MacroFab Blog
You've poured your heart and soul into this project. Late nights fueled by coffee and determination have finally paid off. Your new electronic system prototype sits on your desk, a testament to your engineering expertise. It functions flawlessly, exceeding all expectations. Now comes the moment of truth: transitioning your prototype into a full-scale production run.
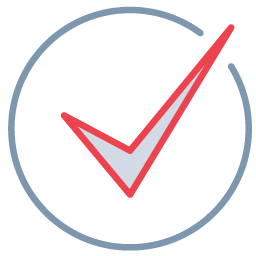
Checkpoint
A digital platform that houses comprehensive design information serves as a single source of truth, ensuring alignment between design inputs and outputs
This final hurdle can feel exhilarating, but also nerve-wracking. Unlike the controlled environment of prototyping, production introduces a complex web of factors outside your direct control. Contract manufacturers (CMs), material availability, and unforeseen manufacturing challenges can all conspire to derail your first production build. The result? Delays, wasted resources, and a sinking feeling in the pit of your stomach.
This article aims to equip you with the knowledge to navigate the potential pitfalls of full-scale PCBA manufacturing. By understanding the most common roadblocks and implementing proactive solutions, you can significantly increase your chances of a successful first production run.
8 Common Roadblocks on the Path to Production Success
Communication Breakdown: The Perils of Information Silos
Effective communication is paramount in the transition from prototype to production. The absence of a centralized information hub can lead to misinterpretations, delays, and increased costs.
Digital manufacturing platforms provide a robust solution by consolidating design files, assembly instructions, and other critical documentation. This centralized repository ensures that all stakeholders, from engineers to factory floor technicians, possess identical and up-to-date information. By eliminating the potential for discrepancies caused by disparate communication channels, organizations can significantly reduce errors and streamline the production process.
Moreover, digital platforms facilitate real-time collaboration and knowledge sharing. Engineers can provide timely clarifications, and technicians can offer valuable feedback on assembly challenges. This iterative approach fosters continuous improvement and enhances the overall product quality. By investing in a digital manufacturing platform, companies can bridge communication gaps, mitigate risks, and improve operational efficiency.
Subjective Acceptance Criteria: Creating A Foundation for Quality
Precisely defined acceptance criteria are essential for achieving consistent product quality. Vague or subjective standards can lead to inconsistencies between production units, increasing the likelihood of defects and rework.
Establishing clear, objective, and measurable criteria for both electrical and mechanical aspects of the assembly process is crucial. For instance, instead of relying on subjective terms like "good solder joints," engineers should specify precise metrics such as solder joint height, fillet shape, and the absence of voids.
Look for a CM that can manage your prototypes as well as your production. By working with the contract manufacturer (CM) early on in the prototype phase, it is possible to identify potential failure points that may adversely affect future production runs and develop robust acceptance criteria. Bringing your production CM into your process earlier allows engineers to gain valuable insights into the feasibility of design specifications and make necessary adjustments to ensure manufacturability. This proactive approach reduces the risk of costly rework and delays during production when they can really hurt.
Bill of Materials Bottlenecks: Mitigating Supply Chain Risks
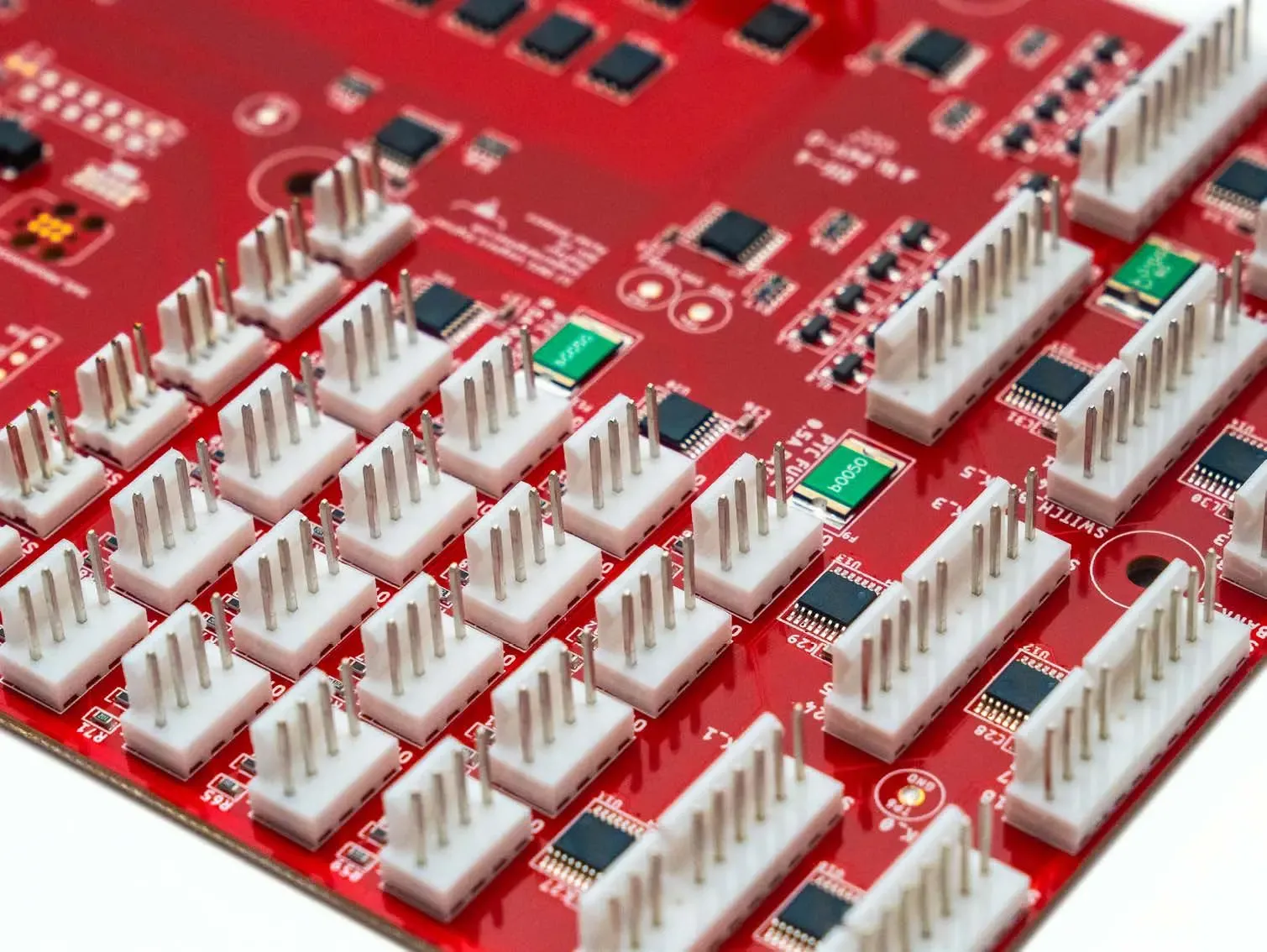
A rigid BOM can create significant hurdles in the face of component shortages or supply chain disruptions. Consequently, engineers should prioritize component selection based on availability and identify suitable alternatives. Maintaining a flexible BOM allows for rapid adjustments in response to changing market conditions or unforeseen supply chain challenges.
Furthermore, accurate lead time estimation is critical for effective production planning. Partnering with a CM that offers BOM kitting and a digital platform offering comprehensive lead time analysis can provide valuable insight into potential supply chain bottlenecks. By proactively addressing these challenges, organizations can minimize production delays and smoothly transition from prototype to full-scale manufacturing.
Tolerance Trap: Navigating Design and Manufacturing Variability
Tolerance accumulation is a common pitfall in product design and manufacturing. Even minor variations in component dimensions can have a significant impact on assembly fit and functionality. To prevent tolerance-related issues, engineers must carefully analyze component tolerances and their cumulative effect on the overall product. Statistical process control (SPC) techniques can be employed to assess the potential impact of manufacturing variability on product performance.
Additionally, close collaboration with the CM during the design phase is essential for identifying and mitigating tolerance-related risks. By involving manufacturing experts early in the process, engineers can gain valuable insights into the achievable tolerance levels and make necessary design adjustments for manufacturability. This proactive approach helps prevent costly rework and delays caused by tolerance-related assembly issues.
Quality Assurance Challenges: From Specification to Implementation
A comprehensive quality specification plan is the cornerstone of a successful production run. This document outlines precise quality expectations for both the assembly process and individual components. By clearly defining these requirements, engineers minimize ambiguity and reduce the likelihood of defects. Incorporating visual and x-ray inspection criteria for incoming materials further strengthens the quality assurance process.
A well-structured quality plan also includes robust quality control procedures. These procedures should specify inspection points, acceptance criteria, and corrective actions for non-conforming products. By implementing a rigorous quality control system, organizations can identify and address quality issues early in the production process, preventing costly rework and scrap. Moreover, a data-driven approach to quality management enables continuous improvement through process optimization and defect prevention.
Manufacturing Mismatch: Optimizing Contract Manufacturer Selection
Selecting the right contract manufacturer (CM) is critical for production success. A CM that lacks the necessary capabilities or expertise can lead to significant challenges, including production delays, quality issues, and increased costs.
As a precaution, engineers should carefully evaluate potential CMs based on their track record, equipment, and experience with similar products. Conducting pilot runs or pre-production builds at the selected CM can provide valuable insights into the manufacturer's capabilities and identify potential issues before full-scale production. Look for a partner with the capacity and willingness to prioritize your needs. This means finding a company with readily available capacity for when business is booming that will also prioritize your smaller orders when necessary.
Additionally, establishing clear communication channels and expectations with the CM is vital to a smooth production process. By diligently selecting and managing the CM, organizations can increase the likelihood of a successful production launch.
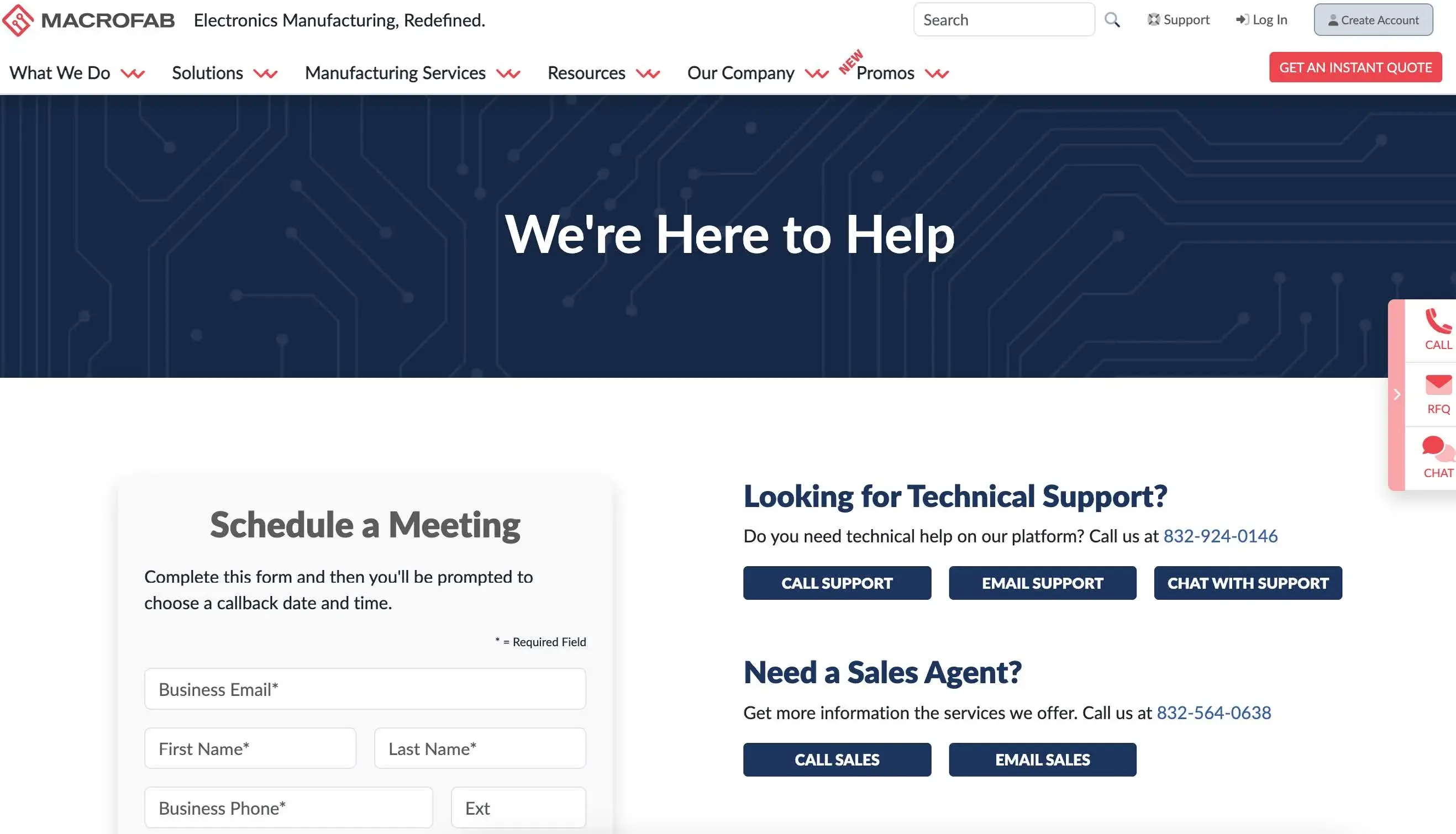
Reliance on Tribal Knowledge: Safeguarding Production Continuity
Traditional reliance on the expertise of specific individuals can create vulnerabilities within the manufacturing process. When key personnel are unavailable, the risk of production disruptions increases significantly. Reduce this risk by working with a CM offering a robust, centralized knowledge repository.
A digital platform that houses comprehensive design information serves as a single source of truth, ensuring alignment between design inputs and outputs. This platform provides a clear roadmap for all manufacturing personnel, eliminating the potential for deviations from the original design intent. By digitizing and standardizing manufacturing processes, organizations reduce reliance on individual expertise and enhance overall production efficiency.
Further, a digital platform facilitates knowledge sharing and collaboration among team members. It enables real-time access to information, enabling rapid problem-solving and decision-making. This collaborative approach fosters a culture of continuous improvement and reduces the risk of knowledge loss due to employee turnover.
Miscommunication Minefield: Effective Communication Strategies
Effective communication is essential for preventing misunderstandings and delays throughout the product development and production process. Engineers should avoid making assumptions about the CM's understanding of design changes or requirements. Instead, they should implement a formal change management process that clearly communicates modifications to the CM.
Regular communication and collaboration between the engineering and manufacturing teams are also crucial for ensuring alignment and addressing potential issues proactively. By fostering an open and transparent communication environment, organizations can minimize miscommunication and improve overall project efficiency. Additionally, using clear and concise language in all project documentation helps to reduce ambiguity and prevent misunderstandings.
Tired of the tedious task of reworking a PCB assembly? See how the Bald Engineer used MacroFab's turnkey service to avoid problems in the first place.
Partnering for Success: How MacroFab Can Help
By following these best practices and partnering with a reliable Contract Manufacturer like MacroFab, you can significantly reduce the risk of production build failure. MacroFab offers a suite of services specifically designed to address the challenges faced by electrical engineers transitioning prototypes to production, including
Digital Manufacturing Platform: Streamline communication and make sure everyone is on the same page with MacroFab's digital manufacturing platform. Upload design files, BOMs, and assembly instructions to a secure and centralized location. You can manage team permissions so that each member of your team has access to the information they need.
DFM Expertise: MacroFab's engineers can analyze your design for manufacturability, identifying potential tolerance issues and suggesting improvements to streamline the production process. This can save you time and money by avoiding costly design revisions later in the development cycle.
Pre-Vetted North American Manufacturing Network: MacroFab’s manufacturing network offers a wide range of capabilities and ready manufacturing capacity for any job. You can rest assured that your project will be produced on the factory line with the specific expertise necessary to best manufacture it.
Seamless Communication: MacroFab prides itself on clear and consistent communication throughout the entire manufacturing process. Your named project manager will be your point of contact, ensuring you are kept informed of every step along the way.
Rapid Prototyping: MacroFab offers rapid prototyping services to help you refine your design and identify potential issues before committing to a full production run. This allows you to iterate quickly and minimize the risk of problems during the first production build.\
Complete Transparency: MacroFab provides real-time production tracking and detailed cost breakdowns, allowing you to stay in control of your project budget and timeline.
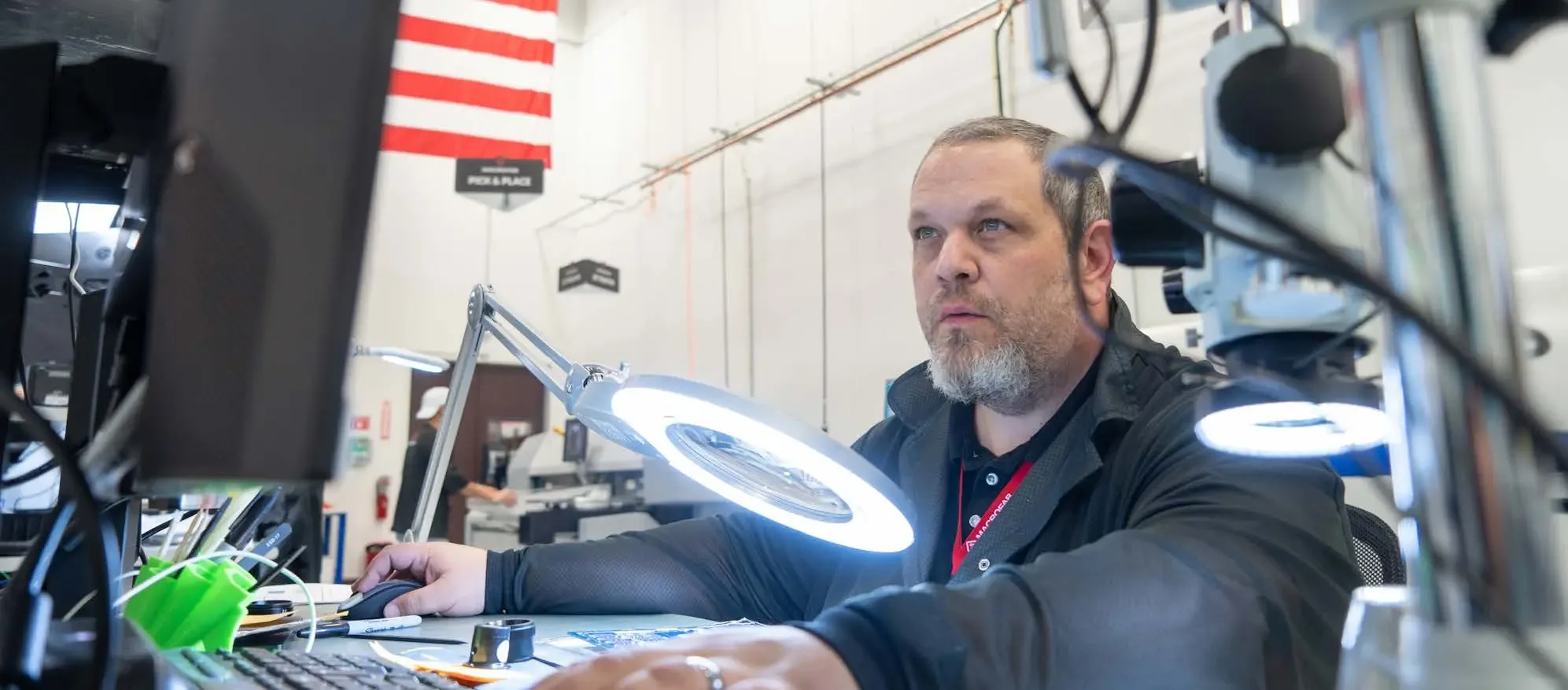
By leveraging MacroFab's comprehensive suite of services and industry expertise, you can navigate the complexities of transitioning your prototype to production with confidence. MacroFab understands the challenges faced by electrical engineers and is committed to providing the tools and support necessary to ensure your project's success.
Related Topics
How MacroFab Ensures Peak Production Quality for Modern Electronics
Discover how MacroFab ensures exceptional production quality for modern electronics, meeting the challenges of complexity and innovation with ease.
How to Shorten PCBA Production Lead Times with MacroFab
In the rapidly evolving electronics sector, extended production lead times are no longer tolerable, and minimizing these lead times is crucial for success.
From Garage to Growth: How Startups Scale with MacroFab
Scale your hardware startup smarter with MacroFab—prototype to production, U.S. manufacturing, instant quoting, and expert support every step.
Ready to turn your innovative design into reality?
Get an instant quote nowAbout MacroFab
MacroFab offers comprehensive manufacturing solutions, from your smallest prototyping orders to your largest production needs. Our factory network locations are strategically located across North America, ensuring that we have the flexibility to provide capacity when and where you need it most.
Experience the future of EMS manufacturing with our state-of-the-art technology platform and cutting-edge digital supply chain solutions. At MacroFab, we ensure that your electronics are produced faster, more efficiently, and with fewer logistic problems than ever before.
Take advantage of AI-enabled sourcing opportunities and employ expert teams who are connected through a user-friendly technology platform. Discover how streamlined electronics manufacturing can benefit your business by contacting us today.