MacroFab Blog
The bullwhip effect is a phenomenon where ever-growing fluctuations across the entire supply chain create unforeseen and unwanted results.
What is the Bullwhip Effect?
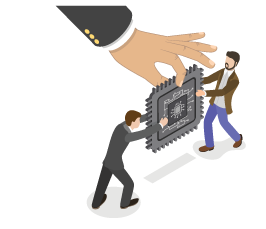
The bullwhip effect is a phenomenon where ever-growing fluctuations across the entire supply chain create unforeseen and unwanted results. Demand signal amplification worsens and increases as order cues move through the supply chain. This can happen when companies hedging against potential future shortages change buying patterns to cover both short- term and longer-term needs, or even when changing demand factors are misread.
Unfortunately, such demand signals create more problems. OEMs may place two or three component orders with different suppliers hoping at least one will pan out. But once a single order has confirmation, the other orders–which never really existed– often get canceled. Manufacturers who ramped up production according to needs can get left holding excess supply. If too many companies implement this strategy at once, the resulting price destabilizing effect can be disastrous.
Ghost Orders and the Illusion of Scarcity
Additionally, forward buying for future need creates other problems. Companies build stockpiles based on their anticipated demand. But what if that demand never materializes? The Q1 2022 electronics market was a good example of component demand driven by future as much as current need, driving some purchasing agents to buy necessary components whenever located. But stockpiles could only accumulate if OEMs paid premium shipping costs to deliver parts to warehousing space, also at an all-time high. Over time, these higher costs can impact profitability.
Finally, ghost orders can push out lead times at the manufacturer while deprioritizing real orders, creating the illusion of scarcity and further snarling the supply chain. Then when those ghost orders get canceled, manufacturers can have too many parts with nowhere to go. In fact, in Q4, 2021 we noted a 30% increase in backlog order cancellations at component manufacturers. If too many orders get canceled before manufacturers can pivot supply downward, the resulting components glut can depress prices.
At the same time, OEMs may be left with a stockpile of unused components purchased at higher than the current market price, stuck in expensive warehousing space. Yet selling off these assets may depress prices further. It’s a difficult situation with no easy or short term fix.
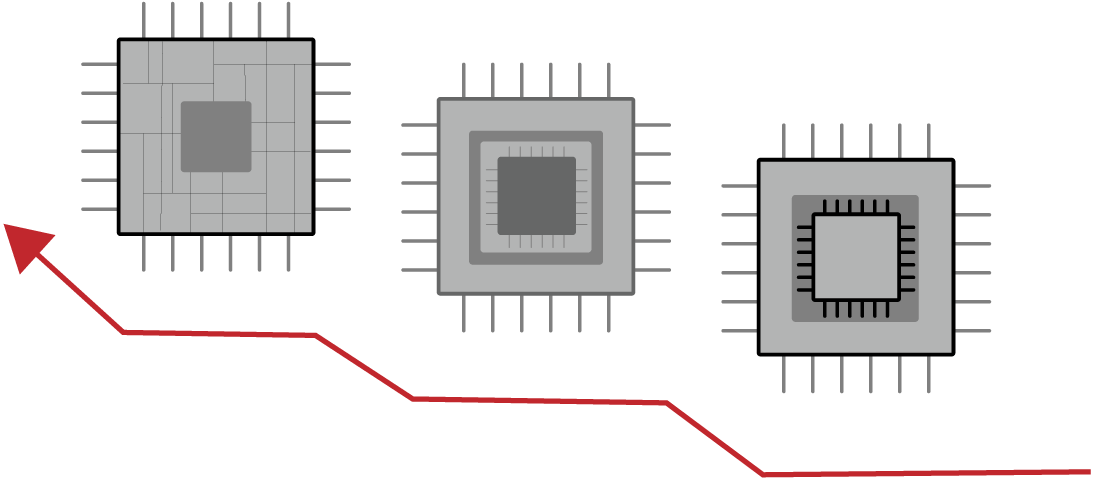
While every company within a supply chain forecasts for inventory control and production scheduling, such forecasting may be based on order history rather than current data. Further, in times of scarcity forecasts may reflect demand plus extra safety inventory. But this can be dangerous when using traditional supply chain information where visibility can be a problem and decisions get based upon out-of-date or irrelevant datasets. Long lead times for some components can further exacerbate variability and cause more supply swings.
How to Avoid the Bullwhip Effect
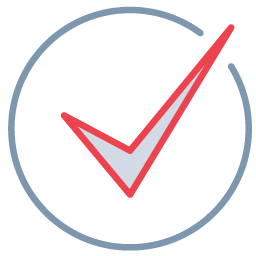
Checkpoint
Supply chains must be both informed and agile to accurately forecast demand, but traditional supply chain management often lacks the end- to-end transparency needed to mitigate and correct for the bullwhip effect.
The simplest way to avoid the bullwhip effect is to use data recognizing the excessive costs of forward buying, and identify real- time datasets to better implement buying decisions. Unfortunately, traditional supply chain management often lacks the end-to-end transparency to mitigate and correct for the bullwhip effect. Supply chains must be both informed and agile to forecast demand frequency and quantity with accuracy. Transparent data flow is a must for this to happen.
Additionally, controlling lead times can minimize the bullwhip effect through better planning and decreased holding costs. When implemented properly, customer demand remains satisfied. This goes hand-in-hand with providing better communication by using a better data policy. Better data also improves forecasting and inventory audit procedures.
How to Avoid the Bullwhip Effect
MacroFab’s cloud manufacturing model is built upon data transparency, data integration, and automation. By centralizing the procurement process of your non-critical purchases using MacroFab’s alternative part sourcing modeling, you can improve your supply chain transparency while furthering your parts network. Potential inventory options come without unnecessary complicated vendor negotiations. As an additional benefit, MacroFab’s bulk purchasing power can lower your overall costs.
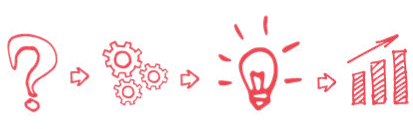
Using MacroFab’s alternative parts sourcing may improve your sourcing efficiency, thereby lowering your associated acquisition costs through decreased transactional expenditures and lower work hours invested. As you build orders, changes, and integrations within MacroFab’s platform, the AI algorithm understands more about your company’s needs and patterns. MacroFab’s digital thread maintains ongoing data about every change that remains available and accessible to your team at all times. Your new insight on order speed, inventory replenishment, and costs can then help you better forecast demand and minimize lead times for a leaner production process, keeping the bullwhip effect at bay.
Related Topics
Preparing for Potential Supply Chain Disruptions During Lunar New Year
This blog discusses on how to prepare for unexpected events for global supply chains such as the dockworker strike in preparation for Lunar New Year.
Mapping Out a PCBA Supply Chain Strategy in Five Moves
Companies should create unique vendor relationships with numerous international suppliers due to the necessity of having to source components globally.
MacroFab’s Modern Approach to Strategic Sourcing
Many Contract Manufacturers (CMs) and Original Equipment Manufacturers (OEMs) have some sort of procurement team. So what makes MacroFab so different?
Upload Your RFQ Today
Want to know more about how MacroFab can help your production? Upload an RFQ for a fast and reliable quote to get the process started.
About MacroFab
MacroFab offers comprehensive manufacturing solutions, from your smallest prototyping orders to your largest production needs. Our factory network locations are strategically located across North America, ensuring that we have the flexibility to provide capacity when and where you need it most.
Experience the future of EMS manufacturing with our state-of-the-art technology platform and cutting-edge digital supply chain solutions. At MacroFab, we ensure that your electronics are produced faster, more efficiently, and with fewer logistic problems than ever before.
Take advantage of AI-enabled sourcing opportunities and employ expert teams who are connected through a user-friendly technology platform. Discover how streamlined electronics manufacturing can benefit your business by contacting us today.