MacroFab Blog
Electronics manufacturing spans many industries including aerospace, automotive, consumer electronics, and medical. Each industry and/or project has its own design drivers whether that be cost, reliability, time to market, value and assembly, or some combination of the above. All too often, design engineers, sacrifice optimal solutions to satisfy various corporate or departmental initiatives. These various design drivers can conflict with each other or even conflict between departments. Procurement focuses on piece cost along with supplier selection and development. Manufacturing is often focused on just-in-time delivery. Quality Control is concerned with a supplier’s processes and ensuring good incoming quality and longer-term reliability of parts. Design engineers try to complete the design while meeting the initiatives of each department.
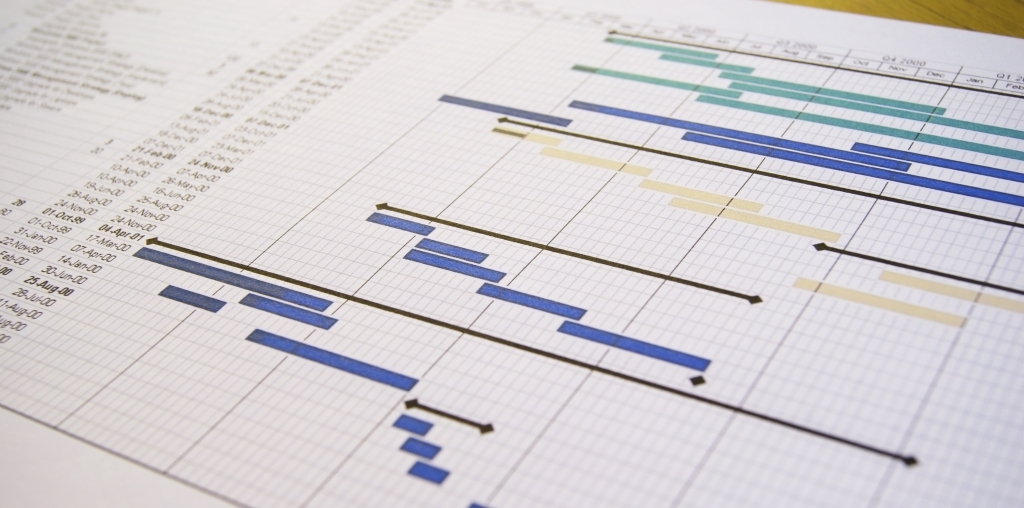
Product Design Phases
When engineers have an initial design, the focus shifts to the building of prototypes and validating the design. Historically, this has necessitated working with small prototype shops to build initial designs. This phase of the project is where the engineers:
- Learn and define critical characteristics
- Identify intellectual property
- Validate the critical design parameters
As this process progresses, engineers prefer to work with small prototype manufacturers where immediate service and feedback are received prior to engaging with a production contract manufacturer who specializes in the specific project drivers (cost, quality, etc..). While this works well to validate the design, the learnings related to the design do not transfer very well from a prototype manufacturer to a production contract manufacturer. In fact, once a contract manufacturer is chosen, a redesign of the PCB layout to optimize cost or reliability to better match the capabilities or equipment of the chosen manufacturer is often necessary. Additionally, many production contract manufacturers are located offshore which results in poor service due to time zone or language differences. Ask any design engineer, they could likely give you examples of working with a supplier where learnings did not translate well between design stages.
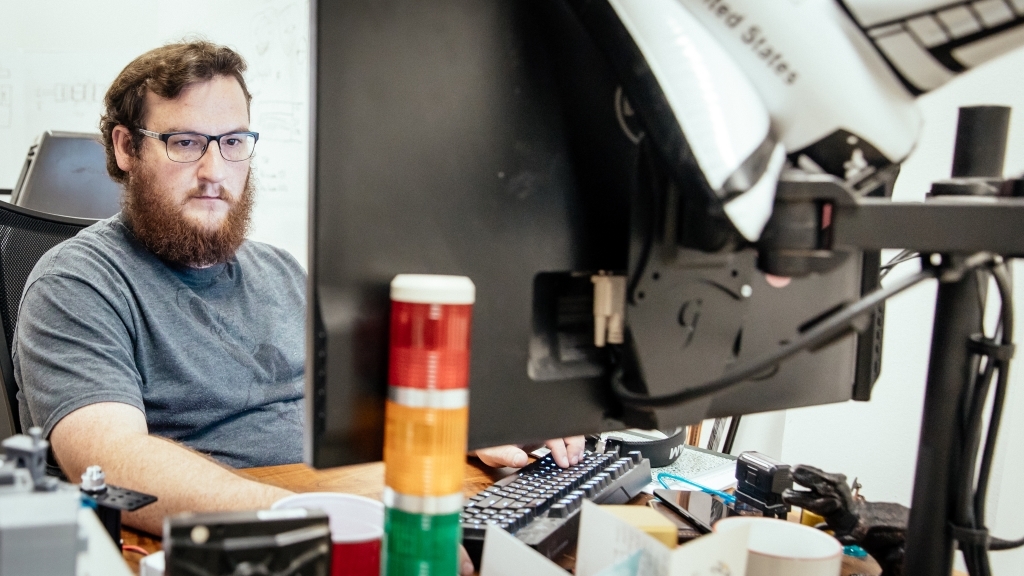
Choosing a Contract Manufacturer 1
The PCB progresses through the design stages and moves from a prototype manufacturer to the initial launch (usually onshore) and then finally to a mature production contract manufacturer (often overseas). Each transition turns into a small project in and of itself. Maintaining the goals of cost, quality, delivery, and design learnings present a challenge through each transition. The inefficiency of such a process adds considerable costs in terms of additional engineering, procurement, and quality engagement.
Selecting a Contract Manufacturer
The selection of the contract manufacturer typically occurs after the initial design validation. Procurement departments usually work with engineering to create a list of potential suppliers. Quotation packages are sent out and then preliminary quotes are received 2 to 6 weeks later. Only then can cost and capital estimates are compared against real quotations. Of course, this usually takes another 2 to 4 weeks to properly compare all the bid packages from potential suppliers and reach a consensus on the proper partner moving forward.
Once work begins with the selected supplier, design elements are modified to work well with the supplier processes and equipment. Approving part substitutions, modifying design packages, and a review of those packages add additional weeks and unnecessary cost. Through this process, the intent is to keep intact those critical design characteristics identified so much earlier during the prototype builds and testing.
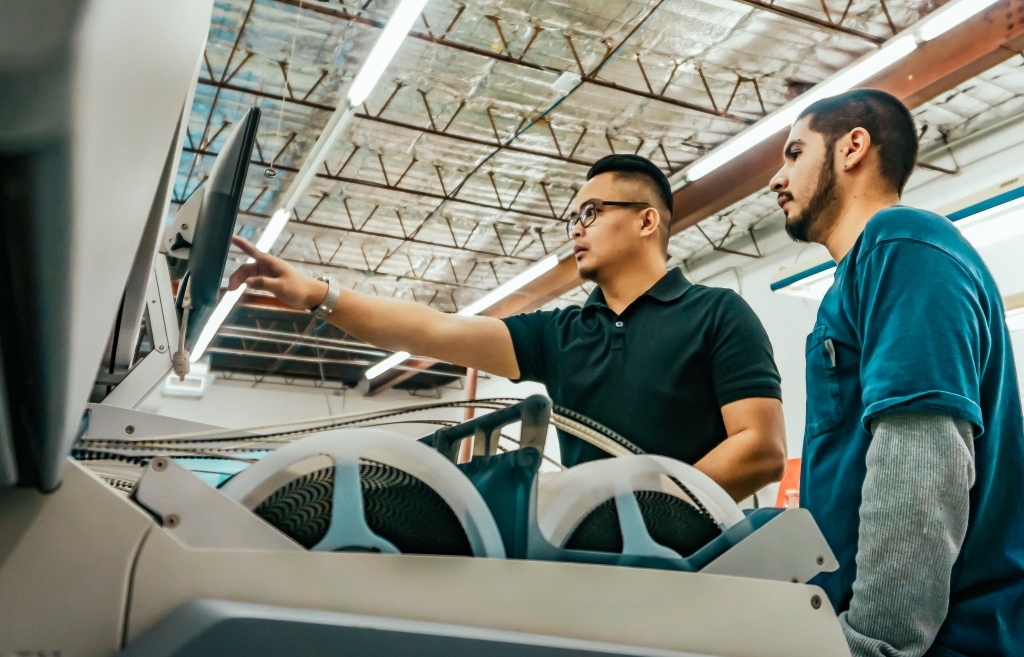
Choosing a Contract Manufacturer 2
For many design engineering firms, success depends on contract design work. In order to receive contract work, it is imperative that engineers operate as efficiently and accurately as possible to provide a good value proposition. Even in large companies, where designs are completed internally, timelines and manpower are critical issues to manage.
I would like to introduce you to a new electronics PCB design model that addresses these outlined issues and works with the majority of designs. This model assists in controlling cost against targets from the initial phase forward while working with the same manufacturing group. This manufacturing group is engaged from the initial design prototype(s) all the way through production.
Imagine a scenario where you can upload your bill of materials along with your Gerber files (or native files) and receive immediate quotations for prototypes as well as allowing you to view the cost reductions and impact as you scale. Once the initial design is complete, you may upload your design files and have immediate prototype costs and production cost scenarios based on the volume scale.
Consider that this same service lets you retain learning from the prototype phase to the production phase. This same tool implements automatic revision control and allows you to scale your design as your production scales. Most of the laborious and time-consuming tasks so boorishly described at the beginning of this article can be streamlined or even eliminated. Does this sound appealing so far? To make it interesting let’s add a few more elements:
- Outstanding service where you can speak with a knowledgeable person immediately and receive valuable feedback on manufacturing-related needs.
- Designs manufactured in days, versus weeks.
- Onshore (USA) manufacturing
- A large contract manufacturer factory pool, all with guaranteed capabilities to manufacture your design.
The MacroFab Advantage
MacroFab has put together an electronics contract manufacturing process that compliments the design process. MacroFab’s innovative online tools link the entire design and manufacturing process from initial design prototypes through production runs. MacroFab does much more than just contract manufacturing. You can immediately see your costs and approve alternate parts. Does your design require rigorous levels of critical validation testing prior to the receipt? If so, MacroFab can build custom test fixtures to validate your critical characteristics. If you require other value-added services such as programming, manufacturability reviews or warehousing MacroFab can assist with that as well.
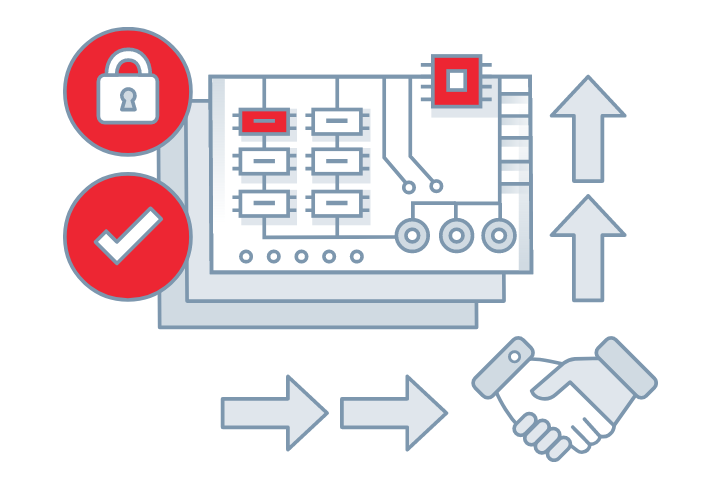
Choosing a Contract Manufacturer 3
For designs where volumes exceed the “on demand” services, MacroFab creates custom quotations as well. MacroFab’s methods of pairing the manufacturing process with the engineering design process are revolutionizing the way electronic designs are quoted and moved from prototype to production scale. The savings are measured not only by the time (and money) realized by the contract designers but also in the satisfaction of knowing that you have exceeded your customer’s expectations.
Switch to a Better PCBA Experience
Was this post helpful? Let us know in the comments below.
Related Topics
Designing Rugged PCBAs for Smart City Applications
PCBA design in smart city applications have become a staple in making a change. From instances such as smart electric grids, crime detection, and waste.
Ultimate Guide To PCB Schematics: Concept to Prototype
A comprehensive guide for navigating early design phases and utilizing schematics alongside Gerber and drill files during the PCB creation process.
Improve Your Next PCB Prototype: Better Debugging, Testing, and Reliability
Enhance PCB prototypes with debugging, testing, and reliability features. Get design tips like test points, power management, and signal integrity testing
About MacroFab
MacroFab offers comprehensive manufacturing solutions, from your smallest prototyping orders to your largest production needs. Our factory network locations are strategically located across North America, ensuring that we have the flexibility to provide capacity when and where you need it most.
Experience the future of EMS manufacturing with our state-of-the-art technology platform and cutting-edge digital supply chain solutions. At MacroFab, we ensure that your electronics are produced faster, more efficiently, and with fewer logistic problems than ever before.
Take advantage of AI-enabled sourcing opportunities and employ expert teams who are connected through a user-friendly technology platform. Discover how streamlined electronics manufacturing can benefit your business by contacting us today.