MacroFab Blog
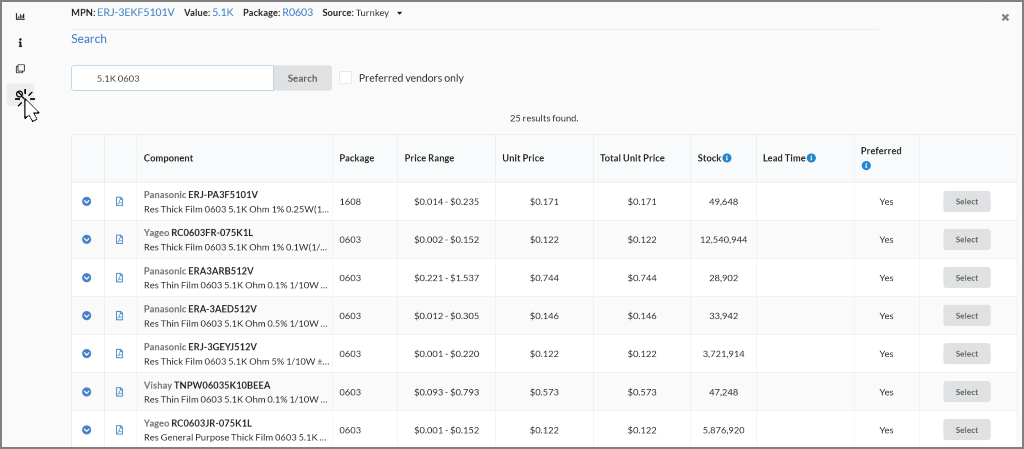
BOM Management 12
A successful manufacturing implementation of a new system project needs a plan for supply chain component dependencies during the development. Supply chain planning for a complex system bill of materials (BOM) can be challenging with many logistics interactions and dynamics. In some cases, a single key component shortage can put the manufacturing of a system in a line-down situation. However, by designing for success early in the development process and establishing a supply risk mitigation plan with your manufacturing partners, the potential supply chain issues can be minimized or eliminated entirely.
System Design Stage
During a new system design stage, the design-in of broadly available product components should be encouraged as much as possible. This enables the procurement of lower cost and more readily available components to fulfill the complete BOM. A broadly available component will often have a lower lead time since more vendors offer the solution. There is also a generally greater supply of the more common components in the marketplace.
As a final part of the system design, the development team should identify any long lead time component delivery issues in advance of production at the design stage. Some test run cases can be done for prototype builds to determine any bottlenecks resulting from back-order status, long lead times and delayed deliveries. Determine the worst-case logistics situation for kitting the BOM and simulate the impact of a single point of failure on the BOM from a missing component. Each component lead-time can be modeled for a critical case plan for procurement of the full system BOM.
Finding Alternate Parts
In addition to the primary BOM selections, each component should have at least one corresponding alternate or substitute component identified to use in the situation that the primary cannot be obtained in a timely fashion. The alternate components should be vetted for the same or very similar required attributes in advance of their approval.
During the prototyping phase, establish any turn-key kitting with your CM and plan with them in advance to help mitigate any potential shortages in inventory that could arise. Many CMs have access to multiple distribution partners that expand their procurement network beyond a single distributor. MacroFab offers a bill of materials section showing in real-time the best available parts from the top sourcing vendors.
For kitting purposes during manufacturing, discuss with your contract manufacturer (CM) when they have the authority to use these alternate components. It should be explicitly decided when alternates can optionally be ordered in lieu of the primary. Conversely, if the CM should not decide, determine what communication and data are needed for the design team to make this decision in a timely manner.
As an alternative, The MacroFab Platform gives you the ability to immediately check alternative part sourcing that fits your needs, while also showing instant lead times and a pricing breakdown for each part.
Setting Expectations
Review any critical and single-sourced customer component plans with the CM. Chart the best course of action to ensure stock is available for any system upside demand. Component obsolescence by the vendors should also have an identified mitigation strategy in advance. Determine how this case will be handled and by what party, in advance of the situation. These activities should all be part of a general inventory risk plan agreed with your CM kitting partner.
For unplanned business, establish the best-case lead-time for a complete system build including BOM procurement, assembly, manufacturing, test. Include any expedites and priority purchases when they are available. This process will help frame the timeline delivery expectations for the design, procurement, and sales teams as well as the end customer.
If you are having trouble getting accurate planning on your production level BOM, contact our sales team to see how you can get industry-matched pricing and lead times.
Summary
The ability to diversify your system supply chain for materials sourcing is key to removing logistical risk for the manufacturing of your complete BOM. Starting early in the development cycle to anticipate potential issues and designing in lower-risk components will provide a base framework for supply chain success later. During the prototype and manufacturing planning stage, work closely with your CM to establish a risk management plan for BOM kitting. Determine the decision ownership for alternate components and kitting procurement expedites for long lead time items and custom components. Lastly, identify the best-case timeline scenario for unexpected upside business and any methods to shorten it in the future. These planning steps will improve the delivery experience for your end customers.
Related Topics
Preparing for Potential Supply Chain Disruptions During Lunar New Year
This blog discusses on how to prepare for unexpected events for global supply chains such as the dockworker strike in preparation for Lunar New Year.
Mapping Out a PCBA Supply Chain Strategy in Five Moves
Companies should create unique vendor relationships with numerous international suppliers due to the necessity of having to source components globally.
MacroFab’s Modern Approach to Strategic Sourcing
Many Contract Manufacturers (CMs) and Original Equipment Manufacturers (OEMs) have some sort of procurement team. So what makes MacroFab so different?
About MacroFab
MacroFab offers comprehensive manufacturing solutions, from your smallest prototyping orders to your largest production needs. Our factory network locations are strategically located across North America, ensuring that we have the flexibility to provide capacity when and where you need it most.
Experience the future of EMS manufacturing with our state-of-the-art technology platform and cutting-edge digital supply chain solutions. At MacroFab, we ensure that your electronics are produced faster, more efficiently, and with fewer logistic problems than ever before.
Take advantage of AI-enabled sourcing opportunities and employ expert teams who are connected through a user-friendly technology platform. Discover how streamlined electronics manufacturing can benefit your business by contacting us today.