MacroFab Blog
As we look to the skies, we’re on the brink of a significant transformation. By 2036, the International Air Transport Association (IATA) suggests an annual flight tally of 7.8 billion passengers. As more people fly, the need for high-performance aircraft grows, and so does the challenge of creating robust avionic electronics.
Avionic electronics operate in demanding conditions. They must withstand intense vibrations without any circuit board malfunctions. Traditional hydraulic and pneumatic systems in aircraft are not only weighty but also have notable reliability concerns. The intricacies of aircraft manufacturing lead to supply chain complications, extended prototype development periods, and greater waste. Additionally, there’s a rising call for predictive maintenance to reduce aircraft downtime.
It’s fascinating to watch forward-thinking companies harness the latest trends in avionic electronics to overcome challenges. What sets the modern generation of aircraft apart are breakthroughs in sensor technology, such as engine vibration diagnostics, smart skins, and structural health monitoring.
The utilization of virtual reality for aircraft diagnostics and advances in propulsion technology are also noteworthy. Powering onboard sensors with energy harvesting represents another transformative step.
But it’s not all smooth flying. Avionics, like many established heavy industries, is often hesitant to fully adopt emerging tech trends. And they have good reasons: regulatory hurdles, compatibility concerns, the necessity of new investments, and the aim to maximize value from recently incorporated technologies—especially given the long life cycle of aircraft.
Throughout this article, we’ll explore four cutting-edge trends in avionic electronics and shed light on the challenges they present.
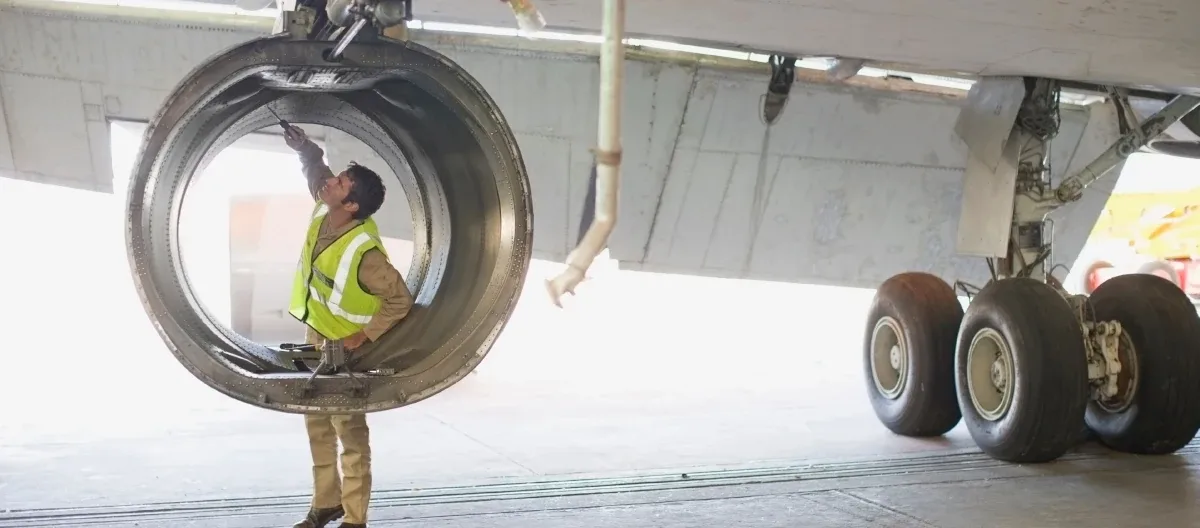
- Sensor Technologies for Enhanced Aircraft Safety and Performance
Modern aircraft are equipped with thousands of sensors, serving as critical components for improved safety, efficiency, reliability, and passenger comfort. These sensors not only monitor and diagnose various aircraft systems in real-time but also set the stage for proactive interventions and optimizations.
Key trends in sensor technology currently shaping the future of aviation include:
- Engine Vibration Diagnostics: Enables early detection of engine anomalies, preventing potential malfunctions. As initially reported by Military Aerospace Electronics, officials from the U.S. Federal Aviation Administration (FAA) Airport Safety Research have embarked on a two-year project. The aim is to use jet aircraft engine vibration monitoring to track both regular and irregular engine vibration levels during development phases, certification testing, and while in airline service.
- Structural Health Monitoring (SHM): Environmental stress can compromise the durability of avionic electronics. SHM plays a pivotal role in safeguarding the integrity of avionic structures. Recent trends in SHM have seen an uptick in the use of more refined and sensitive sensors. These advanced sensors excel at pinpointing fatigue damage, concealed cracks in difficult-to-access areas, disbonded joints, and a host of other structural issues common in aging aircraft.
- Smart Skins: Smart skins aim to provide a sensory layer on the external surface of an aircraft to detect changes, damages, or stress, similar to how biological skin detects stimuli. With advances in flexible electronics and smaller sensors from nanotechnology and micro-fabrication, smart skins are now more reliable. They’re increasingly used on modern aircraft to enhance safety and performance.
- Cutting-Edge Trends in Powering Sensors: Using energy harvesting, aircraft capture electricity from vibrations with embedded piezoelectric transducers. Aircraft naturally vibrate due to engines, aerodynamics, and air conditions, and so energy harvesting using piezoelectric can power onboard sensors, enhancing aviation sustainability.
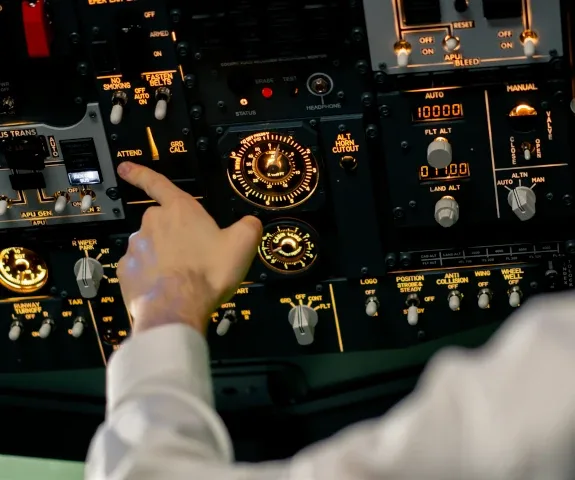
Improved engine diagnostics, SHM, and smart skins, when paired with data analytics are optimizing maintenance in the aviation sector, significantly reducing the estimated $62 billion annual cost due to aircraft-on-ground time. These technologies enable immediate repair actions as soon as aircraft land, minimizing downtime.
Highlighting this advancement, Honeywell and Cathay Pacific have partnered to deploy Honeywell’s GoDirect Connected Aircraft maintenance system for their Airbus A330 fleet. This program, leveraging comprehensive diagnostic information, connectivity, and data analytics, has been shown to decrease system failures by up to 35 percent, reducing aircraft downtime and minimizing flight disruptions.
2. Thermal Features Protecting Aircraft Electronics from Overheating
Electronics produce heat, and managing this heat effectively is vital for the reliability and longevity of aircraft systems.
One of the foremost trends in cooling power electronics and semiconductor devices in aircraft is a shift from using air-cooled methods to liquid-cooled or two-phase flow solutions. These methods offer superior heat transfer density, which helps the electronics stay within safe temperature ranges and thereby reduce the risk of component failures.
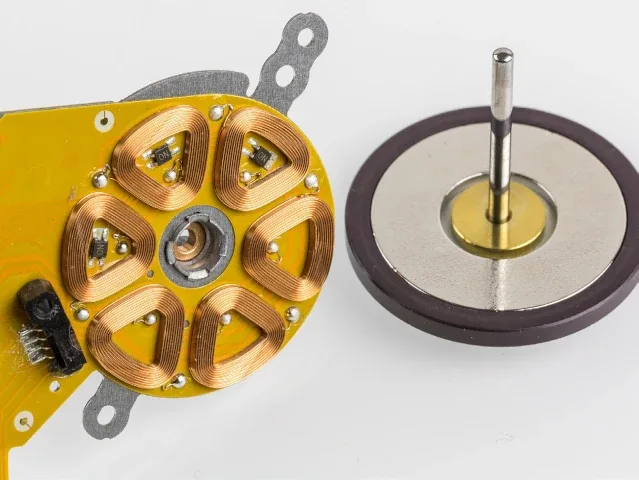
Concurrently, there’s a renewed interest in air-cooled systems, especially air-cooled heat sinks integrated with advanced materials like Annealed Pyrolytic Graphite and Aluminum Graphite. These provide lighter thermal management systems than their liquid-based counterparts.
Additionally, tools such as thermoelastic stress analysis are used in identifying crack locations in fastened aircraft joints.
3. Increased Aircraft Electrification
Global efforts to reduce pollution have spurred the push for greener, more sustainable aviation through aircraft electrification.
This shift starts with replacing hydraulic and pneumatic systems with electrical alternatives, resulting in weight savings, improved fuel efficiency, and a reduced environmental footprint.
The primary objective is to transition from fossil fuel-powered propulsion to cleaner, quieter electrical propulsion systems. Yet, this change presents challenges, given the bulky motors and the low energy density typical of electric systems. To address these issues, there’s active research into cutting-edge solutions like axial flux motors and superconducting technology. These innovations aim to reduce motor weight and size.
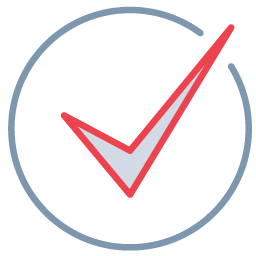
Checkpoint
We’re currently witnessing a rise in more electric-powered aircraft (MEA), where only the propulsion remains fuel-driven, while other subsystems are electric.
Consequently, we’re currently witnessing a rise in more electric-powered aircraft (MEA), where only the propulsion remains fuel-driven, while other subsystems are electric.
Hybrid electric aircraft (HEA) are expected to follow soon, blending conventional jet engines with electrical power. At the forefront of this transformation are industry giants like Airbus, Rolls-Royce, and Siemens, who have teamed up to pioneer a flight demonstrator for commercial hybrid-electric propulsion.
Ultimately, the vision is the emergence of all-electric aircraft (AEA) or full-electric aircraft (FEA), which are entirely devoid of combustion engines.
4. Diagnosing Aircraft Electronics with Virtual Reality (VR)
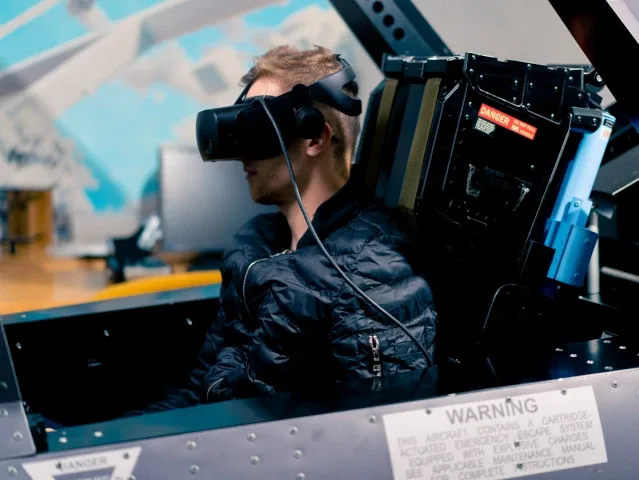
The VR Diagnostic System offers a virtual environment where technicians can navigate through a life-size, 3D representation of an aircraft’s electronic system. With immersive visuals and interactive elements, it provides a hands-on experience without ever touching the actual hardware.
Technicians can view components from all angles, zoom in for detailed inspections, or even view inside components. Since this method is non-intrusive, it mitigates the risk of inflicting damage to delicate electronics or inadvertently triggering malfunctions during assessments.
Additionally, it significantly saves time by eliminating the need for traditional paper manuals, enabling maintenance staff to quickly access relevant data on handheld devices.
Beyond diagnostics, VR is being used as an excellent training medium. Novice technicians practice troubleshooting in the virtual environment, refining their skills without the risk of causing harm to actual aircraft components.
Conclusion
Modern aircraft are leveraging advanced sensor technologies for enhanced engine and structural health monitoring, as well as the implementation of smart skins. The vast array of diagnostic data gathered from these sensors is increasingly integrated with data analytics, enhancing inspection and maintenance processes.
Additionally, the advent of Aircraft Maintenance Virtual Reality (AMVR) systems has revolutionized how aircraft are modeled during maintenance and inspection. VR systems also serve as invaluable training tools for novice technicians. Integrated thermal management systems and materials have also made significant strides in the avionic industry.
Related Topics
Drone PCBAs: Tackling Sensor Integration for Defense & Beyond
Understanding the challenges and best practices in creating sophisticated sensors for real-time data collection for different industries.
Red Hot PCB: Liquid Level Monitors
This weeks Red Hot PCB features Dixon Bayco's monitor boards that measure hazardous liquids to maintain safety operations within chemical facilities."
About MacroFab
MacroFab offers comprehensive manufacturing solutions, from your smallest prototyping orders to your largest production needs. Our factory network locations are strategically located across North America, ensuring that we have the flexibility to provide capacity when and where you need it most.
Experience the future of EMS manufacturing with our state-of-the-art technology platform and cutting-edge digital supply chain solutions. At MacroFab, we ensure that your electronics are produced faster, more efficiently, and with fewer logistic problems than ever before.
Take advantage of AI-enabled sourcing opportunities and employ expert teams who are connected through a user-friendly technology platform. Discover how streamlined electronics manufacturing can benefit your business by contacting us today.