MacroFab Blog
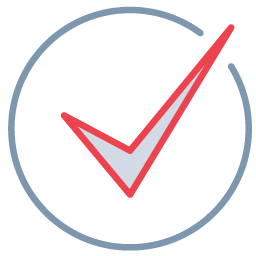
Checkpoint
Supply chain disruptions, whether natural or human-caused, have a steep cost.
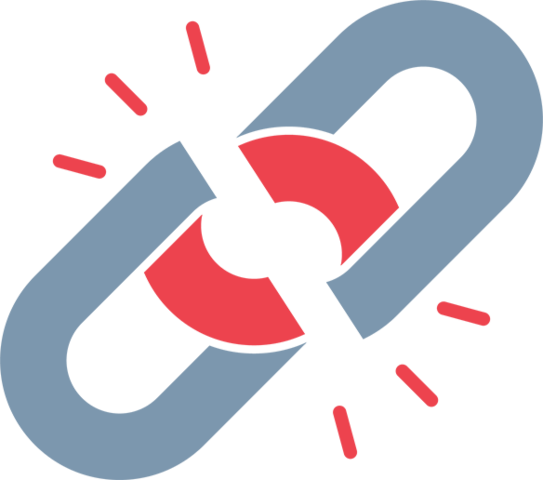
Updated July 15, 2024
The global landscape has shifted dramatically since offshoring became a popular supply chain strategy decades ago. Rising geopolitical tensions and economic uncertainties have forced a critical reassessment of global supply chains. Over time, the business case for offshoring has lost power. As a result, many companies are now reshoring electronics production to build more resilient and agile operations.
This shift is driven by a combination of factors, including economic considerations, supply chain risks, and intellectual property protection. The recent surge in manufacturing construction investment is a testament to this reshoring trend. As of February 2024, annual investment in new manufacturing facilities hit nearly $225 billion dollars, a record high even after adjusting for inflation. This significant uptick, driven primarily by investments in computer, electronic, and electrical real manufacturing construction, was catalyzed by the passage of the CHIPS Act and the Inflation Reduction Act.
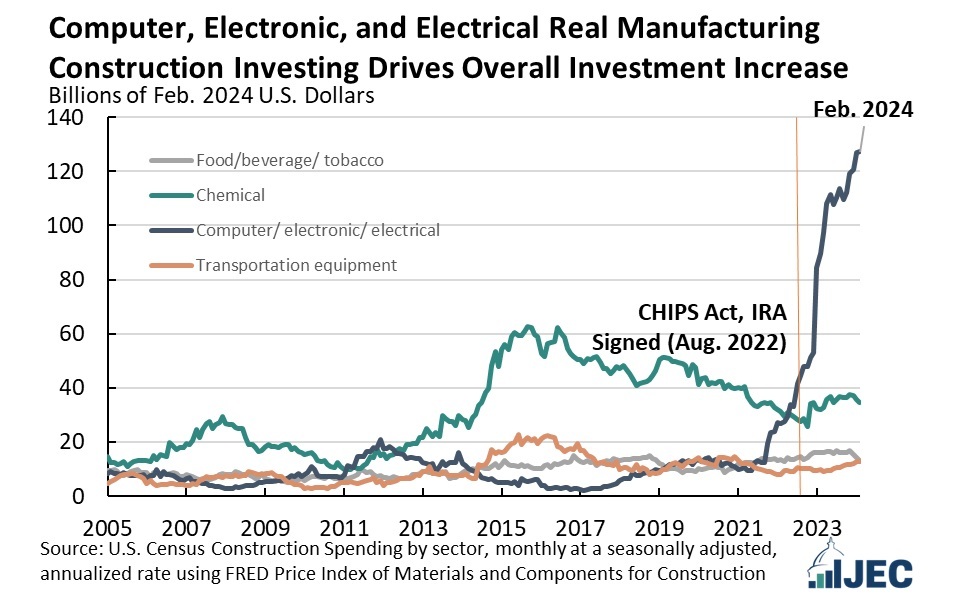
Computer Electronic and Electrical Real Manufacturing Construction Investing Drives Overall Investment Increase
In this post, we’ll cover the three leading reasons why companies are reshoring electronics production. All stem from long-term trends that have been bubbling under the surface, leading to what we believe will result in a new electronics production paradigm – one that revolves around risk assessment and risk mitigation to drive better business processes and fewer supply chain disruptions by working with nearshore and domestic vendors.
Savings Have Declined
Historically, offshoring was primarily a cost-saving strategy. In the past, companies moved manually- intensive work to foreign markets because labor costs were cheaper.
But over the years savings related to outsourced manufacturing, IT, and services work have dried up. Labor, energy, and transportation costs now eat further into margins. Wages in China – the leading producer of semiconductor chips in the world – have increased considerably as the country has grown more prosperous. The gap between Chinese and U.S. manufacturing wages is much smaller.
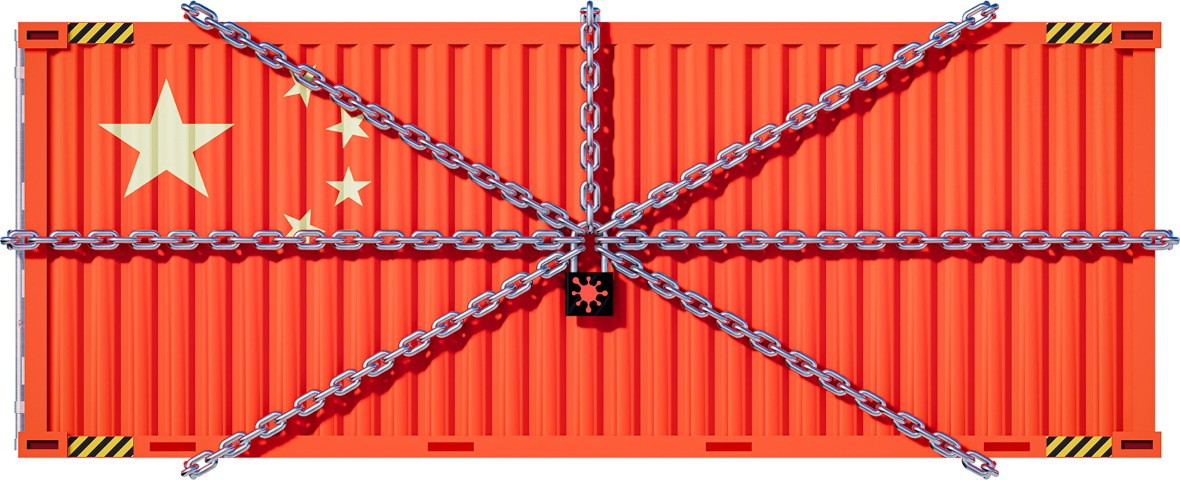
Shipping and freight costs also skyrocketed during the COVID-19 pandemic. While rates have come down since, volatility still exists, leaving companies to wonder when the next spike might happen.
The same has happened with gas, coal, and electricity. And as our electronics supply chains have grown more interconnected, it has become nearly impossible to protect against price fluctuations. Moving raw materials and finished goods around the world is no longer as cost-effective as it used to be.
Moreover, companies now realize offshoring has many hidden costs. Monitoring progress and maintaining quality control is hard over such large distances. Domestic teams have to trust that their foreign factory managers are reporting accurately and upholding high standards.
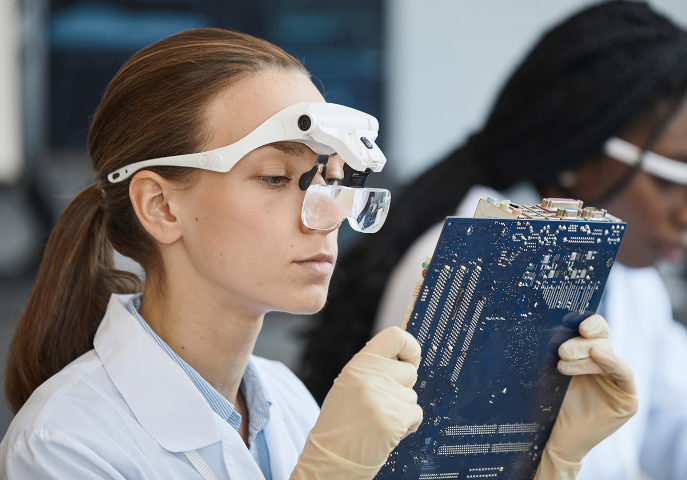
However, profits decline when product quality slips, putting the company’s reputation on the line if that trust isn’t respected. Companies have to produce more to ensure they have enough high-quality goods to satisfy demand. Or they have to redesign products altogether.
This happens much less when producing in the U.S., Mexico, or Canada. In the event that problems arise, visiting domestic or nearshore facilities is less expensive from a time and money perspective. Communicating with vendors in a similar time zone also enables better collaboration and real-time monitoring.
Finally, foreign countries now offer fewer financial incentives to bring work while some U.S. lawmakers are trying to curb the attractiveness of outsourcing to the same. In fact, the U.S. government is actively working to bring manufacturing jobs back to the States through subsidies and credits.
Combined, these factors have altered where electronic production is most financially advantageous.
Lower Supply Chain Risk
Our global electronics supply chains are far more complex than they used to be. Supplier networks can run several layers deep and across geographies, which means disruption can spread quickly. Disruptions, whether natural or human-caused, have a steep cost.
This is the problem: companies can’t simply pass these costs onto consumers. Customers today have more choices and information available to them than ever before. Buying power has shifted away from enterprises to end-users, and it takes only one misstep for loyal patrons to walk away forever.
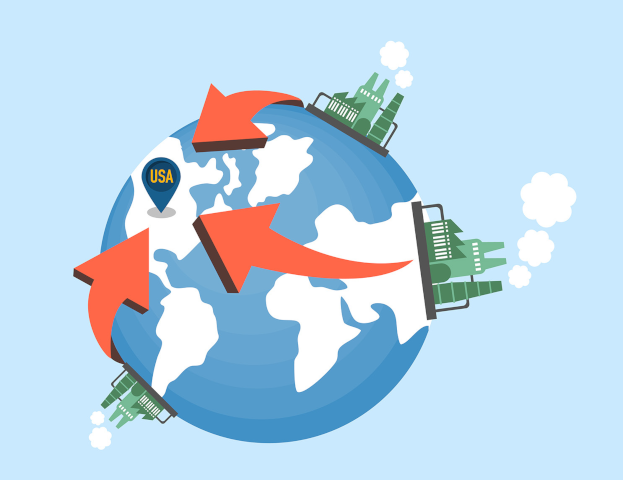
Widely distributed supply chains can also be slower and less agile. Launching new products or delivering finished goods can be challenging depending on market dynamics. We saw this play out with the COVID-19 pandemic. Geopolitical turmoil, clogged shipping lanes, mandatory factory shutdowns, and more have made it difficult for companies to meet normal deadlines.
By bringing production closer to the end user, reshoring eliminates much of this risk. Companies deal with less uncertainty around transportation logistics and international relations. They can build local supplier networks that offer greater insight into component availability, lead times, and pricing. By reshoring, products travel fewer distances, lowering shipping costs as well.
Furthermore, supply chain professionals don’t have to place orders as far in advance when using North American manufacturers to secure necessary volumes. This makes it easier to align production with anticipated demand.
In addition, reshoring allows for faster and more customized prototyping. The iteration cycles and feedback loops are shorter when working with domestic or nearshore factories. As a result, companies can test new ideas without investing massive amounts of capital upfront. This also keeps inventory costs down, ultimately leading to lower prices for consumers.
Stronger IP Protection
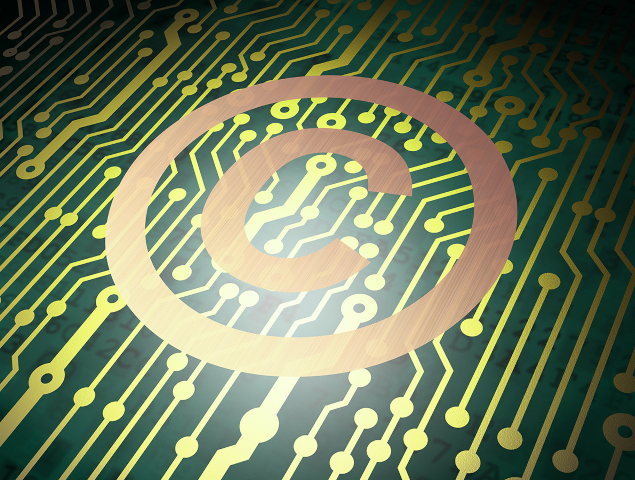
Many companies have struggled to protect intellectual property overseas. Countries like China don’t share a similar commitment to intellectual property rights as lawmakers in the United States. This exposes organizations to massive risk – financial losses, stolen designs, and copycat products.
The U.S. makes it easy to protect intellectual property in order to incentivize innovation. Without such protections, it would be harder to convince companies, entrepreneurs, and engineers to pursue new ideas that could lead to financial gains.
Reshoring alleviates much of the worry associated with IP protections. Those who want to partner with nearshore factories in Mexico and Canada can enjoy similar peace of mind. The United States- Mexico-Canada Agreement that went into effect in July 2020 includes protections for U.S. IP, which is good news for those considering reshoring electronics production.
Conclusion: Reshoring is Both a Short and Long-term Solution
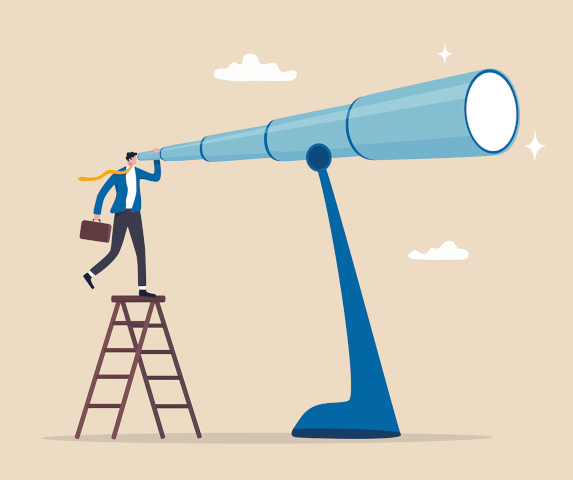
Companies are reshoring electronics production to take advantage of shifting tides. The reasons that once pushed leaders to send manufacturing overseas aren’t there anymore, at least not to the same extent. Those looking to develop basic and complex electronics products can now do so in North America.
Reshoring not only makes sense as a short-term solution to recover from COVID-19 but also as a long-term strategy to increase electronics supply chain resilience.
MacroFab makes it easy to bring offshore operations closer to home. We’ve built a network of high-quality manufacturing facilities across the U.S., Canada, and Mexico. Through this network, we are able to provide elastic factory capacity, cost-effective pricing, and high-quality production. Companies in all industries take advantage of our cloud manufacturing platform and production capabilities.
Related Topics
Preparing for Potential Supply Chain Disruptions During Lunar New Year
This blog discusses on how to prepare for unexpected events for global supply chains such as the dockworker strike in preparation for Lunar New Year.
Mapping Out a PCBA Supply Chain Strategy in Five Moves
Companies should create unique vendor relationships with numerous international suppliers due to the necessity of having to source components globally.
MacroFab’s Modern Approach to Strategic Sourcing
Many Contract Manufacturers (CMs) and Original Equipment Manufacturers (OEMs) have some sort of procurement team. So what makes MacroFab so different?
Find out more about reshoring with MacroFab.
More on ReshoringAbout MacroFab
MacroFab offers comprehensive manufacturing solutions, from your smallest prototyping orders to your largest production needs. Our factory network locations are strategically located across North America, ensuring that we have the flexibility to provide capacity when and where you need it most.
Experience the future of EMS manufacturing with our state-of-the-art technology platform and cutting-edge digital supply chain solutions. At MacroFab, we ensure that your electronics are produced faster, more efficiently, and with fewer logistic problems than ever before.
Take advantage of AI-enabled sourcing opportunities and employ expert teams who are connected through a user-friendly technology platform. Discover how streamlined electronics manufacturing can benefit your business by contacting us today.