. One key approach is using ruggedized printed circuit board assemblies (PCBAs). Unlike their standard counterparts, ruggedized PCBAs are built to withstand the harsh realities of a city environment. Moisture, extreme temperatures, shocks, and vibrations – these PCBAs can handle it all.
This article dives into specific methods for fortifying PCBAs in smart city applications. We'll explore techniques like applying protective coatings, selecting extra-durable materials, and implementing design features that handle bumps and shakes.
Robust PCBA Design
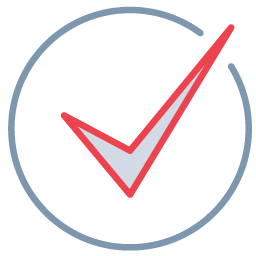
Checkpoint
To create a durable smart device, you need to know the stresses it will face.
Robust PCBA design is a methodology to improve product quality and reduce costs. It identifies the best design parameters to ensure top performance, affordability, and high quality in the final product.
Advantages of Robust Design in Smart City Applications
- Extended Lifespan and Reduced Maintenance Costs: Smart city devices often feature extensive sensor networks. A robust design reduces how often maintenance or replacements are needed, saving money in the long run.
- Improved Product Quality and Performance: Robust PCBA design helps devices operate efficiently with minimal performance degradation. This involves rigorous testing and validation. This is very important for dependable smart city systems like smart energy grids or public safety tools.
- Faster Development, Lower Costs: Robust PCBA design uses Design for Manufacturing and Assembly (DFMA) strategies. DFMA helps bring down development time and costs for new smart city devices. Companies can adjust the initial design to match production needs. This avoids expensive changes later and speeds up the production cycle.
To create a durable smart device, you need to know the stresses it will face. Smart city devices must endure temperature swings, humidity, mechanical shocks, and city pollutants, among other factors. These factors dictate the level of robustness required in the PCBA design to ensure reliability and durability.
Smart City Application: Air Quality Monitoring and Control
Air pollution is a major environmental health issue, linked to more premature deaths than HIV and malaria combined. According to OpenAQ, sharing air quality data is key to tackling this problem; people need to know what they are breathing every day.
Smart Cities offer solutions through the concept of a smart environment. Here, advanced technology tackles environmental issues like air quality. Cities can distribute low-cost sensors across urban areas, which instantly report pollution levels. Using data analysis and machine learning, cities can pinpoint pollution hotspots and predict trends. This lets them target interventions to cut air pollution.
Furthermore, the data collected from these sensors can be made accessible to the public through mobile apps and online platforms. This transparency empowers residents to make informed decisions about their daily activities, such as choosing cleaner routes for commutes or planning outings for better air quality days.
Even indoor spaces can benefit. Monitoring systems can detect poor air quality and activate air purifiers or adjust ventilation to improve conditions.
Humidity and Moisture Challenges for Air Quality Monitor PCBAs
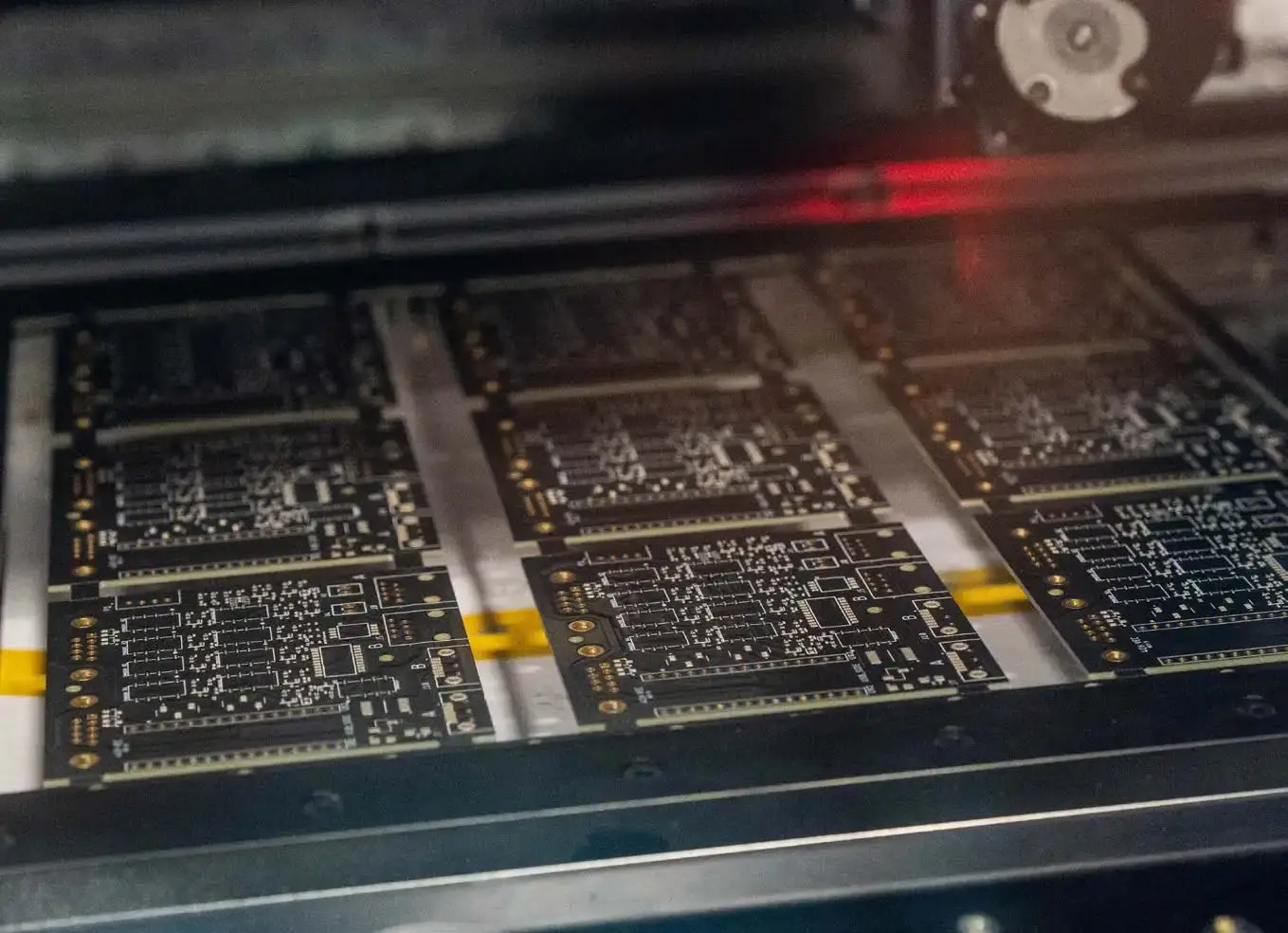
Air quality sensors in smart cities face a double threat: pollutants and moisture. In industrial areas, they battle harmful gases like ozone and nitrogen oxides. Even underground parking sensors embedded in asphalt can be vulnerable to moisture infiltration.
Moreover, during the manufacturing of PCBs, any moisture trapped inside can transform into steam when heated. This steam rapidly expands during soldering processes such as vapor phase reflow, infrared soldering, and wave soldering. The intense pressure from this expansion can cause the PCB layers to separate, form hidden cracks, and weaken the structural bonds.
Moisture's Impact on PCBAs
Material Degradation: Moisture alters the electrical properties of PCB materials. It acts as a plasticizer, reducing the glass transition temperature (Tg) and increasing the dielectric constant. This can lead to slower circuit speeds and signal transmission delays.
Corrosion Formation: Moisture accelerates the corrosion process, which can cause electrical shorts and open circuits. This can lead to malfunctions and ultimately device failure.
Delamination Risk: Moisture expands rapidly when heated, causing layers to separate, delaminate, and form blisters.
To combat these challenges, air quality sensors often feature protective coatings, such as conformal coatings, and are housed in weatherproof enclosures. Regular maintenance also keeps these sensors working accurately and reliably for years.
Smart City Application: Intelligent Industry
Smart Cities integrate Industry 4.0 technologies to enhance industrial production efficiency. This approach supports predictive maintenance routines, minimizes material use, and reduces waste from heat and gas emissions.
Industrial sensors monitor operations, providing real-time feedback. Devices like servo actuators, motors, and robotics ensure precise control and smooth production flow.
Smart energy is another interesting application within Smart Cities. Here, sensors track energy production, transmission, and distribution. This includes the use of electric vehicle charging systems and smart grids.
In both these applications, the PCBAs in the sensors and actuators face tough conditions. These include high pressure, extreme temperatures, and vibrations. These challenges can lead to complex failures and costly operational downtime.
Vibration and Shock: Threats to Industrial Sensor PCBAs
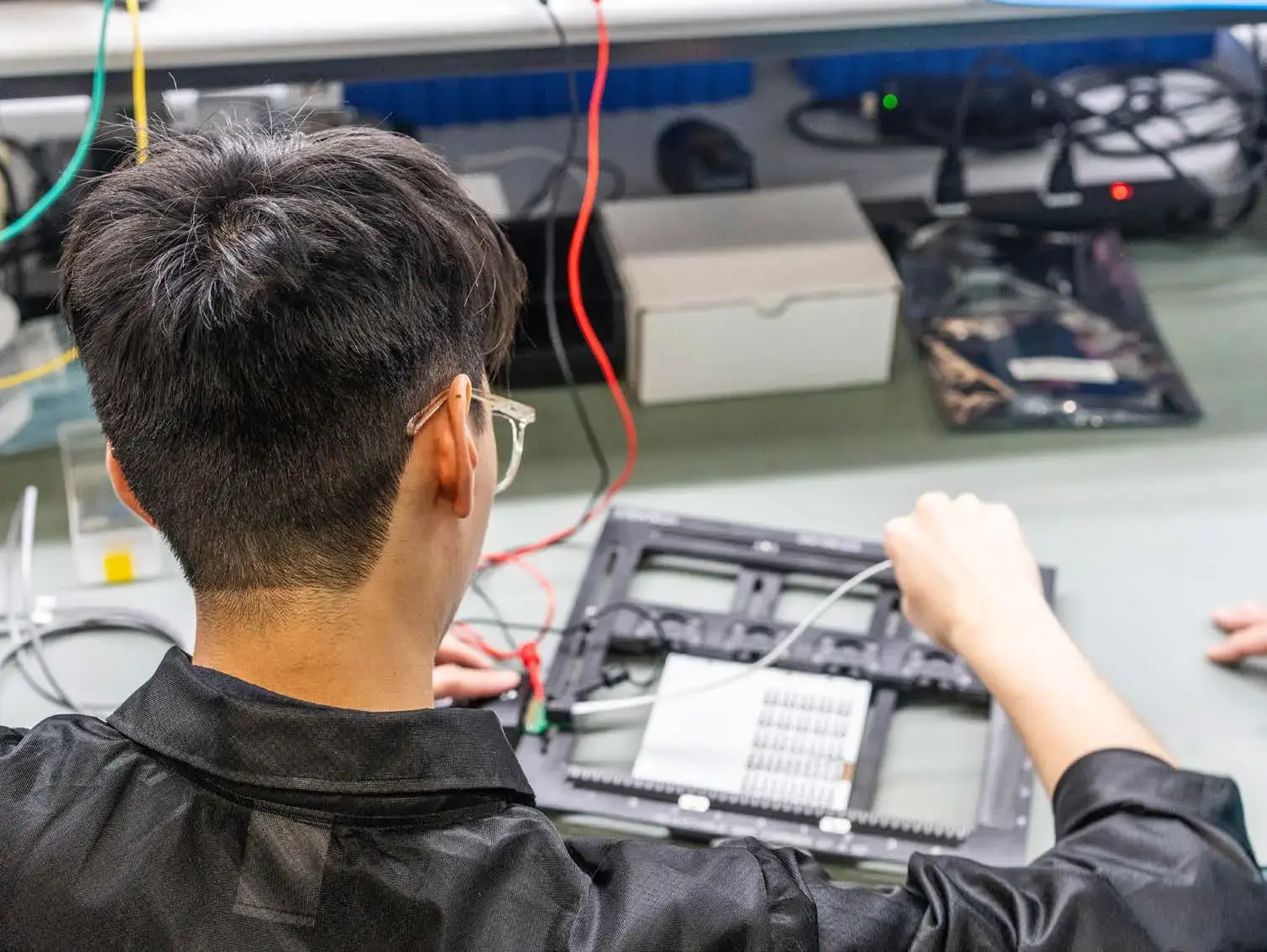
Industrial environments subject PCBAs to both vibration and shock. Vibration is defined as the repeated back-and-forth movement or oscillation of a system. Shock is a sudden jolt of energy that causes a big increase in stress, speed, acceleration, or movement in the system.
Each object, including PCBAs, has a natural resonant frequency at which it vibrates most intensely. When a PCBA encounters vibrations or shocks at or near this frequency, it experiences amplified vibrations. This intense vibration at the resonant frequency can cause the PCBA to bend back and forth repeatedly, stressing electrical leads and components. This stress can result in broken leads, solder joint failure, connector issues, and delamination.
Components like relays and oscillators are particularly prone to malfunction under these conditions. Larger components, exceeding two inches, suffer more from these effects. The most critical area of the PCBA is the center, as it experiences the most significant bending during resonant frequency.
To develop highly reliable products, it's essential to accurately understand how a product’s PCBA responds to vibration and shock forces.
Temperature Challenges for Industrial Sensor PCBAs
Electronics typically last longer when cool. High operating temperatures degrade device reliability. This presents a significant hurdle for PCBAs in smart factories and grids, as they often endure extreme temperature fluctuations.
PCBs are a composite of various materials, including copper, solder, and substrates. Each material expands at a different rate when heated. This mismatch in expansion creates mechanical stress. This stress can manifest as cracked solder joints or delamination, ultimately leading to circuit failures. Cooling poses similar challenges as materials contract at uneven rates.
Elevated temperatures also influence the electrical properties of PCBA components. For example, the resistance of conductive traces can increase. This rise in resistance translates to power inefficiencies or compromised signal integrity. Semiconductors, too, can malfunction when their operating temperature surpasses their junction temperature rating.
Furthermore, heat acts as an accelerant for the aging process of PCB materials. It intensifies chemical reactions such as metal oxidation, further compromising long-term reliability.
Ways to Ruggedize PCBAs for Smart City Applications
1. Application of Conformal Coating
Conformal coating is a thin polymer layer applied to PCBAs to insulate them from moisture and chemicals. There is no one-size-fits-all solution, so it’s important to choose the right conformal coating for each specific application.
Here are some key factors to consider:
Compatibility: Ensure the coating cures properly with all materials on the assembly. Consult the manufacturer and test the coating on sample materials to confirm compatibility.
Moisture Resistance: Also known as moisture and insulation resistance (M&IR), this measures how well the coating maintains its insulation properties under high temperature and humidity. A low M&IR value indicates poor protection in humid environments.
Hardness: For products exposed to temperatures below −10°C (14°F), use a soft coating to avoid exerting excessive force on fragile components. For abrasion resistance and protection from handling damage, a harder coating is needed.
Flammability: For assemblies exposed to heat, choose a coating with the appropriate flammability certification standards from Underwriters Laboratories (ULs) to ensure safety and compliance.
Below is a table that compares common conformal coatings:
Types | Properties | Disadvantages |
---|---|---|
Acrylic | - Easy to apply and remove due to reaction with base solvents. - Excellent moisture resistance and electrical properties. - High flexibility, easy rework, fungus-resistant and fast room temperature curing. | - Acrylic coatings are vulnerable to damage from solvent exposure during manual solder joint cleaning. - High solvent emissions make acrylics less eco-friendly. - Not suitable for low-temperature applications. |
Urethane | - Due to their polymerized and cross-linked structure, urethanes are highly resistant to chemicals, moisture, and solvents. | - Urethane is tough to remove due to its resistance to chemicals. It must be taken off with heat or mechanical effort, making repairs difficult and expensive. |
Epoxy | - Epoxy coatings are strong, long-lasting, and highly resistant to chemicals. - Their low thermal expansion coefficient matches well with the PCB epoxy resin, due to similar chemical properties. - Has higher glass transition temperature (Tg) than most other coatings. - Can be used as the foundation for anti-tampering coatings. | - Epoxy coatings often have a strong smell and can irritate the skin. - They are also hard to rework. |
Silicone | - Silicone coatings are soft, adhere well, and stay flexible across a broad temperature range. - Provides strong resistance to high humidity and good thermal endurance, making them suitable for components that dissipate heat, like power electronics. | - Once applied, they contaminate the surface and prevent other materials from adhering. |
Para-xylylene (Parylene) | - It offers the highest dielectric strength, lightest weight, lowest outgassing, and is mostly chemically inert and highly moisture-resistant. - It provides the most uniform coating. | - Requires batch processing with specialized equipment in a vacuum. - Difficult to rework, often requiring micro-abrasion. |
2. Vibration and Shock PCBA Design Guidelines
Follow the Octave Rule: The natural frequency of your PCBA should be twice that of the chassis to avoid extreme vibrations. They can amplify each other's vibrations if their frequencies are too similar.
Position Sensitive Components Carefully: Don't place sensitive parts like relays in the center of the PCBA, where shaking is strongest. Mount them on the edges where there's less movement.
Add Snubbers: These small devices, attached between PCBAs, help control movement and reduce stress during heavy vibrations by cushioning the boards against each other. Place them near the center of the PCBAs where movement is greatest.
Use Damping: This method turns movement into heat, reducing the energy available to cause damage. It’s especially useful in environments with lots of vibration and shock.
Use Stiffening Ribs: Use stiffening ribs to secure the edges of the PCBA. This will increase its natural frequency, which reduces movement.
3. Thermal Management PCBA Design Guidelines
Here are some key strategies for designing PCBAs for optimal thermal management:
- Maximize Heat Dissipation: Replace unused copper areas with pin fin or straight fin cooling pins. These pins effectively enlarge the surface area of the PCBA, enhancing heat dissipation into the surrounding environment.
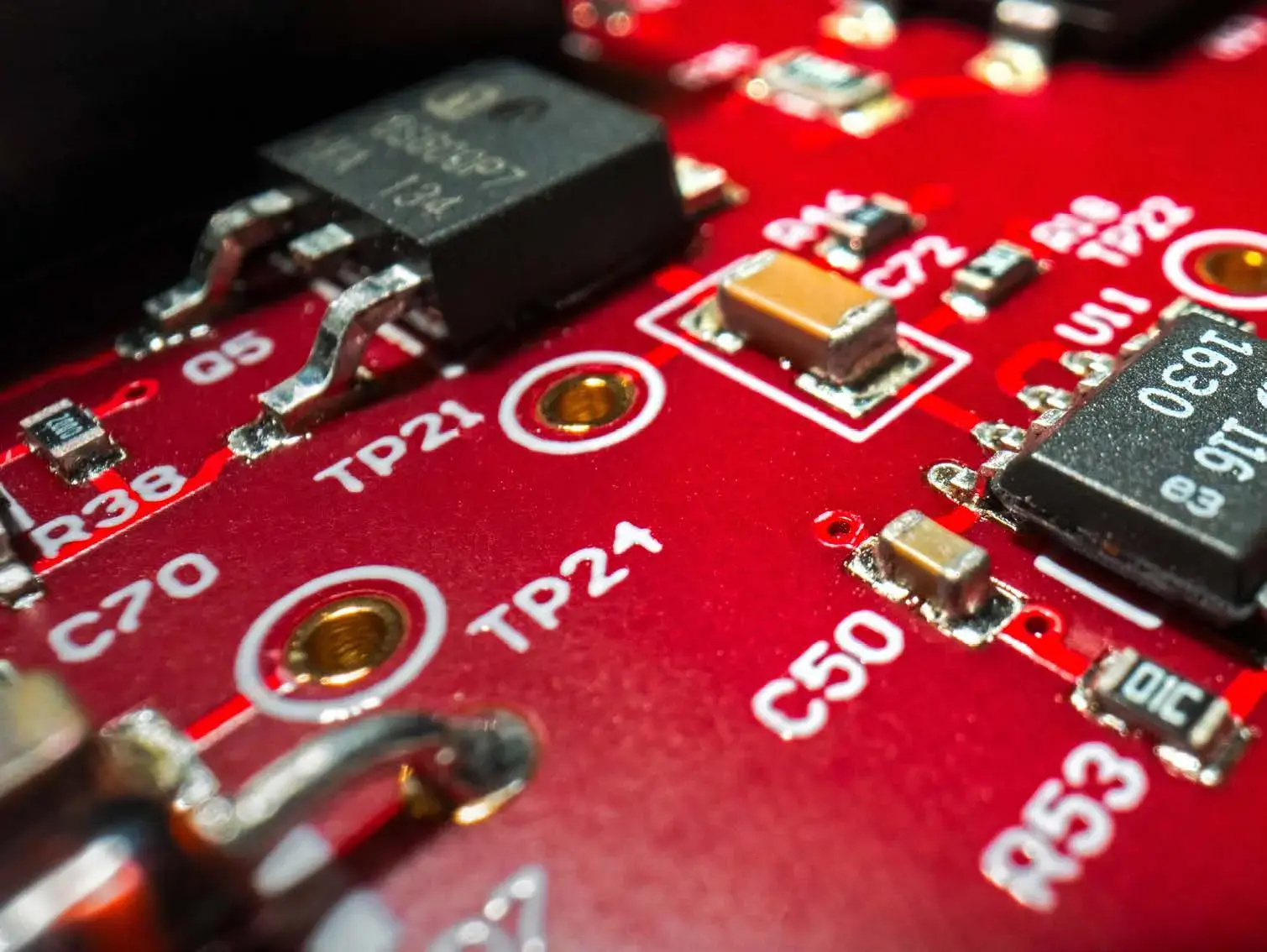
Efficient Heat Transfer: Securely attach the PCBA to heat spreaders or heat sinks. Utilize thermal pads or pastes to bridge any air gaps and ensure efficient heat transfer from the board to these cooling devices.
Spreading the Heat Load: Fill as many layers of the PCBA with copper as possible. This increases the overall thermal mass of the board, allowing it to distribute heat more effectively across a larger area.
High-Power Applications: For situations with high power demands, consider using Metal-Core Printed Circuit Boards (MCPCBs). These boards have a core made of metal, such as aluminum, which offers superior thermal conductivity compared to standard FR4 material.
Thermal Vias: Incorporate thermal vias throughout the PCBA design. These vias act as thermal conduits, transferring heat from internal layers to the outer layers of the board where it can be dissipated.
Forced Convection: If possible, leverage any available forced or convective airflow within the system to further enhance heat removal from the PCBA. This could involve strategically placing fans or vents to direct cool air over the board.
By following these guidelines, you can design PCBAs that operate within their designated temperature range, ensuring long-term reliability and optimal performance.
4. Design for Manufacturability and Assembly (DFMA) Considerations
By using DFMA, products can meet their functional requirements while being easy to manufacture and assemble. This approach encourages designers to consider fabrication and assembly early in the design process. The result is simpler designs with fewer components, and standardized materials and processes.
DFMA ensures that the design is mature and meets manufacturing requirements, reducing the need for costly and time-consuming redesigns that could increase the price of the final smart device.
Five DFMA considerations for designing PCBAs for smart devices:
DFMA Design Consideration | Benefits |
---|---|
Simplicity |
- Simplicity in design means using fewer parts. This makes products cheaper to make, assemble, and store. It also reduces defects and speeds up production.
- A simple design also uses fewer fasteners, multifunctional parts, and modular assemblies. This allows for easy updates and improvements, supporting continuous product evolution. Designers should minimize parts by integrating functions where possible and questioning the necessity of each component. |
Standard materials and a standardized design |
Establishing company-specific or product-family standards for materials, parts, and design processes boosts reliability, speeds up time to market, and cuts production costs. Reduced production costs can lead to lower prices for customers without sacrificing quality.
Maintain updated standards and enforce their consistent use across the development team to ensure the success of this approach. |
Specify tolerances based on process capability |
Set design tolerances based on what your manufacturing processes can actually achieve, rather than just aiming for the tight tolerances that designers often prefer. This approach helps avoid the use of overly complex components.
The best practice is to have design and manufacturing engineers work together in a team environment. This collaboration ensures that parts are designed to be easily and cost-effectively manufactured. Manufacturing engineers need to know the capabilities of all equipment and processes, both in-house and from suppliers. |
Choose commonly used materials |
Using common materials avoids the hurdles of creating new processing methods. Doing so can be costly, time-consuming, and can compromise reliability.
Opt for materials that your company or its suppliers regularly process when selecting components. Avoid exotic or cutting-edge materials and processes whenever possible. |
Engineering Collaboration |
Ensure the design team includes manufacturing engineers, quality engineers, and procurement specialists. This team with different expertise can analyze and choose the best design options as the product is developed.
Avoid the outdated method of passing designs to manufacturing only after engineering is finished. This old approach often leads to higher production costs and longer time to market. |
5. Testing and Validation
PCBA reliability testing is a crucial step to identify potential issues and ensure durability. Smart devices must withstand temperature changes, moisture, mechanical vibrations, and shocks. To validate the ruggedness of PCBAs in smart devices, they should undergo the following tests:
Environmental Test Methods: Includes corrosion, humidity, thermal shock, moisture resistance, flammability, and chemical tests.
Physical Test Methods: Includes vibration, random drop, solderability, terminal strength, high impact shock, and shock at a specified pulse tests.
Electrical Test Methods: Includes electrical characteristic tests, in-circuit, and functional testing. In-circuit testing examines individual components and connections on the PCBA. Functional testing simulates the final smart device environment by applying inputs to the PCBA and measuring outputs to check performance.
Standards for these tests include MIL-STD-202, MIL-STD-801, IEC 60068, IPC-SM-786, J-STD-001, J-STD-002, and J-STD-003.
Conclusion
Design greatly impacts a product's cost, quality, reliability, and time to market. This article discusses how to design ruggedized PCBAs for smart city infrastructure. These PCBAs must withstand moisture, temperature changes, vibrations, and shocks.
To ensure durability, conformal coatings protect against moisture and chemicals. Design guidelines that address vibrations, shocks, and temperature extremes are incorporated. Furthermore, applying DFMA principles and thorough testing also make these PCBAs robust.
The benefits of making robust PCBAs are clear. They lead to better system reliability, reduced maintenance costs, and a longer lifespan for devices within smart city projects.
Related Topics
How to Shorten PCBA Production Lead Times with MacroFab
In the rapidly evolving electronics sector, extended production lead times are no longer tolerable, and minimizing these lead times is crucial for success.
From Garage to Growth: How Startups Scale with MacroFab
Scale your hardware startup smarter with MacroFab—prototype to production, U.S. manufacturing, instant quoting, and expert support every step.
PCBA Order Lead Time Report: Guidance for Lunar New Year 2025
With Lunar New Year coming up, MacroFab wants to ensure they give the best guidance when planning orders to continue meeting delivery guidelines.
Ready to Start Your Next Project?
Get an instant quote nowAbout MacroFab
MacroFab offers comprehensive manufacturing solutions, from your smallest prototyping orders to your largest production needs. Our factory network locations are strategically located across North America, ensuring that we have the flexibility to provide capacity when and where you need it most.
Experience the future of EMS manufacturing with our state-of-the-art technology platform and cutting-edge digital supply chain solutions. At MacroFab, we ensure that your electronics are produced faster, more efficiently, and with fewer logistic problems than ever before.
Take advantage of AI-enabled sourcing opportunities and employ expert teams who are connected through a user-friendly technology platform. Discover how streamlined electronics manufacturing can benefit your business by contacting us today.